点击蓝字 ● 关注我们
随着板带材轧制技术的进步,轧制过程向着大型化、连续化和高速化的方向发展,轧机生产效率和产品质量不断提高。四辊轧机作为板带箔材生产的主要机型,其工作辊轴承为滚动轴承,支撑辊轴承为滚动轴承或油膜轴承,由于工艺、设备等因素的影响,使得轧制过程中轧辊轴承的受力情况比较复杂。文献研究表明多列滚动轴承列间载荷分 布不均、偏载严重是影响轴承寿命的重要因素[1-3],大多数有限元模拟和简化计算方法将轴承载荷视为集中载荷或简单均布载荷,使得对轧件板形的预报精度与实际有偏差[4-5]。本研究利用自主设计的四辊实验轧机支撑辊四列圆柱滚子轴承力、温综合 测试装置,对轧制过程中各列圆柱滚子轴承的载荷分布进行了测试,分析了压下率、厚度和宽度等因素对轴承列间载荷分布和轧件轧后板凸度的影响,研究结果可为滚动轴承使用和板形分析模型的建立提供有益参考。
轧辊轴承径向载荷分布理论及实验研究表明,轧制过程中轴承径向载荷以余弦规律分布在对应轴承圆心角约120°的圆弧范围内[6-7]。为测量轴承载荷的列间实际分布情况,设计了四辊板带轧机下支撑辊轴承力、温综合测试装置,在轴承座对应的承载区域沿轧辊轴向加工一个宽度为148mm的槽,在槽内与各列圆柱滚子轴承对应的位置安装4个可上下移动的压力块,各压力块上部圆弧部分与对应列轴承的外圈相接触(如图1(a)所示),与上轴承箱的镗孔共同组成直径为170mm的轴承座内孔,压力块底部加工两个对称布置的沉孔,用于安装两个径向压力传感器。轧制过程中,轴承受力后将压力传递给轴承外圈,轴承外圈将压力传递给压力块,压力块受压后使径向压力传感器产生变形,两个压力传感器承受的径向力和即为该列轴承所受的实际径向力。
为便于记录和分析轴承载荷分布情况,将各列圆柱滚子轴承或压力块进行编号,以驱动侧距辊身最远的轴承为第一列,随着与辊身距离的减小依次为第二、三、四列,操作侧距辊身最近的轴承为第五列,随着与辊身距离的增大依次为第六、七、八列,各列轴承或压力块的具体编号如图1(b)所示。

轧制实验在实验室四辊可逆冷轧机上进行(如图2所示),主要设备参数如下:工作辊尺寸为φ100 ×320mm,支撑辊尺寸为φ220×320mm;主电机功率90kW,转速1500~2800r/min;液压缸压下速度5mm/s;卷取/开卷张力0.5~20kN;最大轧制力1200kN;轧制速度为0~60 m/min;原料厚度≤6mm;成品厚度≥0.2mm。
实验材料为:厚度的2mm,且厚度分布均匀的H24纯铝板。实验方案如下:长度为250mm,宽度分别为80mm、120mm、160mm、200mm、240mm和300mm的试样进行轧制实验,设定压下率均为40%;长度为250mm,宽度为240mm的试样进行轧制实验,设定压下率分别为10%、20%、30%、40%和50%。其中轧制速度均为0.2m/s。对轧制过程中数据采集仪采集的径向压力传感器输出数据进行处理,得到各列轴承的径向载荷分布,并测量轧制后铝板沿板宽方向的厚度分布,进而得到铝板的板凸度。
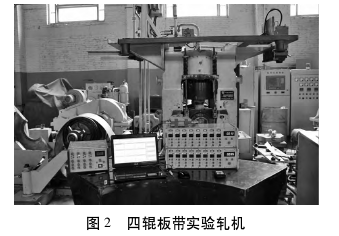
2 轴承列间径向载荷分布分析
为分析各列轴承间径向载荷分布的不均匀程度,定义轴承承载百分比α(i)为第i列轴承径向载荷占总径向载荷的比例,即:α(i)=F(i)/F×100% 。
式中,α(i)为第i列轴承承载百分比,F(i)为 第i列轴承的径向载荷,F为总的径向载荷。
宽度相同时,各列轴承径向载荷随压下率的变化及其分布如图3所示。由图3(a)可以看出,随着压下率的增加,各列轴承径向载荷基本呈线性增加,这是压下率增加导致总轧制力增加的结果。由图3(b)可以看出,轴承列间径向载荷的承载百分比总体呈“M”形分布,轴承座支点所在的第二列和第七列轴承承载百分比最大,超过25%,靠近支点的第一列、第三列和第六列、第八列轴承承载百分比较大,远离支点的第四列、第五列轴承承载百分比最小,小于5%;当压下率小于43%时,随着压下率的增加,第二列和第七列轴承承载百分比逐渐减小,当压下率大于43%时,随着压下率的增加,第二 列和第七列轴承承载百分比增大;随着压下率的增加,第一列、第二列和第七列、第八列轴承承载百分比变化幅度较大,即轴承径向载荷分配主要发生在支点位置和远离轧制中心线的两列轴承间,其余各列轴承承载百分比变化较小。这是因为支撑辊挠曲和压扁变形是导致各列轴承载荷分配不均的主要原因,当压下率小于43%时,随着压下率的增加 支撑辊的挠曲变大,由于第二和第七列处柱面垫的自位调整作用,第二列和第七列轴承承载百分比逐渐减小,而第一列和第八列轴承承载百分比逐渐增大,当压下率大于43%时,总轧制力基本接近轧机的最大轧制力,柱面垫的自位调整作用减小,使得第二列和第七列轴承的承载百分比又增大。

来料厚度和压下率相同时,各列轴承径向载荷随板宽的变化及其分布如图4所示。由图4(a)可以看出,各列轴承径向载荷均随轧件宽度的增加而增大,其中第二列和第七列轴承径向载荷随板宽的增加其增长速率减慢,第一和第八列轴承径向载荷基本呈线性增大,第三、四、五和六列轴承径向载荷变化不大。由图4(b)可以看出,轴承列间径向载荷的承载百分比总体呈“M”型分布,随着轧件宽度的增加,第一和第八列轴承承载百分比逐渐增加,其余各列轴承承载百分比逐渐减小,但第四和第五列轴承变化量较小,即列间载荷不均匀程度在减小。这是因为支撑辊挠曲和压扁变形的程度是影响轴承载荷分配不均匀程度的主要原因,当来料厚度和压下率相同时,轧制力随轧件宽度基本成正比增加,使支撑辊的挠曲变形变大,但此时轧制力的作用范围也变宽,又会使支撑辊挠曲变小,上述现象即是二者共同作用的结果。

宽度相同时,轧后轧件横向厚度分布和板凸度随压下率的变化情况如图5所示。由图5(a)可以 看出轧后轧件沿宽度方向产生了较为明显的不均匀变形,轧件由轧前的矩形截面变为凸形截面。由图5(b)可以看出,随着压下率的增加板凸度先增大后减小,压下率为30%时,板凸度达到最大值。工作辊挠曲变形是影响辊缝形状和轧件凸度的主要因素,而影响工作辊挠曲变形的因素主要为轧制力和辊间压力,对于同一原始厚度的铝板,轧件宽度相同时,轧制力与压下率成正比,辊间压力主要取决于工作辊和支撑辊间的协调变形情况[8]。本文所研究的实验轧机,支撑辊与工作辊的辊径比为2.2,达到了板带轧机辊径比的上限[9],即支撑辊的刚度较大,当压下率小于30%时,轧制力较小,支撑辊的挠曲变形较小,辊间压力作用范围主要集中在轧辊的中间区域;此时,随着压下率的增大,轧制力增大引起的工作辊挠曲增大起主要作用,因此板凸度增大;由图3(a)可以看出,轴承座内靠近支点的第一列与第三列轴承载荷的差值变化不大,也表明 支撑辊挠曲变形较小。当压下率大于30%时,轧制力较大,支撑辊发生了明显的挠曲变形,随着压下率的继续增加,支撑辊的挠曲变大,轧制力增加的同时,辊间压力的作用范围变宽,在两者的综合作用下,工作辊挠曲变形变小,导致板凸度又减小[10] , 由图3(a)可以看出,轴承座内靠近支点的第一列与第三列轴承承载载荷的差值变大,表明支撑辊发生了较大的挠曲变形。
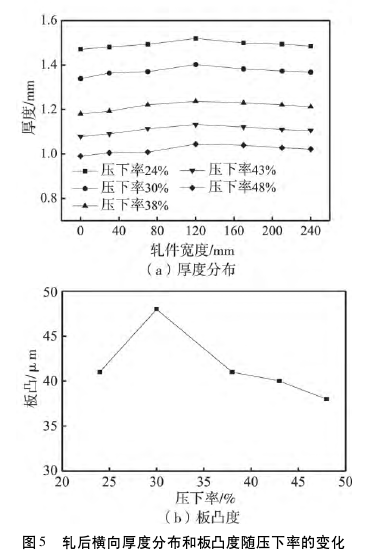
压下率相同时,轧后轧件横向厚度分布和板凸度随板宽的变化情况如图6所示。由图6(a)可以看出轧后轧件沿宽度方向产生了较为明显的不均匀变形,轧件由轧前的矩形截面变为凸形截面。由图6(b)可以看出,随着板宽的增加板凸度先减小后增大又减小,其中极小值出现在板宽为120mm 处,极大值出现在板宽为240mm处。轧件凸度主要是由轧制力和辊间压力引起的工作辊挠曲变形决定的,对于同一原始厚度的铝板,压下率相同时,轧制力与轧件宽度成正比。当轧件宽度较小而压下率较大时,轧制力较小,随着轧件宽度的增加,轧制力增大,使工作辊的挠曲变形增大,但同时轧制力的作用范围也变宽,又使工作辊的弹性变形减小,且此时支撑辊的挠曲变形也较小,辊间压力也 主要集中在轧辊中间区域,导致轧件宽度为120mm时,板凸度达到最小值;随着轧件宽度的继续增大,轧制力继续增大,使得支撑辊发生了一定程度的挠曲变形,但此时轧制力对工作辊挠曲变形的影响增大仍起主要作用,故板凸度又增大,在轧件宽度为240 mm时,板凸度达到最大值;当轧件宽度进一步增大时,轧制力继续增加,但此时轧制力的作用范围变宽,且支撑辊也发生了较明显的挠曲变形,板凸度又开始减小[11-12] ,由图4(a)可以看出,轴承座内靠近支点的第一列与第三列轴承承载载荷的差值变大,表明支撑辊发生了较大的挠曲变形。

为了分析板厚对板凸度的影响规律,对宽度均为240mm,厚度为2mm、3mm和5 mm,且厚度分布均匀的H24纯铝板,在设定压下率为30%的情况下进行了轧制实验(实际压下率分别为30%、32%、30%)。轧后轧件横向厚度分布和板凸度随板厚的变化情况如图7所示。由图7(a)可以看出轧后轧件沿宽度方向产生了较为明显的不均匀变形,轧件 由轧前的矩形截面变为凸形截面。由图7(b)可以看出,随着轧件原始厚度的增加板凸度增大。
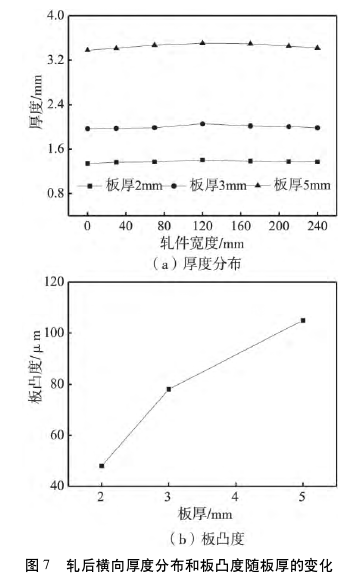
这是因为轧件宽度和压下率基本相同,随着轧件原始厚度的增加压下量增加,虽然单位宽轧制力增大,导致其对板凸度的影响减小,但轧制力的增大使工作辊的挠曲变大对板凸度的影响起主导作用,故板凸度不断增大,但增大的趋势逐渐变缓。
(1)轧件原始厚度相同,当压下率或轧件宽度增加时,轴承列间载荷总体呈增加的趋势,轴承列间承载百分比呈“M”型分布,轴承座支点所在的第二和第七列轴承承载百分比最大,靠近支点的第 一、三、六、八列轴承承载百分比较大,远离支点的第四、五列轴承承载百分比最小。
(2)随着压下率的增加,轴承载荷分配主要发生在支点位置的第二、七列轴承和远离轧制中心线的第一、八列轴承间,其余各列轴承承载百分比变化较小;随着轧件宽度的增加,第一、八列轴承承载百分比逐渐增大,其余各列轴承承载百分比逐渐减小,但第四列和第五列轴承承载百分比变化较小。
(3)由于支撑辊刚度较大,压下率较小时,支撑辊挠曲变形较小,随着压下率的增大,支撑辊挠曲变形逐渐变大,辊间压力分布产生了明显变化, 在轧制力和辊间压力的综合作用下,轧件板凸度呈现先增大后减小趋势。
(4)轧件宽度较小时,轧制力分布对工作辊挠曲的影响较大,轧件宽度较大时,轧制力对工作辊挠曲的影响变大,随着轧件宽度的进一步增大,支撑辊发生明显挠曲后,辊间压力分布也发生了明显变化,在上述因素的综合作用下,板凸度呈先减小后增大又减小的趋势;当压下率和轧件宽度基本相同时,随着轧件厚度的增加板凸度呈增大趋势。
[声明]本文来源网络,由轧机轴承整理发布,版权归原作者所有。转载请注明来源,如有侵权,请联系我们删除。(联系方式:13861477666微信同号)