采用数字孪生设计轮毂轴承单元
[日] Hideo Nishizawa
1 引言
近年来,发达国家为实现碳中和推出了各种政策,包括收紧汽车燃油效率法规和最终淘汰内燃机汽车。另外,分析认为汽车产业正面临百年未遇之大变革,如采用信息与通信技术(ICT)实现自动驾驶等。为了应对这些趋势,NSK采用数值分析开发了一种先进的设计技术,并在轮毂轴承单元的减重、减摩以及提高性能等领域精简了流程(减少试验和评估的次数)。通过充分利用现象预测技术,采用从观察和测量实际物理现象中收集的数值分析模型(该模型的精度已被验证),NSK的开发和设计技术带来了新的解决方案。将这种开发和设计技术称为数字孪生 (DT)。
虽然生产第1—3代轮毂轴承单元,但是本文仅讨论第3代轮毂轴承单元的设计,因为其需要先进的设计技术。安装在乘用车驱动轮和非驱动轮上的轮毂轴承单元如图1所示。轴承除了有两列滚动体外,还与轮毂、车轴和制动器等联结或紧固在一起,使其更小且更轻,因此比常规单列轴承的功能更强且更易装配和维护。
轮毂轴承单元通常专为每辆车或台架设计。尽可能减少试验和评估的次数,以减少开发工时和降低成本,在广泛的领域应用DT,以开发最优设计。轮毂轴承单元的设计流程如图2所示。将过程分为两类:轴承内部设计(过程1)和单元组件设计(过程2)。经常使用具有内部数值分析软件和商用专用分析软件的过程1,已获得大量可靠的追踪记录作为轴承具体理论,其公式和标准化已取得进展。由于这类软件大多可在普通PC上使用,而且计算时间短,因此也在研究采用将几种分析软件相结合的多目标优化算法进行设计。经常使用具有高度通用数值分析方法的过程2,如商用有限元(FEA)软件。
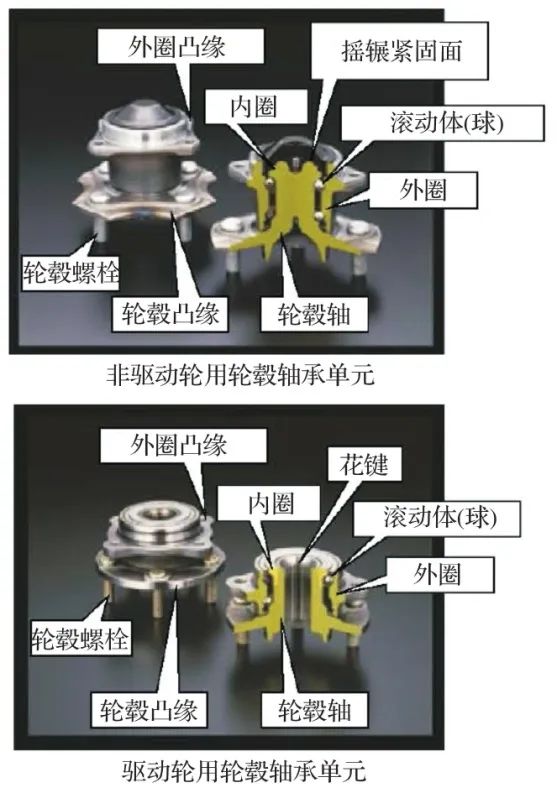
图1 轮毂轴承单元
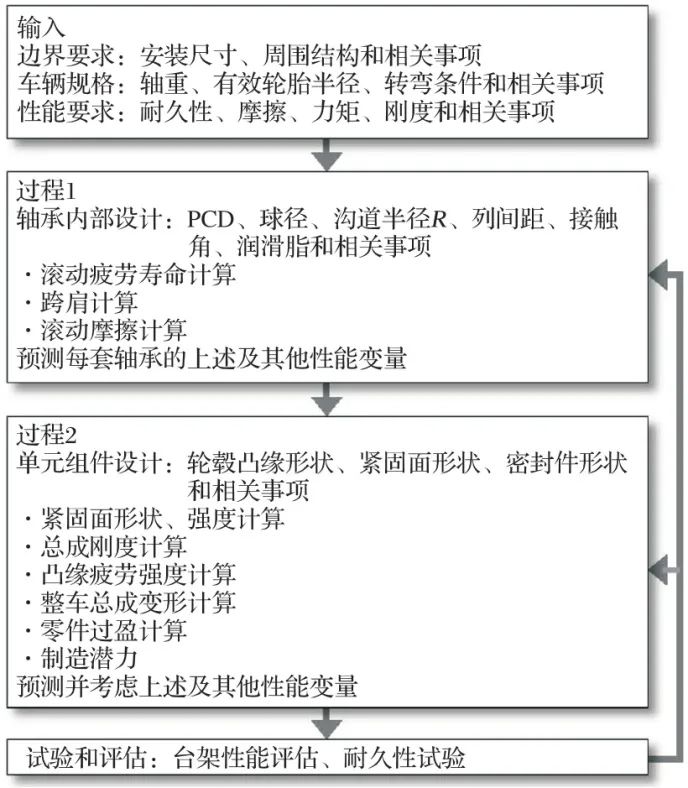
图2 轮毂轴承单元的设计流程
最近,在如多核CPU和GPGPU等高速运算单元、大容量内存、高速大容量存储系统等领域,降低成本的趋势非常普遍。因此,即使是相对小规模的计算系统,计算能力也有显著提高,使采用大型模型的FEA可用于日常设计研究。NSK正通过创建使设计工程师可操作和执行大规模分析的环境来加速DT的使用,分析专家以前经常在该环境中进行研究。接下来将介绍在设计过程中使用DT的一些最新示例。
2 套圈滚动疲劳寿命预测示例
当输入较大载荷时,跨肩状态的示例如图3所示,其中球与沟道之间的接触范围超过沟肩,造成接触应力过大。根据车辆使用情况的不同,很难避免跨肩,因此需进行精确接触分析,以研究沟肩的最优形状。采取应对措施后的耐久性试验和接触应力分析的结果如图4所示。通过保持沟道表面肩部附近产生的接触应力较小,成功地防止了早期滚动疲劳损伤。
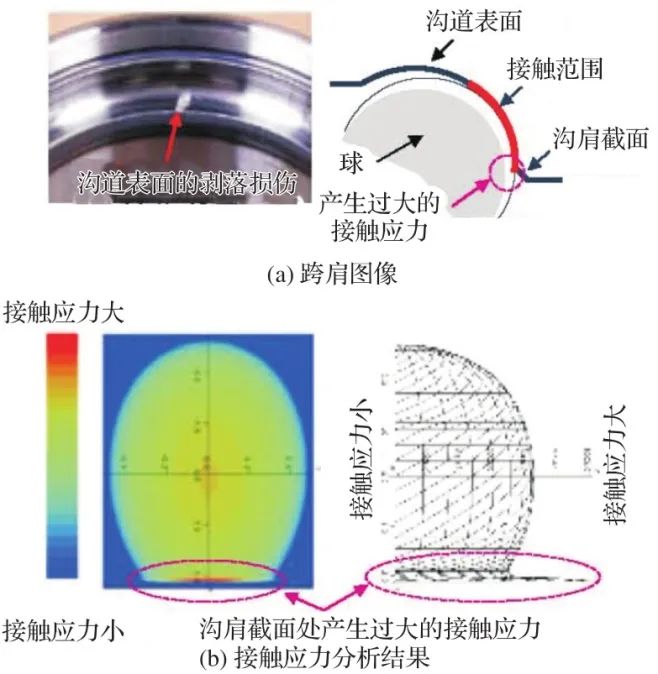
图3 由跨肩造成的剥落损伤示例以及接触应力分析结果
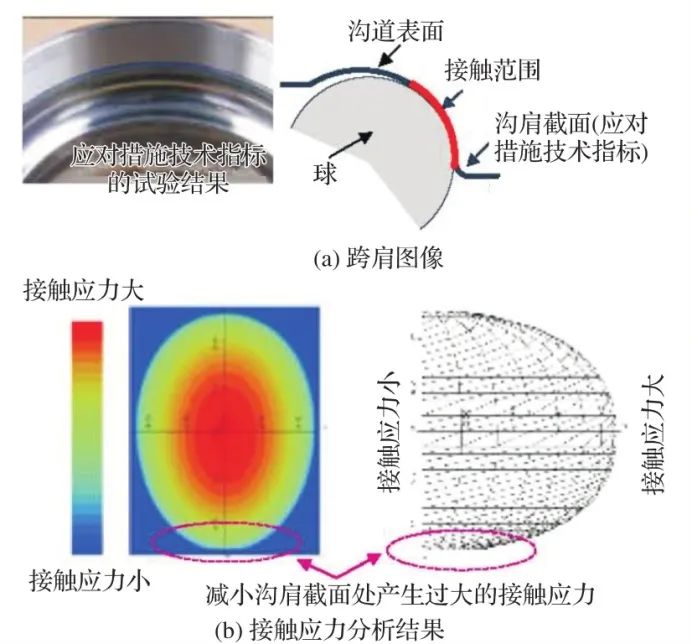
图4 抗跨肩技术指标的耐久性试验结果和接触应力分析结果
滚动疲劳寿命一般基于ISO 281标准化的计算寿命来评估。然而,作为其设计过程的一部分,通过研究精确的滚动疲劳寿命,同时也考虑将配合件紧固到外圈凸缘的影响,NSK正研究防止轮毂轴承单元严重损伤的方法。
3 摇辗紧固面的形状预测示例
用于确定摇辗紧固后的形状和残余应力的弹塑性FEA的示例如图5所示。在分析中采用了Deform,其在紧固模具操作条件设置和大规模塑性变形分析方面非常出色。得到的紧固面形状预测的高精度也如图5所示。分析中输入的加工条件反映了采用实际制造设备的加工载荷测量结果。此外,从各种材料试验中提取了诸如应力-应变曲线等材料特性。由分析结果可得加工后的强度(硬度)和残余应力,因此可预测车辆在运行过程中的疲劳强度。采用该方法可使以往依赖简单分析方法和实际机械试错的紧固面设计更有效。
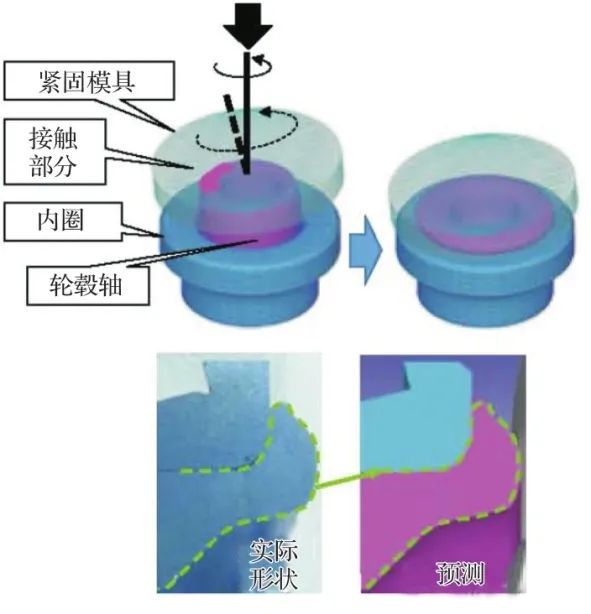
图5 摇辗紧固分析
4 刚度预测示例
轮毂轴承单元支承着由车辆质量和转弯等运动产生的惯性力,变形(刚度)的大小是影响车辆动力学性能的重要因素。将变形分为三类:1)轮毂轴(包括轮毂凸缘)的变形;2)滚动体与套圈之间的接触变形;3)外圈凸缘的变形。把各面排列成一个序列,使其相互依赖,并且具有包括接触在内的非线性载荷位移特性。采用非线性FEA对该刚度进行预测,并采用Abaqus作为分析软件。刚度评估试验示意图和分析模型示例如图6所示。轮毂凸缘和加载夹具、外圈凸缘和固定夹具分别用螺栓紧固。等速节也用螺母紧固。为了简化分析,未对螺栓的螺纹部分和等速节进行建模,但施加一个压缩载荷作为紧固轴向力。由于滚动体与套圈之间的接触面积很小,为了采用FEA进行精确计算,必须使网格尺寸足够小,这需要大规模且耗时的计算。在这种情况下,分析方法是Full-FEA。一般认为,滚动体(球面)与套圈(曲面)之间的接触处于规定的Hertz接触状态。此外,当对轮毂轴承单元施加载荷时,由于滚动体与滚道表面之间接触角的变化以及承载区范围的变化,刚度变得复杂且非线性。因此,将最初由NSK基于Hertz接触理论开发的BRAIN (Bearing Analysis In NSK)软件作为用户子程序集成到Abaqus中,消除了对接触部分进行精细网格划分的需要,这是Full-FEA所必不可少的。同时,构建了一种能考虑高精度非线性刚度的耦合分析方法,该方法被称为Usub-FEA。
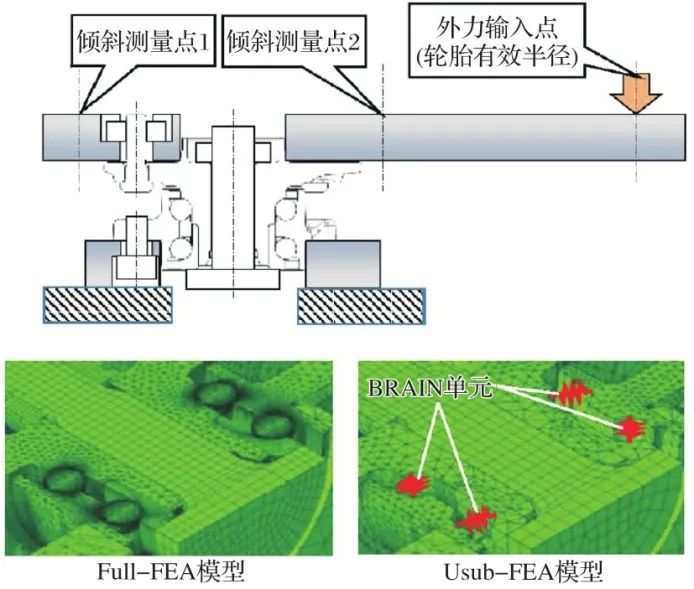
图6 刚度试验机原理图及FEA模型
刚度预测值与实测值的对比如图7所示。由Full-FEA和Usub-FEA分析得到的预测值与实测值趋于一致,具有足够的精度。Full-FEA在滚道表面有许多传输接触载荷的节点。该方法具有高的接触刚度和高的滚道表面变形重现性,且有精度略高于Usub-FEA的趋势。2种分析方法计算时间的对比如图8所示。由于无需减小Usub-FEA的网格尺寸来模拟接触状态,因此可成功地减小模型规模,从而在保持分析精度的同时显著减少计算时间。
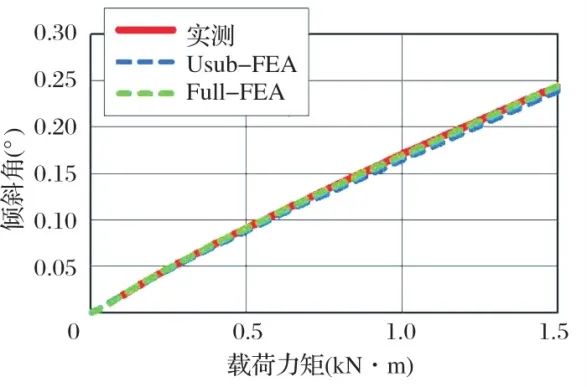
图7 刚度预测值与实测值的对比
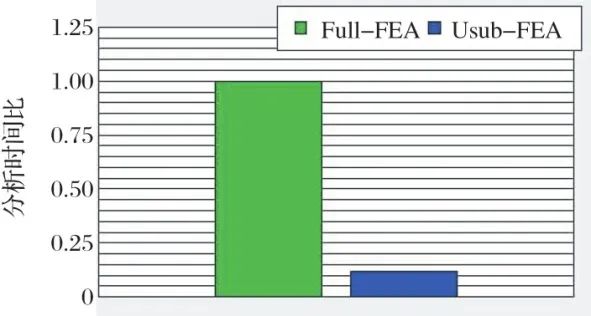
图8 分析时间的对比
由于Usub-FEA可减小滚动体和滚道表面的网格尺寸,因此通过采用具有备用容量的计算资源,其极易扩展到分析,包括车轮、制动盘和关节等车辆周边零件。当轴承安装在车辆上时,希望将该方法用于轮毂轴承单元性能的预测,以开发轮毂轴承单元为目标,可为提高车辆动力学性能做出贡献。此外,尽管Full-FEA有模型规模增大的缺点,但计划将其用于刚度预测以外的应用,因为其具有更高的分析精度。
5 采用Full-FEA预测抗压痕能力的示例
在实际应用中,由于轮胎或轮辋与路沿的碰撞以及道路坑洼与轮胎的接触或其他任何事故,过大的载荷可能输入轮毂轴承单元。这可能导致滚道表面的塑性变形,称为压痕。在许多情况下,车辆甚至在压痕产生后也可运行。但当滚动体旋转时,会周期性地与滚道表面的压痕发生碰撞,产生振动和异常噪声,可能会使驾驶员感到不适。此外,由于从压痕起源的滚道表面疲劳,轮毂轴承单元的连续使用可能导致严重损伤。一般来说,抗压痕能力的变化取决于设计参数,如套圈的形状、滚动体的数量和尺寸、外圈凸缘的形状以及材料的强度。因此,必须研究设计时假定外载荷下的抗压痕能力。
压痕重现试验的示意图如图9所示。采用圆度测量仪测量带有压痕的滚道表面状态(图10),表明了车轮外侧滚道与内侧滚道之间压痕的范围和深度不同。假定当施加过大的载荷时,各零件的变形影响压痕形成,因此采用Full-FEA方法计算滚动体载荷分布。车轮外侧滚道与内侧滚道之间滚动体载荷分布以及外圈变形对比如图11所示。在车轮内侧滚道中,滚动体承载区与套圈刚度较小的范围重叠,滚道表面变为椭圆形。可假设由于套圈变形,压痕数量随着承载区变宽而增加。由该结果发现采用Full-FEA可实现基于抗压痕能力的套圈厚度优化设计。
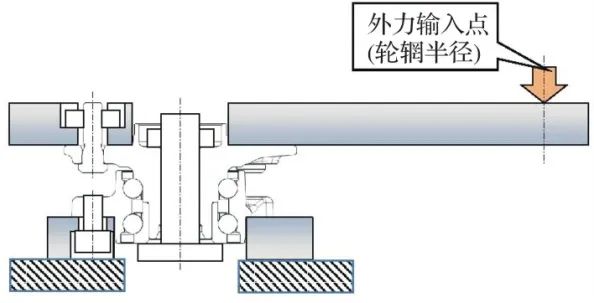
图9 重现试验压痕示意图
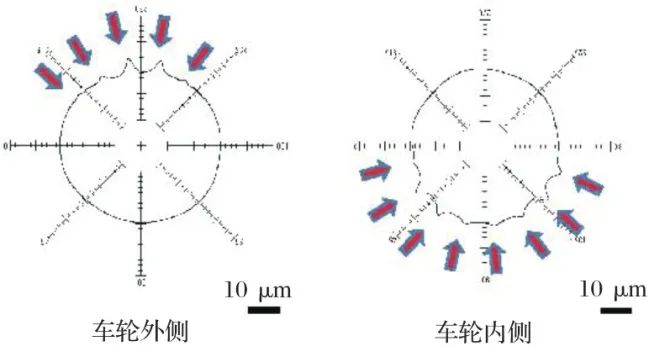
图10 压痕试验后的外圈圆度测量
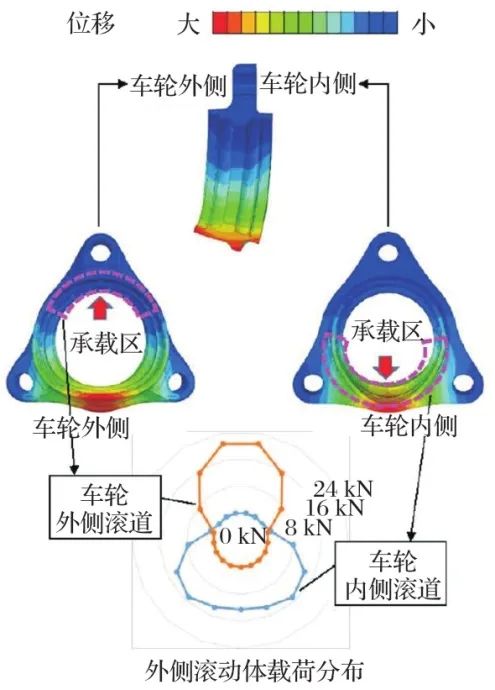
图11 滚动体载荷分布以及外圈变形示意图
未来通过将材料强度分布输入该方法,可定量预测压痕形状。
6 轮毂凸缘疲劳强度预测示例
由于轮毂轴承单元支承着车辆,其损伤可能导致事故,因此轮毂单元必须具有较高的耐久性。特别是轮毂凸缘紧固在车轮和制动器上,车辆在行驶过程中会输入重复循环应力,因此需对疲劳强度进行高度可靠的预测。为此,通过Abaqus充分利用了车轮和制动器的FEA。分析模型的轮廓如图12所示。由于主要损伤因素是由轮胎传递的外力导致以车轮紧固部分为支点的轮毂凸缘变形(弯曲)造成的疲劳,因此建模的范围不仅包括轮毂轴承单元,还包括车轮和制动器。此外,为了在车辆行驶时输入重复循环应力,设置了多种滚动体载荷条件。
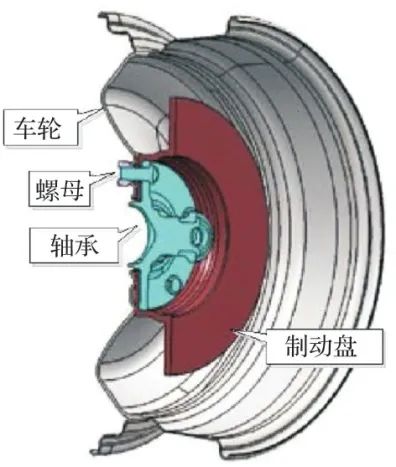
图12 车轮和制动器的疲劳强度分析模型
在各滚动体加载阶段,轮毂凸缘的最大主应力分布如图13所示。除了具有装配车轮和制动器的功能外,为保证减重和刚度等性能,每辆车的轮毂凸缘形状不同。因此,每种模型的最薄弱部分不同,需综合考虑强度来输入旋转载荷。
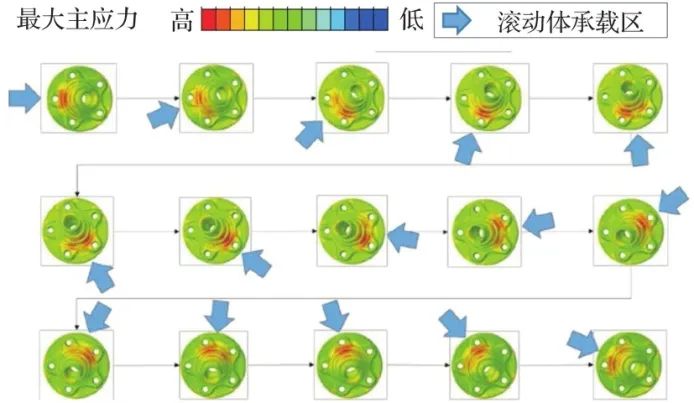
图13 各加载阶段的主应力分布
在得到各载荷条件下的应力分布后,采用疲劳分析软件fe-safe进行后处理,确定了疲劳耐久性。轮毂凸缘有车制面和锻制面,由于表面粗糙度的不同,采用了不同的强度准则。通过数值分析预测的最薄弱部分以及耐久性试验后渗透检验中发现的疲劳裂纹的着色和观察照片如图14所示。一系列数值分析使与实际机械几乎相同位置的损伤预测成为可能。众所周知,疲劳损伤不仅受重复循环应力的影响,还受轮毂轴承单元制造过程中锻造和热处理产生的残余应力的影响。考虑这些在分析模型方面的影响,希望进一步提高强度预测的精度。
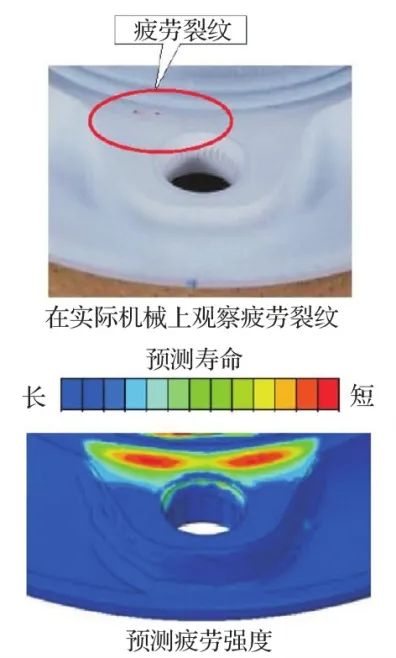
图14 实际轴承的损伤截面和预测疲劳强度
7 结束语
已介绍了轮毂轴承单元的DT应用示例,该示例使用了计算能力的最新改进。尽管在设计中尽量避免在大规模模型中采用非线性FEA,但从计算成本(计算时间)和建模难度的角度来看,发现其有许多优点。
计算服务器和有效利用服务器的软件的性能日渐提高,即使目前的分析技术也很难在常规设计过程中使用,可能在几年内以足够的精度和合理的成本使其变为可用。此外,即使有商用分析软件,也可通过定制一些模型并与其他方法耦合来显著降低分析成本,例如Usub-FEA。DT基于高度可靠的数值分析,其是实现精简流程(即减少试验和评估的次数)这一最终目标所不可或缺的技术。将继续从中长期的角度促进这样的技术发展。
End
参考文献(略)
Hub Unit Bearing Design Using Digital Twins
译自《Motion &Control》,2022(33):26-36.
翻译:高红 校对:张睿祺