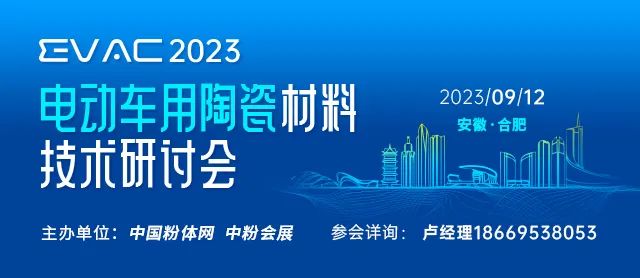

2022年,由北京航空材料研究院实施的航空发动机关键构件抗疲劳寿命试验突破5万小时,标志着我国高端装备制造技术取得全新突破。据了解,此次进行疲劳试验的关键构件是由我国自主研制的航空发动机主轴承,在试验器上等效加速试验疲劳寿命5万小时未失效,更为重要的是,这项试验也创造了我国新的纪录。
轴承作为工业机械领域的关键基础件,素有“装备的关节”之称。轴承性能的优劣直接影响和决定高端装备的精度、寿命、极限转速、承载能力、耐温能力、稳定性、可靠性和动态性能等关键指标,航空航天技术对高质量轴承的需求尤其迫切。在航空发动机设计中,轴承材料和技术始终占到90%~95%以上。可以说,轴承技术代表着发动机极限转速、耐温能力和可靠性水平。轴承材料主要是指高铬抗疲劳轴承钢、耐高温工具钢、高强度齿轮轴承一体化钢等轴承材料,航空技术的发展对高温、高速、高可靠性轴承及材料的的需求也越来越高,由此也促进了轴承材料技术的发展。陶瓷轴承研制开发的最初目标是提高航空航天国防装备轴承的极限性能。瑞典SKF、德国Schaeffler等国际著名轴承公司都开发出高水平的陶瓷轴承技术和产品,特别是热等静压烧结氮化硅陶瓷轴承为高端装备技术的发展提供了核心技术支撑。经过50多年的研究和积累,Si3N4陶瓷轴承已经应用在直升机主传动装置、航空APU、飞机附件传动、导弹发动机、火箭发动机和航天卫星上,已成为高端制造装备中高速和高功率主轴的标配轴承。
近年来,随着陶瓷轴承在高端装备领域的推广应用,材料对轴承质量的影响得到了广泛重视,ISO26602:2009《Fine ceramics(advanced ceramics,advanced technical ceramics)—Silicon nitride materials for rolling bearing balls》对滚动轴承氮化硅陶瓷材料的弹性模量、泊松比、热膨胀系数、弯曲强度、硬度、断裂韧性、显微结构、材料分级等性能指标给出了明确的测量方法和范围,ASTM F 2094/F2094M-08《Standard Specification for Silicon Nitride Bearing Balls》除了对材料质量标准明确要求外,还明确规定了氮化硅陶瓷球的化学成分、表面质量、检测方法、几何参数以及等级用途等。为了充分发挥陶瓷新材料的优势,陶瓷轴承往往需要突破钢轴承的极限性能,如高速性能、高温性能、长寿命质载和高可靠性等。因此与通用滚动轴承设计不同,在设计陶瓷轴承时,除了需要设计基本的结构参数外,还需要面向工况开展表面摩擦学性能的匹配性设计、材料匹配性设计、结构动态性能设计、热特性设计、润滑性能相容性设计和工作性能设计等,但设计理念和结果还需要进一步验证。在航空陶瓷轴承材料匹配性设计方面,重点考虑轴承的抗疲劳能力匹配问题,过大的硬度差会导致轴承元件的过早疲劳和不对称疲劳。FAG研究结果显示,Si3N4陶瓷与M50NiL钢以及Cronidur 30钢组成的混合式陶瓷轴承性能匹配最佳。哈尔滨工业大学的长期研究结果则表明,通过材料配方与组分设计及轴承钢表面的2次改性处理技术,将陶瓷元件的硬度从高向低调整,将轴承钢滚道承载区域改性和表面改性适当提高,其寿命相应比全钢轴承延长1.5~2倍。作为航空轴承的新型材料,航空陶瓷轴承还要经过大量的适应工作状况的试验。寿命验证试验是最基本的试验,还需要完成高速试验、极限温升试验、抗污染能力试验、断油试验和叶片脱落冲击试验等。经过大量的试验可以得到清晰的边界的各种参数,并为陶瓷轴承的设计提供科学依据。尽管Si3N4陶瓷在所有的工程陶瓷中具有优异的综合性能,但与轴承钢相比,其低韧性、高硬度和中等弯曲强度依然是陶瓷材料对损伤和缺陷敏感的致命弱点,因而低缺陷毛坯、低损伤加工工艺和无损检测是保障陶瓷轴承质量一致性和工作可靠性的最直接手段,即使是采用热等静压制造的氮化硅陶瓷滚动体亦如此,因此,高可靠性的陶瓷轴承需要100%的无损探伤来保证。陶瓷无损检测技术分为毛坯检测技术和成品检测技术,其中声发射共振技术和激光材料评价技术在高端应用中具有良好的前景。氮化硅陶瓷球是氮化硅陶瓷轴承中重要的组成部分,氮化硅陶瓷球的滚动接触疲劳是衡量氮化硅陶瓷轴承性能的一个重要的性能指标,表面气孔数量、气孔尺寸、气孔分布均匀性、氮化硅陶瓷球表面粗糙度、氮化硅陶瓷球残余应力及润滑条件均对氮化硅陶瓷球滚动接触疲劳强度有较大影响。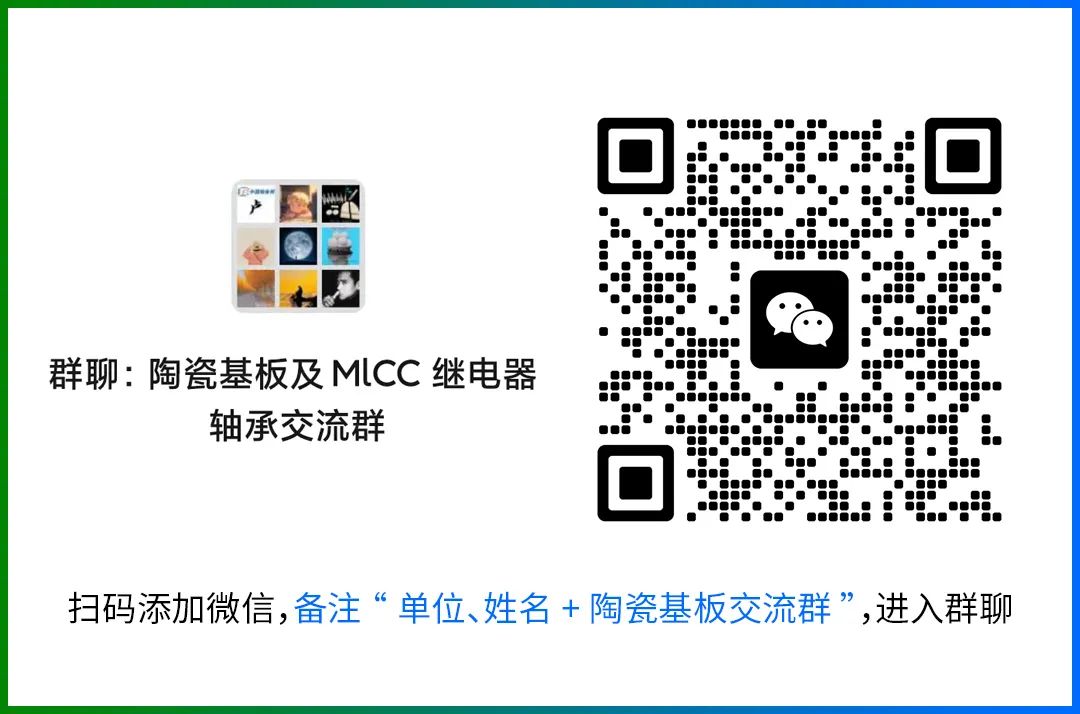
氮化硅陶瓷球的制造过程可以分为四个阶段。第一阶段为氮化硅原料制备,即将氮化硅粉料与烧结助剂以一定的比例均匀混合。第二阶段为氮化硅陶瓷球的成型,常用的有挤出成型、注射成型、干法压制成型及注浆成型等成型方法。第三阶段为氮化硅陶瓷球致密化烧结,烧结方法有常压烧结、热压烧结、气压烧结与热等静压烧结。第四阶段为后处理研磨加工,即粗磨、精磨、粗研、精研和抛光。由于存在夹杂、微型气孔和晶界玻璃相等,早期陶瓷材料的脆性始终是影响长寿命轴承失效模式和抗冲击能力的最直接因素之一。近年来,通过大量研究,发展了陶瓷毛坯的热等静压烧结技术,据中国粉体网小编了解,通过控制陶瓷粉体的纯度、粒径及其一致性、造粒过程与相成分等,使氮化硅陶瓷轴承的综合性能大幅度提高,抗弯强度和断裂韧性等关键指标都能满足要求,其相对密度可以达到99.9%以上,3点抗弯强度高于1000MPa,断裂韧性可达到8~9MPa·m1/2以上,大大优于滚动轴承的最低门槛值6MPa·m1/2。航空轴承技术的发展历史表明,从M50到M50NiL、Cronidur 30,再到目前正在推广使用的氮化硅陶瓷材料,每次轴承材料的改进都推动着航空轴承技术的快速发展。陶瓷轴承以其优异的性能,能够为航空装备领域发展提供重要基础技术保障,高性能的陶瓷轴承将是应对航空装备高速化发展的有效技术途径之一。高韧高强材料技术。据中国粉体网小编了解,采用高纯、高球型度和粒径分布相对集中的氮化硅粉,经过脱氧和脱碳等预处理,去除粉体中的有害成分,进行热等静压烧结,通过工艺优化,提高烧结助剂分散均匀性和陶瓷晶粒长径比,可达到制备显微结构均匀、抗弯强度1000MPa以上、断裂韧性8~9以上的优质陶瓷毛坯材料。低成本批量稳定生产技术。陶瓷轴承的成本包括全寿命期研发费用、产品费用和维修费用,高成本依然是制约目前高端陶瓷轴承系统深入研究的影响因素,在应用中还主要依赖全钢轴承,同时高成本还源于主机技术复杂、对轴承需求批量小和可靠性要求高等特点。轻质化结构,精确设计技术。航空传动系统技术要求结构轻、可靠性高。为此基于轴承接触力学性能、热学性能、摩擦学性能匹配与分析、轴承动力学性能、轴承-转子系统动力学性能、轴承-基座结构力学分析的轴承精确设计技术依然是重点发展趋势;此外,通过极限性能的精确设计,发展先进的表面抗疲劳技术、高速高温固体润滑技术、脂润滑技术、C-C轻型保持架技术,改善轴承内部冲击,降低轴承发热,简化轴承润滑系统,可以进一步减少零件数量和减轻主机质量,这对有限寿命和异常情况下航空装备的安全将带来突破性技术变革。陶瓷轴承的运行健康状态监控技术。现代航空器的转速、温度和载荷越来越高,而轴承性能的波动和轴承失效都会导致严重的系统问题或者失效,智能健康监测系统是航空装备技术监测的总体发展趋势,轴承和齿轮的健康状态监测是其核心技术之一。无损检测和可靠性评价技术。陶瓷滚动体是多相烧结材料,其滚动接触疲劳寿命受原材料、工艺、工况和工作历史等参数明显影响,因此轴承寿命的离散度大,可靠性评价还存在技术困难。发展对表面和次表层缺陷和损伤的无损检测技术,特别是快速可靠的无损检测技术,控制陶瓷元件的成品质量,定量研究损伤模式和规律、极限抗损伤能力,建立可靠性评价模型,都是陶瓷轴承高可靠性应用的重点关注技术。参考来源:
王黎钦等,高可靠性陶瓷轴承技术研究进展,哈尔滨工业大学
饶水林,航空发动机用氮化硅陶瓷轴承技术研究现状,江西昌兴航空装备股份有限公司
注:图片非商业用途,存在侵权告知删除!进粉体产业交流群请加中国粉体网编辑部微信:18553902686

当前,汽车产业进入百年一遇的大变革时期,汽车电动化正成为新的发展潮流和趋势。电动化浪潮下汽车的各大系统设计均发生了翻天覆地的变化,不仅发动机变速箱等这些大总成正经历一场变革,其零部件材料及设计的新旧更替也在迅速刷新着整条产业链。
目前来看,先进陶瓷材料凭借特殊性能优势正在加速“上车”。从最基础的锂电材料用陶瓷窑具、电池隔膜涂层,到轴承、刹车片、基板、电容器、继电器等零部件,再到汽车零部件的高效切削加工,先进陶瓷材料的优势在新能源汽车产业中发挥得淋漓尽致。
种种迹象表明,电动汽车已经成为先进陶瓷应用与发展的新风口。
为此,中国粉体网将于2023年9月12日在合肥举办“第一届电动车用陶瓷材料技术研讨会”,会议诚邀先进陶瓷、新能源汽车行业研发与生产单位、设备制造企业等上下游产业人员参会交流,共同探讨新能源汽车用陶瓷材料与技术,推动我国新能源汽车产业的高质量发展。
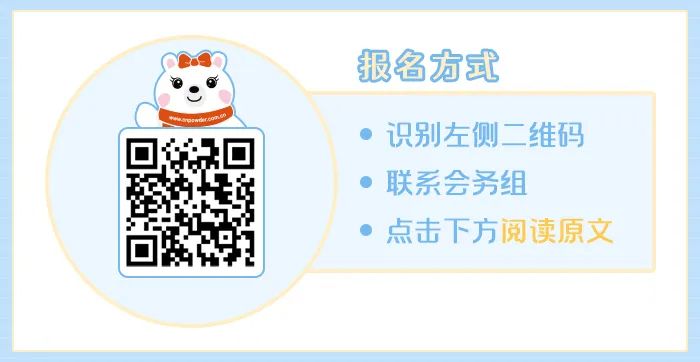