电池包壳体轻量化,对于提升电池包能量密度有着重大意义。
研究以铝合金型材为主体结构的电池包壳体,对铝合金型材断面、搅拌摩擦焊接接头、连接工艺等方面进行了分析研究,并在成本、工艺性等方面进行综合比较,通过CAE对设计方案进行分析验证。
合理的结构设计和连接方式,可以有效地保证壳体整体强度,降低加工难度,使壳体减重,为电池包壳体的轻量化设计提供参考。
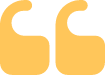
►►►
01 铝合金电池包壳体结构
图 1 铝合金电池包壳体图
►►►
02 设计方案介绍
图 2 边框断面
图 3 底板断面
属于固态焊接技术,焊接过程不存在焊接材料融化; 焊接接头质量好,焊缝为细晶锻造组织结构,没有气孔、裂纹、夹渣等缺陷; 不受焊缝位置的限制,可实现多种接头形式的焊接; 焊接效率高,在 0.4-100 mm 厚度范围内可以实现单焊道焊接成型; 焊件中残余应力低,变形小,可实现高精度焊接; 接头强度高、疲劳性能好,冲击韧性优异; 焊接成本低,没有焊接过程消耗,不需要填丝和保护气体; 焊接操作简单,便于实现自动化焊接。
表 1 为焊接厚度与型材尺寸的对应关系。
图 4 底板断面
表 1 焊接厚度与型材厚度对应关系
图 5 边框与底板双面搅拌摩擦焊接图
图 6 边框与底板外部搅拌摩擦焊接+内部MIG焊接
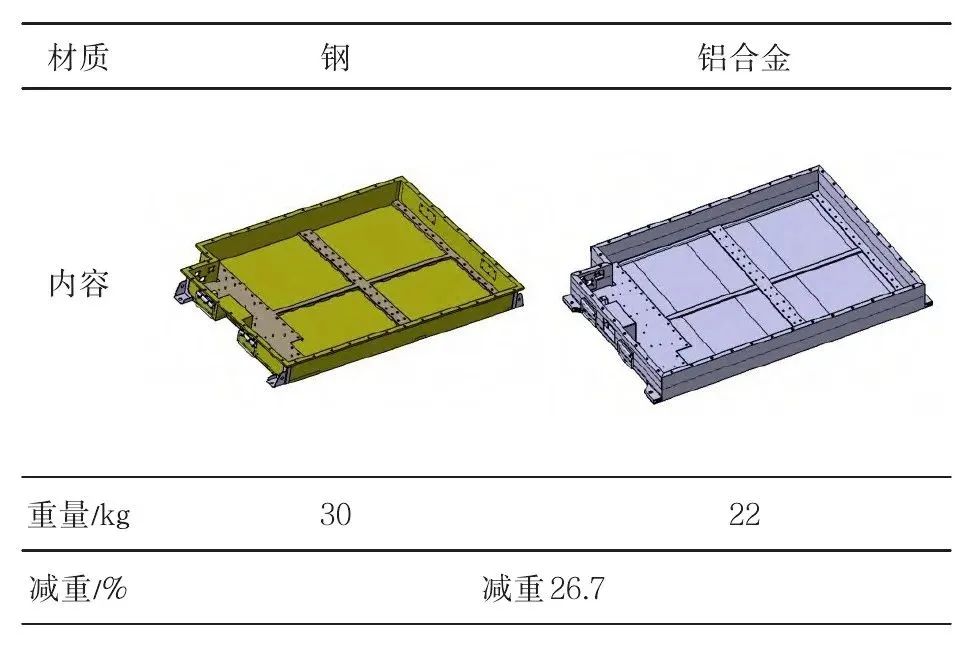
表 2 钢与铝合金电池包壳体重量对比
►►►
03 仿真分析
根据GB/T 31467.3—2015电动汽车用锂离子动力蓄电池包和系统第三部分:安全性要求与测试方法,对铝合金电池包壳体强度、振动、挤压等方面进行仿真分析。
图 7 为某铝合金电池包壳体仿真分析结果
图 7(a)3G 向前工况应力最大值为 29.4 MPa,
图 7(b)振动应力最大值为55.98MPa,最大值均小于6005A屈服强度215 MPa,
图 7(c)挤压最大位移7.081 mm,电池模组安全距离为10mm(每个电池包结构不同,安全距离也会不同,需要客户确认),满足要求。
►►►
04 经验结论
来源:动力电池BMS