中国铸造行业媒体联盟成员之一的热加工行业论坛(www.rjghome.com)——热加工行业人员的网上技术交流家园。以冶炼、铸造、锻压、焊接、热处理、理化检测等相关知识为主,以机加工、电脑设计等知识为辅的行业技术网站。点击标题下蓝字“热加工行业论坛”免费关注,我们将为您提供铸造、锻造、热处理、焊接方面知识的延伸阅读。
【荐读】混砂工艺和芯砂对粘土湿型砂性能的影响
通过采用不同的混砂工艺方案,随着混砂时间的改变,研究了混砂工艺对型砂性能的影响;同时,采用不同的芯砂加入方案,随着加入量的改变,研究了芯砂对型砂性能的影响。结果表明,型砂各种性能均随混砂工艺和混砂时间的不同而变化,也会随着芯砂加入工艺和加入量的不同而改变。为最终确定和选用混砂工艺和芯砂的加入量提供了指导依据。
砂型铸造是最常见的铸造方法,粘土湿型砂因具有砂型无需烘干、不存在硬化过程、混制效率高、便于组织流水线生产、材料成本和混砂成本低等特点,使其成为使用最方便、最广泛的造型材料,其用量占所有砂型铸造使用量的70%~80%。想要生产出优良的湿型砂铸件,必须要先获得优良的湿型砂。品质优良的湿型砂,除了需要选用优质的原材料和较为理想的砂处理设备以外,还必须要有合理的混制工艺,其中包括回用砂的预处理、型砂配比、混砂工艺和混砂时间等。所以混砂工艺和回用砂质量对粘土湿型砂性能都起着决定性的影响。
我公司目前有多个砂型铸造车间,每个车间配备的铸造设备和所生产的铸件结构、铸件材质以及生产过程的控制和检测方法均无明显差异。但是,各个车间的芯砂在型砂系统中的占比和混砂参数却各有不同,因此混砂工艺也不尽相同,生产出的铸件因为型砂质量的原因导致的铸造缺陷也各不相同、废品率相差甚远。本文研究了混砂工艺随着混砂时间的改变对型砂性能的影响,研究了型砂混入芯砂后的混制工艺,并揭示了芯砂对型砂性能的影响规律。为各个车间制定统一的混砂工艺、使型砂性能趋于一致,减少因为型砂质量问题导致的砂眼、粘砂、涨型和气孔等铸造缺陷的产生,尤其是在降低铸件废品率方面作出了积极的贡献。
1 试验用原材料、型砂配方和检测设备
1.1 试验用原材料
原砂为内蒙古某厂生产的硅砂,型号为ZGS90-70/140;膨润土为钠基膨润土,型号为PNa-12-35;煤粉选择铸造用煤粉,型号为SMF-30。硅砂、膨润土和煤粉的性能指标如表1、表2和表3所示。芯砂是在浇注后,从落砂工序经收集、回收而来的,呋喃树脂热芯盒砂和酚醛树脂壳芯砂原砂的性能指标分别见表4和表5所示。
表1 硅砂性能指标
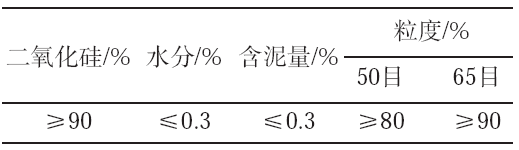
表2 膨润土性能指标
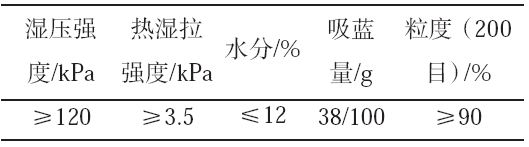
表3 煤粉性能指标
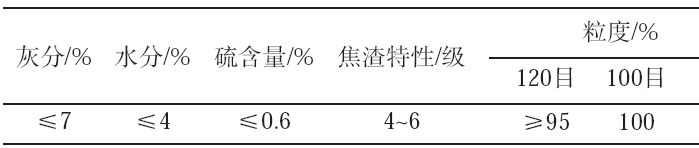
表4 呋喃树脂热芯盒砂性能指标

表5 酚醛树脂壳芯砂性能指标

1.2 型砂配方和检测设备
根据试验用混砂作业指导书的要求,混砂工艺试验用型砂配方如表6所示;芯砂加入量实验用型砂配方如表7所示。
表6 混砂工艺试验用型砂配方
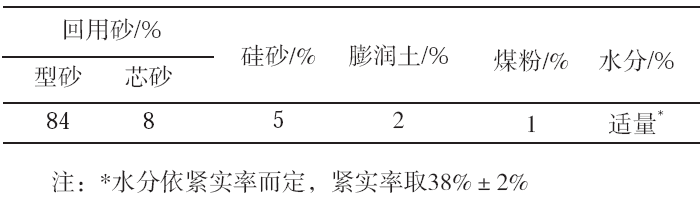
表7 芯砂试验用型砂配方
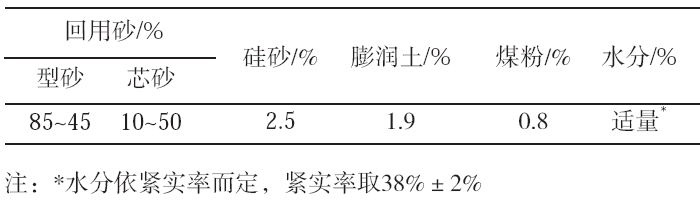
型砂在SHN-1碾轮式混砂机上进行混制。在不同的取样时间节点,从混砂机出砂口对经过混制的型砂进行取样并检测。型砂性能分别在SQR湿拉强度测试仪、SWY-2型砂强度试验仪,STZ直读透气性测定仪和SPO-1型破碎指数测定仪上进行检测,检测结果取3个相近试验数据的算术平均值。
2 试验方案
2.1 混砂工艺试验
长期以来,一些铸造车间采用的混砂工艺都是以往传统的先干混后湿混的混制工艺。即:回用砂+新砂+煤粉+膨润土先干混一段时间,再加水进行湿混。这种混砂工艺的明显缺点主要有以下方面。
(1)污染环境,未加水先混干料时,粉尘容易飞扬,是铸造车间污染的主要来源。
(2)干料混匀后再加水,虽然加水时也是均匀淋入,但却很难使水分均匀分散,因为水滴的表面张力和粘土的亲水力,水滴落下的地方很快就会被粘土聚集,从而形成较大的粘土球,将这些粘土球碾碎并使其均匀地分布于砂粒表面是比较困难的,混砂时间会增加,需要的能量也很大。
(3)在干混过程中粉尘容易在混砂机夹角和碾盘周围堆积,加水后膨润土和煤粉浸润较慢,需要很长的时间才能混匀。
(4)有效膨润土和煤粉在干混时容易被除尘设备抽走,造成资源浪费。
为了解决上述混砂工艺的缺点,将试验的混砂工艺定为以下两种方案,每2 min作为一个取样周期,通过检测结果对比和研究各混砂工艺的优势和不足,从中确定最为合适的混砂工艺。
方案1:(回用砂+原砂+膨润土+煤粉)混1min+水再混制。
方案2:[回用砂+原砂+(65%)水)]混1min+[膨润土+煤粉+(剩余所需)水]再混制。
2.2 芯砂加入量试验
在铸造生产过程中,落砂后的芯砂有两种状态存在:一种是经过高温作用后充分燃烧的芯砂,称为浇注后芯砂;另一种是受热不均匀、不充分、树脂尚未完全燃烧和分解,以及未与高温金属直接接触的未燃烧和分解的芯砂,称为未浇注芯砂。
为了分析芯砂在型砂系统中的作用,研究芯砂不同加入量对型砂性能的影响,将从落砂处经过分选处理后、收集到的呋喃树脂热芯盒砂和酚醛树脂壳芯砂的以上两种状态作为回用砂的一部分,在混砂过程中分别同回用砂一起加入混砂机内,加入的比例为10%~50%(在实际铸造生产过程中,>50%的芯砂加入量或者说型砂一半以上都是由芯砂组成的,这种情况几乎不存在,没有研究价值。因此,仅研究了从10%到50%的芯砂加入量),每10%作为一个取样周期。具体试验工艺方案为:
方案1:[(回用砂+未浇注呋喃树脂热芯盒砂)+原砂+(65%)水)]混2min+[膨润土+煤粉+(剩余所需)水]再混制。
方案2:[(回用砂+浇注后呋喃树脂热芯盒砂)+原砂+(65%)水)]混2min+[膨润土+煤粉+(剩余所需)水]再混制。
方案3:[(回用砂+未浇注酚醛树脂壳芯砂)+原砂+(65%)水)]混2 min+[膨润土+煤粉+(剩余所需)水]再混制。
方案4:[(回用砂+浇注后酚醛树脂壳芯砂)+原砂+(65%)水)]混2 min+[膨润土+煤粉+(剩余所需)水]再混制。
3 试验结果及分析
3.1 混砂工艺对型砂性能的影响
3.1.1 混砂工艺对热湿拉强度的影响
混砂工艺对热湿拉强度的影响见图1。由图1可以看出,方案1和方案2的热湿拉强度在型砂混制4min时趋于一致;但随着混砂时间的延长,两种方案的热湿拉强度均呈上升趋势。方案2的上升速率更快,到混砂8min左右的时候已达峰值,后续再增加混砂时间其热湿拉强度保持峰值不变;而方案1的热湿拉强度却仍缓慢上升,直到混砂时间接近12min时,方案1才与方案2的热湿拉强度趋于一致,后续再增加混砂时间,方案1的热湿拉强度也保持不变。
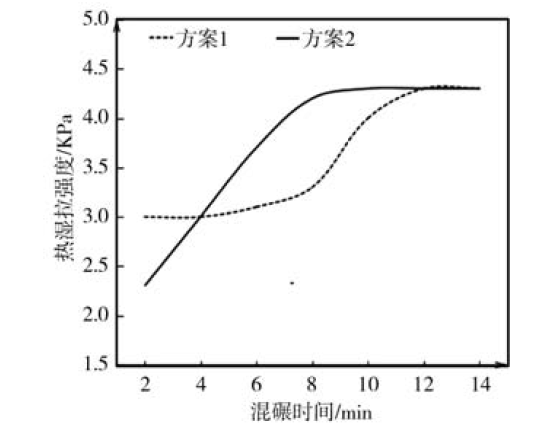
图1 混砂工艺对热热湿拉强度的影响
3.1.2 混砂工艺对湿压强度的影响
从混砂开始,两种方案的湿压强度均随混砂时间的增加而呈强劲上升趋势。不同的是方案2的湿压强度在混砂初期比方案1更高,混砂时间达到7min左右的时,方案2的湿压强度已达峰值,后续再增加混砂时间其湿压强度保持峰值不变;方案1的湿压强度仍呈上升趋势,直到混砂时间达到8min后,方案1与方案2的湿压强度趋于一致,后续再增加混砂时间,方案1方案2的湿压强度也将保持不变,见图2所示。
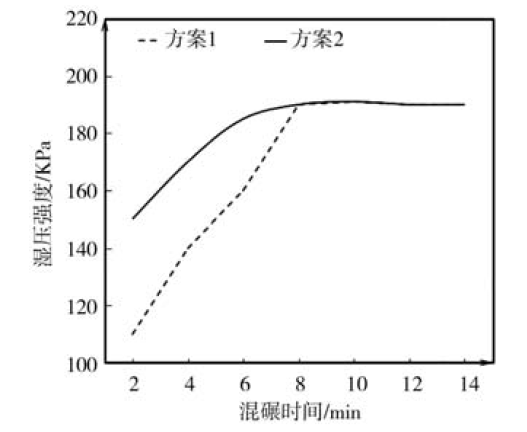
图2 混砂工艺对湿压强度的影响
3.1.3 混砂工艺对透气性的影响
混砂工艺对透气性的影响见图3所示。由图3可知,两种方案的透气性随混砂时间增加而呈平缓上升趋势,上升起点基本一致;当混砂时间达到12min时,两种方案的透气性均达到峰值,后续再增加混砂时间,透气性均保持不变。最终方案2的透气性明显高于方案1的透气性。
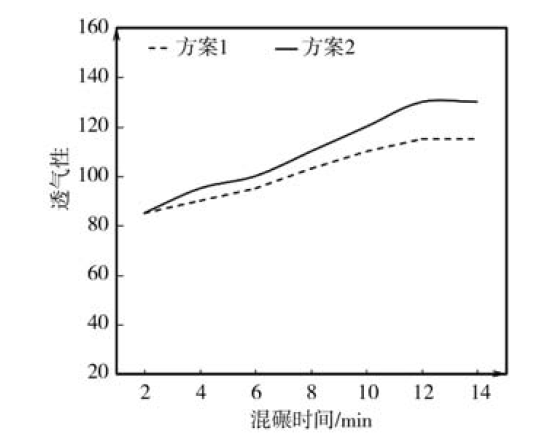
图3 混砂工艺对透气性的影响
3.1.4 混砂工艺对破碎指数的影响
方案1和方案2的破碎指数从混砂开始后的6min前均呈上升趋势,虽然方案1的起点更低,但上升速度却更快,当达到6min时两种方案的破碎指数达到了一致;从6min以后方案1的上升速度开始变得平缓,直到10min后达到峰值,之后破碎指数不再上升;从6min以后,方案2的上升速度基本保持不变,直到9 min达到峰值,同方案1的破碎指数相当,见图4所示。
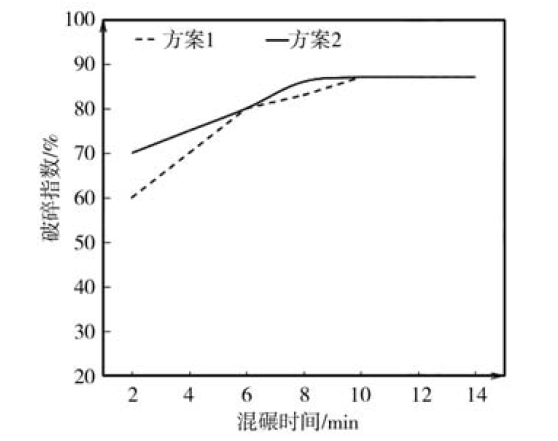
图4 混砂工艺对破碎指数的影响
3.1.5 混砂工艺方案对型砂性能影响的比较和分析
通过对混砂工艺的试验,表明两种混砂工艺均对型砂的性能起到了决定性的影响,除透气性外,两种方案的其他性能最终达到的峰值相当,均能混制出满足铸铁件生产所需的合格型砂。但是方案2的热湿拉强度、湿压强度、透气性和破碎指数达到峰值时所需的混砂时间均比方案1更短、混砂效率更高、环境污染和能量消耗更少,原因如下。
(1)当混砂8min左右的时候,方案的2热湿拉强度已达峰值,混砂7min左右的时候,方案2的湿压强度已达峰值。而方案1的混砂时间接近8min时湿压强度才达峰值、12min后热湿拉强度才达峰值,且与方案2的性能持平;两种方案的透气性基本都到12min的时候达到峰值,方案2的透气性比方案1的透气性明显高出很多;混砂9min的时候,方案2的破碎指数即达峰值,而方案1混砂时间到10min时才达峰值,与方案2的性能持平。方案2的型砂性能均能比方案1提前达到峰值或达到造型所需的指标,缩短了混砂时间,减少了能量消耗,提高了生产效率。
(2)方案2,加水先预混,避免了过多的粉尘飞扬,减少了环境污染。
经过分析和研究以上两种混砂工艺的优势和不足,结合长期的生产实践和经验积累认为:方案2的混砂工艺是最适宜的。进一步研究得知:这样先湿混的混砂工艺不仅缩短了混砂时间,提高了铸造生产效率,还使得先加入的硅砂和水分更易混匀,也使得随后加入的膨润土、煤粉和补加水分更容易被分散,且在加入膨润土和煤粉后形成的粘土球会更多、更小,不会产生大的粘土球,最重要的是碾开这些小粘土球是比较容易的,需要的能量也会小很多。
3.2 芯砂加入量对型砂性能的影响
3.2.1 芯砂对水分的影响
如表4所示,由于呋喃树脂热芯盒砂使用了呋喃1型树脂作为粘结剂,呋喃1型树脂属于水溶性高分子有机化合物,比表5所示的酚醛树脂壳芯砂的酚醛树脂更容易吸水。从图5中可以看出,未浇注的覆膜热芯盒砂会使型砂水分增加,要想使得加入覆膜热芯盒砂的型砂达到同样的强度则需要添加更多的水分,也就是说在同等水分的条件下,型砂强度将明显低于不加呋喃树脂热芯盒砂的型砂和加入酚醛树脂壳芯砂的型砂。
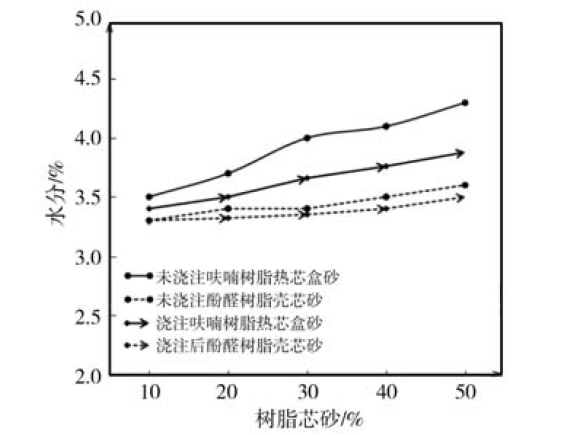
图5 芯砂对水分的影响
3.2.2 芯砂对热湿拉强度和湿压强度的影响
为了验证芯砂和型砂酸碱度对型砂性能的影响,用PHS-2酸度计(精度0.02pH)测得混砂工艺试验的型砂pH值为9.5,未浇注的呋喃树脂热芯盒砂和酚醛树脂壳芯砂的pH值分别为5.1和7.3,也就是说呋喃树脂热芯盒砂呈酸性。由于膨润土中的N+能与呋喃树脂热芯盒砂中H+发生阳离子交换现象,这种阳离子交换能够改变膨润土的膨胀性,从而降低了膨润土粒子的有效性,使得型砂强度由于芯砂酸碱度的不同而受到不同程度的损害。而酚醛树脂壳芯砂的酸碱度基本呈中性偏上状态,与膨润土几乎不发生反应,因此酚醛树脂壳芯砂对型砂的影响没有呋喃树脂热芯盒砂那么严重。
从图6和图7中可以看出:这两种芯砂都会降低型砂的强度,芯砂含量越多,型砂强度越低,而且呋喃树脂热芯盒砂对型砂强度损害比壳芯砂更严重,未浇注的芯砂又比浇注后的芯砂危害更大、且未浇注的呋喃树脂热芯盒砂对型砂强度的影响最大,这说明树脂能充分挤压和封闭膨润土粒,伤害了膨润土粒对水偶极子的吸附能力,减少了膨润土粒的表面积,树脂使膨润土的粘结能力降低了。如图8所示,通过亚甲基蓝测试也说明随着芯砂加入量的增加,型砂中的有效膨润土量显著降低。混砂过程中,在实际加入的膨润土量都为9%的前提下,芯砂加入量越多,型砂中有效膨润土越低,从而使型砂性能变差,因此未浇注的呋喃树脂热芯盒砂使型砂强度下降的更低。
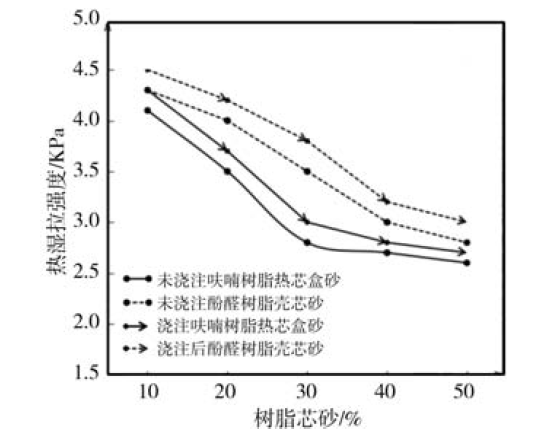
图6 芯砂对热湿拉强度的影响
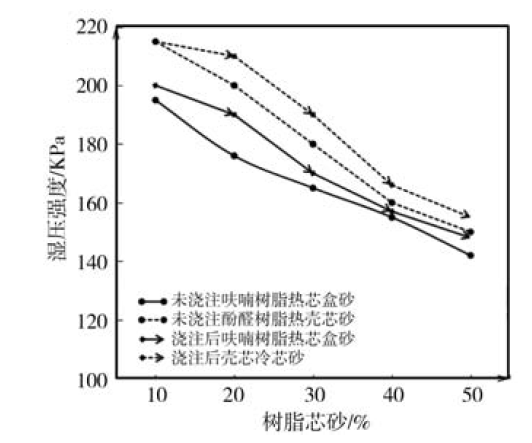
图7 芯砂对湿压强度的影响
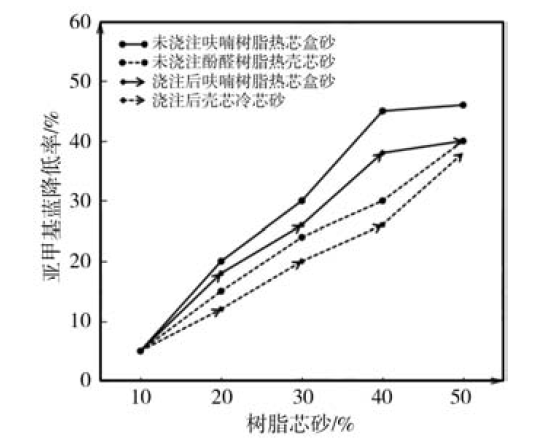
图8 芯砂对亚甲基蓝降低率的影响
3.2.3 芯砂对透气性的影响
从图9中可以看出:两种芯砂均使型砂的透气性降低,芯砂加入量越多,透气性就会越低,随着芯砂加入量的增加,这种作用越发明显,透气性越低。原因是酚醛树脂壳芯砂的砂粒比型砂更细,且未浇注的酚醛树脂壳芯砂使型砂的透气性下降的更为明显;树脂附着在膨润土粒上加大了砂粒在紧实压力下的滑动能力,使型砂的容重增大,从而使得型砂的透气性下降。
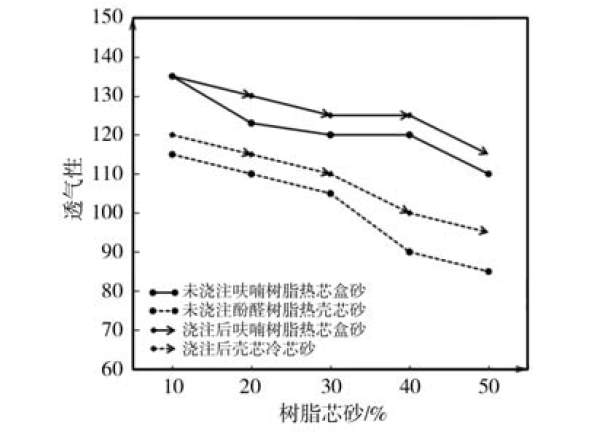
图9 芯砂对透气性的影响
3.2.4 芯砂对破碎指数的影响
从图10中可以看出,芯砂对破碎指数的影响就如同对型砂强度的影响一样,随着芯砂加入量的增加,型砂的破碎指数越来越低。
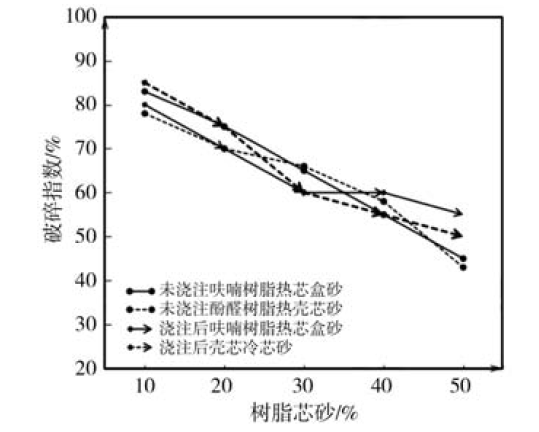
图10 芯砂对破碎指数的影响
3.2.5 芯砂的加入量对型砂性能影响的比较和分析
经高温浇注后,芯砂表面的树脂几乎可以被全部分解、燃烧掉,因此,浇注后的芯砂在10%~30%范围内变化,对型砂性能几乎没有多大的影响,仅酚醛树脂壳芯砂引起的型砂透气性下降较为明显,这是由于壳芯用砂较型砂用砂细的缘故,由此可见,芯砂经高温浇注后可作为新砂看待;从研究结果来看,对于未浇注的芯砂在型砂中的含量,最好控制在10%以内,超过20%会使型砂性能下降过多,可能满足不了造型对型砂性能的要求;对于经浇注后芯砂在30%~50%之间和未浇注芯砂≥20%的型砂,通过大量的生产实践经验积累,也可以通过控制型砂中酚醛树脂和呋喃1型树脂含量来间接控制型砂质量,酚醛树脂含量一般不超过膨润土量的8%,呋喃1型树脂含量不应超过膨润土量的3.5%。
4 结论
通过对混砂工艺和芯砂对湿型砂性能的试验研究,最终统一了各个车间的混砂工艺,使型砂性能趋于一致,便于生产过程控制,减少了铸造缺陷的产生,并在生产实践中积累了一些数据和经验。
(1)混砂时最适宜的混砂工艺是:加入回用砂和新砂的同时加入60%~70%的需水量,混匀后再一次性地加入煤粉和膨润土等粉料,然后补加剩余的水量进行二次混砂。与以往传统的先干混后湿混的混砂工艺相比,最大的优势在于:型砂性能达到峰值所需的混砂时间更短、提高了混砂效率,降低了混砂能耗,减少了环境污染。
(2)分别确定了可作为新砂看待的浇注后芯砂和未浇注芯砂在型砂中的合适比例;对于超出限度的两种状态的芯砂,可以通过控制型砂中酚醛树脂和呋喃1型树脂含量来间接控制型砂质量。
(3)型砂中树脂含量增加,还可以通过增加膨润土量来改善型砂的性能。增加膨润土含量可使型砂强度得到恢复和提高,但却会使型砂水分过高、流动性降低和透气性下降,也会增加混砂成本。另外,如果芯砂,特别是从砂芯上修下的砂芯射芯嘴、飞边毛刺和因各种原因报废的砂芯,未浇注前已下芯的废型、浇注后的砂芯芯头等未浇注的芯砂占比较大的情况下,可以在落砂后,通过分选,采用回用砂再生技术使回用砂中的树脂得到部分去除,从而改善型砂的性能。
作者:任现伟
单位:洛阳古城机械有限公司
参考文献:点击请参看原文
来源:《铸造》杂志202304期
编辑:刘东辉
审核:曲学良

编辑部:刘冬梅
电话:024-25847830、25852311-205
邮箱:journal@foundryworld.com
广告发行:王巧智
电话:024-25611775
邮箱:ad@foundryworld.com
官网:www.foundryworld.com
免责声明:除注明原创及明确标注来源外,文章系网络转载,版权归原作者所有。但因转载众多,或无法确认真正原始作者,故仅标明转载来源,如标错来源,涉及作品版权问题,请与我们联系,我们将在第一时间协商版权问题或删除内容!
欢迎大家点击阅读原文,进入论坛进行讨论。
敬请长按下方的二维码关注我们,以便获取最新的资讯信息。
或者搜索公众号RJGRZM