
鐐瑰嚮涓婃柟钃濆瓧鍏虫敞鎴戜滑!


瑗垮畨鐭挎簮鏈夎壊鍐堕噾鐮旂┒闄互閫夌熆宸ヨ壓銆侀€夊巶璁捐銆侀€夌熆鏂版妧鏈爺鍙戜负浼樺娍锛屽舰鎴愪簡浠ラ€夊巶璁惧閰嶅銆佸湡寤鸿澶囧畨瑁呫€佺敓浜ц皟璇曘€佹妧鏈鐞嗘壙鍖呭叏鏂逛綅鏈嶅姟浣撶郴锛涘€″閫夌熆鐜繚鑽墏銆侀€夌熆鑷姩鍖栫殑鐜颁唬鍖栫豢鑹茬熆灞辨妧鏈紶鎾笌璺佃鑰�銆�
缁胯壊鐭垮北鎶€鏈紶鎾笌璺佃鑰�
鎹粺璁★紝鐩墠鎴戝浗鍐堕噾宸ヤ笟鍥轰綋搴熷純鐗╁勾浜х敓閲忕害 4.3浜垮惃锛岀患鍚堝埄鐢ㄧ巼涓�18.03%銆傚叾涓伐涓氬熬鐭夸骇鐢熼噺涓�2.84浜垮惃锛屽埄鐢ㄧ巼1.5%锛涢珮鐐夋福浜х敓閲�7557涓囧惃锛屽埄鐢ㄧ巼65%锛涢挗娓d骇鐢熼噺3819涓囧惃锛屽埄鐢ㄧ巼10%锛涘寲閾佺倝娓�60涓囧惃锛屽埄鐢ㄧ巼65%锛涘皹娉�1765涓囧惃锛屽埄鐢ㄧ巼98.5%锛涜嚜澶囩數鍘傜矇鐓ょ伆鍜岀倝娓�494涓囧惃锛屽埄鐢ㄧ巼59%锛涢搧鍚堥噾娓� 90涓囧惃锛屽埄鐢ㄧ巼90%锛涘伐涓氬瀮鍦�436涓囧惃锛屽埄鐢ㄧ巼45%銆傞拡瀵规垜鍥藉喍閲戝伐涓氬浐浣撳簾寮冪墿鐨勭幇鐘讹紝璧勬簮鍖栧鐞嗕笌缁煎悎鍒╃敤鏄浉鍏充紒涓氬拰鏈烘瀯蹇呴』閲嶈鍜屽姞澶у姏搴﹁繘琛岀爺绌剁獊鐮寸殑璇鹃銆傛湰鏂囧氨鍐堕噾鍥轰綋搴熷純鐗╄祫婧愬寲澶勭悊涓庣患鍚堝埄鐢ㄨ繘琛屼簡涓€浜涙湁鐩婄殑鎺㈣銆�
涓€銆佸喍閲戞福鐨勮祫婧愬寲澶勭悊鍜岀患鍚堝埄鐢�
鐩墠鎴戝浗閽㈤搧骞存€讳骇閲忓凡杈惧埌5浜垮惃锛屾瘡骞翠骇鐢熺殑鍐堕噾娓h揪1浜垮惃浠ヤ笂銆傚湪鍐堕噾娓d腑鎺掗噺澶х殑涓昏鏈夐珮鐐夋按娣熆娓c€侀挗娓c€侀珮鐐夐噸鐭挎福绛夛紝鍏朵腑楂樼倝姘存番鐭挎福鍜岄珮鐐夐噸鐭挎福鍒╃敤鐜囪緝楂橈紝鑰岄挗娓e埄鐢ㄧ巼杈冧綆锛屼粎鏈�20%宸﹀彸銆傛湭寰楀埌鍒╃敤鐨勫喍閲戞福闀挎湡鍫嗘斁鏈強鏃剁患鍚堝埄鐢紝涓€鏂归潰浼氶€犳垚鍐堕噾娓i€愭笎澶卞幓娲绘€ч毦浠ュ啀鍒╃敤锛屽彟涓€鏂归潰鍐堕噾娓g殑鍫嗘斁瑕佸崰鐢ㄥぇ閲忓湡鍦板苟浼氫弗閲嶆薄鏌撶幆澧冦€�2009骞�1鏈� 1鏃ワ紝銆婂惊鐜粡娴庝績杩涙硶銆嬮甯冨疄鏂斤紝濡備綍澶ч噺鍒╃敤鍐堕噾娓e凡鎴愪负鍚勯挗閾佷紒涓氱殑褰撳姟涔嬫€ャ€�
锛堜竴锛夊喍閲戞福璧勬簮鍖栧鐞嗗拰缁煎悎鍒╃敤鐨勫彂灞曟柟鍚�
鐩墠锛屾垜鍥界殑閽骇閲忕ǔ灞呬笘鐣岀涓€锛屼絾鐢变簬鐐奸搧鐐奸挗鎶€鏈皻涓嶅鍏堣繘锛屽洜鑰屽悇閽㈤搧浼佷笟姣忓勾閮戒細浜х敓澶ч噺鐨勩€佷笉鍚岀绫荤殑鍐堕噾娓c€傛牴鎹垜鍥界殑鍥芥儏鍜岀洰鍓嶇殑鎶€鏈按骞筹紝瑕佹兂澶ч噺鍒╃敤鍐堕噾娓o紝鍙湁璧板紑鍙戣妭鑳姐€佸埄搴熴€佺幆淇濈殑寤烘潗浜у搧杩欐潯璺€傚喍閲戞福璧勬簮鍖栧鐞嗗拰缁煎悎鍒╃敤鏄寚浠庡喍閲戞福涓閫夐櫎閾佸苟灏嗗熬鏂欏ぇ閲忕敤浜庡缓鏉愪骇鍝佺殑鐢熶骇銆備粠鍐堕噾娓d腑纾侀€夊洖鏀剁殑搴熼挗閾佸彲杩斿洖閽㈤搧鍘傚喍鐐煎啀鍒╃敤锛涚閫夊洖鏀剁殑灏炬枡鍙敤鏉ョ敓浜ф按娉ユ贩鍚堟潗銆佽矾鍩烘潗銆佺爩绛戞按娉ャ€侀鎷岀爞娴嗐€佹贩鍑濆湡鏍囩爾銆佸瀛旂爾銆佸喍閲戞福钂稿帇鍔犳皵鐮屽潡绛夊缓鏉愪骇鍝併€傚喍閲戞福鐨勫紑鍙戝埄鐢ㄦ棦瑕佽€冭檻璧勬簮鐨勫啀鍒╃敤锛岀鍚堝惊鐜粡娴庣殑浜т笟鏀跨瓥锛涘張瑕佽€冭檻鍒伴噰鐢ㄥ悎鐞嗙殑鐢熶骇宸ヨ壓寮€鍙戝嚭鑺傝兘銆佺幆淇濄€佺鍚堝競鍦洪渶姹傘€佽揪鍒板浗瀹舵爣鍑嗚姹傜殑寤烘潗浜у搧銆�
锛堜簩锛夊喍閲戞福璧勬簮鍖栧鐞嗗拰缁煎悎鍒╃敤涓庤妭鑳界幆淇�
鍒╃敤鍐堕噾娓g敓浜ц妭鑳界幆淇濆缓鏉愪骇鍝佺殑鏂规硶鏄埄鐢ㄩ挗閾佸巶浜х敓鐨勫喍閲戞福銆侀珮鐐夌叅姘斻€佷綑鐑捀姹界瓑鍐嶇敓璧勬簮鐢熶骇鍑鸿妭鑳姐€佺幆淇濄€佸彲鏇夸唬楂樿兘鑰楀缓鏉愪骇鍝佺殑鏂板伐鑹恒€傜牬纰庣閫夐櫎閾佸悗鐨勯挗娓e惈鏈夎緝澶氱殑娓哥CaO绛夌熆鐗╄川锛岃繖浜涚熆鐗╄川鍏锋湁姘寸‖鎬с€傚綋閽㈡福涓庨珮鐐夋按娣熆娓i厤鍚堜娇鐢ㄦ椂锛岄挗娓f按鍖栨瀽鍑虹殑Ca(OH)2鑳藉鐭挎福璧峰埌纰辨€ф縺鍙戜綔鐢紝鑰岀熆娓e張鍙秷闄ら挗娓d腑娓哥CaO鐨勪笉鑹奖鍝嶏紝鏀瑰杽浜у搧鐨勪綋绉畨瀹氭€с€傜牬纰庣閫夐櫎閾佸悗鐨勯噸鐭挎福鍏锋湁璐ㄥ瘑銆佷綋绉畨瀹氭€уソ鐨勭壒鐐癸紝鍙彇浠g鐭炽€侀粍鐮傜敤浣滃缓鏉愪骇鍝佺殑绮楃粏楠ㄦ枡銆傛湰鏂囦互閽㈡福娣峰悎鏉愩€侀挗娓g熆娓f贩鍑濆湡鐮栧拰鍐堕噾娓h捀鍘嬪姞姘旂爩鍧椾负渚嬶紝鍒嗘瀽浜嗗喍閲戞福缁煎悎鍒╃敤涓庤妭鑳界幆淇濈殑鍏崇郴銆�
1銆侀挗娓f贩鍚堟潗鐨勮妭鑳界幆淇濆垎鏋�
閽㈡福搴旂敤浜庢按娉ュ伐涓氬湪鎴戝浗宸叉湁30浣欏勾鐨勫巻鍙诧紝鎹笉瀹屽叏缁熻锛屽浗鍐呯洰鍓嶆瘡骞村彲浣跨敤閽㈡福娣峰悎鏉�1000涓囧惃銆傜敤浜庣敓浜ф按娉ョ殑閽㈡福娣峰悎鏉愬繀椤荤儤骞诧紝鑰岀洰鍓嶆櫘閬嶇殑鐑樺共鏂规硶鏄敤姹借溅灏嗗惈姘寸害12%鐨勯挗娓f贩鍚堟潗杩愰€佽嚦姘存偿鍘傦紝鐒跺悗鐢ㄧ叅鐕冪儳浜х敓鐑杩涜鐑樺共銆傝杩囩▼涓€鏂归潰澧炲姞浜�10%鐨勬苯杞﹁繍杈撻噺锛屽彟涓€鏂归潰闇€瑕佹秷鑰楃叅鐐祫婧愩€傜幇鍦ㄥ埄鐢ㄩ挗娓d綔涓烘按娉ユ贩鍚堟潗鐨勭粡娴庢柟寮忔槸鍒╃敤鐐奸搧鍘備骇鐢熺殑鍓骇鍝佲€旈珮鐐夌叅姘斿氨鍦拌繘琛岀儤骞诧紝杩欐牱鍙ぇ骞呰妭鐪佹苯杞﹁繍杈撻噺鍜岀煶娌广€佺叅鐐瓑璧勬簮銆傞噰鐢ㄧ偧閾佸巶浜х敓鐨勫壇浜у搧鈥旈珮鐐夌叅姘斿氨鍦拌繘琛岀儤骞诧紝姣忓惃閽㈡福鍒濇按鍒�12%鐑樺共鑷崇粓姘村垎2%闇€150绔嬫柟绫崇殑楂樼倝鐓ゆ皵锛堢儹鍊间互3500鍗冨崱/绔嬫柟绫宠锛夛紝姣忓勾1000涓囧惃閽㈡福娣峰悎鏉愰渶15浜跨珛鏂圭背鐨勯珮鐐夌叅姘旓紝鎶樺悎鏍囩叅75涓囧惃锛堟爣鐓ょ儹鍊肩害7000鍗冨崱/鍗冨厠璁★級锛涙瘡骞�1000涓囧惃閽㈡福娣峰悎鏉愶紙杩愯窛浠�30鍏噷璁★級鍙妭鐪佹苯杞﹁繍杈撶敤娌归噺45涓囧崌锛堥噸鍨嬭浇閲嶆苯杞︿互姣忓惃閽㈡福娌硅€椾互1.5鍗�/100鍏噷璁★級銆佺叅鐐敤閲�75涓囧惃銆�
2銆侀挗娓g熆娓f贩鍑濆湡鐮栫殑鑺傝兘鐜繚鍒嗘瀽
閽㈡福鐭挎福娣峰嚌鍦熺爾涓昏鏄互閽㈡福鐭挎福閰嶅埗鐨勭爩绛戞按娉ヤ负鑳跺嚌鏉愭枡锛屼互閽㈡福銆佹按娣熆娓e拰楂樼倝閲嶇熆娓d负楠ㄦ枡锛屽啀鎺哄叆涓€瀹氶噺鐨勬坊鍔犲墏锛岄噰鐢ㄥ崐骞叉硶鍘嬪埗鎴愬瀷銆侀挗鍘備綑鐑捀姹藉吇鎶ょ殑鏂规硶鐢熶骇鍑烘潵鐨勪竴绉嶅喍閲戞福鐮栥€傝鐢熶骇宸ヨ壓浜�2006骞村湪鏂颁綑閽㈤搧鑲′唤鏈夐檺鍏徃鐨勫缓鏉愮敓浜х嚎涓婂凡缁忓疄鏂姐€傜粡杩囩悊璁哄拰瀹炶返璇佹槑璇ュ伐鑹虹敓浜у嚭鏉ョ殑閽㈡福鐭挎福娣峰嚌鍦熺爾鍚勯」鎬ц兘鎸囨爣鍧囦紭浜庡浗瀹舵爣鍑嗚姹傦紝鑰屼笖浜у搧鎴愭湰浣庯紝鐢熶骇鍘熸枡90%浠ヤ笂閲囩敤閽㈠巶搴熷純鐨勫喍閲戞福锛岄噰鐢ㄩ挗鍘備綑鐑捀姹藉吇鎶わ紝绗﹀悎鍥藉鑺傝兘鐜繚鐨勪骇涓氭斂绛栥€備互鏂颁綑閽㈤搧鑲′唤鏈夐檺鍏徃骞翠骇30涓囩珛鏂圭背鐨勯挗娓g熆娓f贩鍑濆湡鐮栫敓浜х嚎涓轰緥锛屾瘡骞村彲娑堣€楅挗娓g害 11涓囧惃銆佺熆娓�11涓囧惃銆侀噸鐭挎福22涓囧惃锛屽彲涓洪挗鍘傚埄鐢ㄥぇ閲忕殑鍐堕噾娓e苟浜х敓鑹ソ鐨勭粡娴庢晥鐩娿€�
閽㈡福鐭挎福娣峰嚌鍦熺爾鐢熶骇浣跨敤鐨勮兌鍑濇潗鏂欓噰鐢ㄥ喍閲戞福鑷厤鐨凪22.5鐮岀瓚姘存偿锛屾棤闇€閲囩敤楂樿兘鑰楃殑PS32.5浠ヤ笂鐨勬垚鍝佹按娉ャ€傞挗娓g熆娓f贩鍑濆湡鐮栫殑楠ㄦ枡灏卞湴閲囩敤閽㈠巶鐨勫喍閲戞福锛屾瘡骞村彲鍑忓皯36涓囧惃鐮傜煶鐨勫紑閲囧紑鎸栭噺鍜屾苯杞﹁繍杈撻噺銆傞挗娓g熆娓f贩鍑濆湡鐮栫殑鍏绘姢閲囩敤閽㈠巶浣欑儹钂告苯鍏绘姢锛岃妭鐪佷簡鐓ょ偔璧勬簮銆傝鏉$敓浜х嚎闆嗘垚浜嗗喍閲戞福銆佷綑鐑捀姹姐€侀珮鐐夌叅姘旂瓑鍐嶇敓璧勬簮鐨勭患鍚堝埄鐢紝姣忓勾鍙妭鐪佺爞鐭宠繍杈擄紙杩愯窛浠�30鍏噷璁★級鐢ㄦ补閲�16.2涓囧崌锛堥噸鍨嬭浇閲嶆苯杞︽瘡鍚ㄩ挗娓f补鑰椾互1.5鍗�/100鍏噷璁★級锛涙瘡骞村彲鑺傜渷鎴愬搧姘存偿9涓囧惃锛屾姌鍚堟爣鐓ょ害1涓囧惃锛堟垚鍝佹按娉ョ叅鑰椾互 110鍏枻/鍚ㄨ锛夛紱鍚屾椂姣忓勾鍙噺灏�2浜垮潡绮樺湡鏍囩爾鐨勭敓浜т娇鐢紝鎶樺悎鏍囩叅3涓囧惃锛堢矘鍦熺爾鐓よ€椾互100鍏枻/绔嬫柟绫宠锛夈€傝嫢鍏ㄥ浗100瀹跺ぇ鍨嬮挗閾佸巶骞冲潎姣忓寤鸿涓€鏉�30涓囩珛鏂圭背鐨勯挗娓g熆娓f贩鍑濆湡鐮栫敓浜х嚎锛屾瘡骞村彲鍒╃敤鍐堕噾娓e叡绾�4400涓囧惃锛岃妭鐪佹苯杞﹁繍杈撶敤娌归噺1620涓囧崌銆佺叅鐐敤閲� 400涓囧惃銆傝繖鏍锋棦澶ч噺鍒╃敤浜嗛挗鍘傚簾寮冪殑鍐堕噾娓e張澶ч噺浠f浛浜嗙矘鍦熺爾鐨勫競鍦猴紝淇濇姢浜嗚€曞湴锛涘悓鏃剁敱浜庨挗娓g熆娓f贩鍑濆湡鏄竴绉嶅厤鐑х爾锛屽洜鑰屽彲浠ヨ妭鑳介檷鑰椼€�
3銆佸喍閲戞福钂稿帇鍔犳皵鐮屽潡鐢熶骇鐨勮妭鑳界幆淇濆垎鏋愬喍閲戞福钂稿帇鍔犳皵鐮屽潡鏄皢閽㈡福銆佺熆娓e姞姘寸(鎴愭祮鏂欙紝鍔犲叆绮夌姸澶嶅悎娣诲姞鍓傦紝閫傞噺鐭宠啅鍜屽彂姘斿墏锛岀粡鍙戞皵銆侀鍏汇€佸垏鍓层€佽捀鍘嬬瓑宸ュ簭鍚庡埗鎴愮殑鍔犳皵鐮屽潡鍒跺搧銆傝宸ヨ壓鐢熶骇鍑烘潵鐨勫喍閲戞福钂稿帇鍔犳皵鐮屽潡鎬ц兘鑹ソ锛岀鍚堝伐涓氫笌姘戠敤寤虹瓚闇€瑕侊紝鑰屼笖鑳藉ぇ閲忓湴娑堣€楀喍閲戞福銆傝宸ヨ壓閲囩敤鐨勫師鏉愭枡涓�90%浠ヤ笂涓哄喍閲戞福锛屽吇鎶よ捀姹芥槸閲囩敤鐐奸搧鍘傜殑鍓骇鍝佲€旈珮鐐夌叅姘斾綔涓虹噧鏂欎骇鐢熺殑锛屼骇鍝佹垚鏈綆銆傝鐢熶骇绾挎瘡骞存秷鑰楃害7500涓囩珛鏂圭背鐨勯珮鐐夌叅姘旓紙鐑€间互3200鍗冨崱/绔嬫柟绫宠锛夛紝鎶樺悎鏍囩叅绾�3.4涓囧惃锛堟爣鐓ょ儹鍊间互7000鍗冨崱/鍏枻璁★級銆備互婀樻江閽㈤搧闆嗗洟鏈夐檺鍏徃骞翠骇 30涓囩珛鏂圭背鐨勫喍閲戞福钂稿帇鍔犳皵鐮屽潡鐢熶骇绾夸负渚嬶紝姣忓勾鍙秷鑰楅挗娓g害14涓囧惃銆佺熆娓�14涓囧惃锛屽彲鍒╃敤澶ч噺鐨勫喍閲戞福骞朵骇鐢熻壇濂界殑缁忔祹鏁堢泭銆傝嫢鍏ㄥ浗100瀹跺ぇ鍨嬮挗鍘傚钩鍧囨瘡瀹跺缓璁句竴鏉�30涓囩珛鏂圭背鐨勫喍閲戞福钂稿帇鍔犳皵鐮屽潡鐢熶骇绾垮氨鍙埄鐢ㄥ喍閲戞福鍏辩害3000涓囧惃锛屾瘡骞磋妭鐪佺叅鐐敤閲�340涓囧惃銆�
浜屻€佸喍閲戝皹娉ョ殑璧勬簮鍖栧鐞嗕笌缁煎悎鍒╃敤
锛堜竴锛夋妧鏈垎鏋�
閽㈤搧鍘傚喍閲戝皹娉ヤ富瑕佸寘鎷細楂樼倝鐡︽柉娉ャ€佽浆鐐夊皹娉ュ強闄ゅ皹鐏扮瓑銆�
鐐奸挗杩囩▼涓紝鍔犲叆鍒拌浆鐐夊唴鐨勫師鏂欐湁2%宸﹀彸浼氳浆鍙樹负绮夊皹锛岃浆鐐夊皹鐨勫彂鐢熼噺绾︿负20鍏枻/鍚ㄣ€傜偧閽㈢矇灏樹富瑕佺敱姘у寲閾佺粍鎴愶紝鍗�70%锝�95%锛屽叾浠栨哀鍖栫墿鏉傝川锛堝 CaO銆乑nO绛夛級鍗�5%锝�30%銆傝浆鐐夌偧閽㈠皹娉ヤ竴鑸彲鐢ㄤ綔鐑х粨鐨勫師鏂欙紝浣嗛攲鍦ㄧ偧閾佽繃绋嬩腑灞炴湁瀹冲厓绱狅紝鍥犲湪楂樼倝鍐剁偧鐨勮繃绋嬩腑鏄撳舰鎴愮倝鐦よ€屽奖鍝嶇倝鏂欏拰姘斾綋鐨勬祦鍔紝鍥犳杞倝灏樻偿鍦ㄥ洖鏀惰繃绋嬩腑锛屽彲閫氳繃閫夌熆娉曞洖鏀剁矇鐭垮拰瀵� C銆乑n鐨勫熬娉ャ€傚湪鐑х粨娣峰悎鏂欎腑鍔犲叆OG娉ユ偓娴恫鏈夊埄浜庢贩鍚堟枡鍒剁矑锛岄殢OG娉ラ厤閲忕殑澧炲姞锛屾贩鍚堟枡涓�1mm绮掔骇姣旂巼杩呴€熼檷浣庯紝鏈夊埄浜庢敼鍠勬贩鍚堟枡閫忔皵鎬с€佹彁楂樹骇閲忋€侀檷浣庢垚鏈強淇濇姢鐜銆�
楂樼倝鐡︽柉娉ョ殑缁勬垚涓昏鏄害20%鐨勬哀鍖栭搧銆�23%鐨勭⒊銆�1%锝�5%鐨勯攲锛岃繕鏈夎緝澶氱殑CaO銆丼iO2銆丄l2O3 绛夋哀鍖栫墿銆傞珮鐐夌倝灏樺彂鐢熼噺绾︿负25kg/t銆傞珮鐐夌摝鏂偿棰楃矑杈冪粏锛屽皬浜�200鐩殑鍗�90%浠ヤ笂銆傞珮鐐夌摝鏂偿鐨勭壒寰佹槸鍚攲銆侀搧銆佺⒊銆佹按鍒嗗惈閲忛珮锛岄绮掔粏锛岄攲涓昏瀛樺湪浜庤緝灏忕殑棰楃矑涓€傚楂樼倝鐡︽柉娉ャ€佺摝鏂伆鍙噰鐢ㄦ按鍔涘垎绂婚€夌熆娉曟彁鍙栧瘜Zn銆佸瘜C灏炬偿浣滀负璧勬簮鍥炴敹鍒╃敤銆�
鐩墠鎴戝浗澶у瀷浼佷笟鐨勫喍閲戝皹娉ュ洖鏀跺埄鐢ㄧ巼鍙揪 100%銆傝浆鐐夋偿銆侀櫎灏樼伆鍙婄摝鏂偿鍒╃敤宸ヨ壓鍜屾妧鏈浜庤緝鍏堣繘姘村钩锛屽彲涓轰紒涓氬甫鏉ュ緢濂界殑缁忔祹鏁堢泭銆�
锛堜簩锛夊伐鑹哄垎鏋�
鍐堕噾灏樻偿缁煎悎鍒╃敤宸ヨ壓娴佺▼濡備笅锛�
锛�1锛夎浆鐐夋偿銆侀櫎灏樼伆骞叉硶鍒╃敤宸ヨ壓
杞倝娉ャ€侀櫎灏樼伆鈫掔儳缁撹繑鐭库啋娣峰悎鏂欏姞宸ュ満銆�
锛�2锛夎浆鐐夋偿婀挎硶鍒╃敤宸ヨ壓
杞倝娉モ啋鎼呮媽姹犫啋绠¢亾鈫掔儳缁撻厤鏂�鐨甫鈫掕浆鐐夋偿鐑樺共+姘у寲閾佺毊+鍖栧绮樼粨鍓傗啋鎼呮媽娣峰寑鈫掑姞鍘嬫垚鐞冣啋鍏ョ倝骞茬嚗鈫掔悆鍥㈢熆銆�
锛�3锛夌摝鏂偿鍒╃敤宸ヨ壓
鐡︽柉娉モ啋閲嶉€夆啋閾佺簿绮夆啋鐑х粨鍘傗啋鍚攲娉モ啋鐏硶鎻愰攲銆�
涓夈€佸喍閲戝浐浣撳簾寮冪墿璧勬簮鍖栧鐞嗕笌缁煎悎鍒╃敤鐨勫彂灞曡秼鍔�
杩戝勾鏉ワ紝鍥藉唴鍚勯挗閾佷紒涓氫互鍥轰綋搴熷純鐗╁叏鍒╃敤銆侀浂鎺掓斁涓虹洰鏍囷紝鍙栧緱浜嗗緢澶ц繘姝ワ紝涓撲笟鍖栭泦涓鐞嗕笌澶氱绠$悊浣撳埗鐩哥粨鍚堜篃鍒濊鎴愭晥銆傜洰鍓嶏紝鍚勯挗閾佷紒涓氬熀鏈畬鎴愪簡宸ヤ笟鍥轰綋搴熷純鐗╀腑鍚搧璧勬簮鐨勫叏閲忓鐞嗗拰鍥炴敹鍒╃敤锛屽埄鐢ㄨ矾寰勪负锛氬浐搴熻祫婧愬洖鏀垛啋鐑х粨鈫掗珮鐐夆啋鐐奸挗鈫� 杞ч挗锛屽嵆鎵€璋撳ぇ寰幆鍒╃敤妯″紡锛屼絾鍏跺埄鐢ㄤ粛澶勪簬浣庡眰娆°€佷綆鏁堢巼銆佷綆闄勫姞鍊笺€佷綆姊骇鐨勫埄鐢紝琛ㄧ幇涓虹粡娴庢晥鐩婂拰鐜繚鏁堢泭鐨勯潪鏈€浼樺寲锛屽姘у寲閾佺毊銆佽浆鐐夋偿鍙婄摝鏂偿鐨勫埄鐢ㄧ瓑锛屾晠鍦ㄥ浐搴熸繁搴﹀紑鍙戝拰楂樹环鍊煎埄鐢ㄦ柟闈㈣繕鏈夊緟杩涗竴姝ョ爺绌朵笌鍙戝睍銆�
锛堜竴锛夊姞寮洪挗娓g啍鍓傛福閰嶆枡瀵圭儳缁撶熆鍝佷綅涓庤川閲忕殑鐮旂┒
閽㈡福缁忕牬纰庣閫夊悗鍥炴敹鐨勭啍鍓傛福涓€鐩翠互鏉ヤ负鐑х粨鍘傚埄鐢紝閰嶆瘮涓€鑸湪115%宸﹀彸銆備絾鐔斿墏娓g殑閰嶅叆浼氬奖鍝嶇儳缁撶熆鐨勫搧浣嶅拰璐ㄩ噺锛屼富瑕佹槸鐢变簬鎵€閰嶉挗娓g殑鍔犳按娑︽箍鎬ц兘鍜岄€犵悆鎬ц兘杈冮搧鐭跨矇宸紝鐑х粨鍘傜敤閲忔湁闄愮敋鑷冲仠姝娇鐢紝浣跨啍鍓傛福鍒╃敤涓庡閿€鍘嬪姏澧炲ぇ銆傚洜姝ゅ簲鍔犲己鐑х粨鐭块厤鍔犻挗娓g啍鍓傛福寮哄寲鍒剁矑鐨勮瘯楠岀爺绌讹紝鎺㈣鍚堥€傜殑閽㈡福鐔斿墏娓i厤鍏ラ噺锛屼繚璇佺儳缁撻€熷害銆佺儳缁撶熆寮哄害銆佹垚鍝佺巼銆佸埄鐢ㄧ郴鏁般€佺儳缁撶熆杩樺師鎬х瓑鎸囨爣绗﹀悎瑕佹眰銆�
锛堜簩锛夎繘涓€姝ュ紑鍙戦挗娓e湪姘存偿鐢熶骇涓殑搴旂敤
搴旇繘涓€姝ュ姞寮洪挗娓g敤浜庢按娉ュ巶鐨勭敓浜ц瘯楠岀爺绌跺拰鐢熶骇鎬ч獙璇侊紝鎺㈢储閽㈡福姘存偿鐢熶骇鏈€浣冲伐鑹烘帶鍒跺弬鏁帮紝鎻愰珮閽㈡福鎺哄叆閲忋€�
锛堜笁锛夊紑鍙戦挗娓g矇鐢熶骇
鍒╃敤姘存偿鍜屾贩鍑濆湡涓殑閽㈡福绮夋槸鎴戝浗閽㈡福楂樹环鍊艰祫婧愬寲鍒╃敤鐨勬渶浣抽€斿緞銆傜粏搴﹀湪姣旇〃闈㈢Н涓�400m2/kg鐨勯挗娓e彲绛夐噺鍙栦唬10%锝�30%鐨勬按娉ワ紝鐩存帴鐢ㄤ簬娣峰嚌鍦熷缓绛戝伐绋嬶紝鍙彁楂樻贩鍑濆湡鍚庢湡寮哄害锛屾彁楂樿€愮(鎬с€佹姉鍐绘€с€佽€愯厫铓€鎬ц兘锛屾垚鏈瘮姘存偿浣�30%锛屽彲闄嶄綆宸ョ▼閫犱环锛屾槸楂樻€ц兘楂樿€愪箙鎬ф贩鍑濆湡鐨勫師鏂欍€傜洰鍓嶏紝鍏ㄥ浗閽㈡福绮夊勾浜ч噺宸茶揪300涓囧惃锛屼骇鍝佷富瑕佺敤浜庡伐绋嬪缓璁俱€傚湪寮€鍙戦挗娓g矇鐢熶骇涓鍔犲己绮夌(璁惧鐨勯€夋嫨鍜岀矇纾ㄥ伐鑹虹殑鎺у埗銆�
锛堝洓锛夐挗娓d綔閬撹矾鏉愭枡鍜屽缓绛戞潗鏂�
鍏抽敭鏄瑙e喅閽㈡福鐨勭ǔ瀹氭€ч棶棰橈紝闇€瑕佸鐜版湁鐑臣娉曟福澶勭悊宸ヨ壓杩涜鏀硅繘锛屽簲鍔犲己閽㈡福鐑剸娉曞鐞嗗伐鑹哄強瑁呭绛夋妧鏈爺绌躲€傛箹鍗楁稛閽㈣浆鐐夐挗娓g儹鐒栨硶澶勭悊鍙婃按纭€ч挗閾佹福鍏嶇儳鎵块噸鐮栫殑寮€鍙戠爺绌惰揪鍒颁簡杈冨ソ鏁堟灉銆傜編鍥� Alfred澶у鐨凙grwal 聽G绛変汉鍒╃敤閽㈡福鍒堕€犲嚭姣旀櫘閫氱幓鐠冭€愮(鑰愯殌鐨勫瘜CaO鐨勫井鏅剁幓鐠冦€�
锛堜簲锛夊姞蹇摝鏂偿鐨勬绾у紑鍙戝埄鐢�
鐡︽柉娉ラ噸閫夋彁閾佸悗锛屽叾灏炬偿涓⒊鍚噺楂樿揪35%锛屽鐡︽柉娉ヤ腑纰冲厓绱犲姞浠ュ洖鏀朵唬鏇块珮鐐夊柗鍚圭敤鏃犵儫鐓ゃ€備娇鐢ㄥ洖鏀舵柊宸ヨ壓鍙洖鏀剁偔绮夈€�
锛堝叚锛夊紑鍙戝喍閲戝皹娉ョ敓浜х偧閽㈢敤鍐峰嵈鍓傘€侀€犳福鍓�
杞倝娉ャ€侀櫎灏樼伆銆佹哀鍖栭搧鐨瓑鐨勭患鍚堝埄鐢ㄨ繃鍘讳竴鐩撮噰鍙栤€滃洖鏀�-鍔犲伐-鐑х粨鍒╃敤鈥濆伐鑹鸿矾绾匡紝涓嶆槸鍥哄簾璧勬簮鐨勬繁搴﹀紑鍙戦珮闄勪环鍊肩殑鍒╃敤鏂瑰紡銆傚埄鐢ㄨ浆鐐夋偿绛夊喍閲戝皹娉ョ敓浜х鍚堢偧閽㈣姹傜殑鍐峰嵈鍓傘€侀€犳福鍓傦紝浣垮喍閲戝皹娉ョ殑鍒╃敤宸ヨ壓浠庤繃鍘荤殑鈥滃簾鏂�-鐑�-閾�-閽⑩€濆ぇ寰幆鍒╃敤鍚戔€滃簾鏂�-閽⑩€濆皬寰幆鍒╃敤杞彉锛屼娇绯荤粺鑳借€楁洿灏戙€佹薄鏌撴洿灏忋€佹垚鏈洿浣庛€佹晥鐩婃洿濂姐€�
鎬讳箣锛岃繎鍑犲勾鍥藉榧撳姳鍙戝睍寰幆缁忔祹锛屽彿鍙妭鑳介檷鑰椼€傚喍閲戝浐浣撳簾寮冪墿璧勬簮鍖栧鐞嗕笌缁煎悎鍒╃敤鏄渶鍏蜂唬琛ㄦ€х殑璧勬簮寰幆鍒╃敤銆佽妭鑳姐€佺幆淇濇帾鏂戒箣涓€锛屼篃鏄挗閾佸伐涓氬疄鐜板仴搴枫€佸彲鎸佺画鍙戝睍鐨勪竴涓噸瑕佷繚闅溿€傚埄鐢ㄥ喍閲戞福鐢熶骇寤烘潗浜у搧鏃㈠ぇ閲忓埄鐢ㄤ簡宸ヤ笟搴熸福鍙婁綑鐑捀姹姐€侀珮鐐夌叅姘旂瓑鍐嶇敓璧勬簮锛屽張鑳界敓浜у嚭婊¤冻甯傚満闇€瑕佺殑缁胯壊寤烘潗浜у搧锛岃繖鏍风殑椤圭洰鍏锋湁鑹ソ鐨勭幆澧冩晥鐩娿€佺粡娴庢晥鐩婂拰绀句細鏁堢泭銆傚洜姝ゅ簲缁х画鍔犲ぇ鐮旂┒骞舵帹骞垮喍閲戝浐浣撳簾寮冪墿璧勬簮鍖栧鐞嗕笌缁煎悎鍒╃敤鎶€鏈紝涓烘垜鍥介挗閾佷紒涓氱殑鍋ュ悍銆佸彲鎸佺画鍙戝睍鍋氬嚭璐$尞銆�
涓撲笟鐨勪簨浜ょ粰涓撲笟鍥㈤槦
13759951385(寰俊)聽
瑗垮畨鐭挎簮
瑗垮畨鐭挎簮鏈夎壊鍐堕噾鐮旂┒闄�
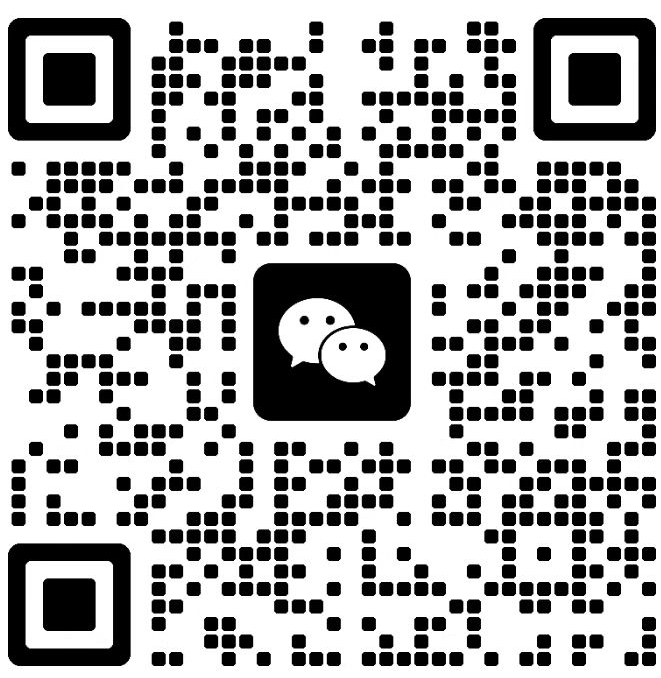