
您看此文已用
·
秒,转发只需1秒呦~
机械工程文萃-5-09月04日星期一
径向预紧法多使用在承受径向负荷的圆锥孔轴承中,典型的例子是双列精密短圆柱滚子轴承,利用螺母调整这种轴承相对于锥形轴颈的轴向位置,使内圈有合适的膨胀量而得到径向负游隙,这种方法多用于机床主轴和喷气式发动机中。在定位预紧中,可通过调整衬套或垫片的尺寸,获得合适预紧量;还可直接使用预先调好预紧量的成对双联轴承来实现预紧的目的,此时一般不需用户再行调整总之,凡是经过轴向预紧的轴承,使用时其相对位置肯定不会发生变化。 定压预紧是用螺旋弹簧、碟形弹簧等使轴承得到合适预紧的方法。
预紧弹簧的刚性—般要比轴承的刚性小得多,所以定压预紧的轴承相对位置在使用中会有变化,但预紧量却大致不变。 定位预紧与定压预紧的比较如下:
(1)在预紧量相等时,定位预紧对轴承刚性增加的效果较大,而且定位预紧时刚性变化对轴承负荷的影响也小得多。 (2)定位预紧在使用中,由于轴和轴承座的温度差引起的轴向长度差,内外圈的温度差引起的径向膨胀量以及由负荷引起的位移等的影响,会使预紧量发生变化;而定压预紧在使用中,预紧的变化可忽略不计。公众号《机械工程文萃》,工程师的加油站!轴承力矩、负荷及寿命
使一轴承套圈或垫圈相对于另一固定的套圈或垫圈开始旋转所需的力矩。当一个轴承套圈或垫圈旋转时,阻止另一套圈或垫圈运动所需的力矩。当轴承套圈或垫圈的相对旋转速度为零时(向心或推力轴承)或当滚动元件在滚动方向无运动时(直线轴承),作用在轴承上的负荷。当轴承套圈或垫圈相对旋转时(向心或推力轴承)或当滚动元件在滚动方向运动时(直线轴承),作用在轴承上的负荷。计算理论负荷用的一般术语,在特定的场合,轴承在该理论负荷作用下如同承受了实际负荷。8.径向(轴向)基本额定静负荷basicstaticradial(axial)loadrating与滚动体及滚道的总永久变形量相对应的径向静负荷(中心轴向静负荷)。如果在零负荷下,滚子与滚道(滚子轴承)为或假定为正常母线(全线接触)时,在最大接触应力下,滚动体与滚道接触处产生的总永久变形量为滚动体直径的0.0001倍。对单列角接触轴承,径向额定负荷为引起轴承套圈彼此相对纯径向位移的负荷的径向分量。9.径向(轴向)基本额定动负荷basicdynamicradial(axial)loadrating恒定的径向负荷(恒定的中心轴向负荷),在该负荷下,滚动轴承理论上可以经受1百万转的基本额定寿命。对单列角接触轴承,该径向额定负荷为引起轴承套圈彼此相对纯径向位移的负荷的分量。轴承的一个套圈或一个垫圈或一个滚动体的材料首次出现疲劳扩展之前,一个套圈或一个垫圈相对于另一个套圈或一个垫圈的转数。11.可靠性(指轴承寿命的)reliability在同一条件下运转的一组近于相同的滚动轴承期望达到或超过某一规定寿命的轴承的百分数。一套轴承的可靠性为此轴承达到或超过规定寿命的概率。以径向基本额定动负荷或轴向基本额定动负荷为基础的寿命的预测值。14.寿命系数lifefactor为了得到与给定额定寿命相应的基本额定径向动负荷或基本额定轴向动负荷,适用于当量动负荷的修正系数。向心轴承与座组合在一起的一种组件,在与轴承轴心线平行的支撑表面上有供安装螺钉的底板。16.立式座plummerblockhousing有径向凸缘及在与轴承轴心线垂直的支承表面上有供其安装用的螺钉孔的一种座。有圆柱形内孔的轴向开口的套筒,其外表面为圆锥形且小端有外螺纹。用于将有锥孔的轴承安装(用锁紧螺母及锁紧垫圈)在有圆柱形外表面的轴上。有圆柱形内孔轴向开口的套筒,其外表面为圆锥形且大端有外螺纹。用于将有锥孔的轴承在圆柱形外表面的轴上安装或拆卸(用螺母)。有圆柱形外表面及轴向槽的螺丝母,用锁紧垫圈的一个外爪及环形板手将螺母锁紧。用于滚动轴承轴向定位。有许多外爪的薄钢板垫圈。一个外爪用于锁紧螺母,一个内爪插入紧定套或轴的轴向槽里。22.偏心套eccentriclockingcollar一端有相对内孔偏心的凹槽钢圈,安装在外球面轴承内圈的相等偏心的伸长端。相对内圈旋转偏心套以将内圈固紧,然后紧固顶丝使之固紧在轴上。23.同心套concentriclockingcollar安装在外球面轴承宽内圈上的钢圈,有顶丝旋入内圈上的孔里并与轴接触。 汽车工作时各系统震动发出的声音统称为汽车的响声,有些书籍上又称之为噪声。而这些响声又可分为正常响声和非正常响声。车的很多故障都是通过异响表现出来的,异响是现象,故障才是本质。如不及时排除故障极易造成重大机械事故。 汽车常见异响主要可分为动力总成异响、传动系异响、行驶系异响、风阻异响等几大类。 动力总成异响
故障主要出现在发动机和其相关部件,异响随发动机转速而变,且频率较高。 这种异响比较好识别,异响伴随发动机强烈抖动,且声音频率与抖动频率相同。如遇到这种情况,不要慌张,就近找一家服务站检查发动机供油、点火、供气以及发动机电脑,排除故障即可。 公众号《机械工程文萃》,工程师的加油站! 也许是长期不做换油保养引起的发动机润滑油变质失效,或者润滑系密封性下降导致的机油压力不够,都会使发动机润滑效果下降,导致摩擦件过度损坏产生异响。这种机械异响的震动频率与发动机转速(激励频率)有直接关系,发动机正常工作转速在800-5000r/min。产生噪音的频率很高,人耳只能听到连续或间断时间很短的响声,随着发动机转速升高,异响在音量和频率上都随之增加。如果您的爱车出现了上述异状,就要做好心理准备了,最起码是解体发动机中修检查磨损情况。 家用轿车通常在结构上选取带式传动将发动机的动力传递给发电机、空调压缩机、转向助力泵、水泵等部件。但是,由于质量问题或工作环境恶劣会导致皮带早期磨损引起打滑。同样的问题也常发生在空调轴承、水泵轴承、发电机轴承等轴承件。这种异响往往声音刺耳、音量较高且凉车明显。判断方法较简单,用一根木棒(或金属棒、长柄旋具等)抵在汽车的某个部位上,靠近异响震源时声音有明显变化。这种故障可以通过更换过度磨损件来排除。 传动系异响
传动系异响常常来源于变速箱、差速器、离合器等部件异响随挡位和离合器状态改变呈现出明显变化。 变速器与离合器零件较多,引起响声的原因也比较复杂,在分析判断时应注意是否与特定的情况有关。有些行星齿轮在60Km/h左右车速时声音明显。换挡拉线、挂挡拨叉异常会导致挂某些特定挡位产生异响。离合器分离轴承磨损引起切离合时产生噪音。 曾出现过这样一辆修事故车,行驶至110Km/h震感强烈。经反复试车发现发动机转速3000r/min有噪音,但随挡位减低,噪音和震动减小,二挡及以下挡位声音均属于正常。对变速箱总成做拆装维修,故障排除。这是一例很明显由变速箱与发动机匹配不当引起的故障,异响和震动随挡位的变化而出现明显不同。 离合器故障同变速箱故障有类似的表现,异响随离合器的分离与结合状态发生变化。只要通晓了基本原理,即便非专业人士也可以对传动系异响进行简单判断。 行驶系异响
行驶系异响与车子行驶状态(车速、转向)有直接关系。 行驶系发生故障往往集中在车轮轴承、内外球笼、拉杆头、控制臂等部件。车轮轴承早期磨损会引起刺耳噪音,并带有比较明显的特点:随车速增加,异响频率增加;与发动机转速、变速箱挡位、离合器状态无关。进行维修前心里对故障有个大致了解对保护自己利益有很大帮助,可减小被不正规修理厂坑害的概率。风阻噪音
这里提到的是非正常风阻引起的异响。这类异响由车身周围气流分离引起压力变化而产生的噪音。具体来说包括空腔共鸣、导管管道噪音以及天线、雨刮器、后视镜及扰流器等附件震动引起。密封条开启、塑料件破裂都会引起车身外部曲线发生变化,行驶至高速下引起空气扰流形成异响。声明:部分内容来源于网络,仅供学习、交流。版权归原作者所有。如有不妥,请联系删除。
商务合作、投稿、技术服务合作联系方式:微信号:baitexing
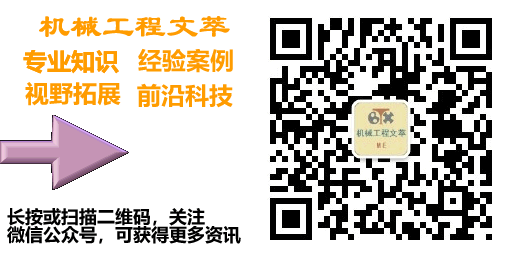
觉得文章不错,就点个在看吧