本世纪,随着对于石油的能源焦虑以及核电技术的提高,电动汽车已经代替汽油汽车逐渐成为家用及商用乘用车的主流。而作为电动汽车的动力系统,虽然核心技术略有不同,但都是以将锂电池组以各种排列方式安装在汽车底盘为主。
不过,众所周知,锂电池虽然技术相对成熟,生产成本较低,可以更加简单批量生产。但是也存在着一定的安全隐患和很大环保压力。目前欧洲针对电动汽车厂家甚至提出了由电动汽车厂家自行解决报废电池的法案,也能看出锂电池回收难以及对于环境污染影响等问题。
那么电力化作为乘用车发展的必然趋势,除了锂电以外,有没有更好的途径可以选择呢?
由于水是由氢和氧组成,在自然界里可以说是取之不尽的资源,所以,在日本氢气作为汽油替代燃料已经被研究了许多年。虽然方向是和汽油使用方法相同,依旧采用燃烧发动机来进行驱动,但利用的是资源丰富的氢气发电给车辆提供动能。
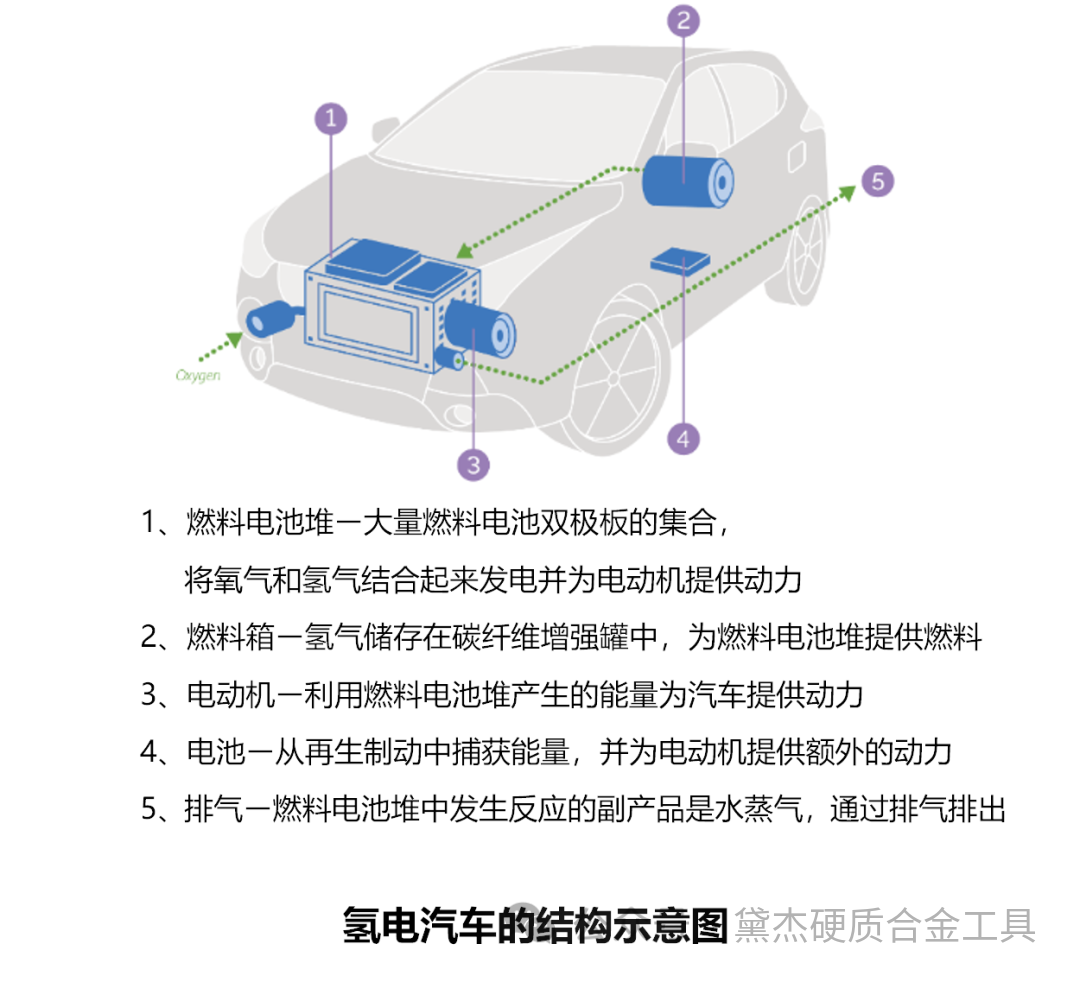
上图目前氢电汽车结构图,通过由燃料电池双极板组成的电池堆将氢气和氧气进行反应产生电力。这样既可以解决目前锂电汽车充电时间过长和里程焦虑的问题;并且,由于双极板为金属产品,回收难度低,对于环境的污染风险也非常小。可以说,目前来看氢燃料电动车是电动汽车的新时代形态。
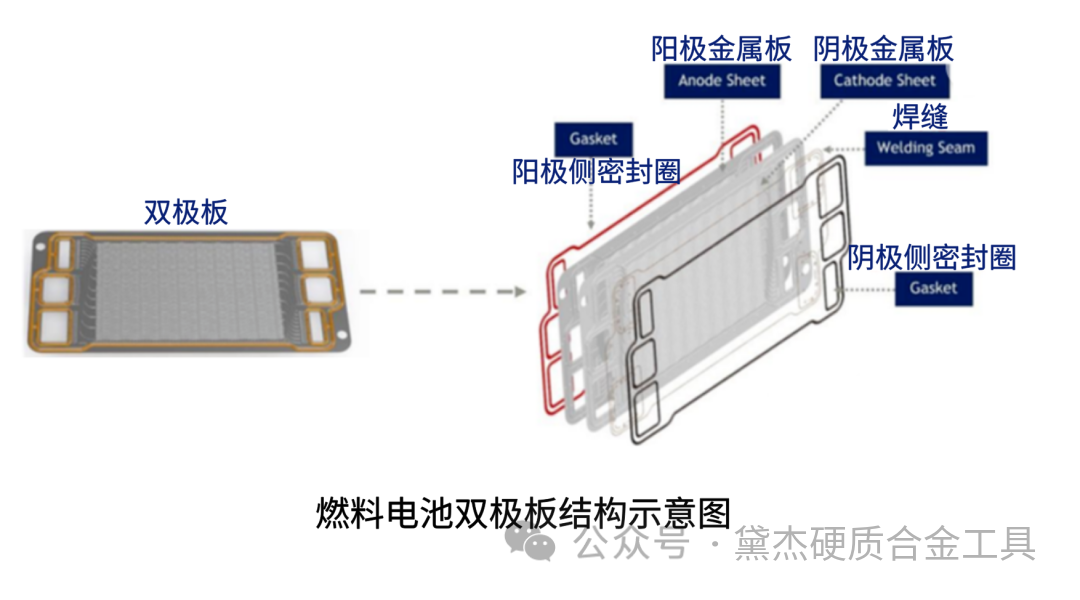
从上图可以看出,双极板组是由一枚阳极金属板和一枚阴极金属板组成,这两枚金属板的厚度非常薄,一般只有0.4mm,由模具冲压制造,将阴阳两张金属板合起来以后从中间打入氢气。为方便氢气顺利通过,双极板上有许多细小的沟槽。双极板本身的制造精度要求非常高,从而对于模具的加工要求就更高了。
上图是双极板模具的实物。传统的加工方式是采用球头和圆角整硬铣刀进行开粗,再用圆鼻刀进行半精加工,最后用CBN球刀和圆鼻刀进行精加工。这样一般来说一块模具从毛胚到成品,整个流程需要7天的时间。
而黛杰公司与TOWA公司技术强强联合,把最花时间的半精和精加工进行优化,采用异形非标刀具进行加工,通过加大步距大幅提高加工效率,最终可以将一块模具的加工时间缩短为3天,效率提高1倍以上。
接下来通过下图以及一些参数数据可以了解到双极板加工的案例,解析双极板加工部位的传统工艺不足和黛杰&TOWA是如何改善并提升效率的。
通过上图可以看到,密密麻麻的铣削沟槽是双极板加工的主要部分,由于传统圆鼻刀的端刃和侧刃为直角,所以在加工这些沟槽时只能采用等高线层切且步距极小,从而导致效率低下。
而黛杰&TOWA提出的方案是采用半标准型特殊刀具,用侧刃一次性将整个沟槽侧壁面铣削完成。
接下来单个沟槽的实际加工中,传统工艺和我们提出的改善工艺有什么区别?
通过以上对比图,可以很直观的感受到黛杰&TOWA提出的改善工艺的优越性。另外,模具的表面粗糙度在工艺要求中也是极其重要的一环,它关系到模具的使用寿命和模具加工出来的产品的质量。下面是模具表面粗糙度数据:
显而易见,新工艺下的模具表面粗糙度远超图纸要求,不仅在效率上,在加工质量上也实现了显著的提高。下面是模具的整体加工参数,供各位参考、借鉴。
来源:黛杰硬质合金工具
编辑 ▎王琰
广告合作 ▎ (微信同号)18240442679 付先生

《汽车工艺师》第一届青年编委会名单 全面剖析宁德时代(CATL)生产线,每个工序都不放过! 国内固态电池及工艺专利 国内多家车企背后庞大的汽车供应链,建议收藏! 2023年全球汽车零部件供应商百强名单 汽车知识大全,一篇文章搞定,必须收藏! 理想供应链如何布局?69家核心供应商揭秘 宝马供应商培训资料 新能源汽车三电系统详解 新能源电池数字化工厂建设必要性及目标 任正非推荐的5G赋能,已经出书了!这个ppt让您内容全知道。 长城徐水智能工厂:286台机器人打造VV5s的豪华与安全