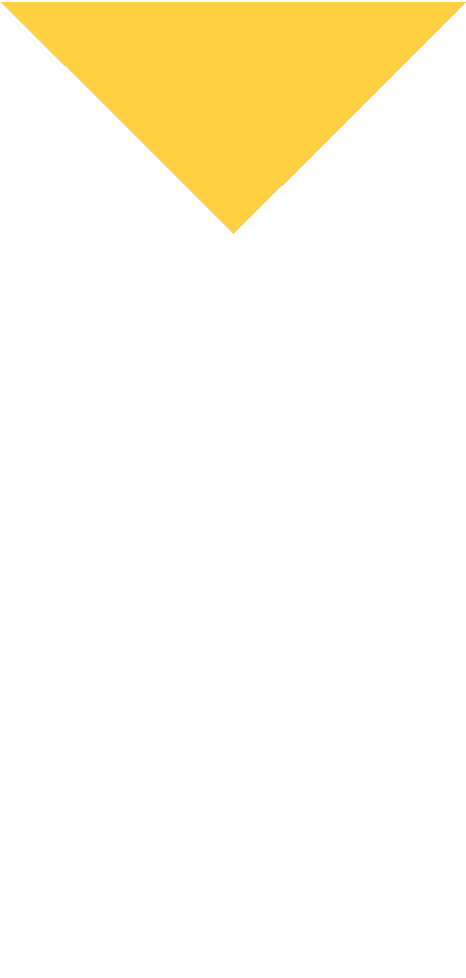
工艺联锁是装置安全运行的保障,系统中的关键工艺联锁能起到报警、关阀停料、打开冷却系统、打开泄压系统等重要作用,使生产过程安全停止运行或自动导入预定的安全状态,有很高的功能安全性。如果关键工艺联锁随意摘除或投用,往往会导致安全事故发生。近年来,国内外发生的多起较大及以上化工事故都与联锁失效或设置不当有关。
一 事故案例
案例1
2005年12月11日,英国邦斯菲尔德油库发生火灾事故,共烧毁大型储油罐20余座,43人受伤,直接经济损失2.5亿英镑。事故主要原因是:912号储罐的自动测量系统(ATG)失灵,储罐装满时,液位计停止在储罐的2/3液位处,ATG报警系统没能启动,储罐独立的高高液位开关也未能自动开启切断储罐的进油阀门,致使油料从罐顶溢出,从罐顶泄漏的油料外溢、挥发,形成蒸气云,遇明火发生爆炸、起火。
案例2
2009年7月15日,国内某染料股份有限公司硝化一车间硝化反应釜发生重大爆炸事故,造成当班操作人员7人死亡、9人受伤,另有周边108名居民被爆炸产生的冲击波震碎的玻璃划伤。经查,该企业的硝化反应装置没有装备自动化控制和高温联锁紧急停车系统,仅靠操作人员现场操作和监控硝化反应釜内的反应情况。
案例3
2017年1月3日,国内某医药化工有限公司C4车间发生爆炸火灾事故,造成3人死亡。事故直接原因是当班工人在开始减压蒸馏操作时甲苯未蒸出,就擅自加大蒸汽开量且违规使用蒸汽旁路通道,致使主通道气动阀门自动切断装置失去作用,蒸汽开量过大,外加未反应原料继续反应放热,釜内温度不断上升,并超过反应产物(含乳清酸)分解温度105℃。反应产物(含乳清酸)急剧分解放热,釜内压力、温度迅速上升,最终导致反应釜超压爆炸。
案例4
2017年7月2日,国内某化工有限公司对(邻)硝车间7#反应釜发生爆炸事故,造成3人死亡、3人受伤,直接经济损失约2380万元。事故直接原因是该公司在生产过程中违规停用了控制压力、温度的安全联锁装置,致使反应釜温度、压力的异常升高不能得到及时有效控制,超过了工艺要求的安全控制范围,最终导致温度、压力异常升高而发生爆炸。
案例5
2020年5月8日,国内某精细化工有限公司三氯化磷车间操作工在投磷作业时,发生爆炸事故,造成2名操作人员死亡。事故直接原因是氯化釜投磷操作时,氯化釜压力升高,造成压力高高报警并联锁动作,切断氯化釜进氯阀,操作人员在未查明原因的情况下,违规操作,擅自投用工艺联锁,继续投磷,五氯化磷与黄磷剧烈反应生成三氯化磷并迅速气化,压力急剧升高,导致氯化釜与洗磷塔连接的上气管和降液管发生爆裂事故。
二 问题分析
近期,笔者在指导服务检查过程中发现,一些企业在安全联锁系统及其相关安全保护措施设计、安装、使用和维护等各阶段的管理,都存在不足。
未按照相关要求设置联锁系统,但却在系统虚设回路,以假乱真
如:辽宁某氟化工有限公司一级重大危险源氟化氢罐区仅设有音叉开关液位高高关闭进料管道紧急切断阀联锁一个回路,但现场氟化氢储罐上无音叉开关。辽宁某化工科技有限责任公司101车间设有烷基化反应釜温度高高打开冷盐水紧急切断阀联锁逻辑,实际现场未设置紧急切断阀,冷盐水系统全为手阀控制。
2
联锁系统故障或未启用,形同虚设
如:辽宁某化工产品生产有限责任公司加氢反应釜搅拌电流显示85.1A(现场搅拌还未运行),超出联锁值57A,但联锁回路未触发。河南某环保科技有限公司杂醇储罐的2个远传液位分别显示为378.92mm、283.72mm,液位低低联锁值为400mm(三取二联锁),已达到触发低低液位联锁条件,但现场出口管道紧急切断阀未动作。
3
联锁系统逻辑设置错误,风险加剧
如:辽宁某新材料有限公司联锁系统中氯化釜超温、超压联锁结果为停止搅拌,设置不合理,因为若氯化釜超温、超压联锁停止搅拌,会局部加剧反应,易导致事故发生。
4
工艺联锁值设置错误,保护失效
如:辽宁某精细化工有限公司DCS系统中,电流低低联锁设置值为“-1.0A”,失去了联锁保护作用。河南某能源科技有限公司脱苯塔(T-6101)顶部压力高限报警值90kPa,超仪表量程0~20kPa,设置错误。
5
联锁长时间摘除,不顾风险
如:河南某环保科技有限公司焦炉煤气气柜入口管道3台在线氧含量检测仪表自2022年12月故障后联锁摘除,至2023年3月核查时未投用。
随着化工装置、储存设施规模的大型化,以及生产过程自动化水平的逐步提高,规范关键工艺联锁系统管理工作亟待加强。建议从以下环节采取措施,防控风险,筑牢过程安全的“最后一道防线”。
完善本质安全设计,从根本上解决问题。根据《危险化学品重大危险源监督管理暂行规定》(国家安全监管总局令第40号)、《国家安全监管总局关于公布首批重点监管的危险化工工艺目录的通知》(安监总管三〔2009〕116号)、《国家安全监管总局关于加强化工安全仪表系统管理的指导意见》(安监总管三〔2014〕116号)等国家法规标准,结合HAZOP分析及企业实际,对安全风险进行评估,科学确定必要的安全联锁系统。
规范开展安全联锁系统的安全仪表功能定级评估、验证及设计工作,确保其安全仪表功能具备既定的功能和满足完整性要求,满足必要的风险管控。
严格按照设计文件及相关标准规范的要求,进行安全联锁系统的安装、调试、审查和联合确认,确保具备安全投用条件。
正确使用关键联锁,严禁带“病”运行。严格按照设计,合理设置工艺联锁值,确保联锁系统正常投用;按照符合安全完整性要求的检验、测试周期,对其功能进行定期全面检验、测试,保证安全联锁能够可靠执行所有既定的功能,实现功能安全。
健全联锁管理制度和内部规范。制定和完善安全联锁相关管理制度、内部技术规范,把功能安全管理融入企业安全管理体系,提升过程安全管理水平,保障安全联锁的正确投用。
严禁随意摘除安全联锁系统。在因故必须摘除安全联锁系统时,应严格执行相关联锁管理程序,分析联锁摘除后可能带来的风险,并采取控制措施,及时修复联锁。联锁摘除不应超过一个月。
来源:中国化学品安全协会
免责声明:所载内容来源于互联网及业内人士投稿,微信公众号等公开渠道。我们对文中观点保持中立,文中观点不代表本公众号观点,文章仅供参考和交流。转载的稿件版权归原作者和机构所有,如有侵权,请联系我们删除。