

在过程中,当加工产生连绵不断的带状切屑时,不仅容易划伤工件加工表面和损坏刀刃,严重时还会威胁到操作者的安全,所以采取必要的工艺措施,控制屑型和断屑一直是机械加工行业中极为重要的工艺问题。
由于切屑是切屑层变形的产物,所以,改变切削加工条件是改变切屑种类、实现断屑的有效途径,而影响切屑加工条件的因素主要包括工件材料、刀具几何角度及切屑用量等。
一般切屑需要满足以下几个基本条件:切屑不得缠绕在刀具、工件及其相邻的工具、装备上;切屑不得飞溅,以保证操作者与观察者的安全;精加工时,切屑不可划伤工件的已加工表面,影响已加工表面的质量;保证刀具预定的耐用度,不能过早磨损并竭力防止其破损;切屑流出时,不妨碍切削液的喷注;切屑不会划伤机床导轨或其他部件等。
由于塑性变形程度的不同,可能会产生不同种类的切屑,如图1所示。加工塑性材料时,主要形成带状切屑、节状切屑或粒状切屑,加工脆性材料时,一般形成崩碎状切屑。
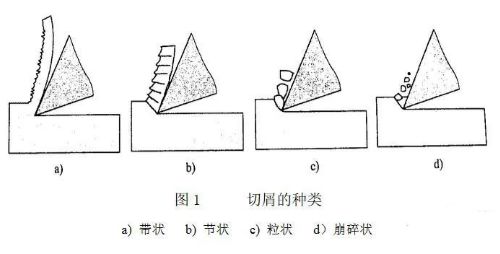
由上可知,切屑的种类随工件材料、切削条件的不同。因此,在加工过程中可以通过观察切屑形态来判断切屑条件是否合适,也可以通过转化切削条件改变切屑形态,使之向着有利于生产的方向转化。
金属切削过程中,切屑是否容易折断,与切屑的变形有直接联系,所以研究切屑折断原理必须从研究切屑变形的规律入手。
切削过程中所形成的切屑,由于经过了比较大的塑性变形,它的硬度将会有所提高,而塑性和韧性则显著降低,这种现象叫冷作硬化。经过冷作硬化以后,切屑变得硬而脆,当它受到交变的弯曲或冲击载荷时就容易折断。切屑所经受的塑性变形越大,硬脆现象越显著,折断也就越容易。在切削难断屑的高强度、高塑性、高韧性的材料时,应当设法增大切屑的变形,以降低它的塑性和韧性,便于达到断屑的目的。
第一部分是切削过程中所形成的,我们称之为基本变形。用平前刀面车刀自由切削时所测得的切屑变形,比较接近于基本变形的数值。影响基本变形的主要因素有刀具前角、负倒棱、切削速度三项。前角越小,负倒棱越宽、切削速度越低,则切屑的变形越大,越有利于断屑。所以,减小前角、加宽负倒棱,降低切削速度可作为促进断屑的措施。
第二部分是切屑在流动和卷曲过程中所受的变形,我们称之为附加变形。因为在大多数情况下,仅有切削过程中的基本变形还不能使切屑折断,必须再增加一次附加变形,才能达到硬化和折断的目的。迫使切屑经受附加变形的最简便的方法,就是在前刀面上磨出(或压制出)一定形状的断屑槽,迫使切屑流入断屑槽时再卷曲变形。切屑经受附加的再卷曲变形以后,进一步硬化和脆化,当它碰撞到工件或后刀面上时,就很容易被折断了。
切屑断与不断的根本原因在于切屑形成过程中的变形和应力,当切屑处于不稳定的变形状态或切屑应力达到其强度极限时,就会断屑,通常切屑是卷曲后折断的。
合理选择刀具几何角度、切削用量、磨断屑槽是常用的断屑方法。
常用的断屑槽有折线形、直线圆弧形、全圆弧形3种槽型,如图2所示。
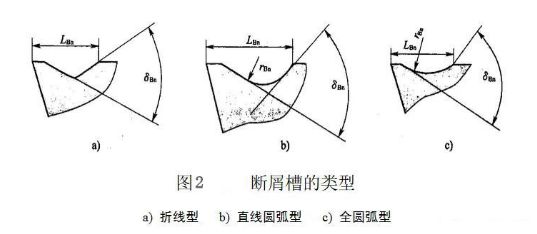
在切削碳素钢、合金钢、工具钢时,可选用折线形、直线圆弧形、断屑槽;切削高塑性材料工件时,例如纯铜、不锈钢工件等,可选用全圆弧形断屑槽。
断屑槽的宽度对断屑的影响很大。一般来讲,槽宽越小,切屑的卷曲半径越小,切屑上的弯曲应力越大,越易折断。所以,采用较小的断屑槽宽对断屑有利。但断屑槽宽度必须与进给量切削深度ɑp联系起来考虑。
若断屑槽宽度与进给量基本合适,则可形成C形切屑。如卷屑槽太窄,易产生堵屑现象,而使车刀负荷增加,甚至损坏切削刃;若卷屑槽太宽,切削卷曲半径太大,则切削变形不够,不易折断,往往不流经槽底而形成不断的带状切屑。
切屑槽的宽度也应与切削深度相适当,否则当槽太窄时,显得切屑宽,不易在槽中卷曲,往往切屑不流经槽底而形成带状切屑。当槽太宽时,又显得切屑窄,流动较自由,变形不够充分,也不折断。
为了得到满意的断屑效果,应按具体加工条件,选择合适的断屑槽宽度。对于硬度较低的工件材料,槽应选得窄些,反之,槽应选得宽些。


往期推荐
版权声明:凡资讯来源注明为其他媒体来源的信息,均为转载自其他媒体。如您对该文章内容有任何疑问或质疑,请第一时间跟我们联系,我们将根据您提供的证明材料确认版权立即删除内容! |