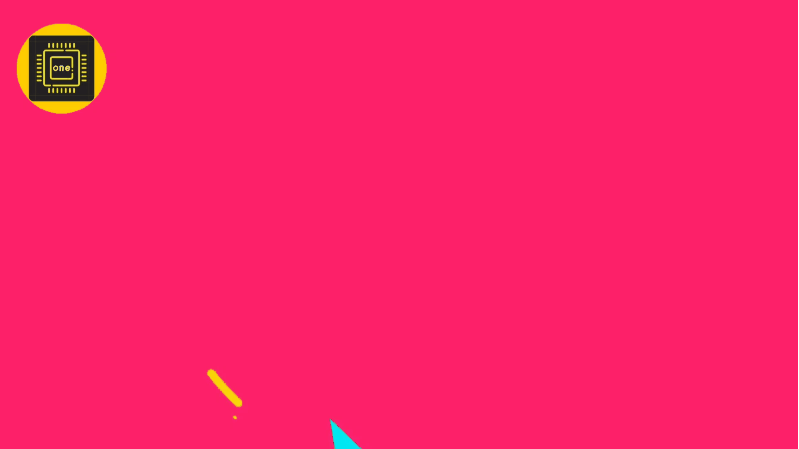
本篇文章主要分为三部分内容,一是离子注入工艺简介。二是离子注入设备系统介绍,包括气体系统、电机系统、真空系统控制系统、射线系统、离子源萃取系统、质谱仪等等。三是半导体离子注入工艺基础详解(131页PPT),最后分享了 全球半导体制造用离子注入设备企业供应商列表离子注入45份资料系列1和其他离子注入机企业深度报告。
(芯一知识库有发过离子注入最新的工艺、设备和技术,可点击下载CMP最新期刊论文50份 + 51份资料系列2)
除此之外,本篇文章分享3份资料:
获取上方资料,请在公众号发送芯ONE资料,或扫描下方二维码,已同步更新到芯一知识库。
丨扫上图二维码,加入星球下载5000+资料
丨市场、技术、研究,半导体领域必备工具
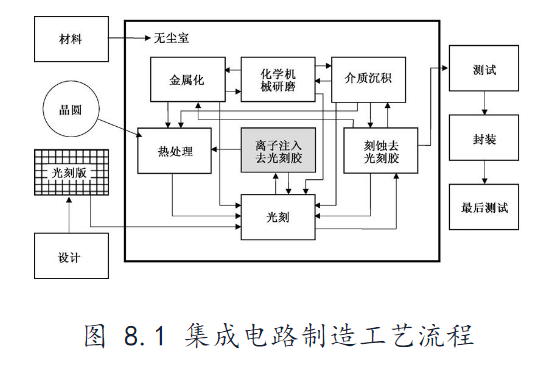
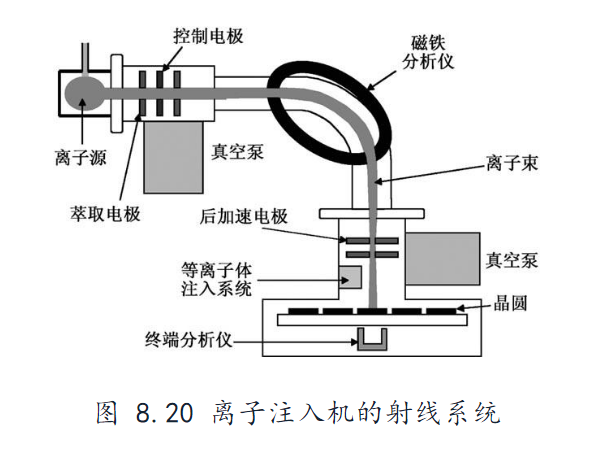
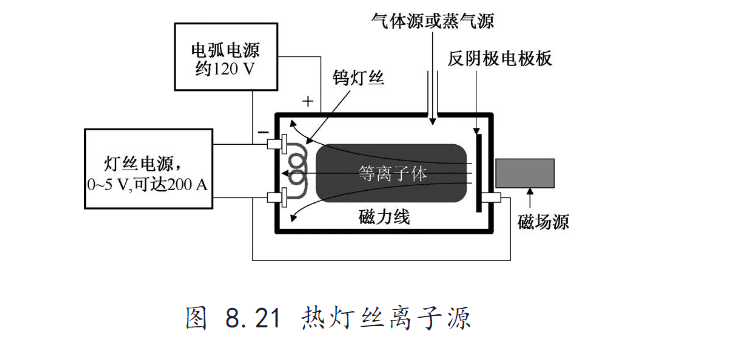
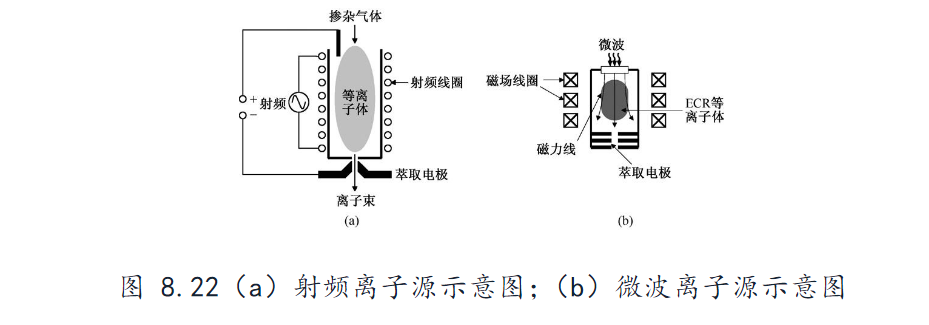
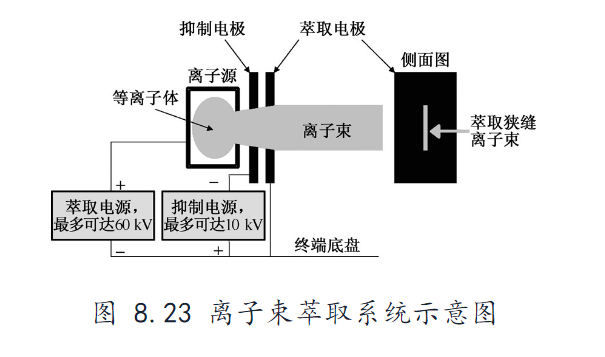
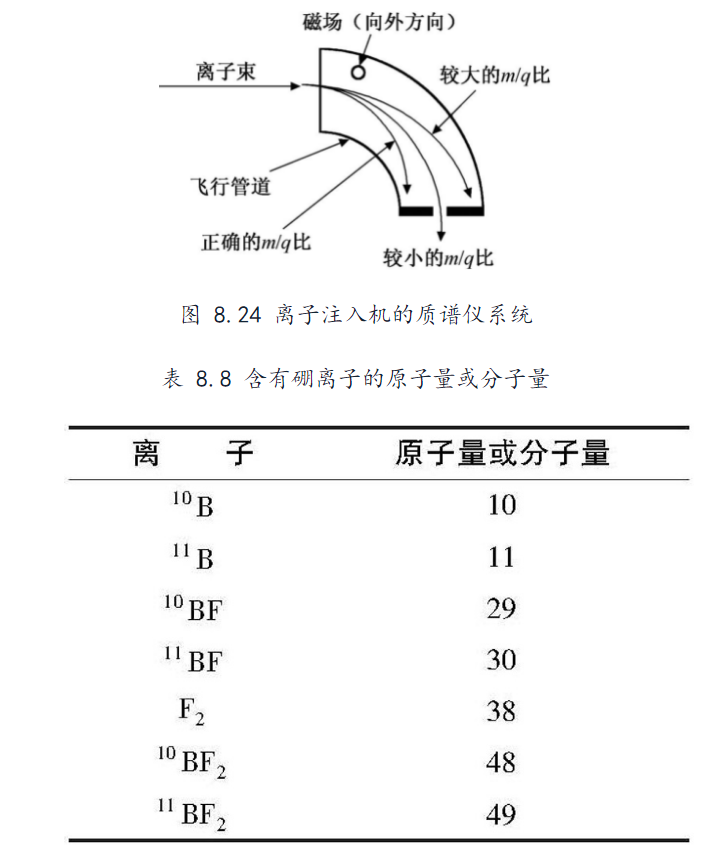
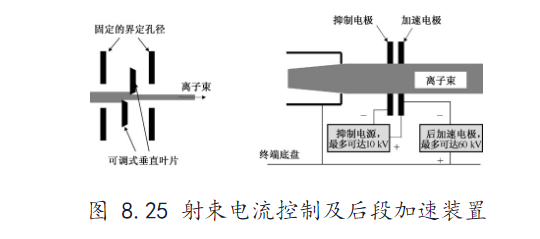
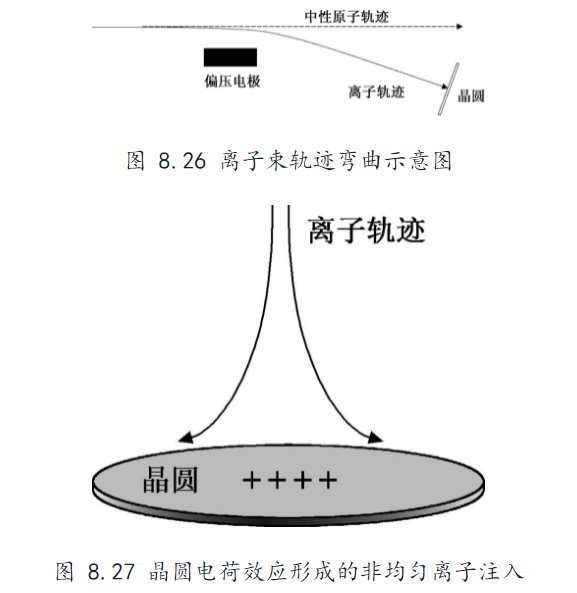
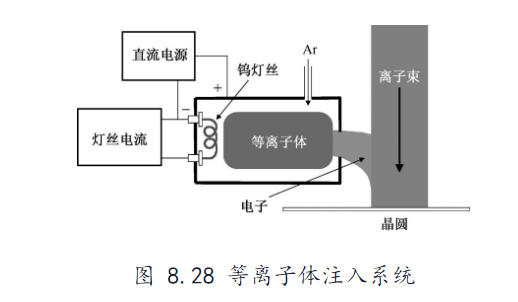
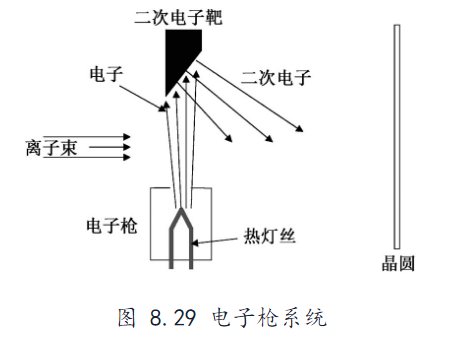
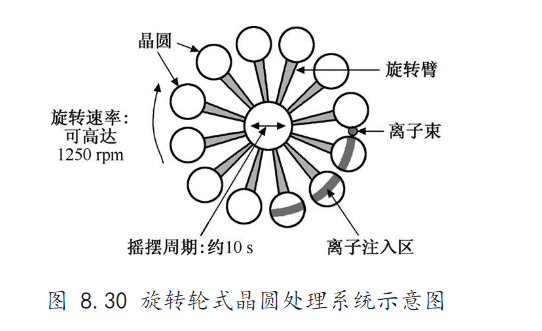
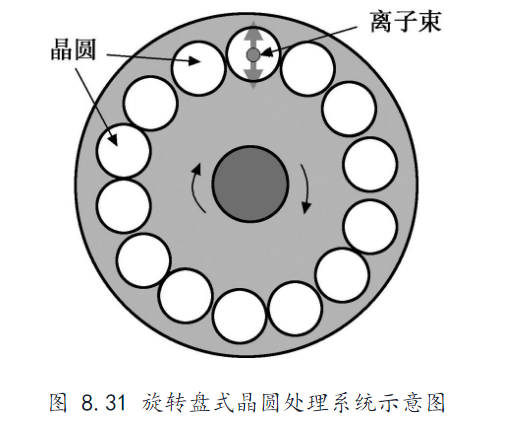
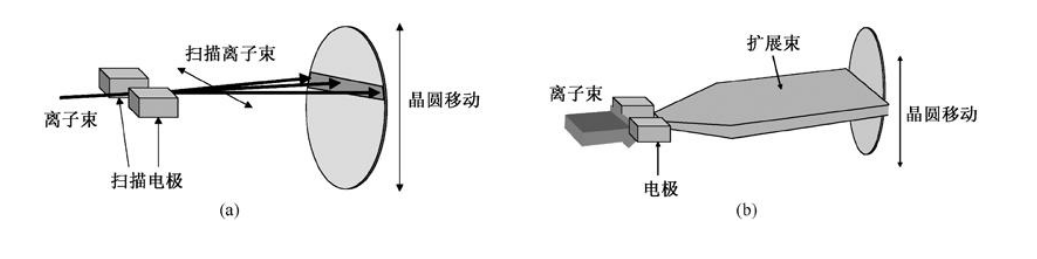
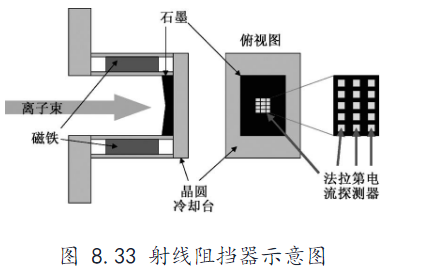
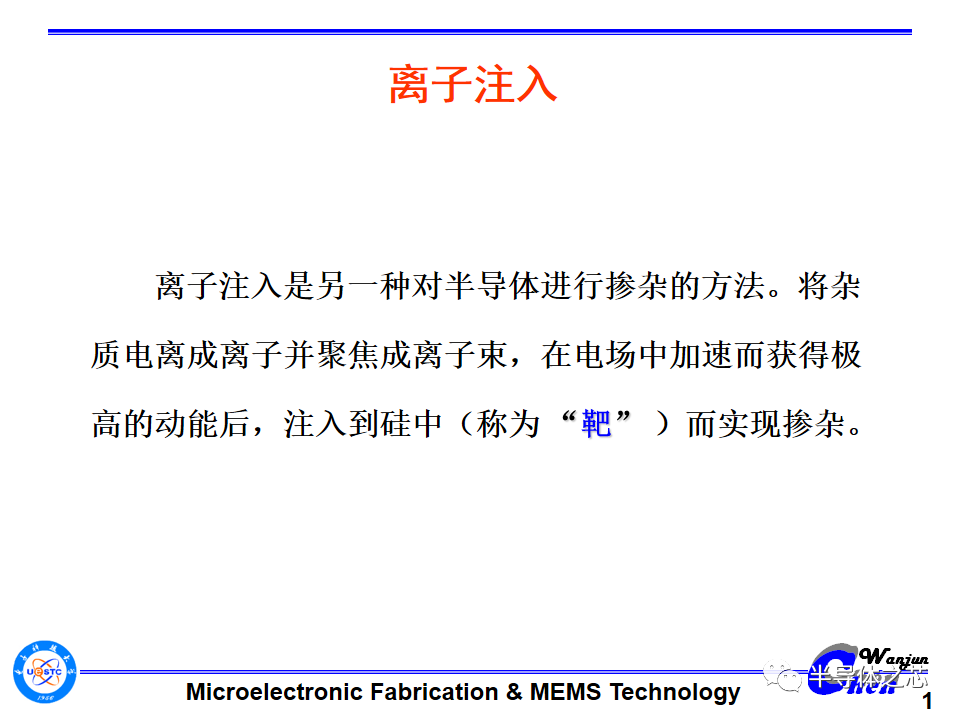
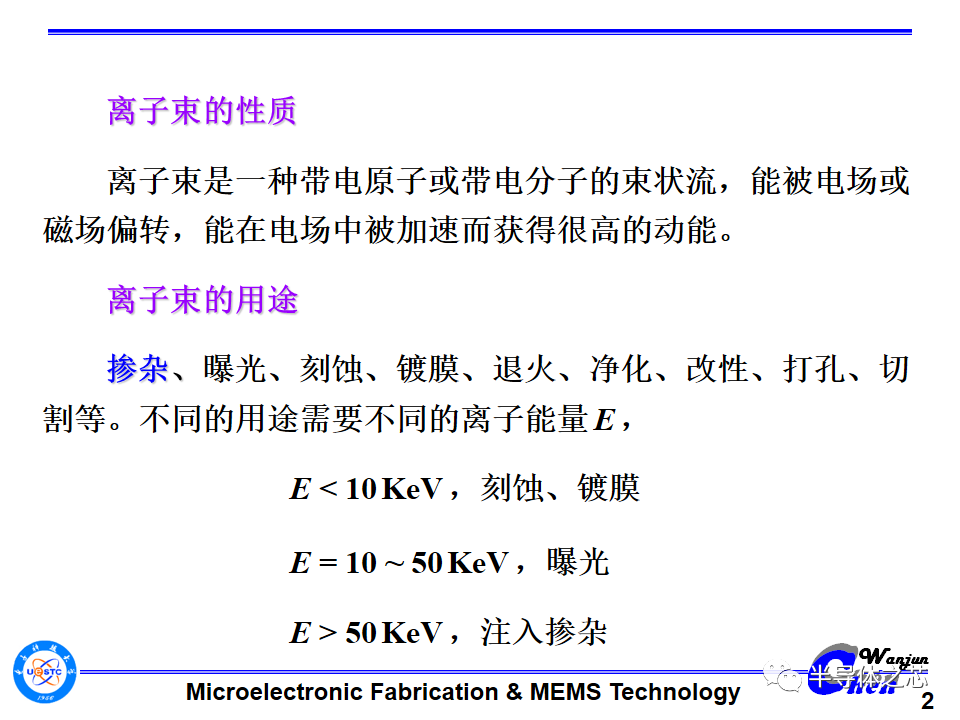
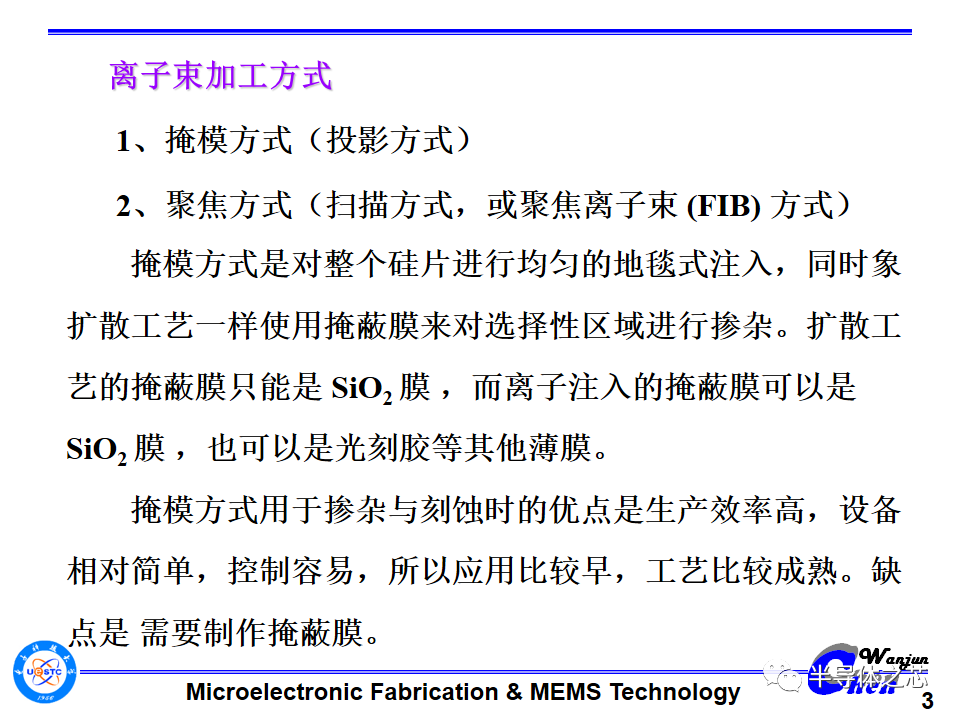
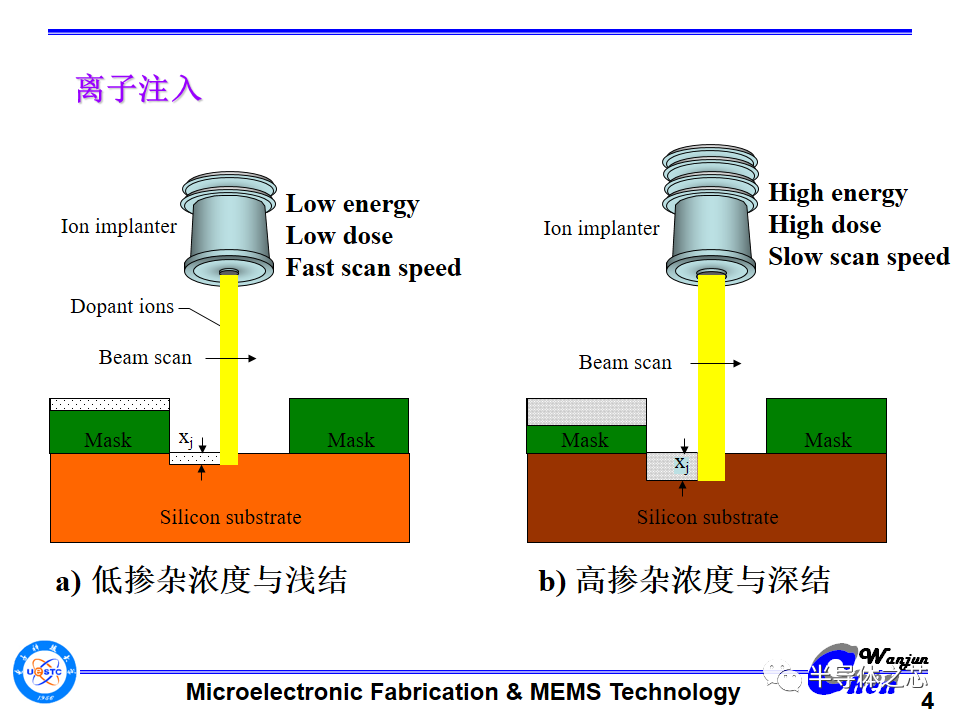
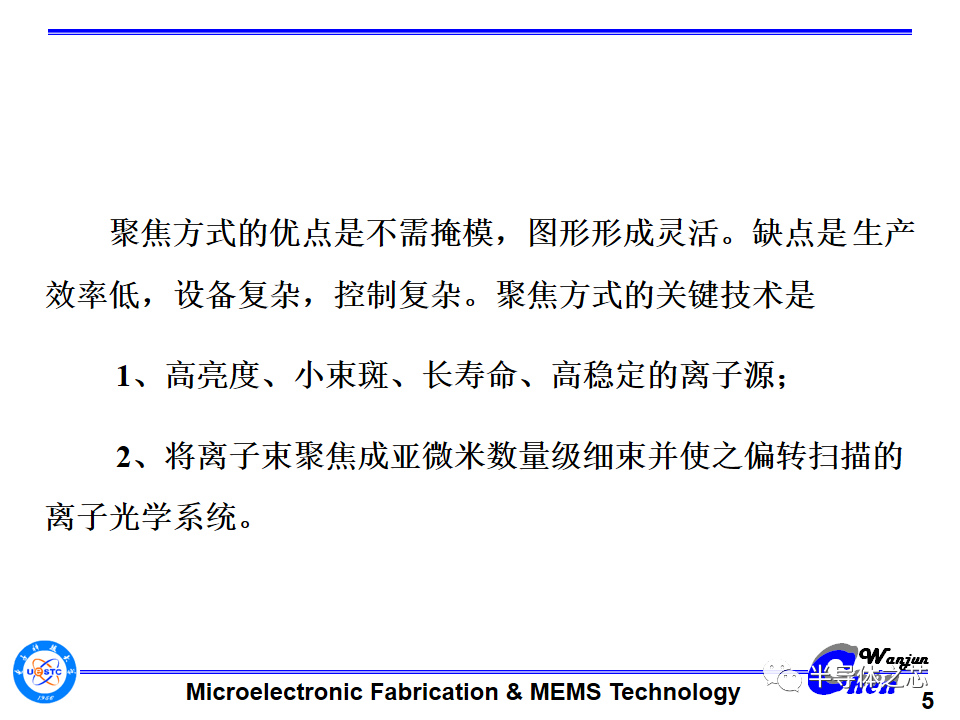
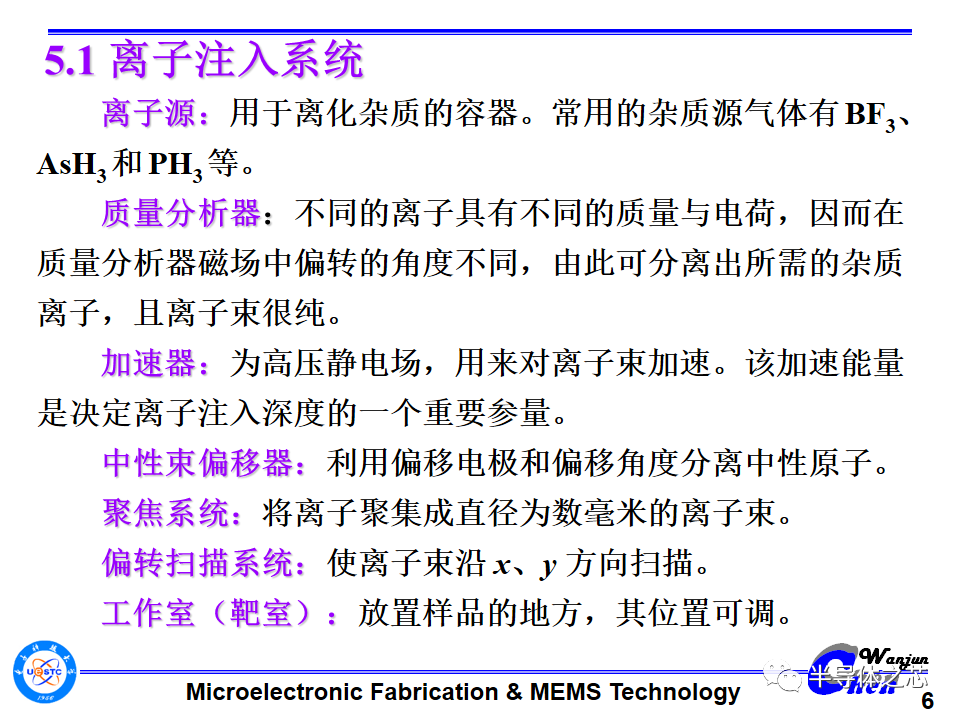
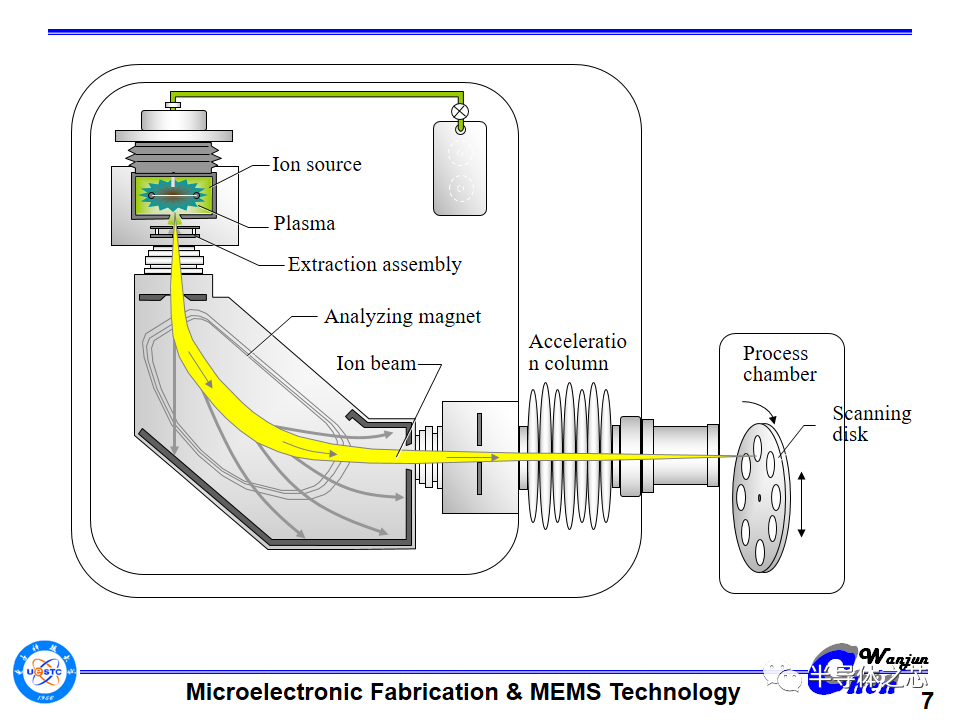
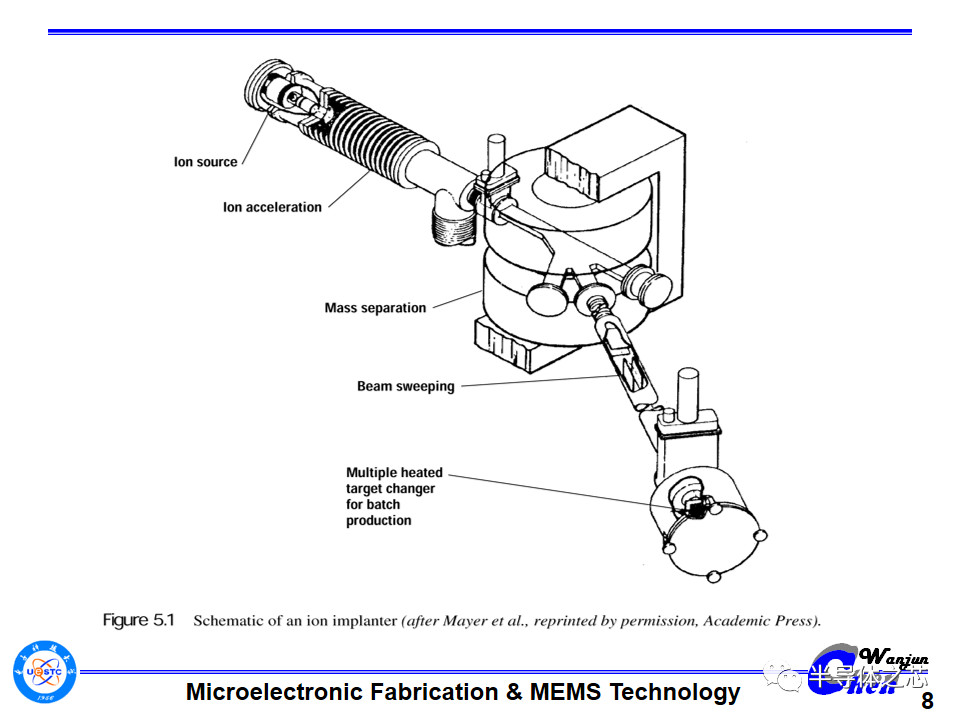
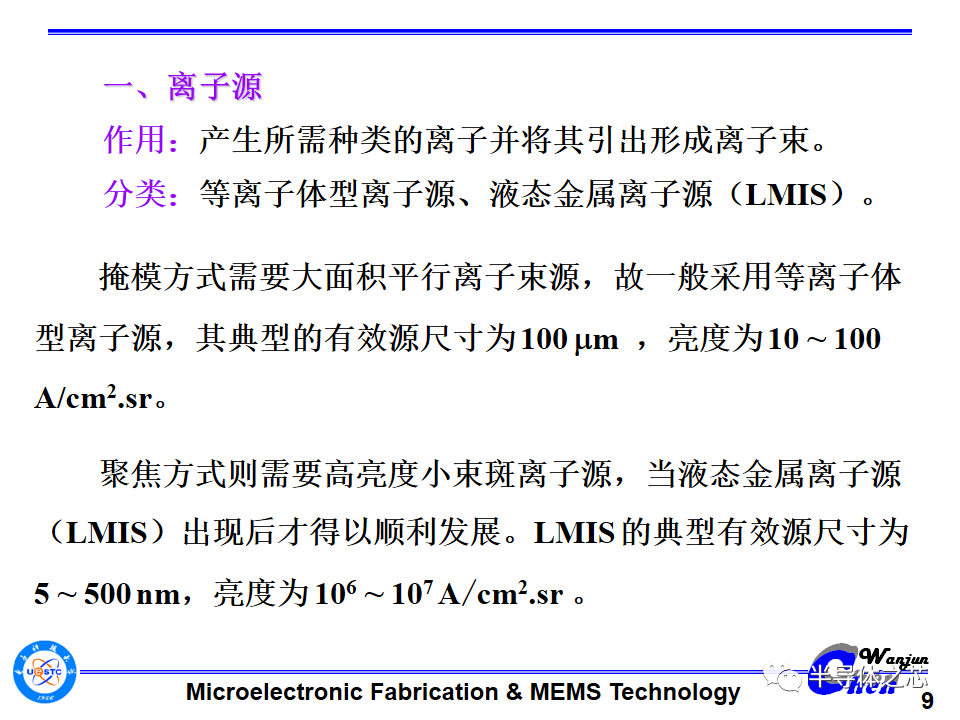
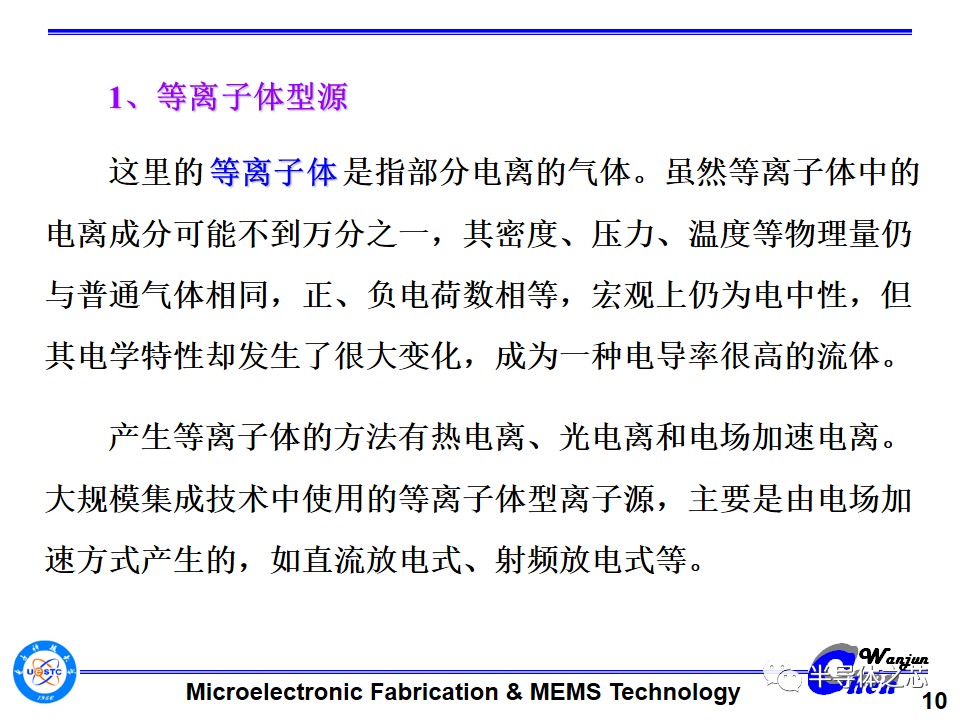
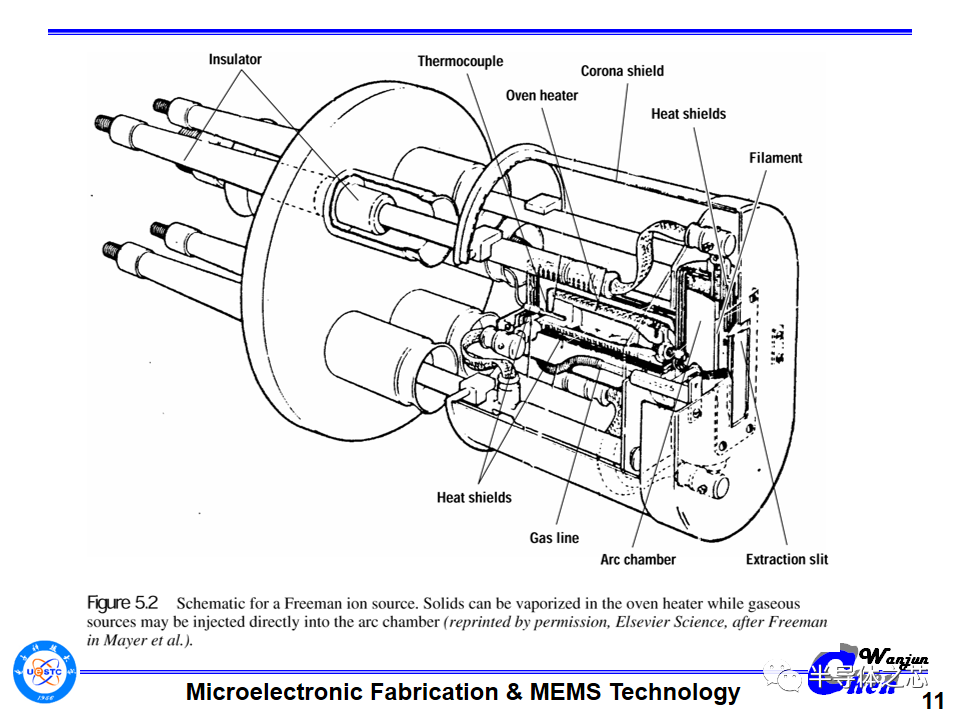
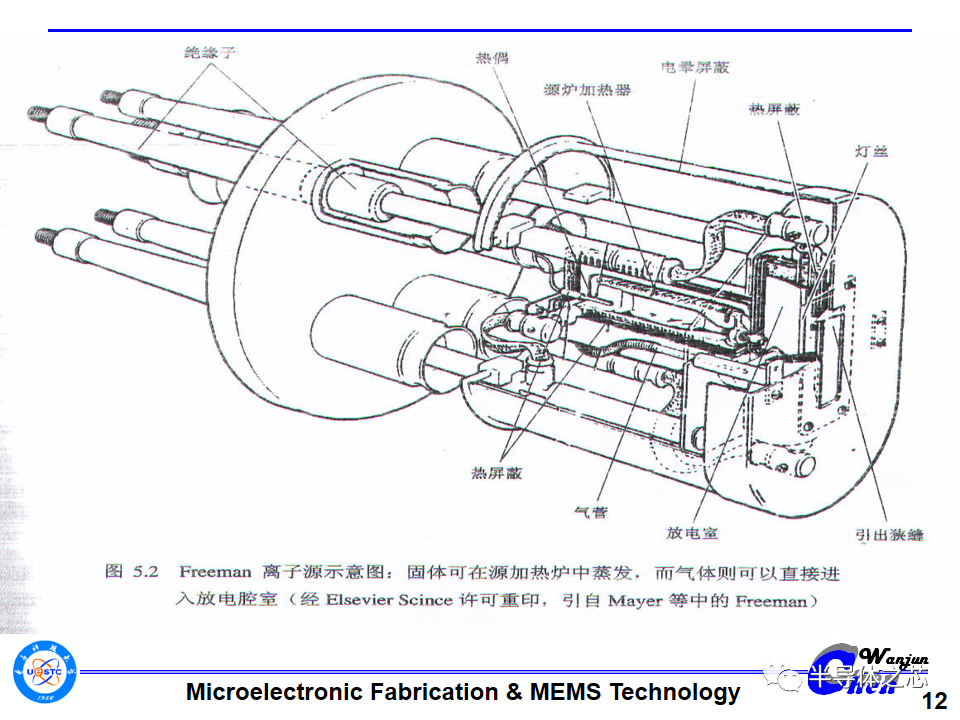
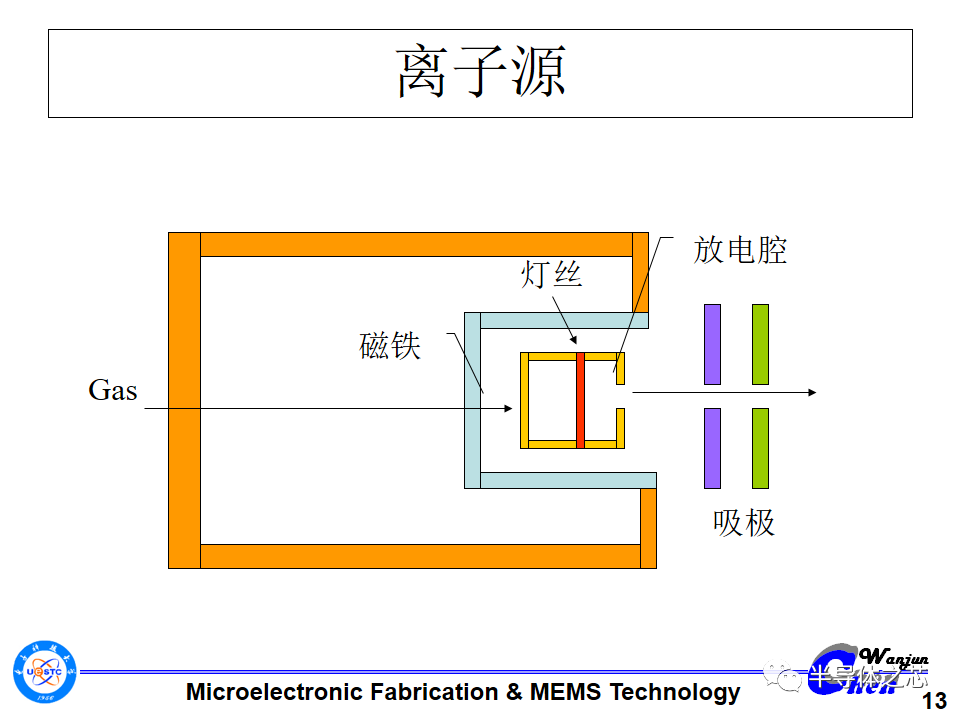
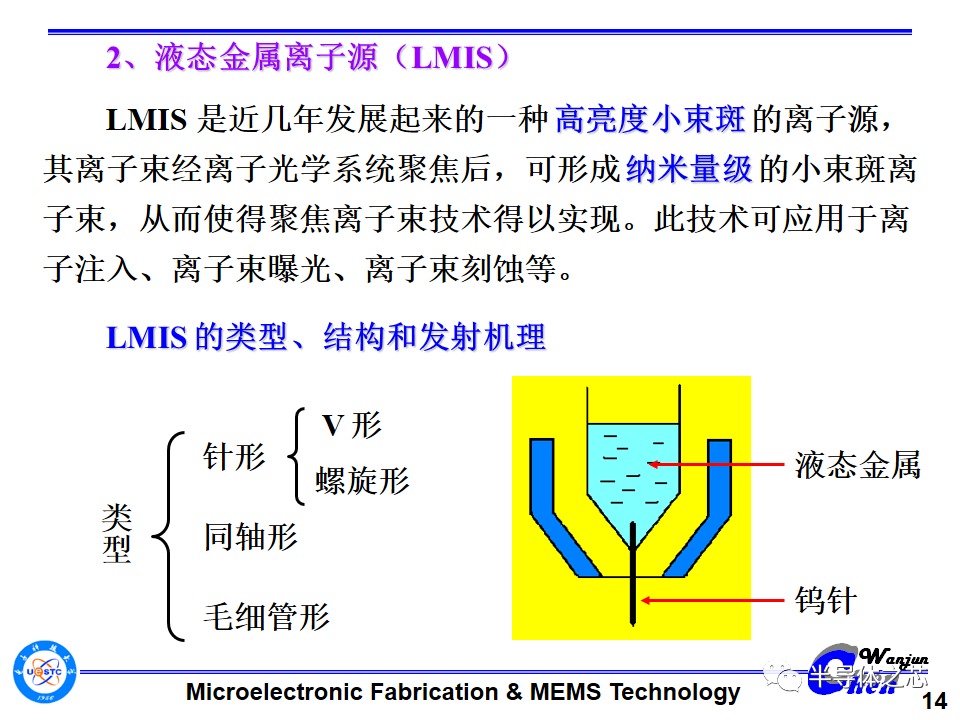
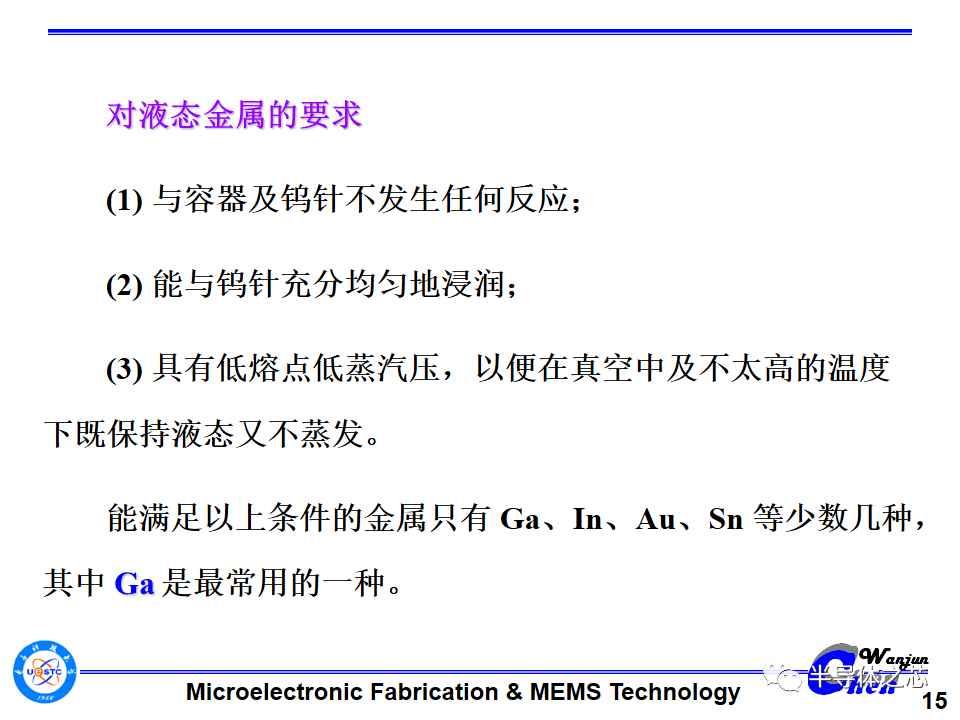
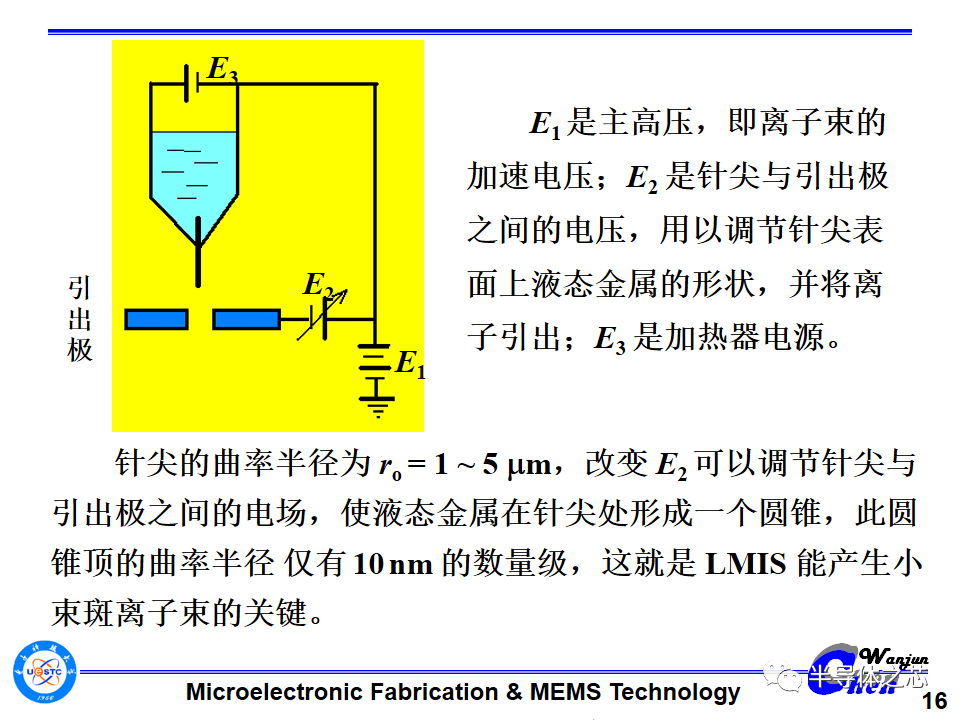

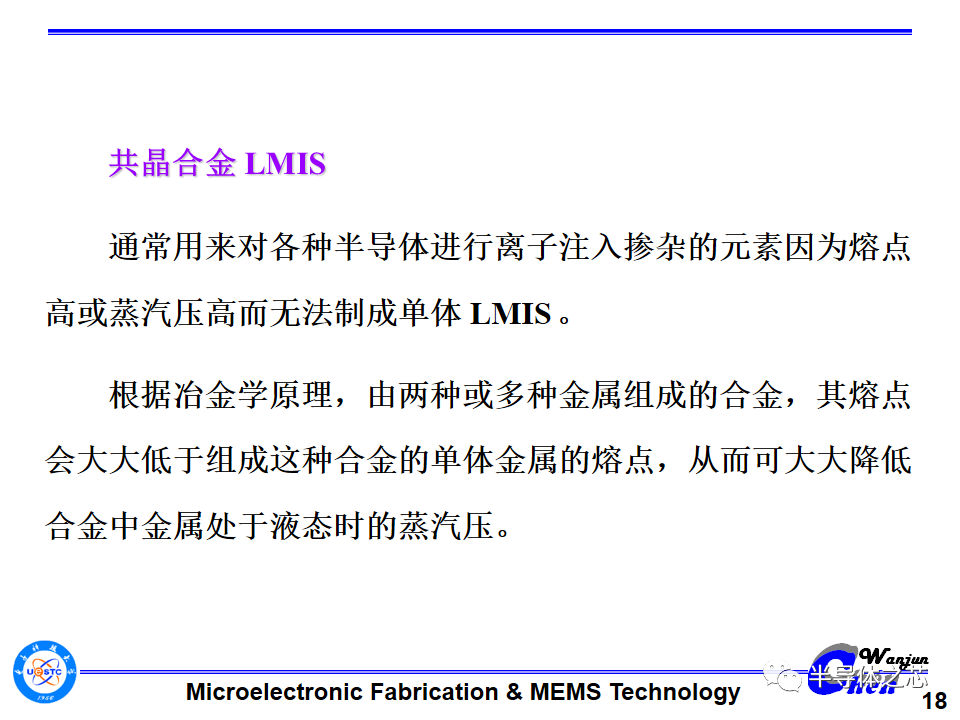
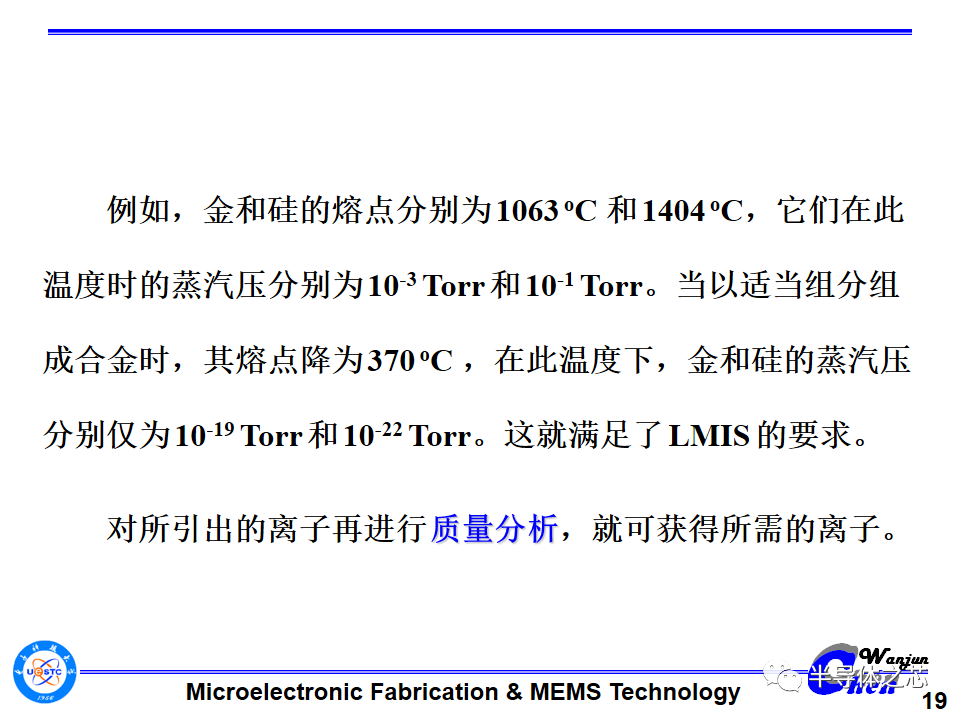
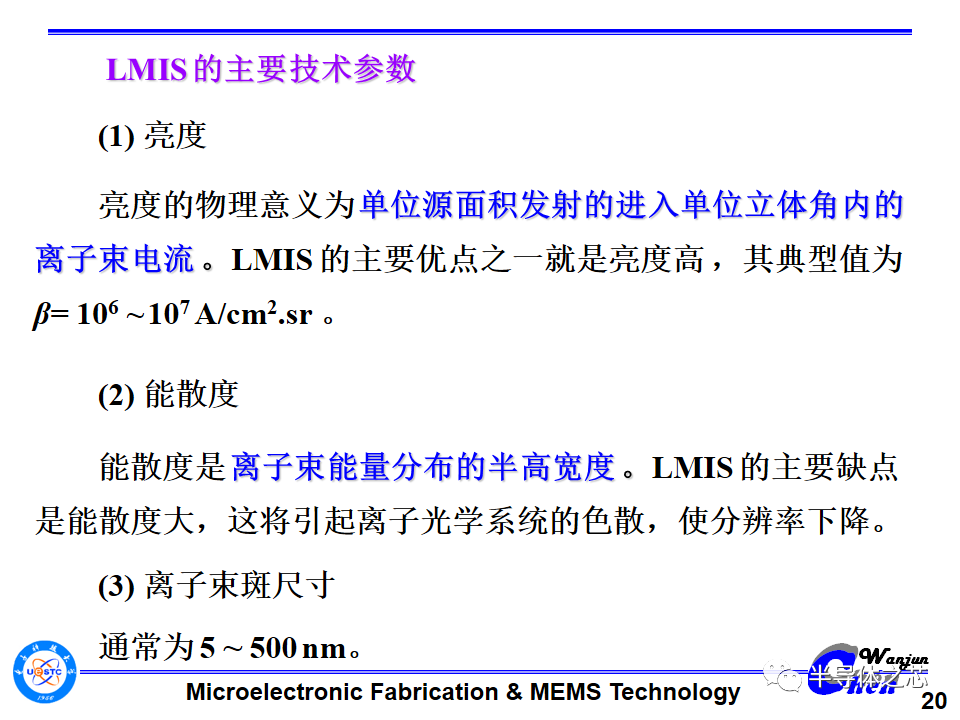
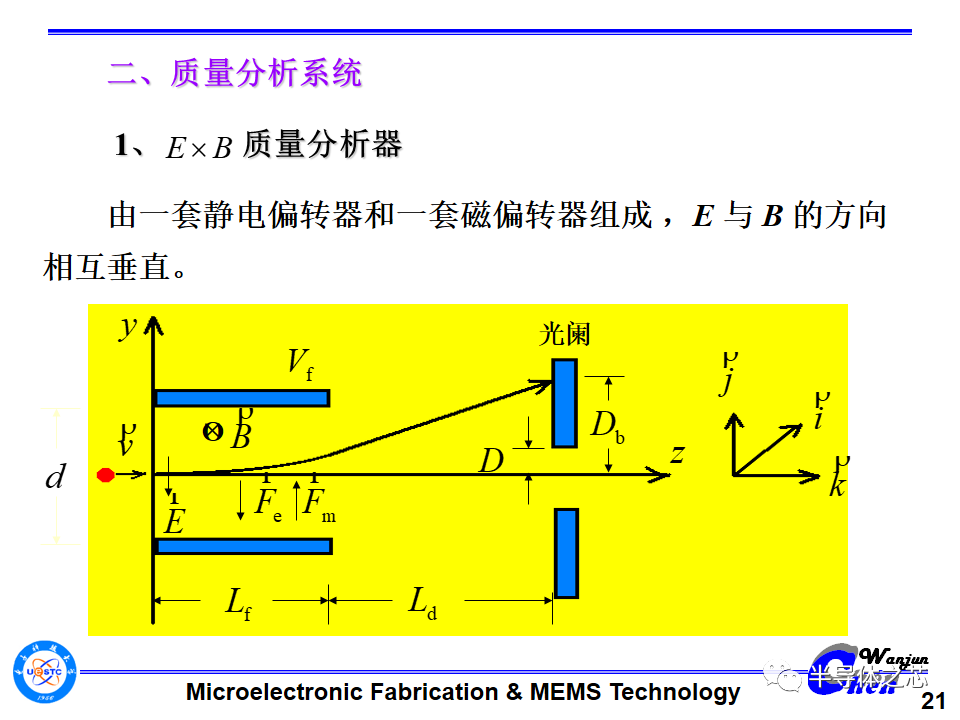
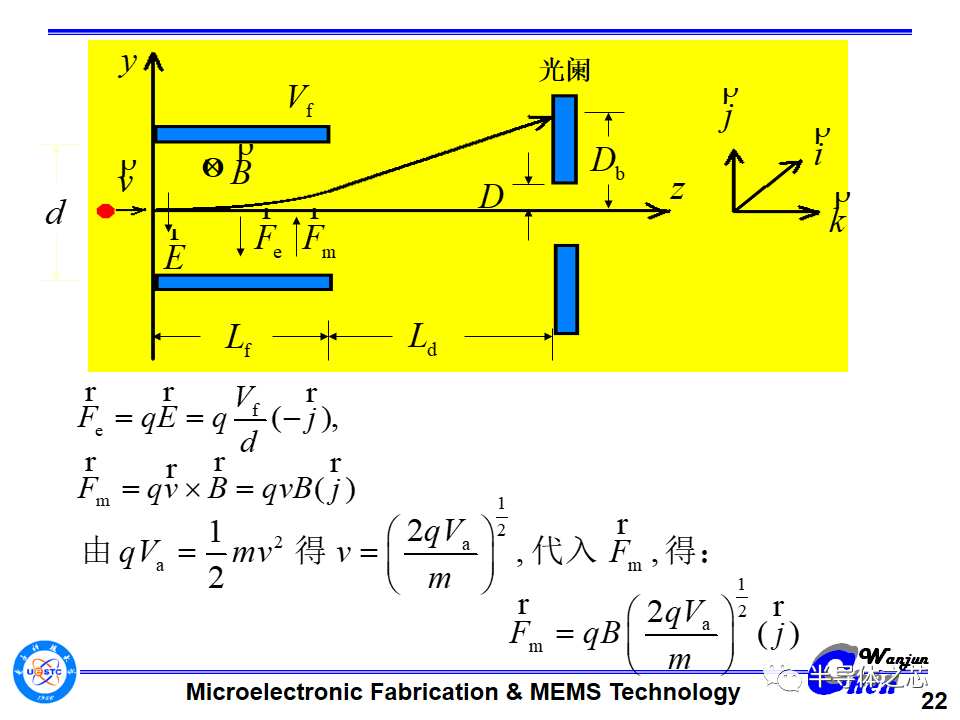
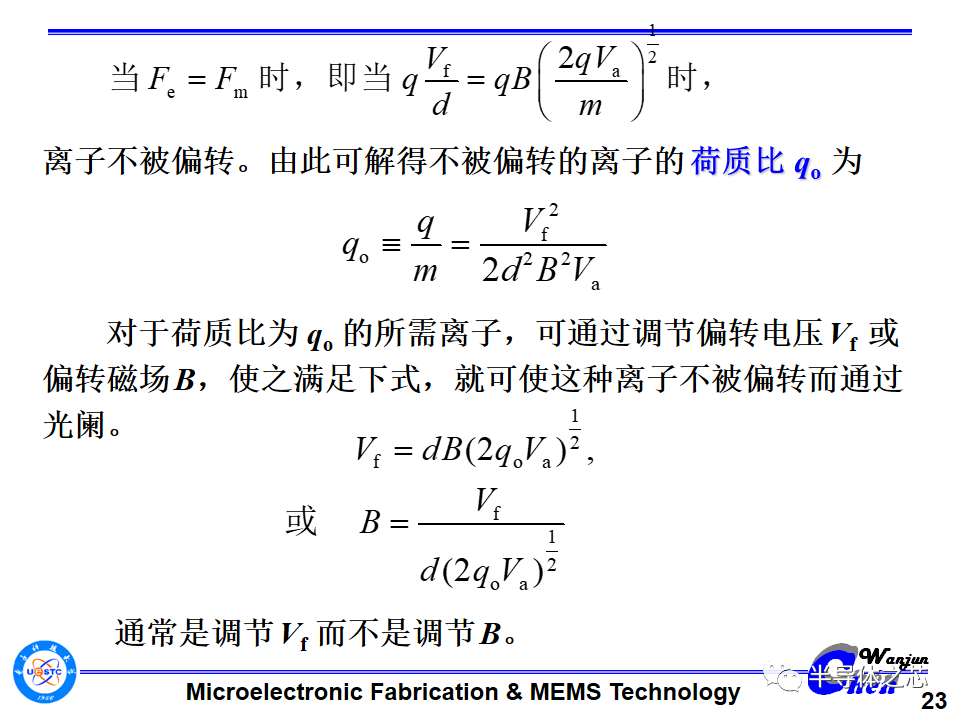
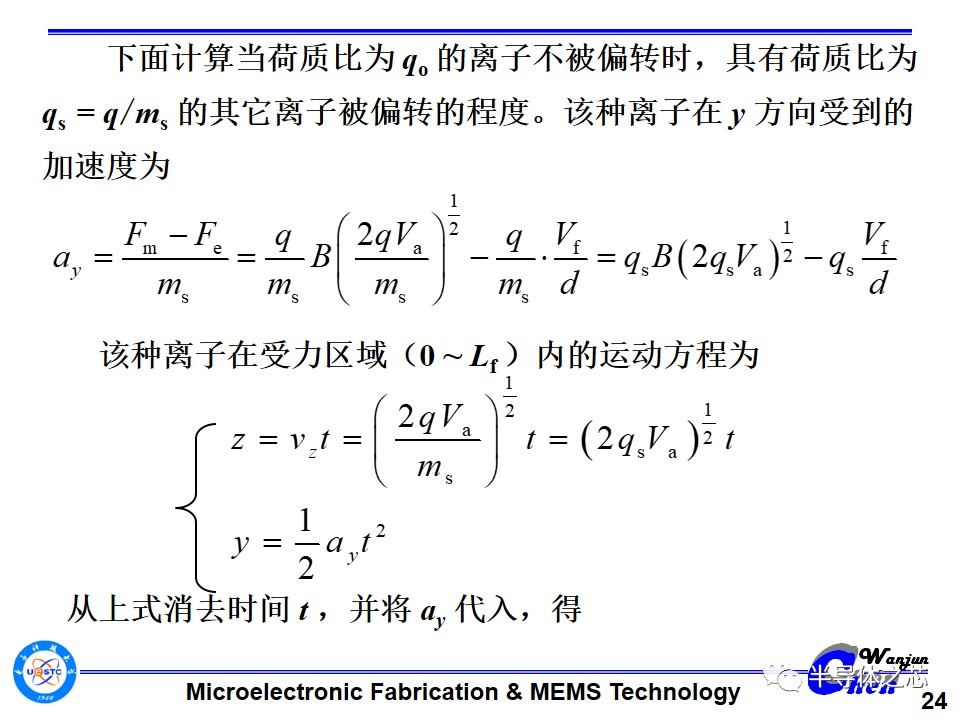

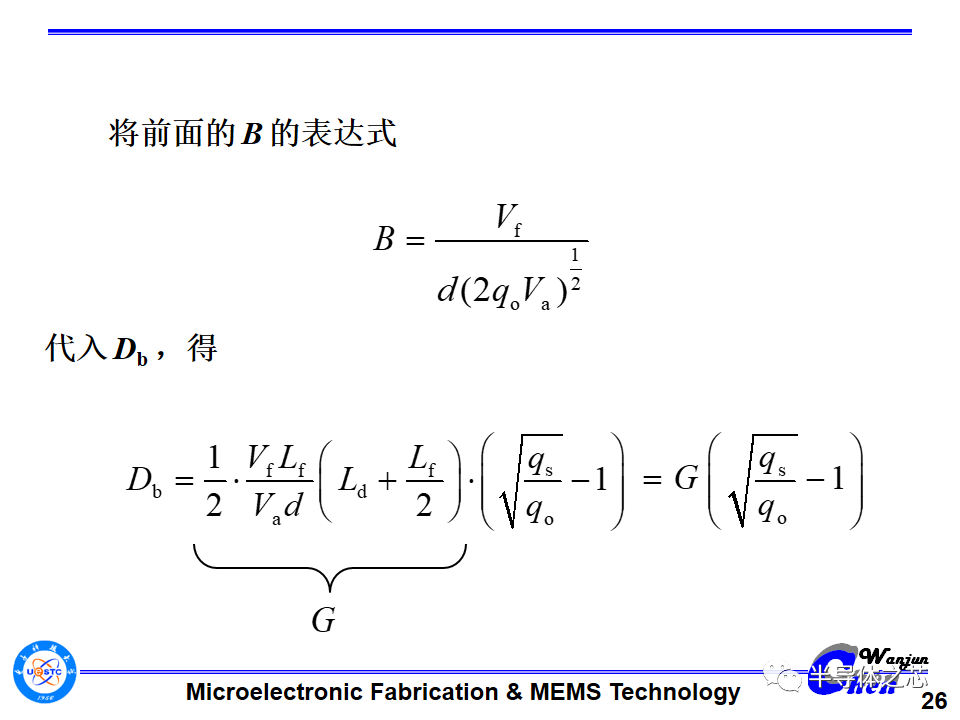
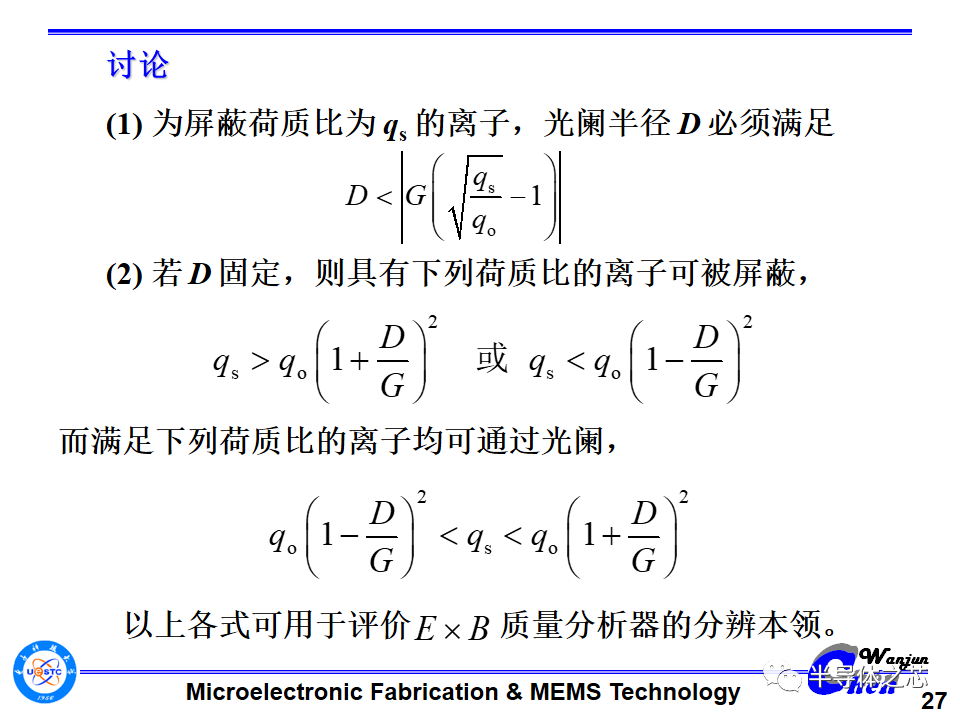
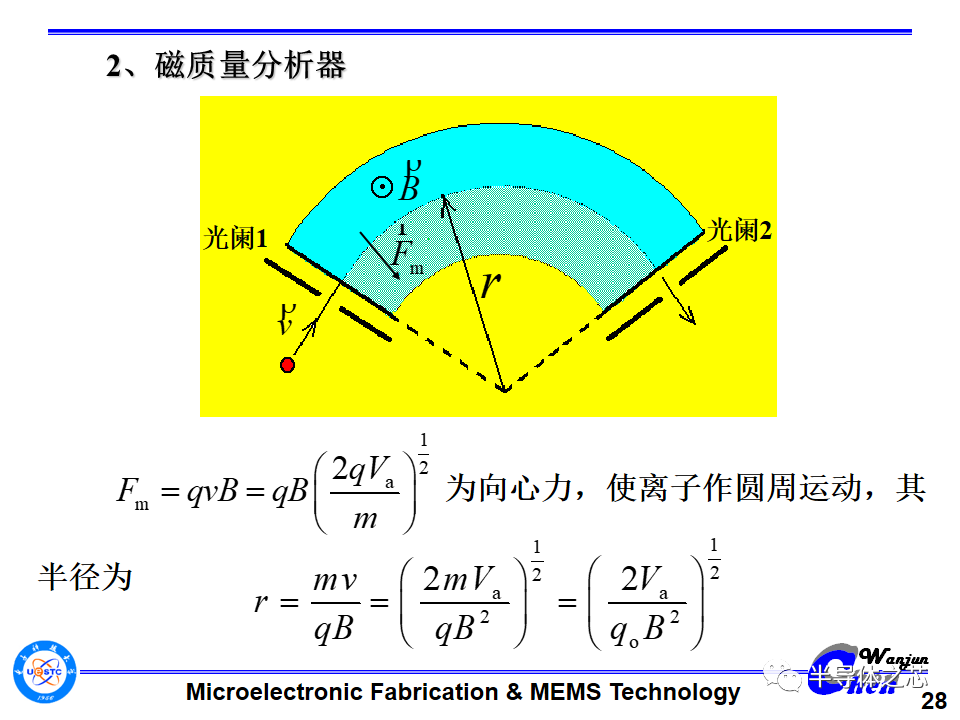
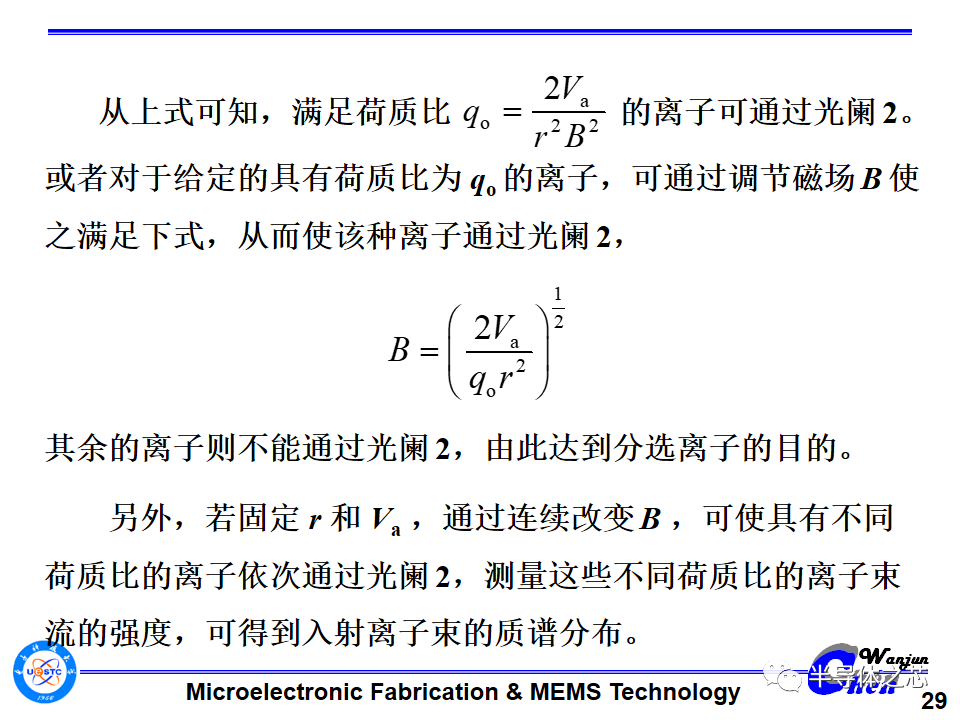
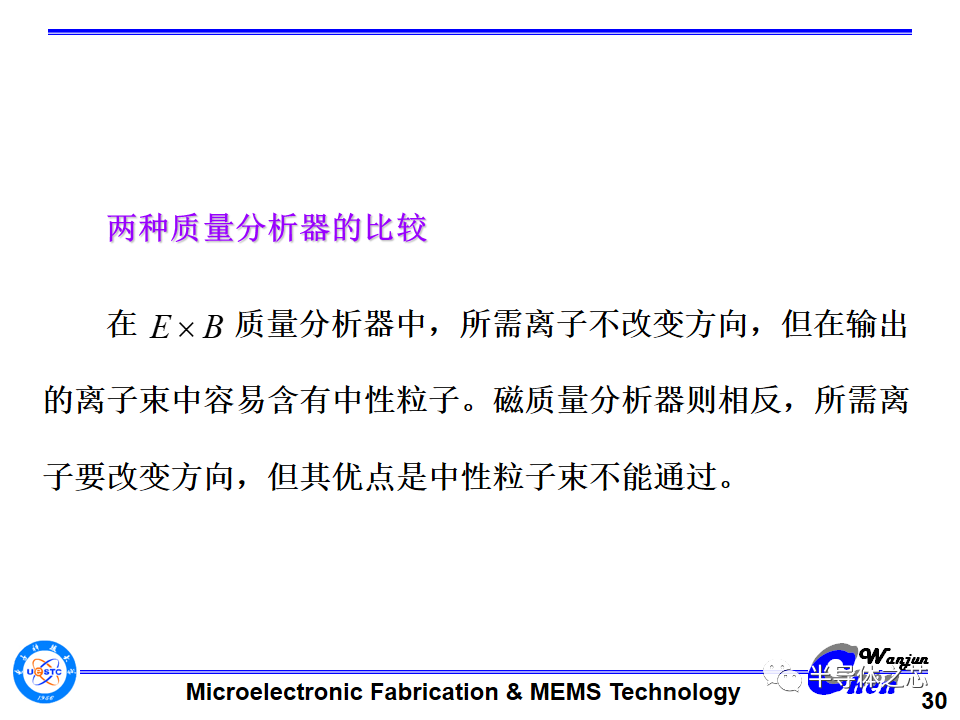
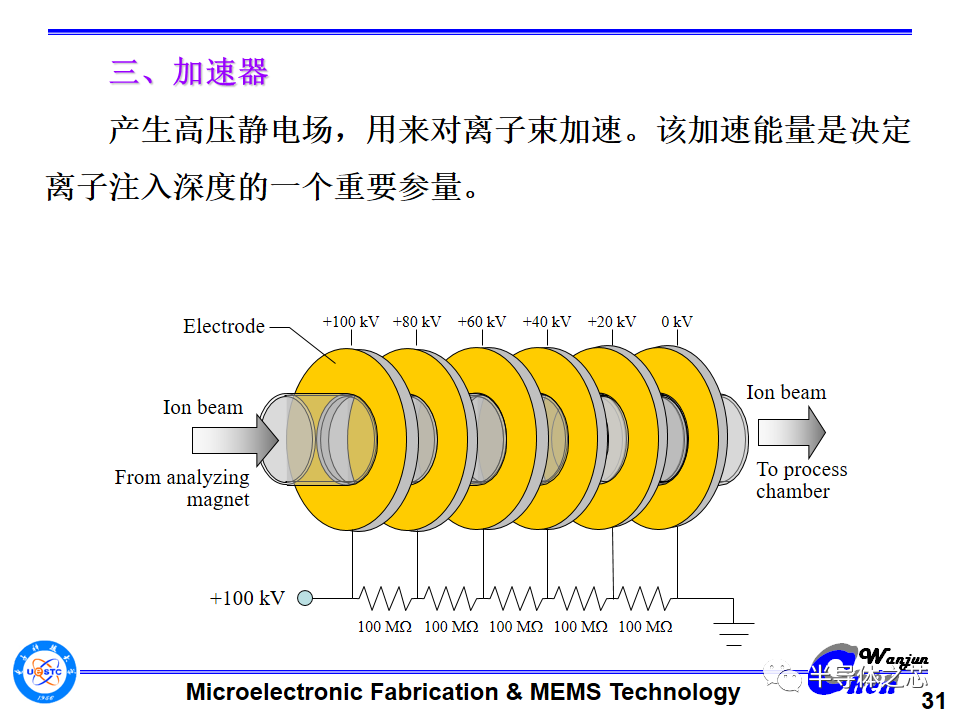
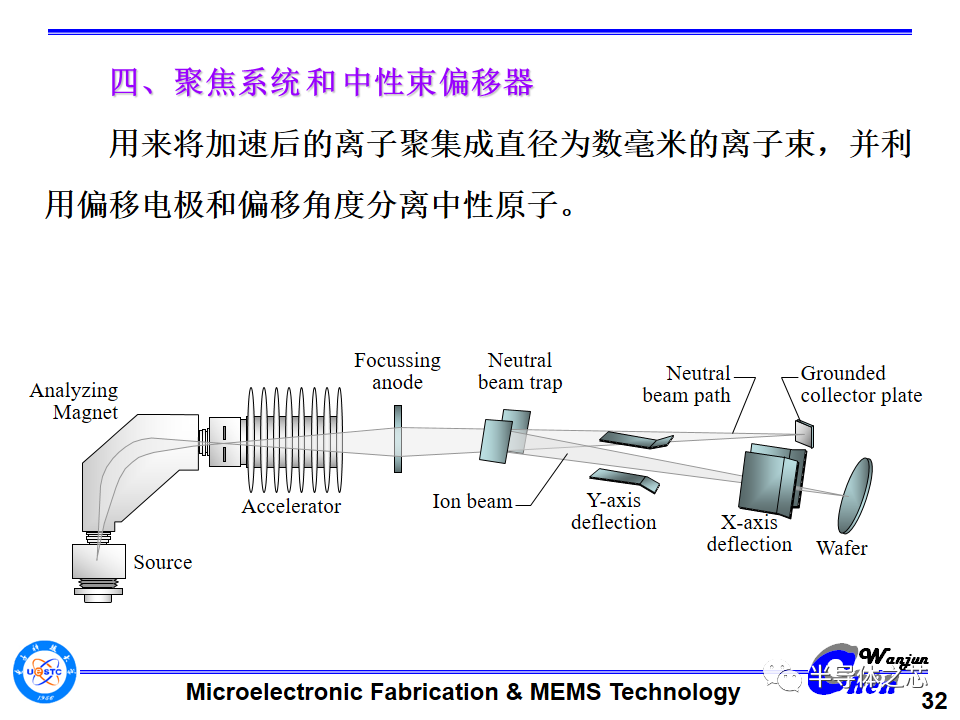
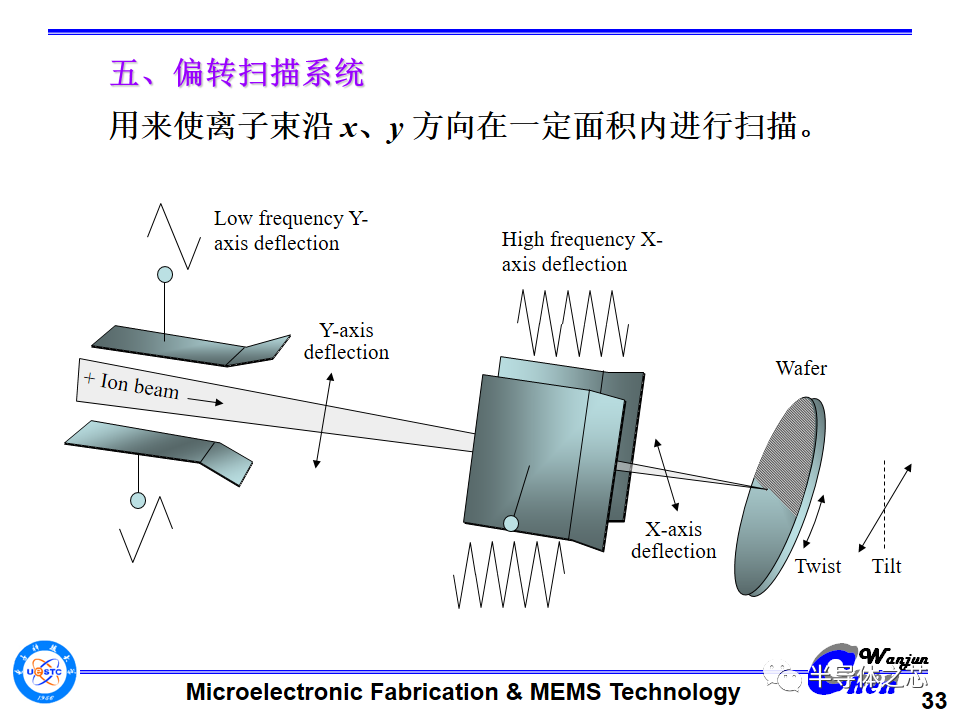
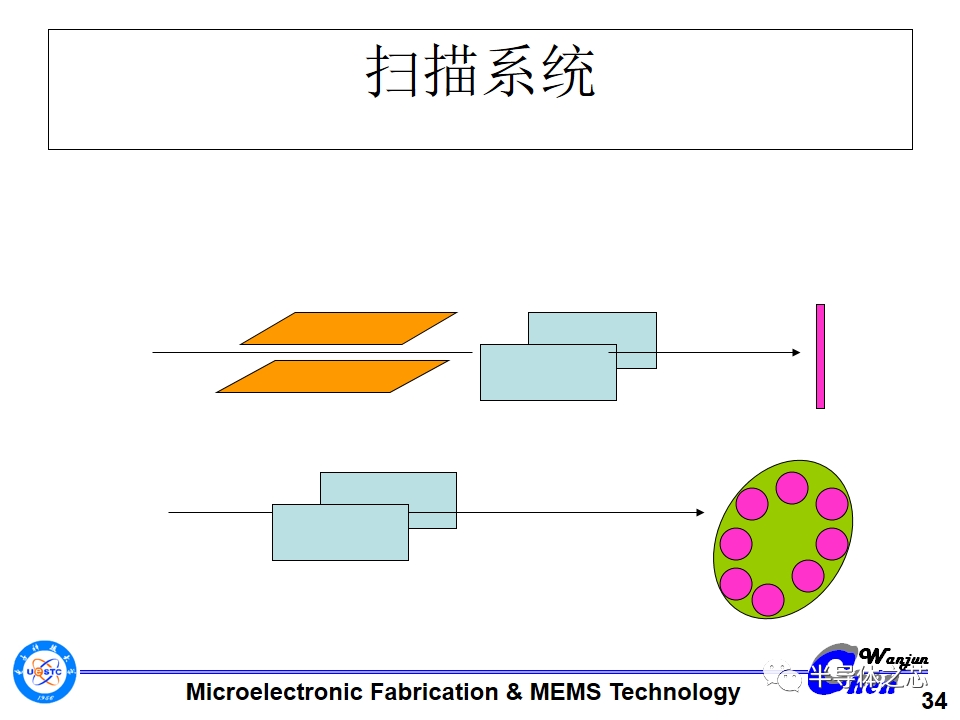

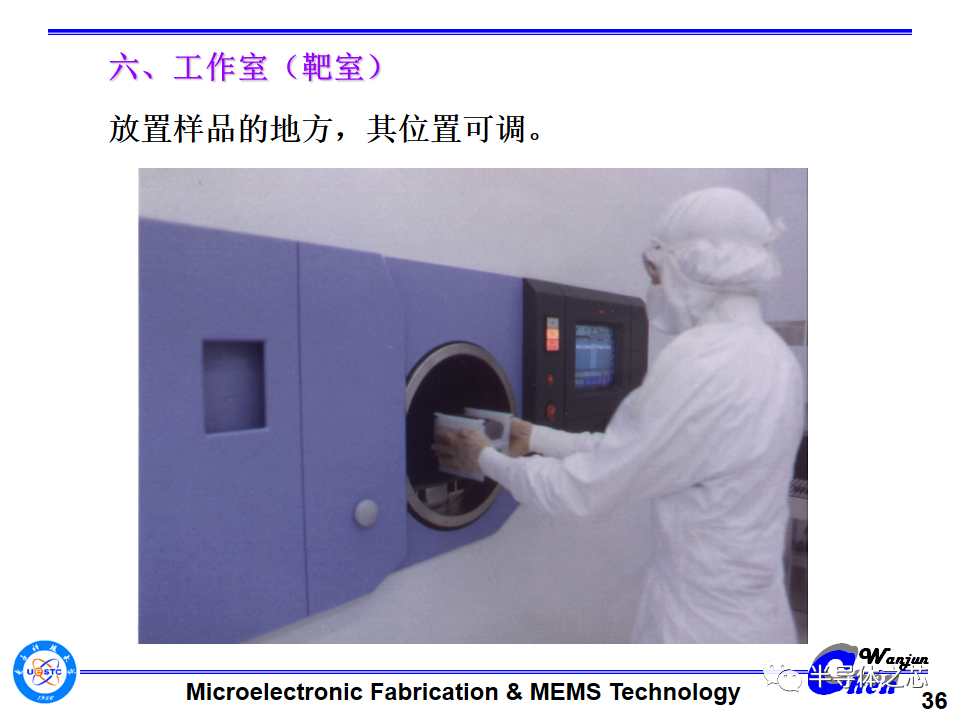
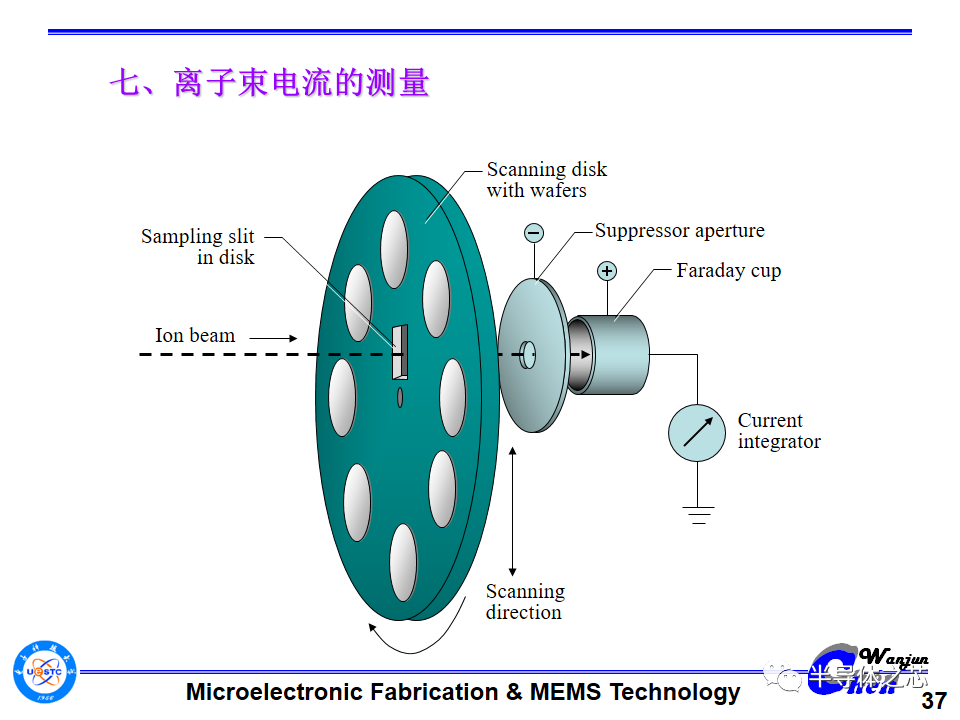
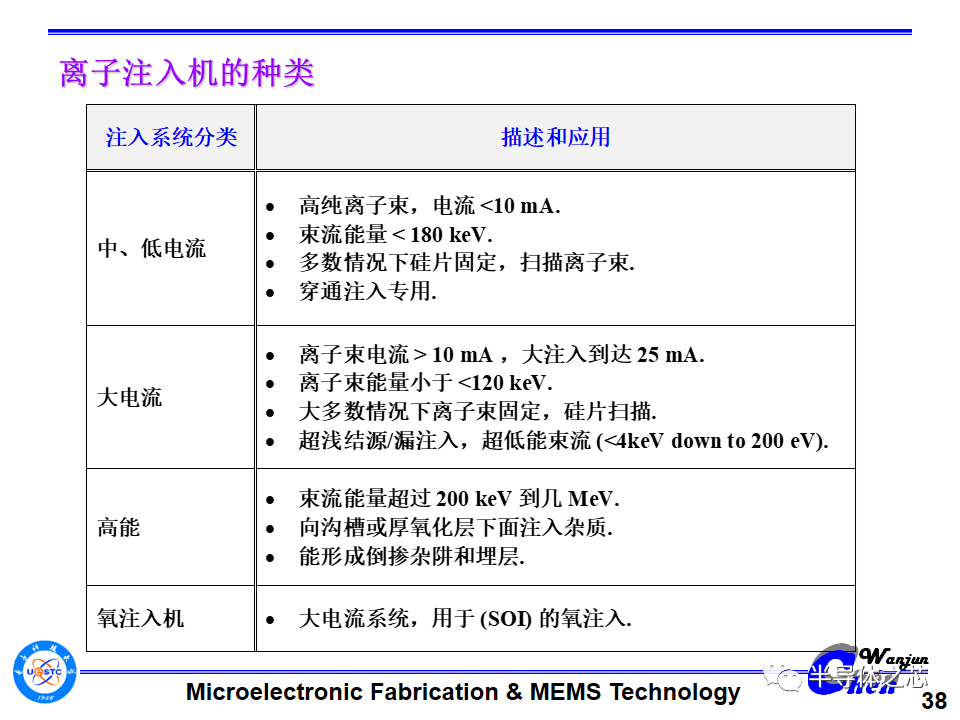
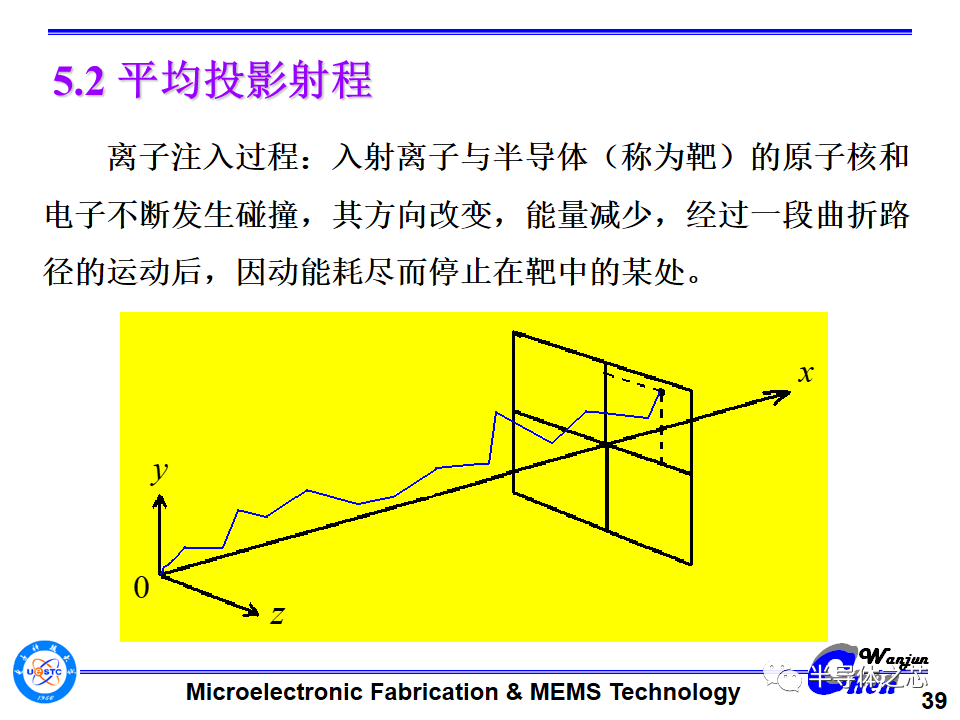
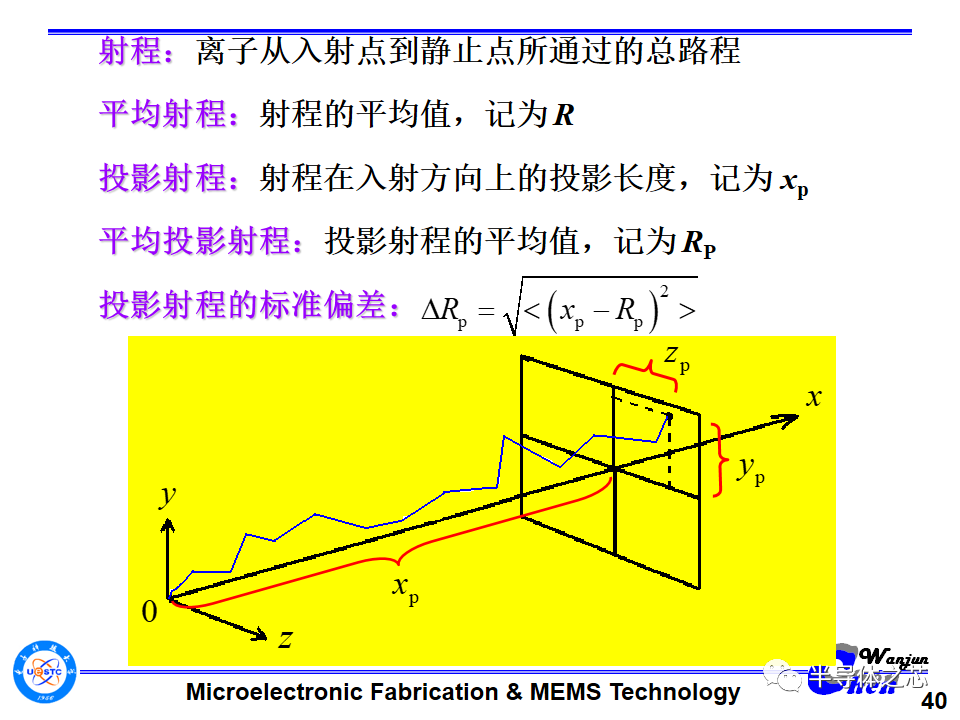
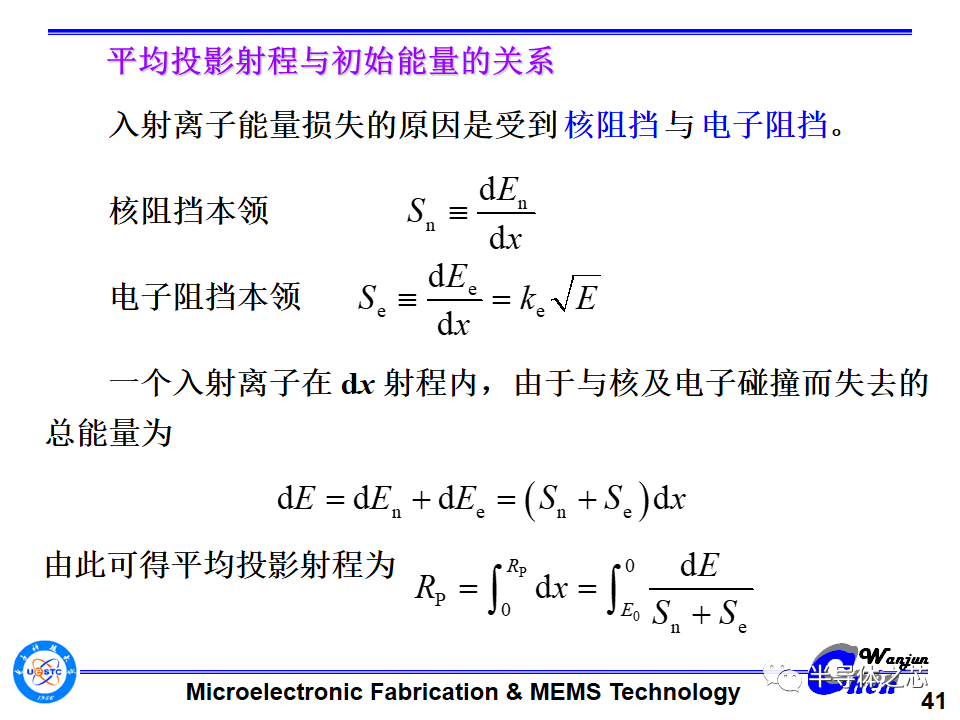
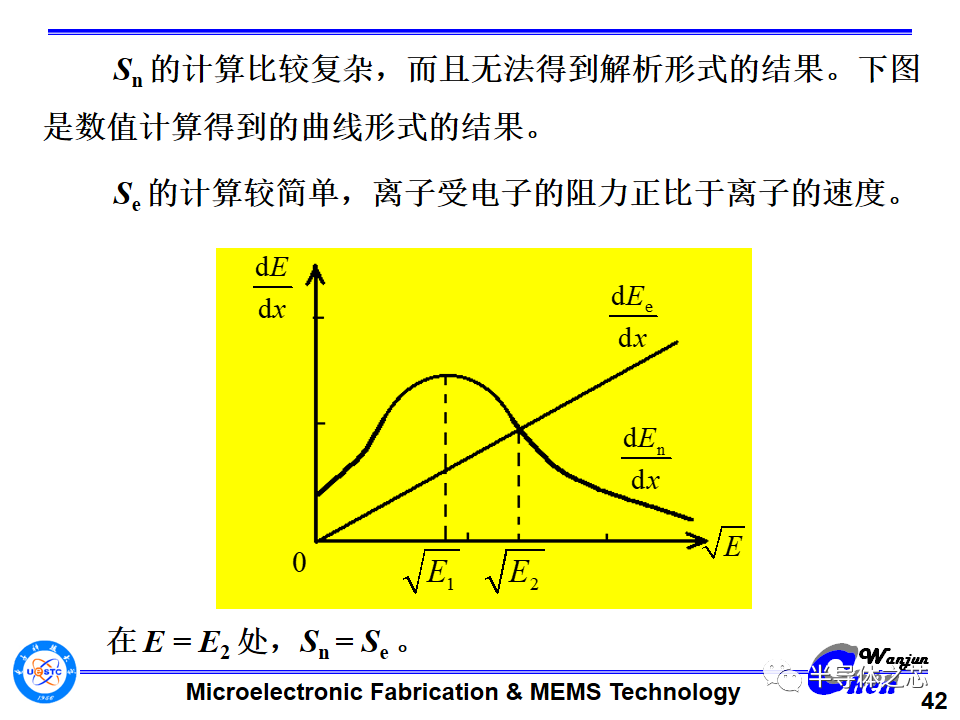
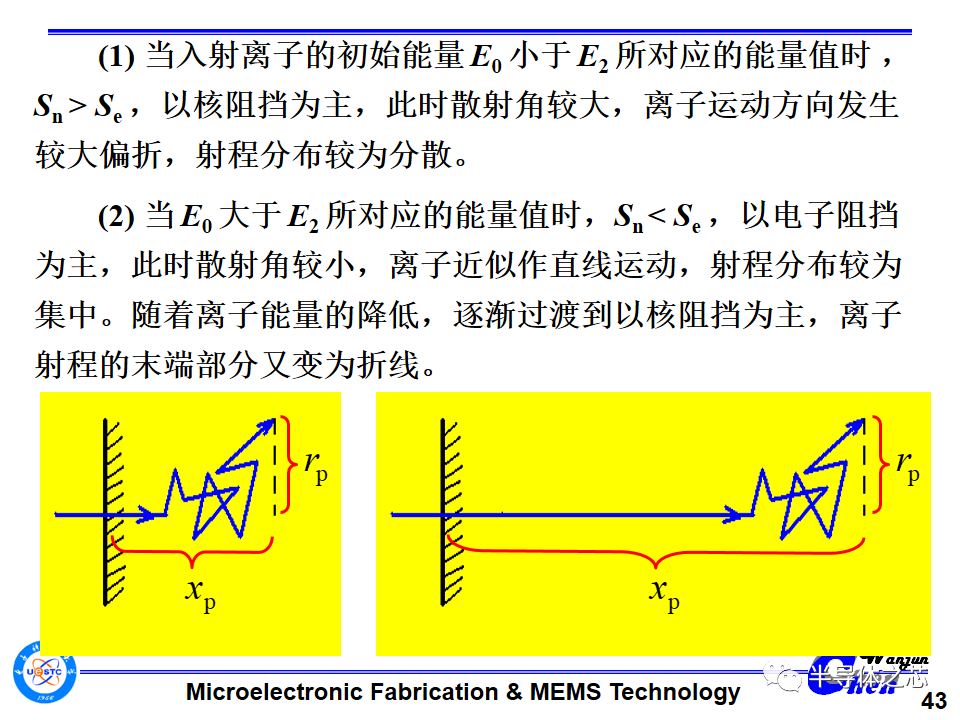
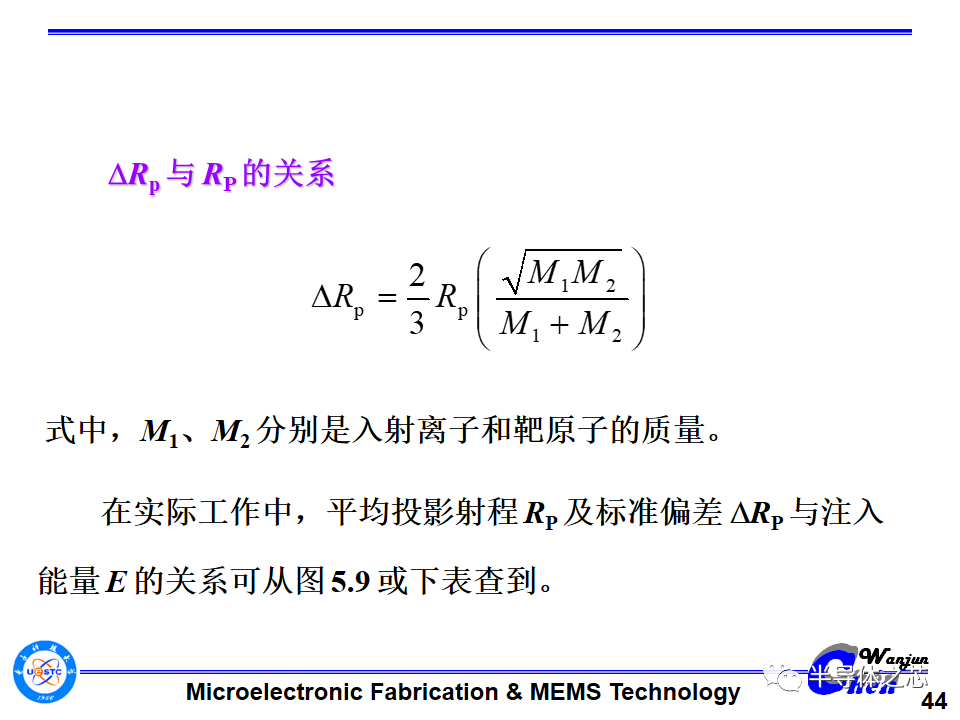
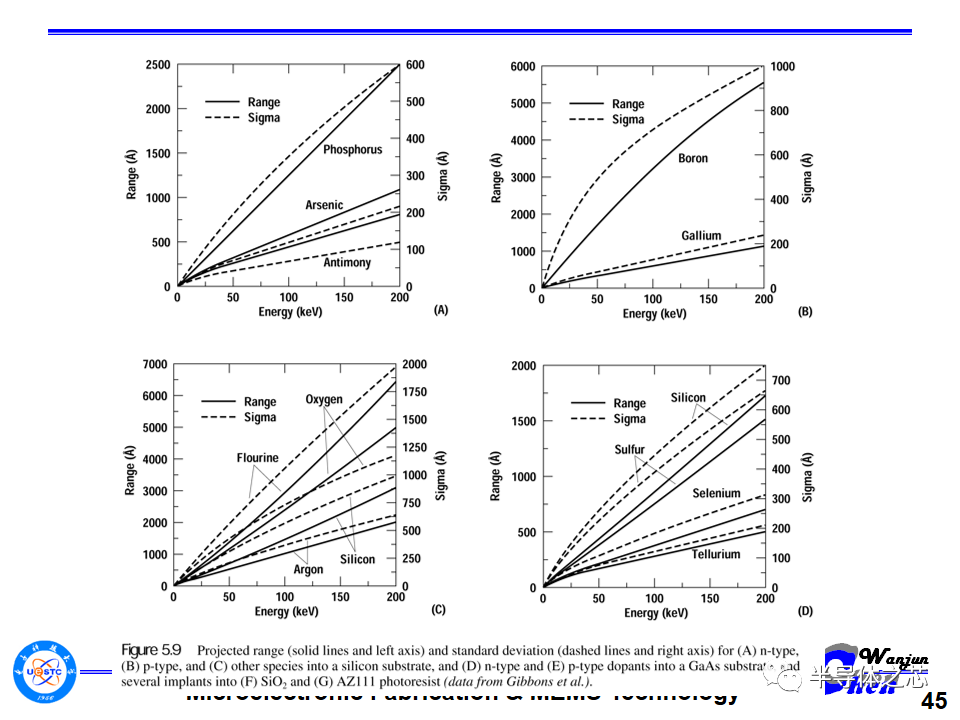
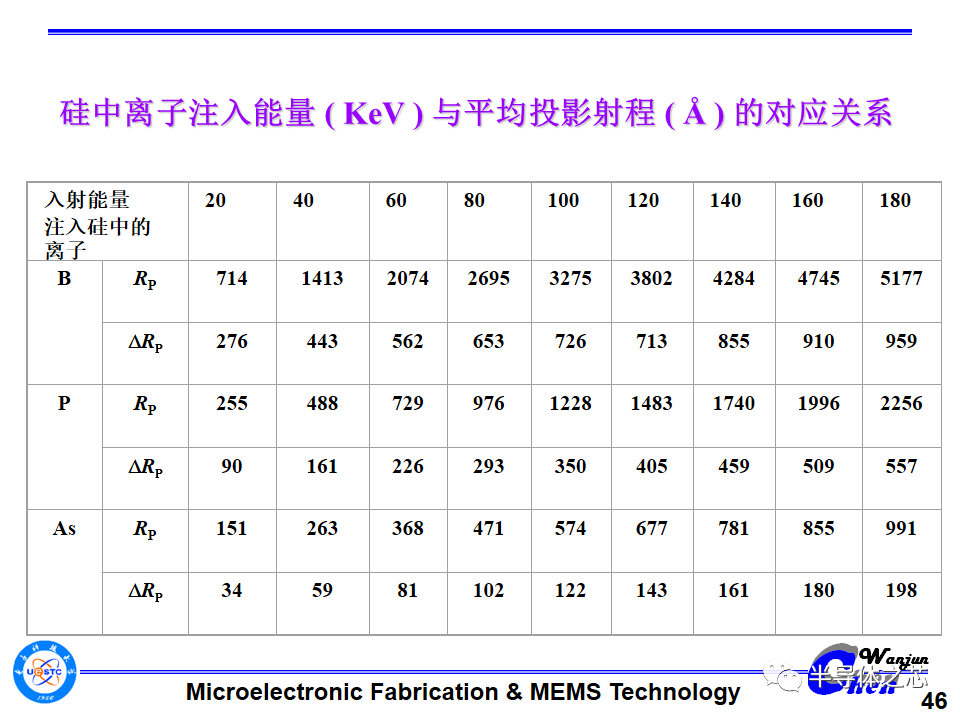
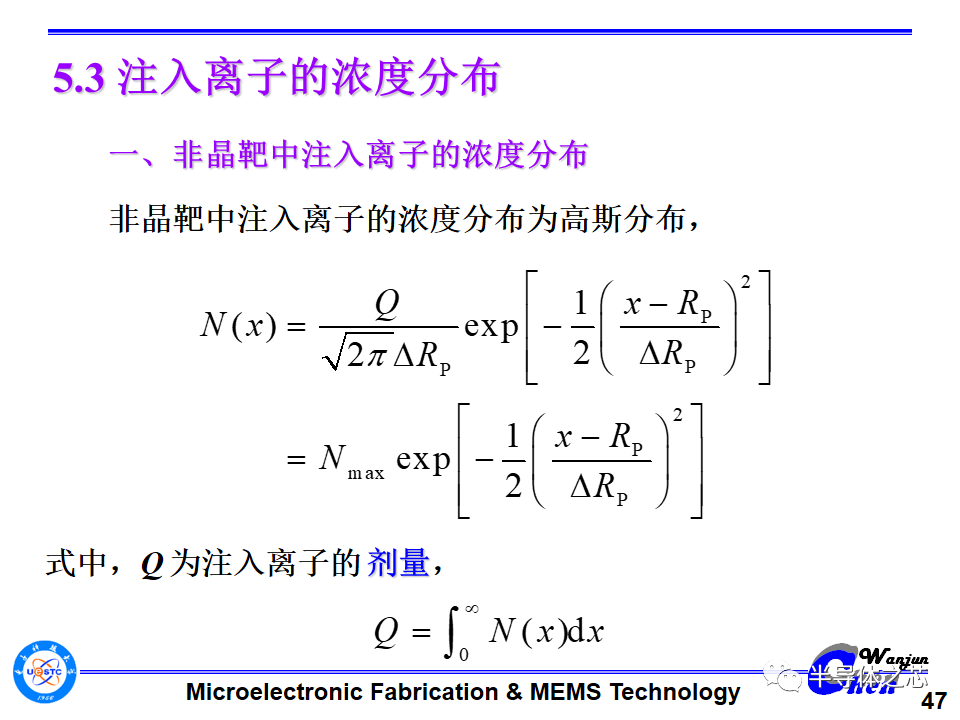
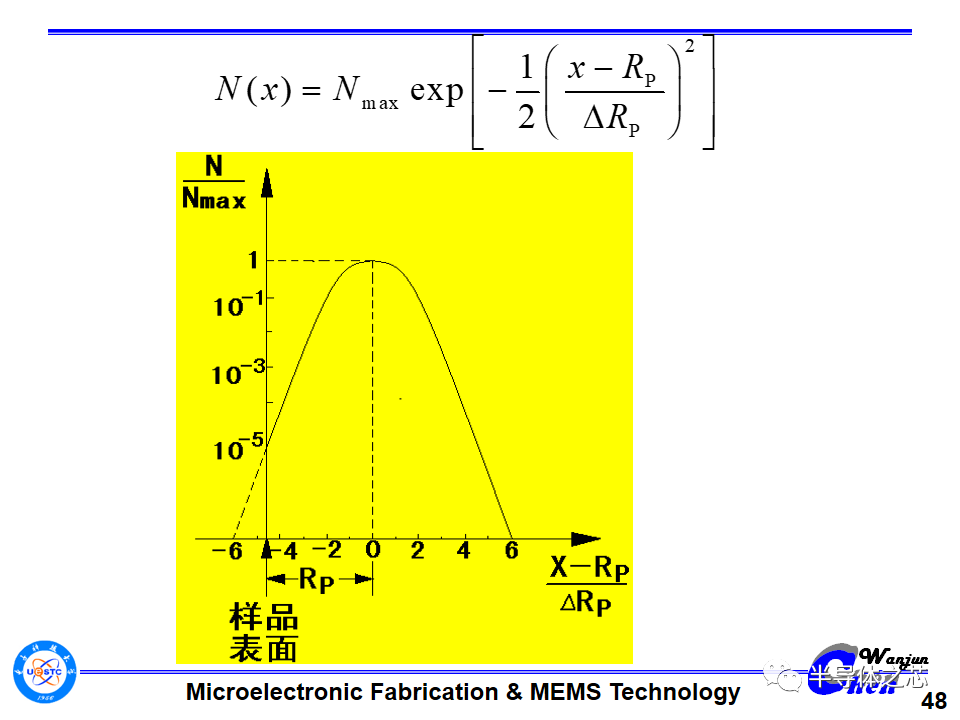
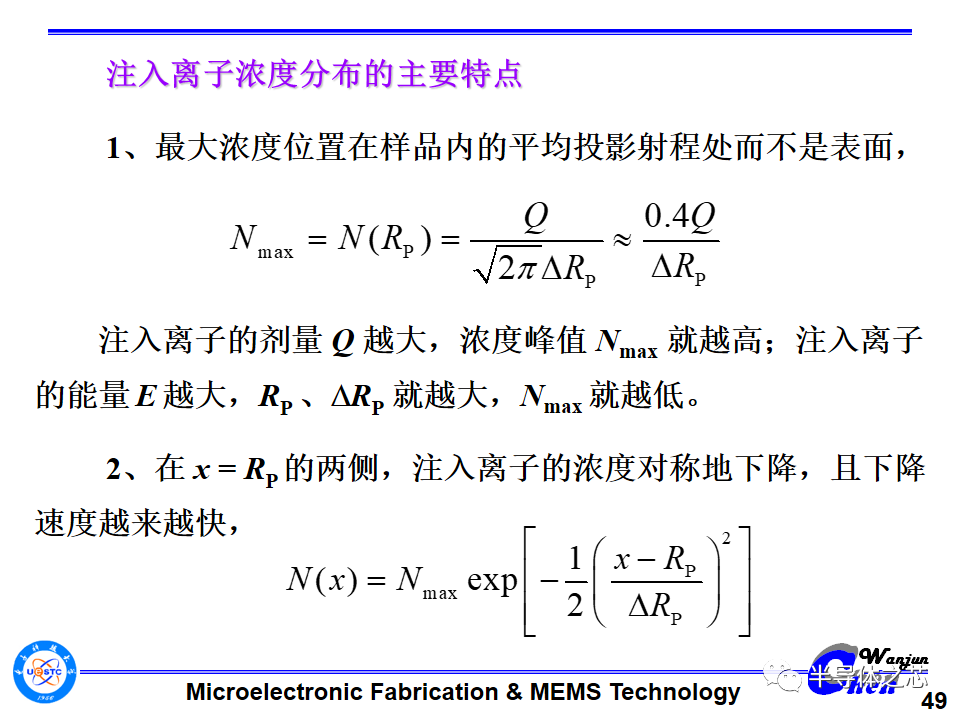
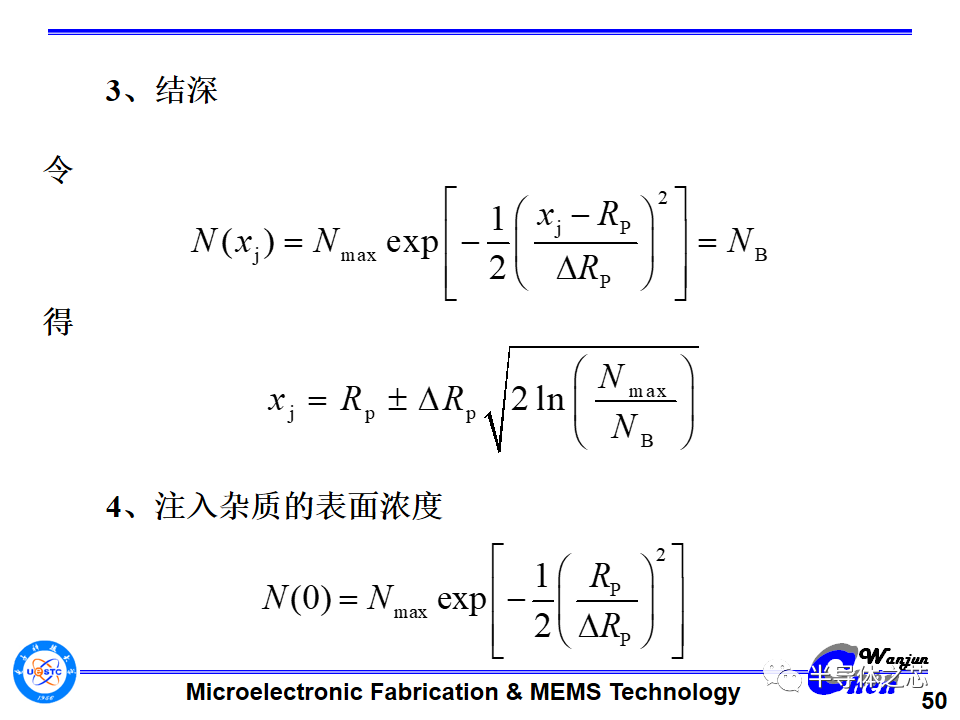
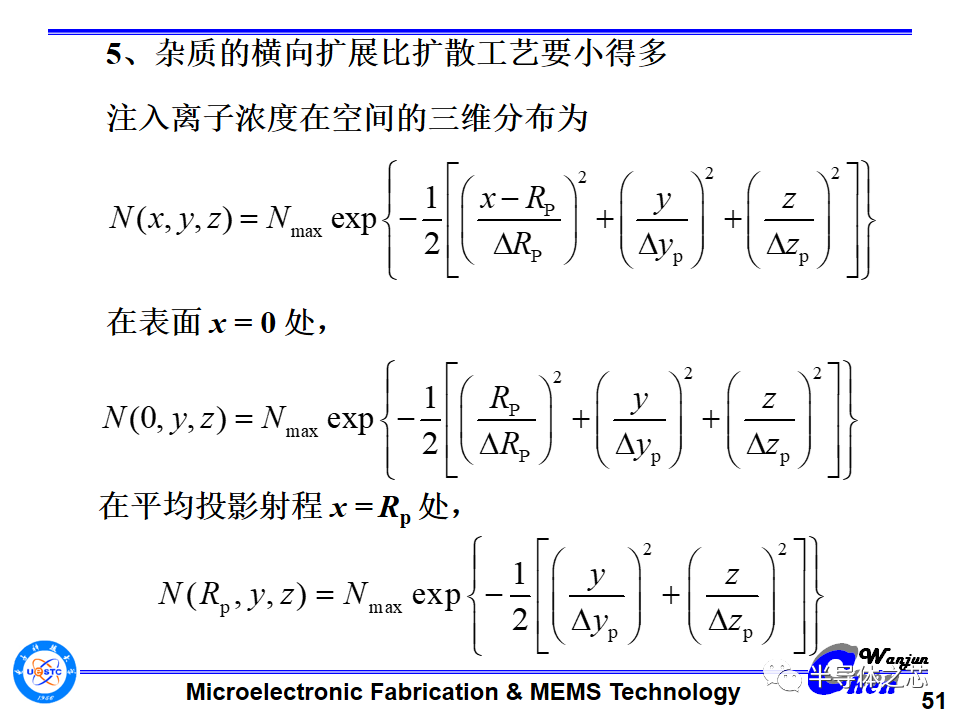
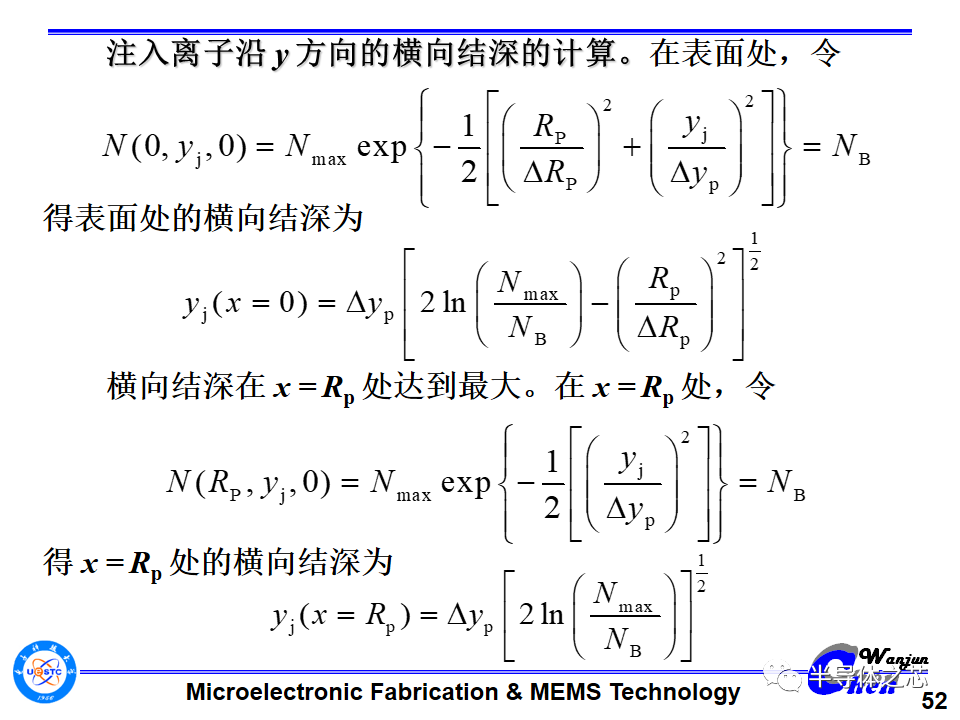
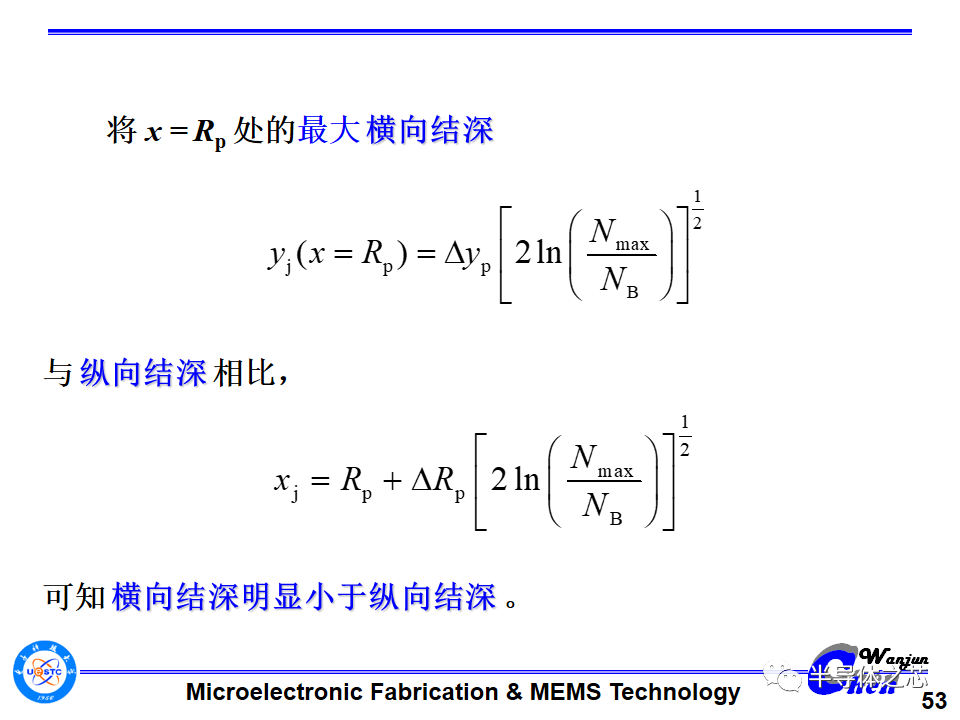
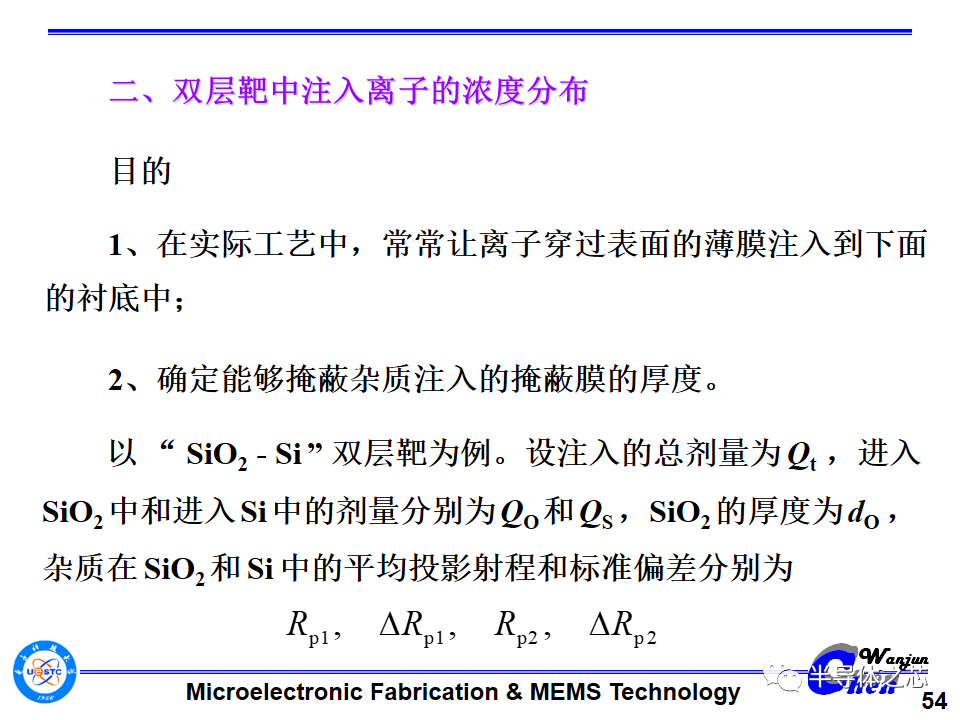
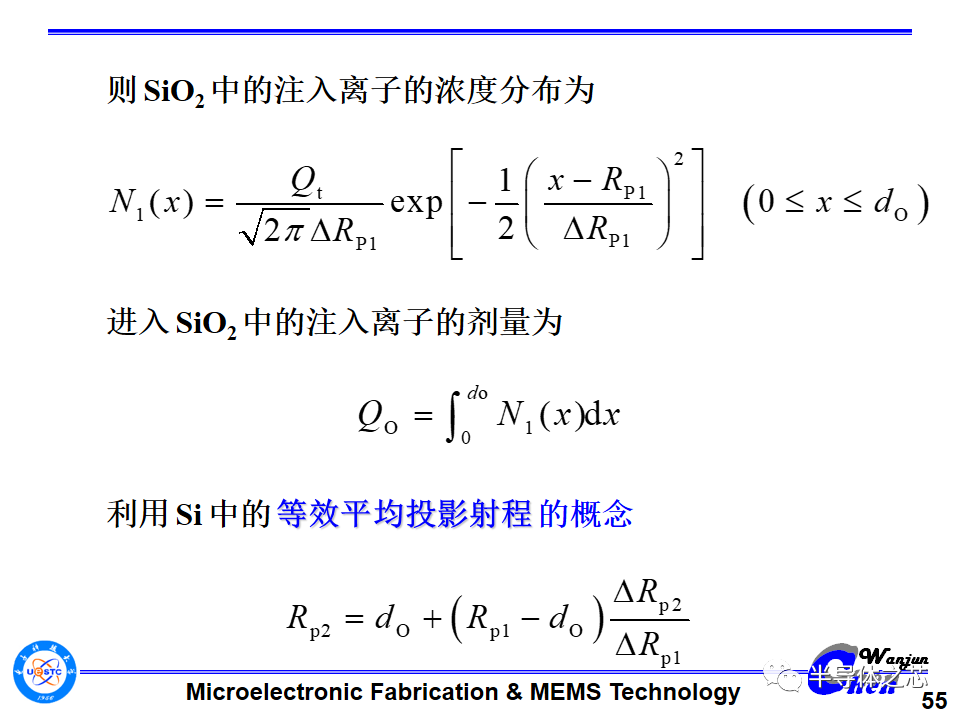
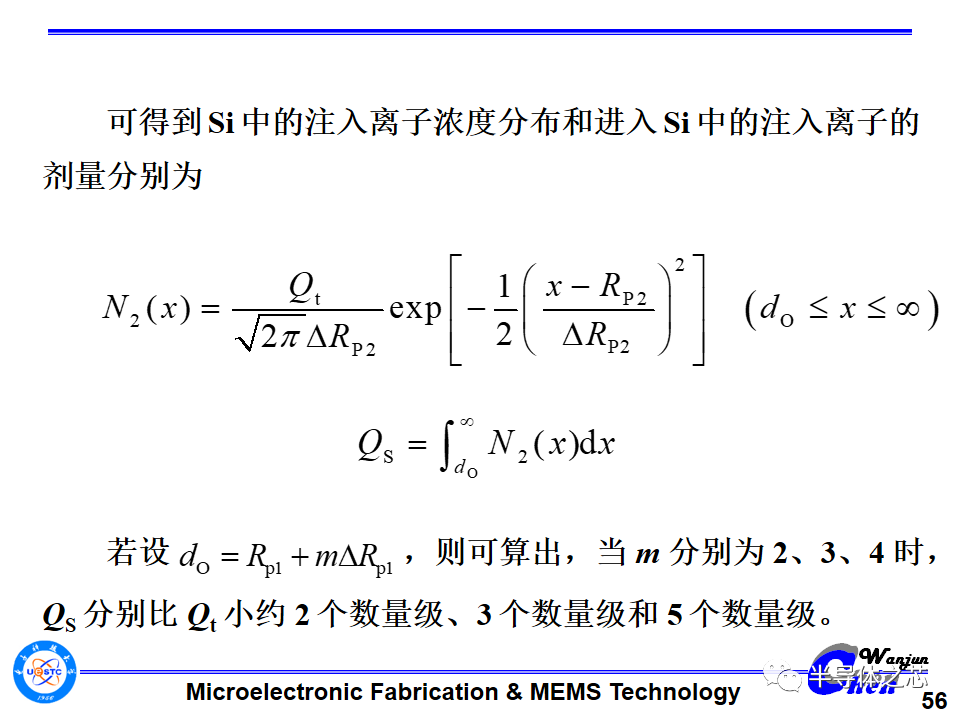

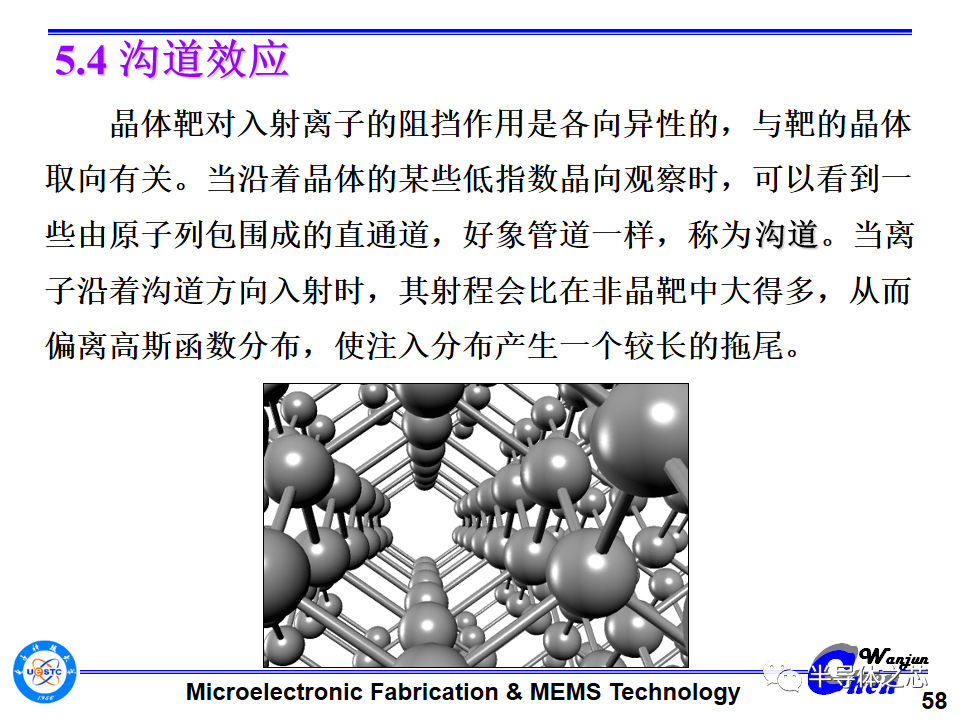
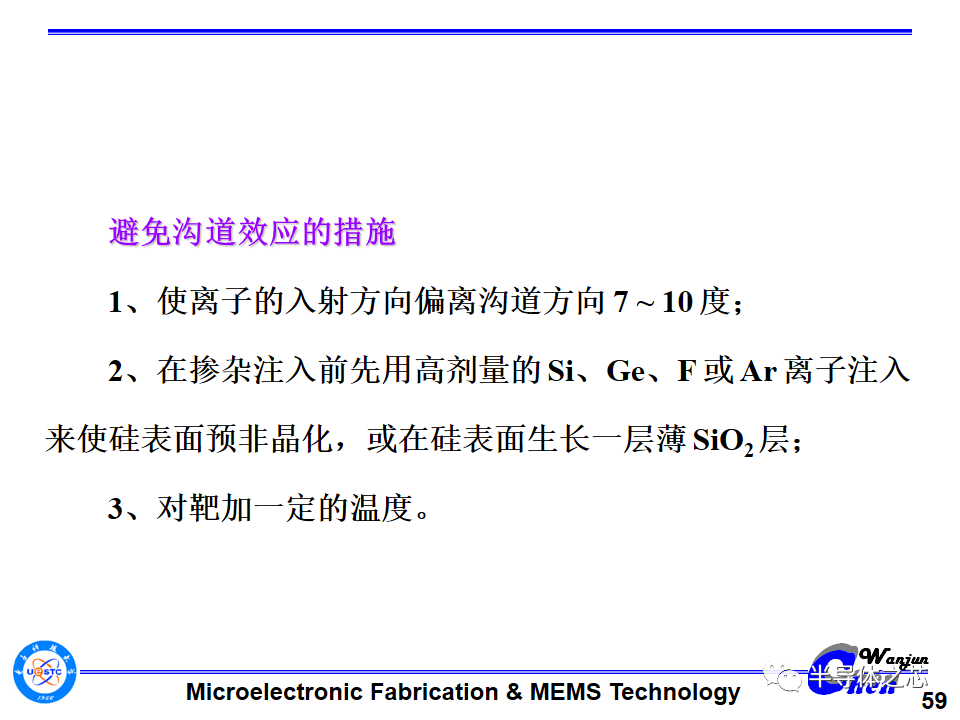
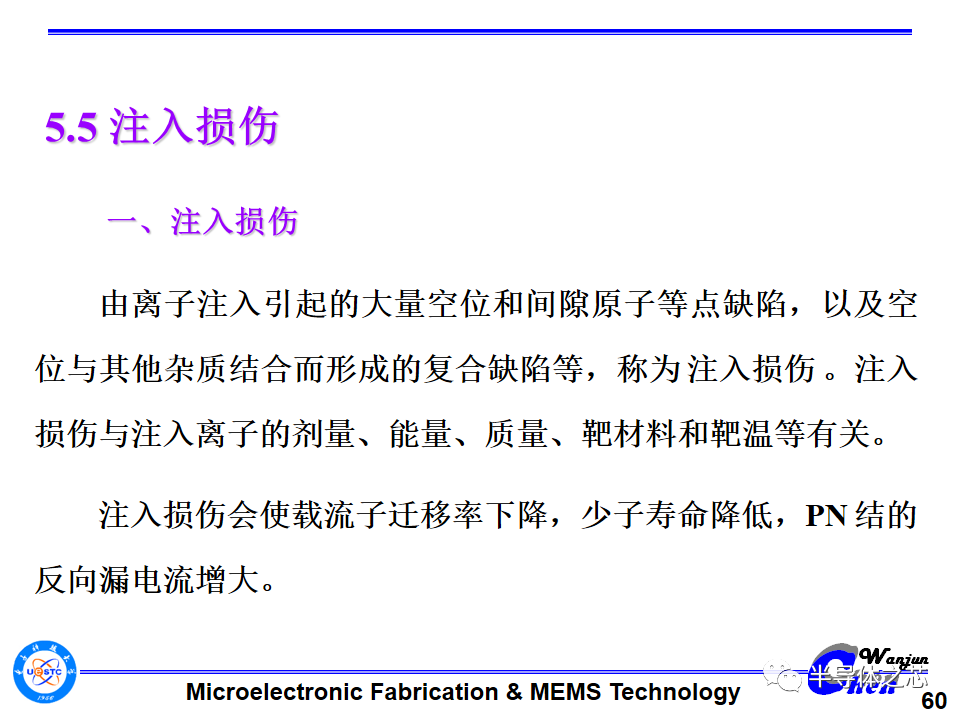
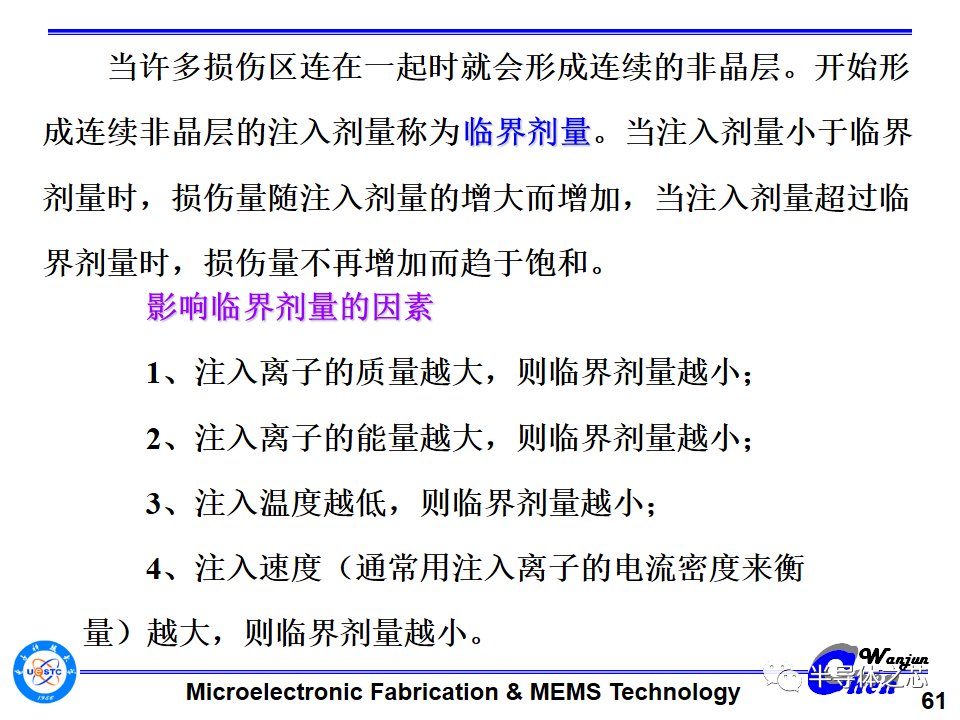
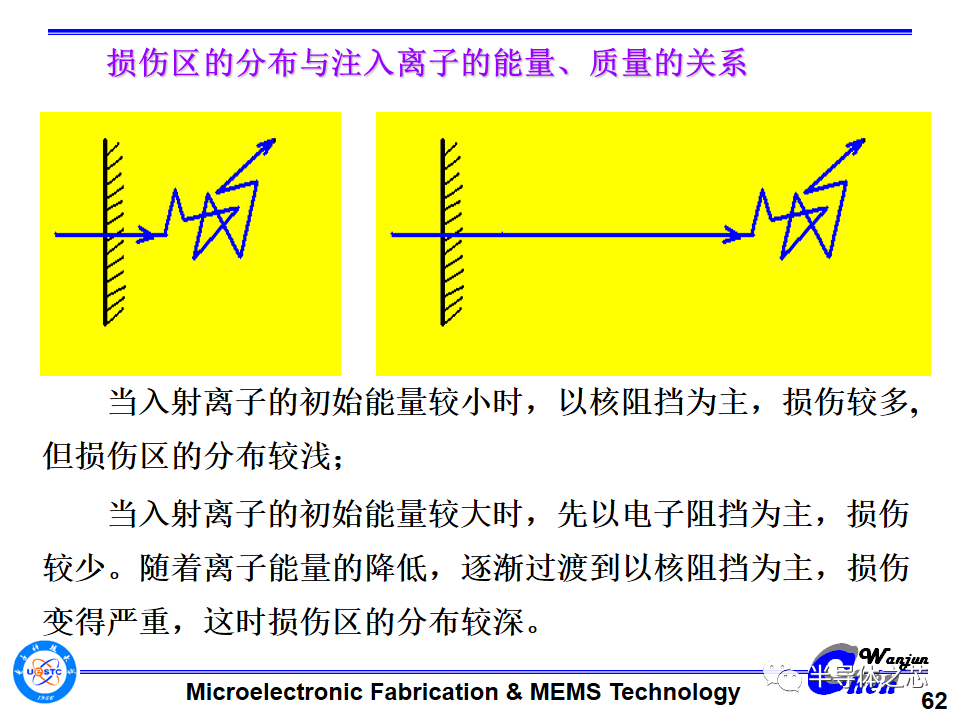
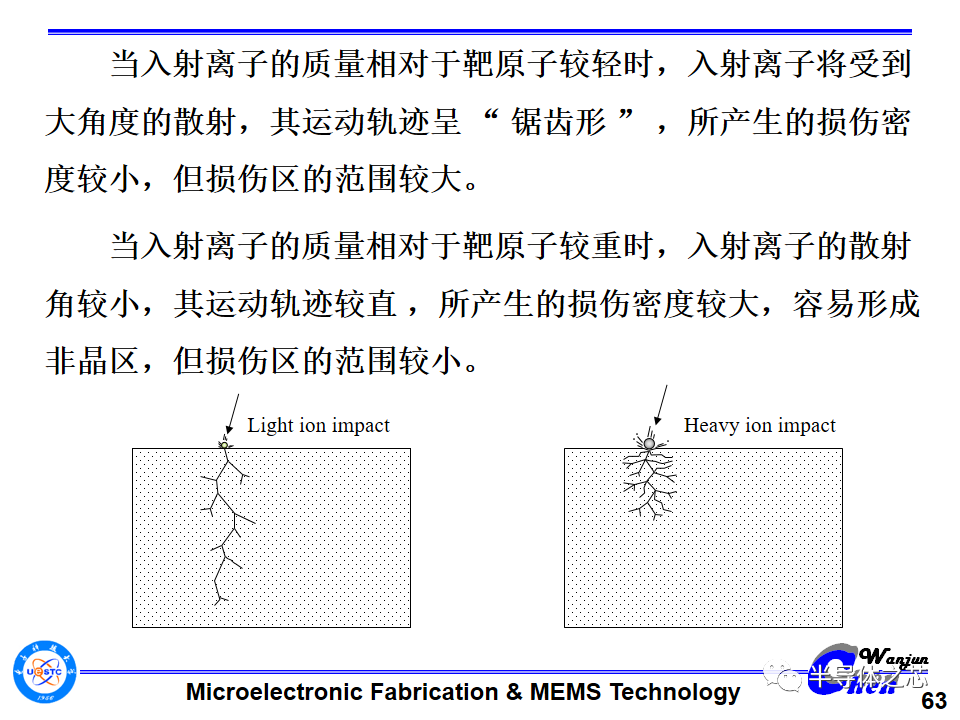

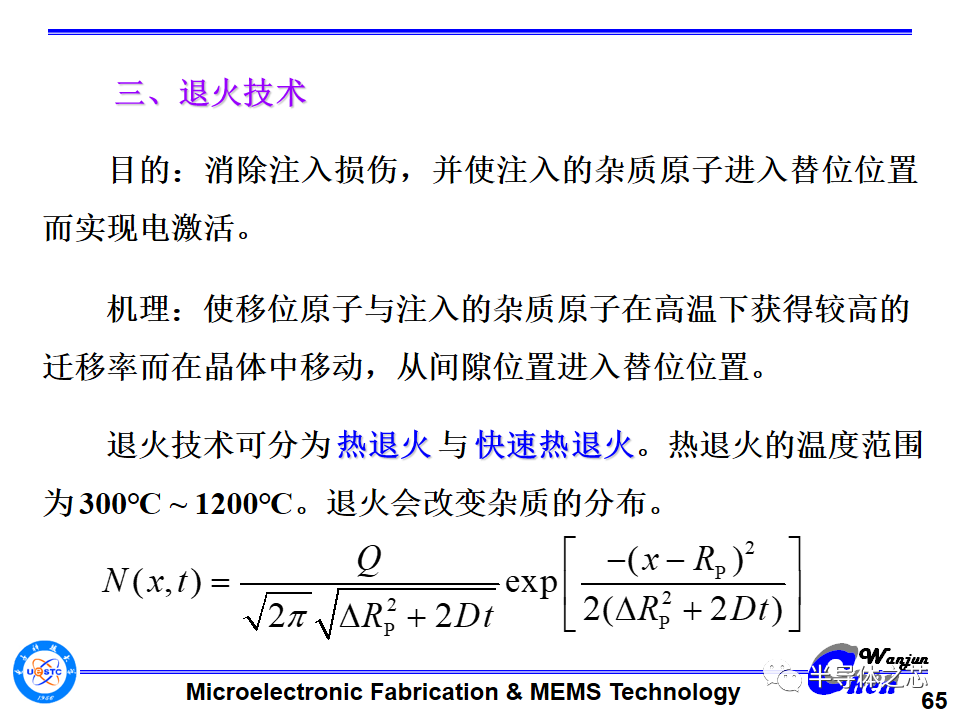
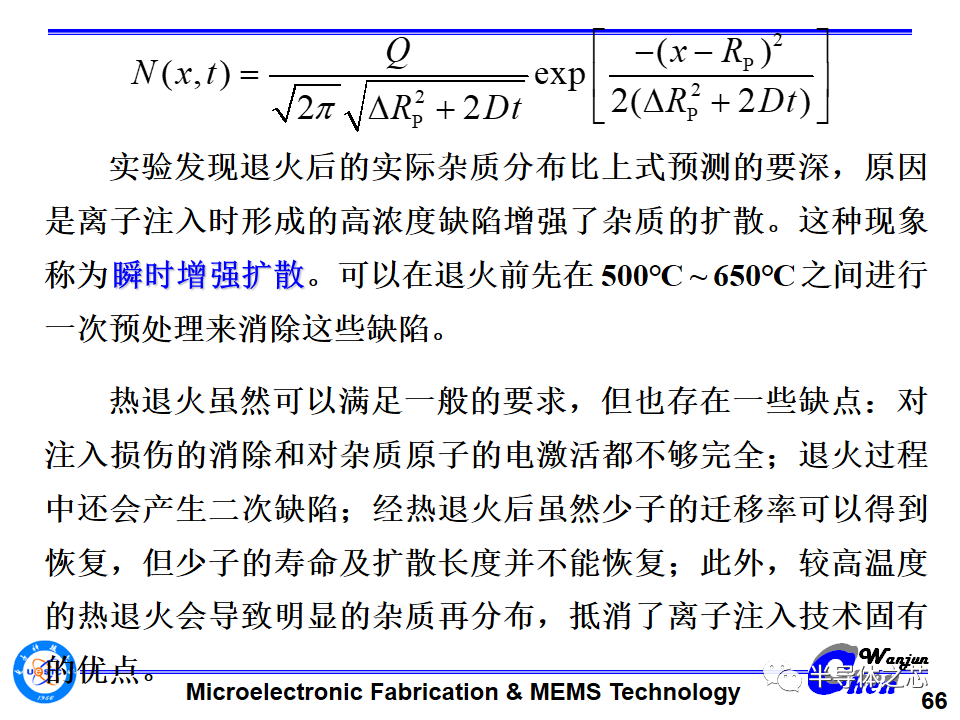

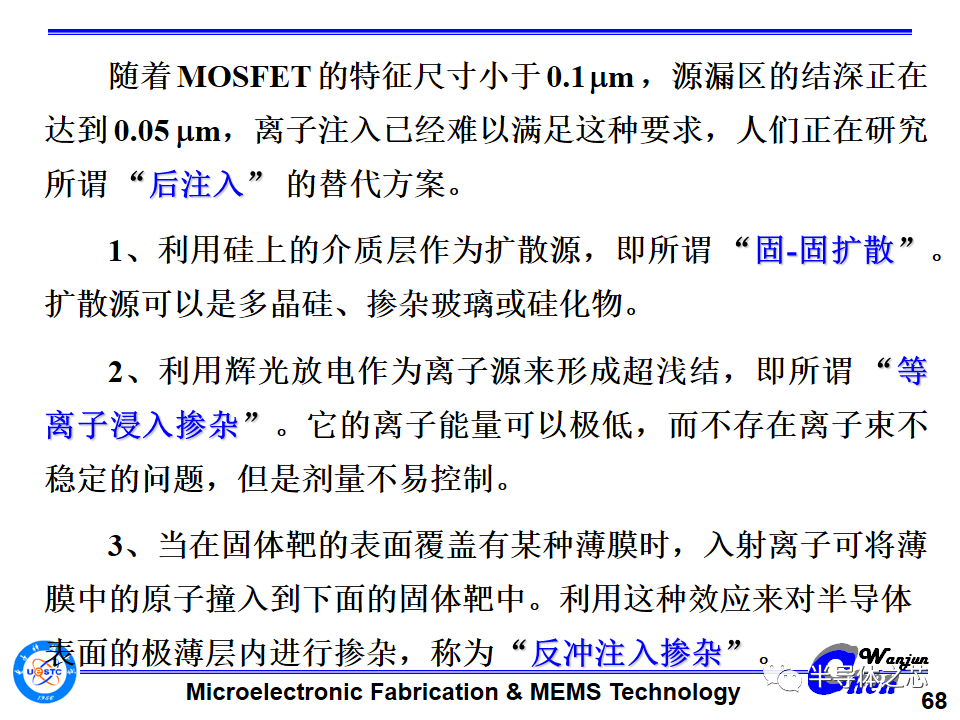
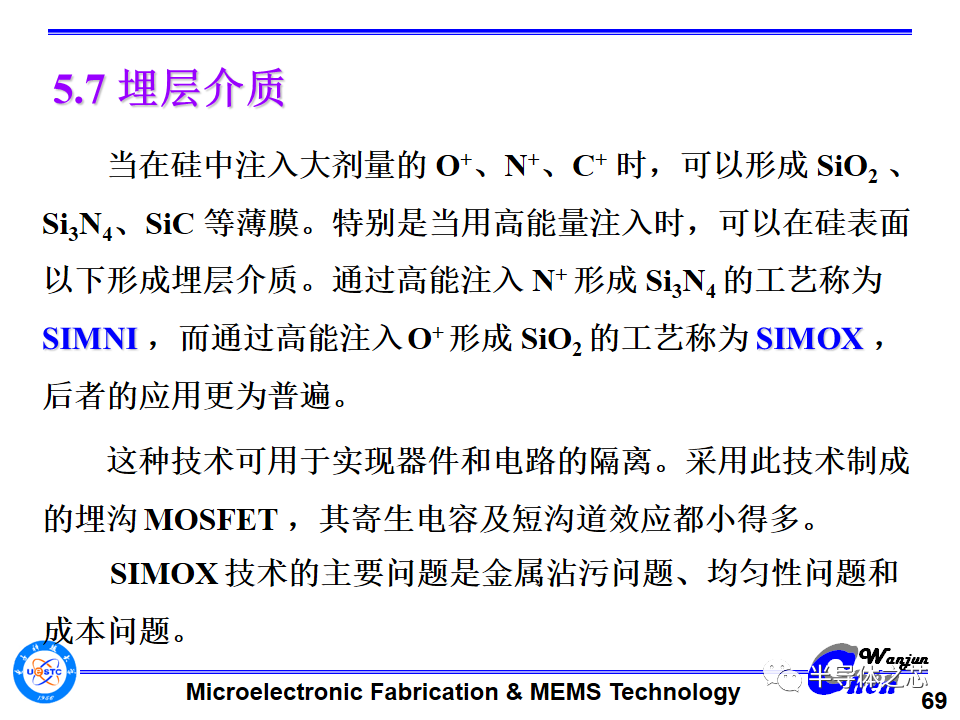
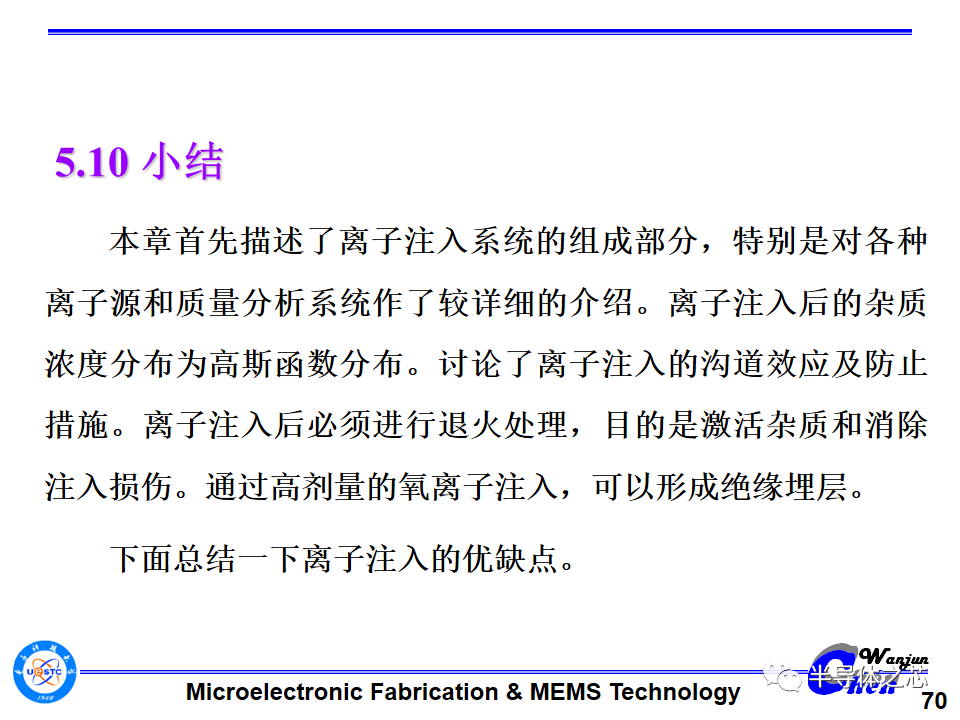
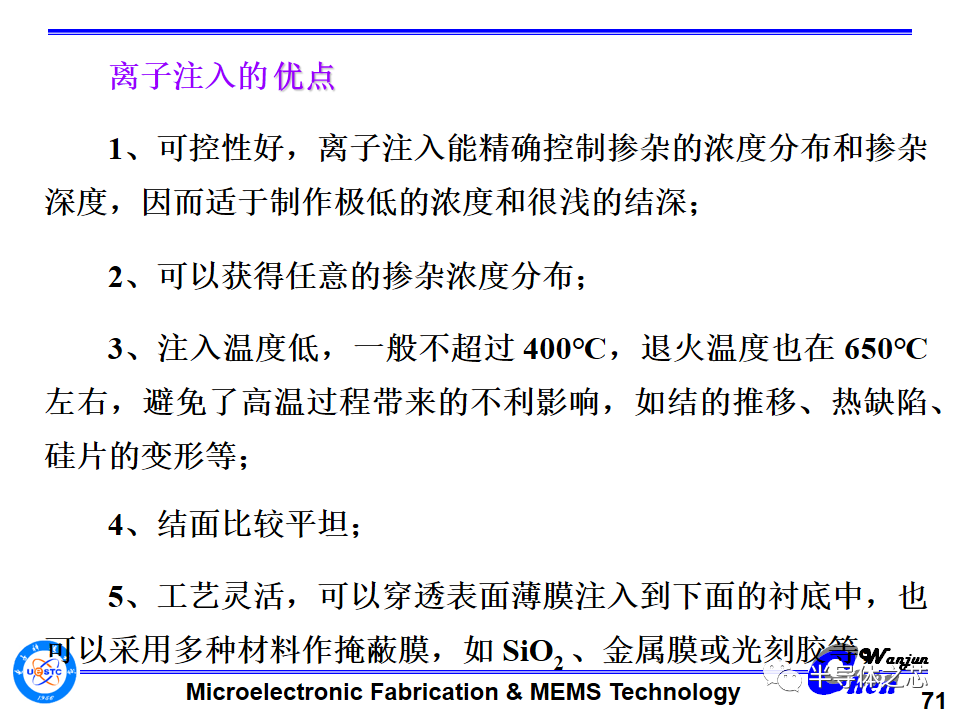
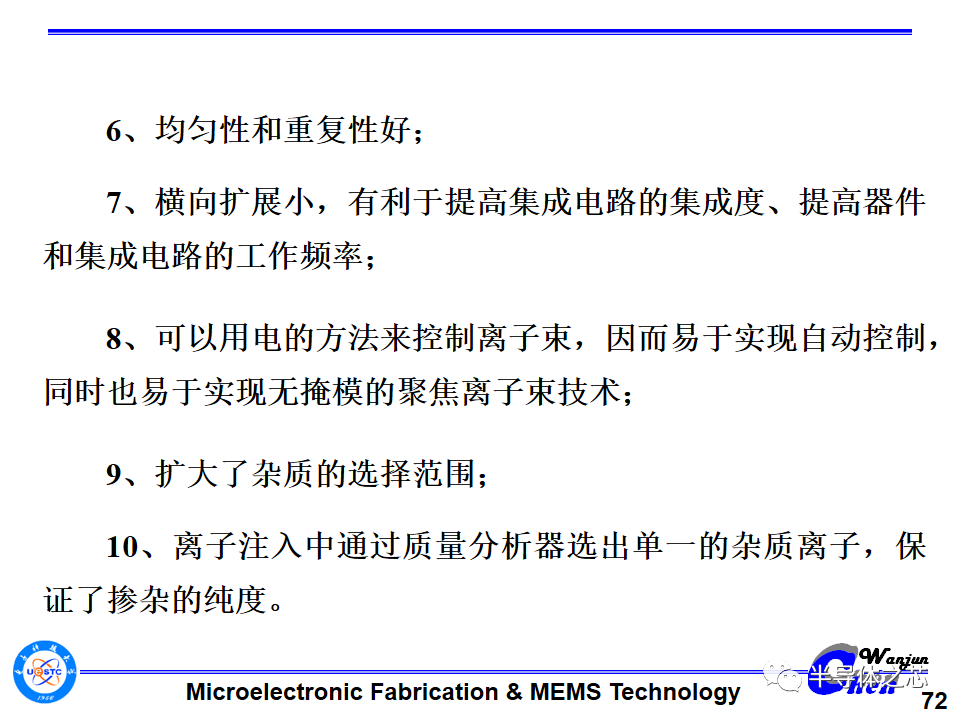
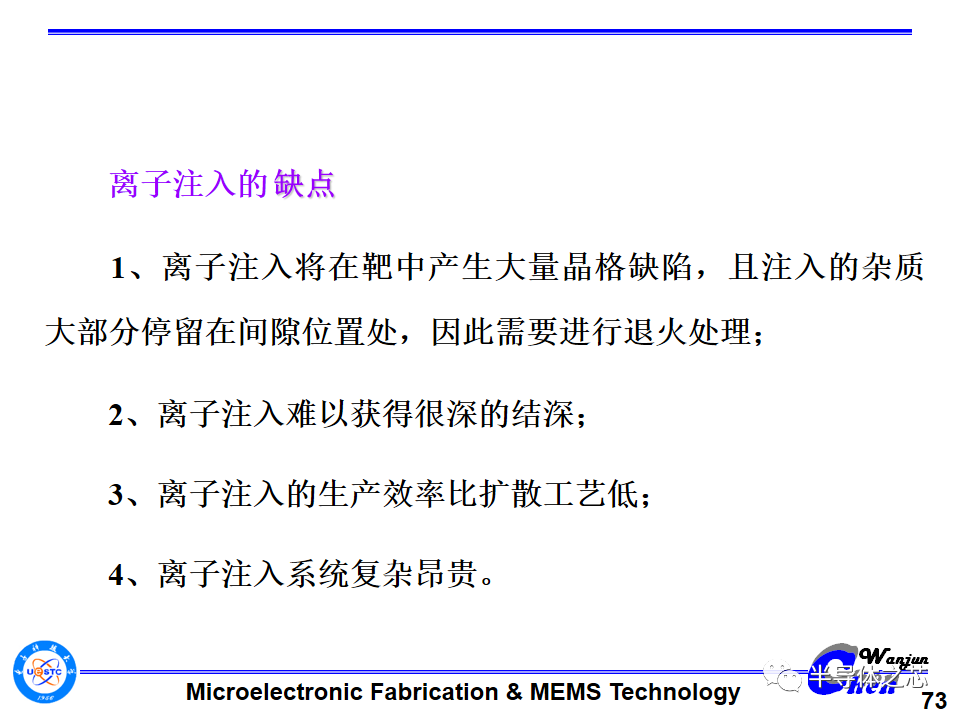
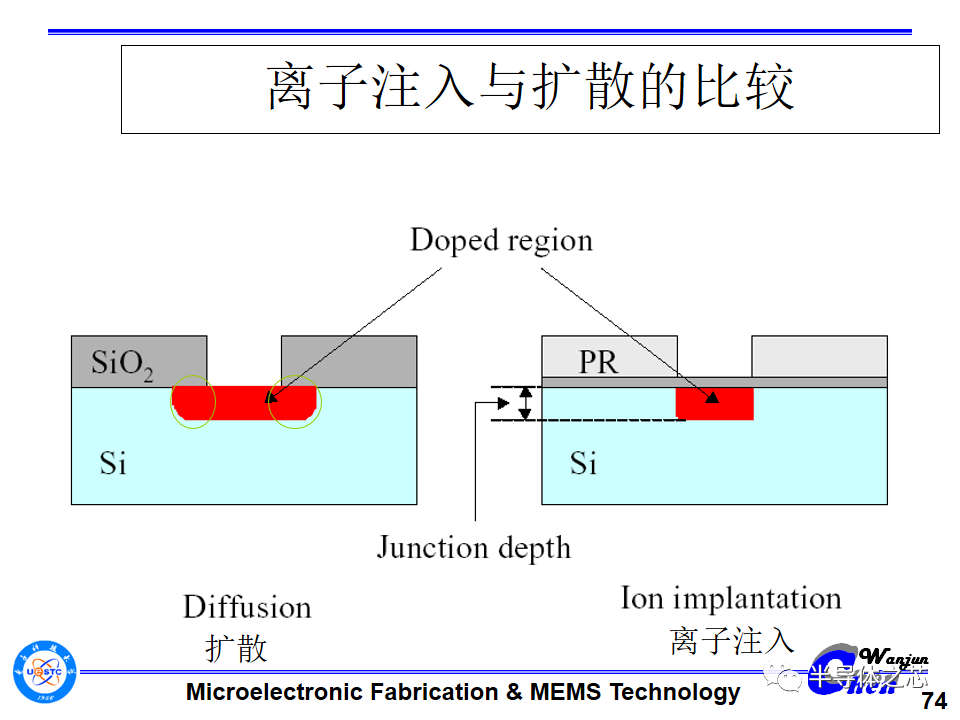
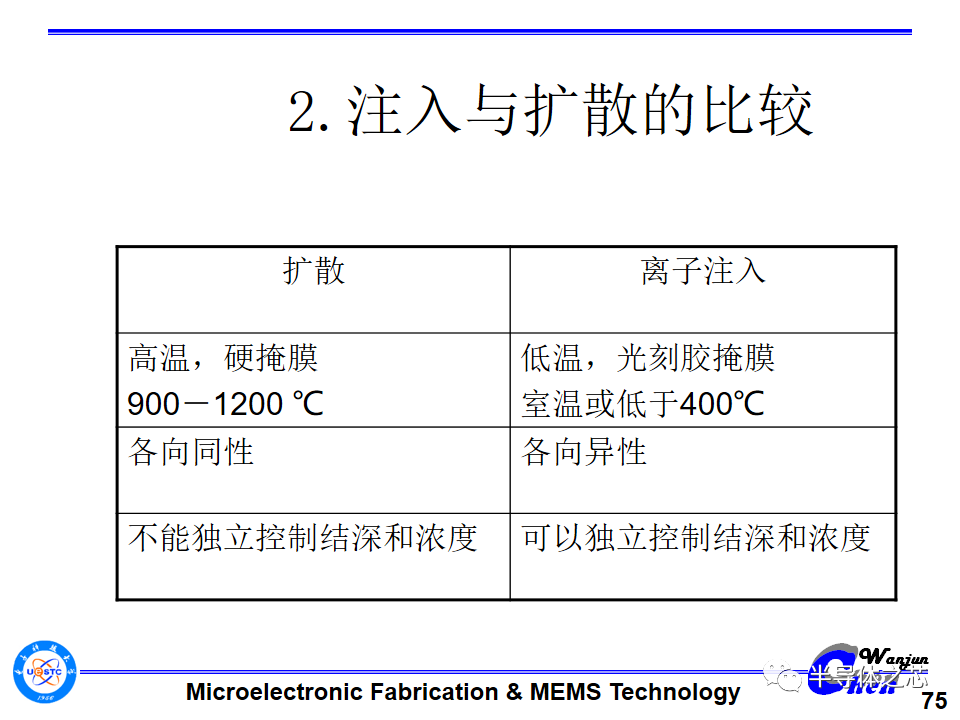
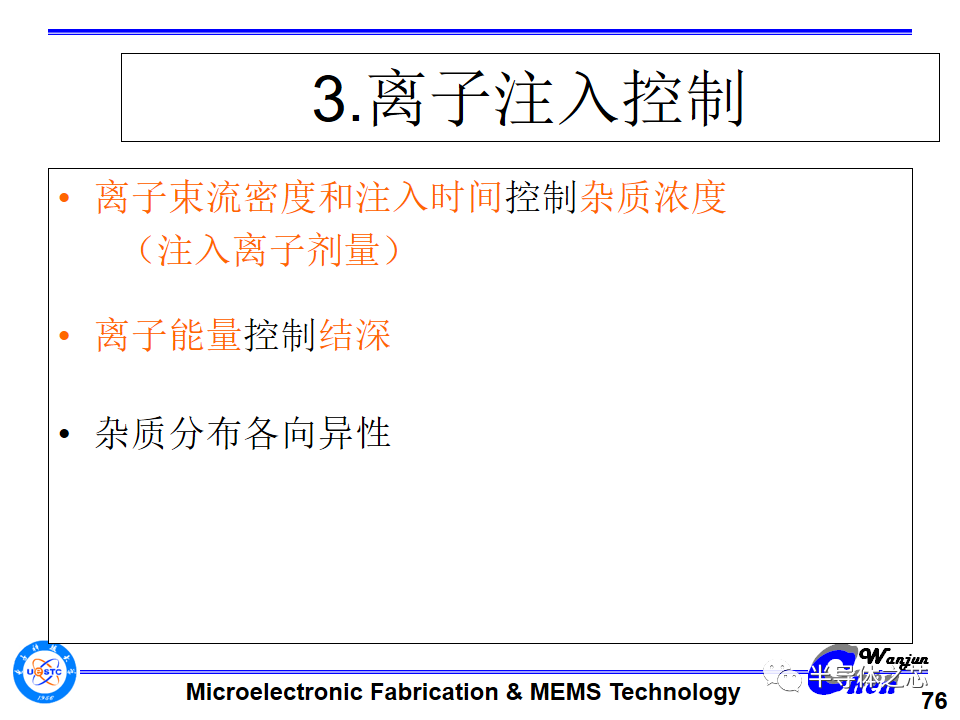
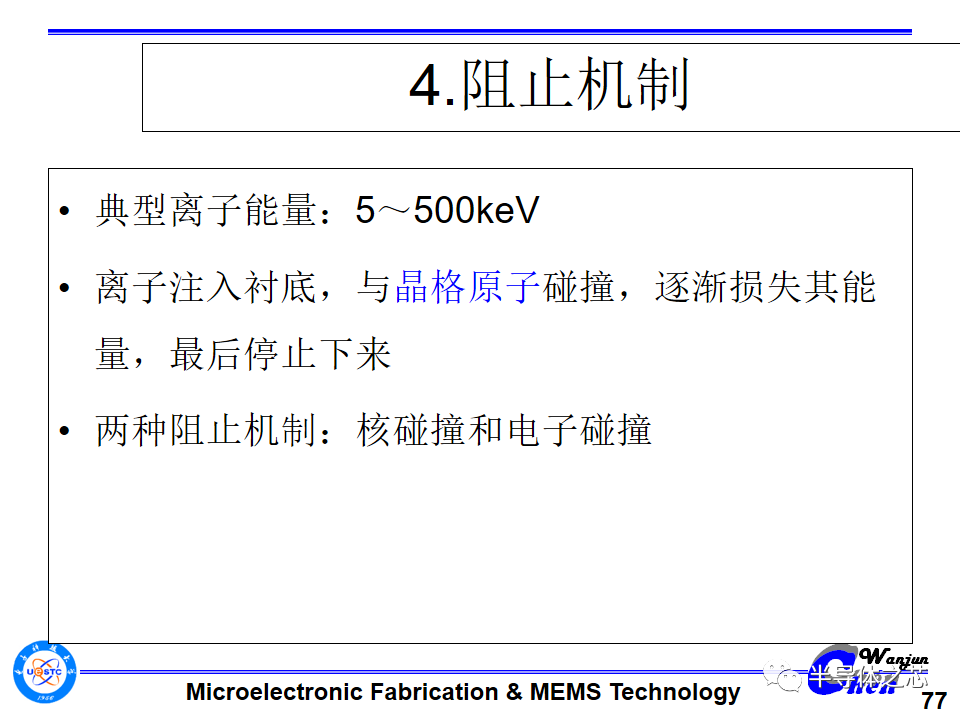
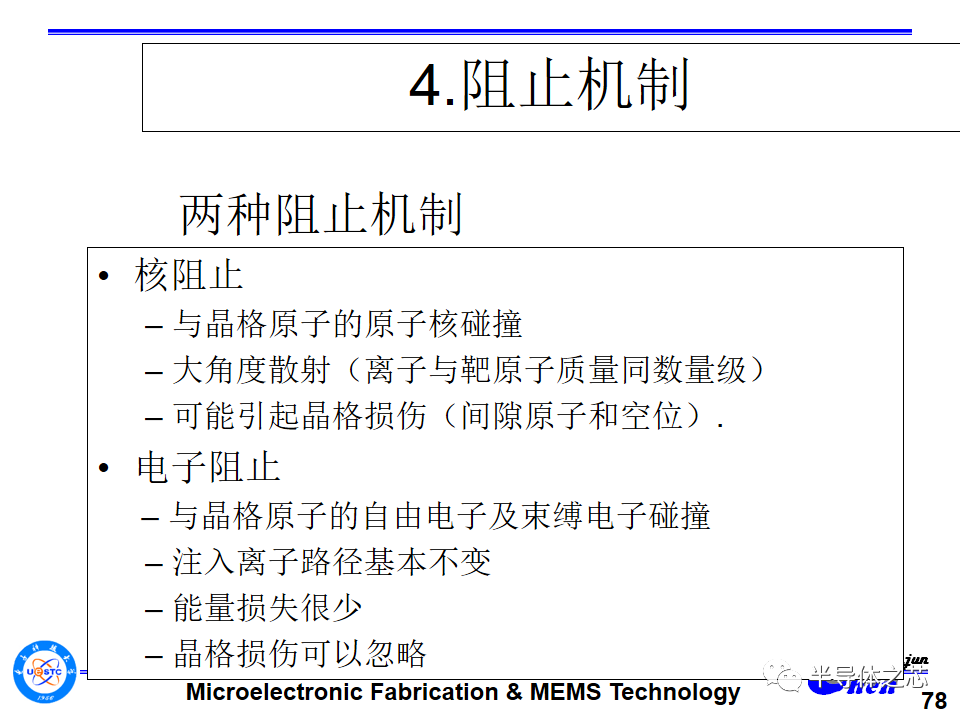
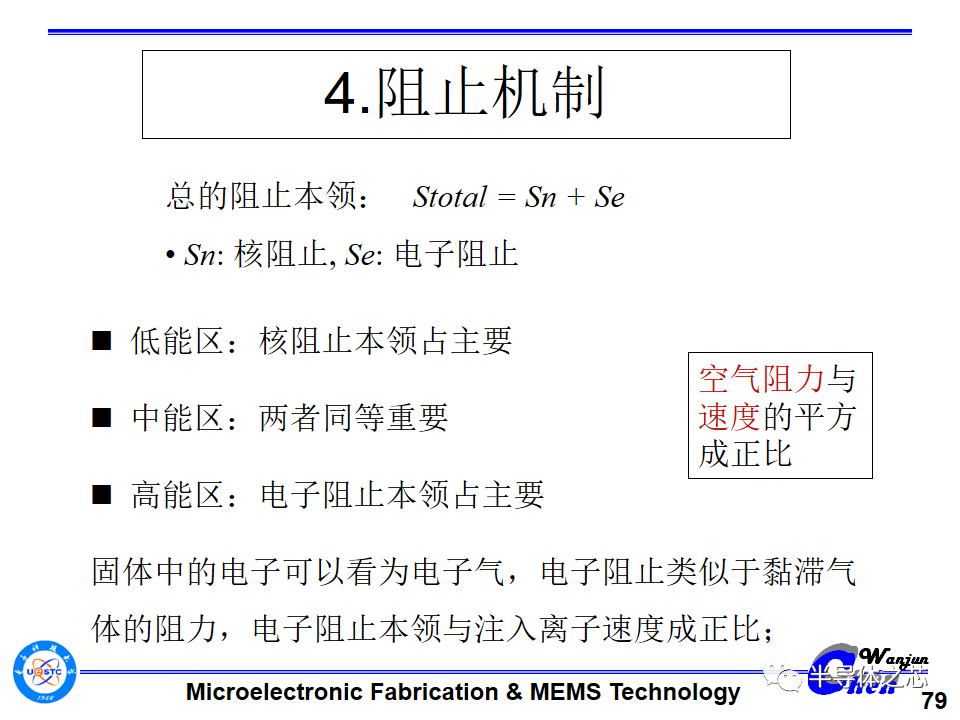
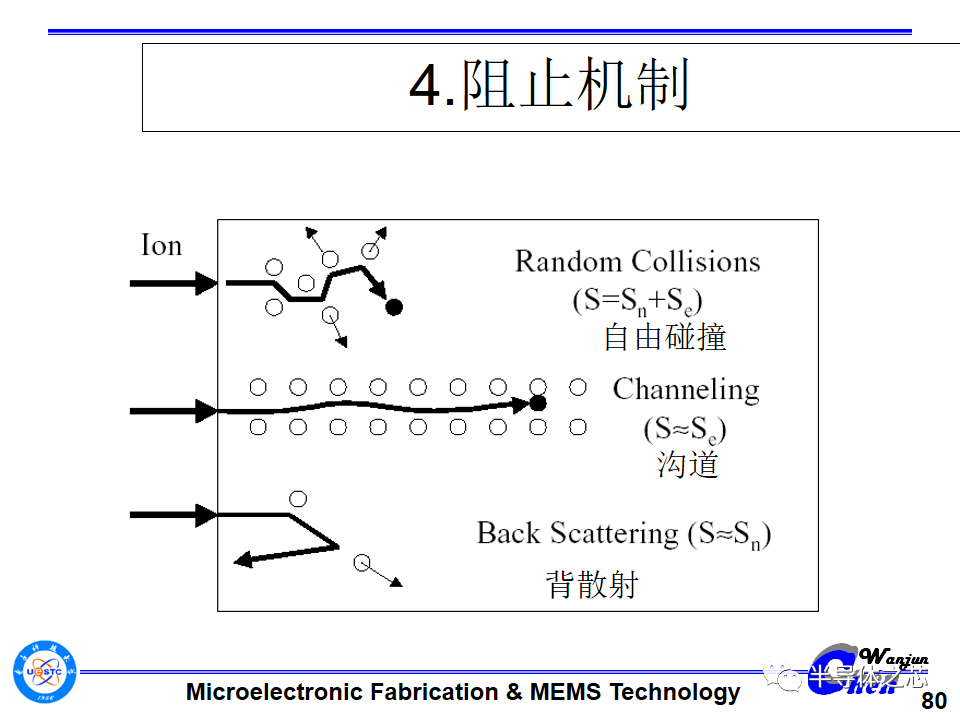
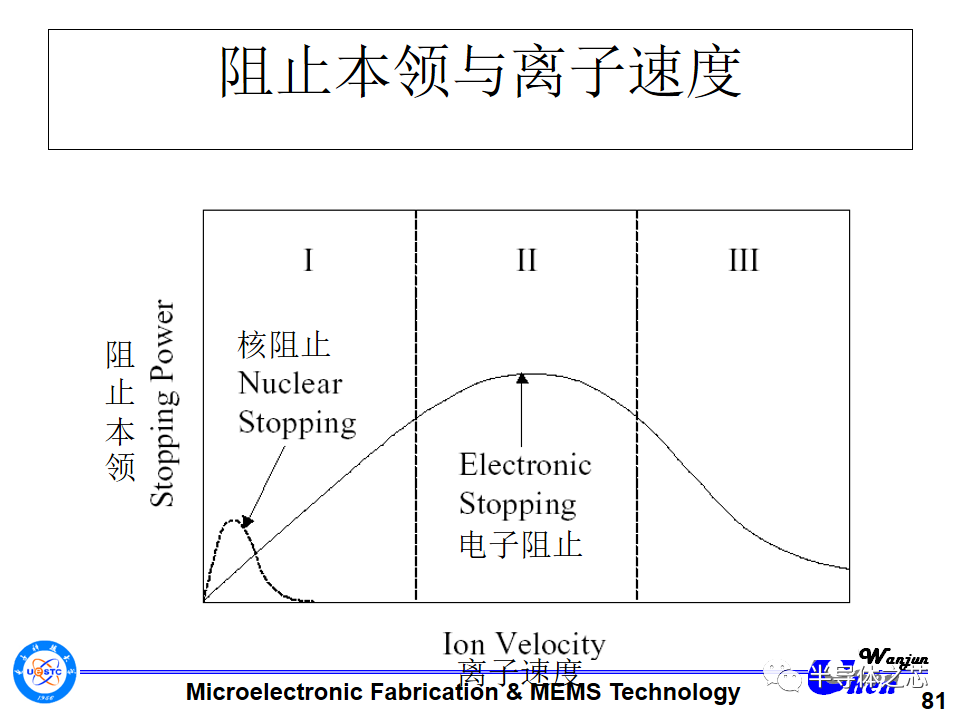
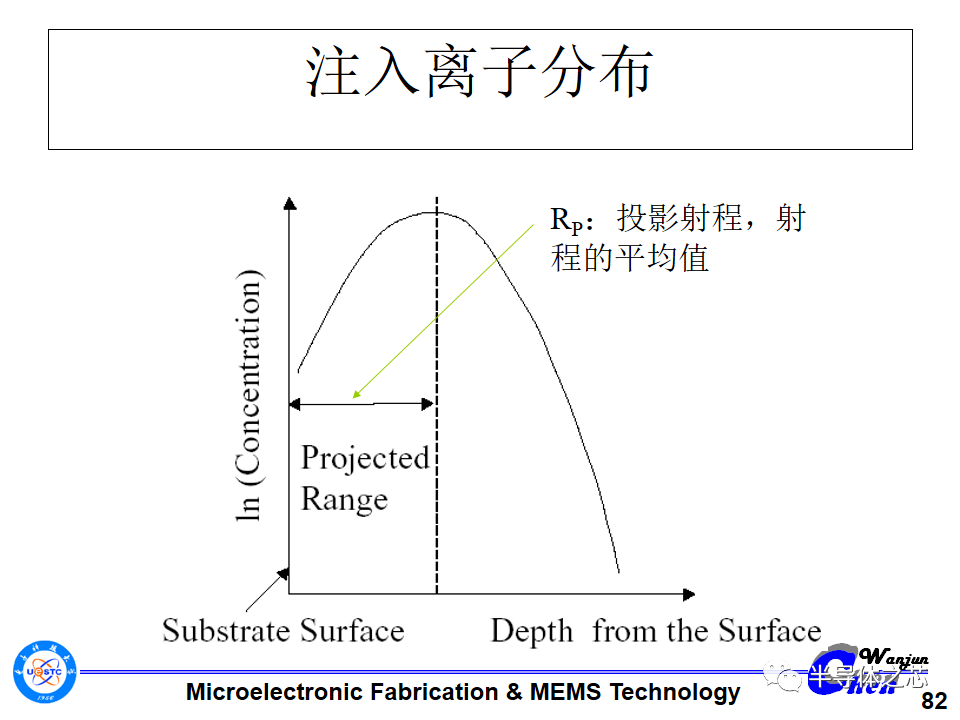
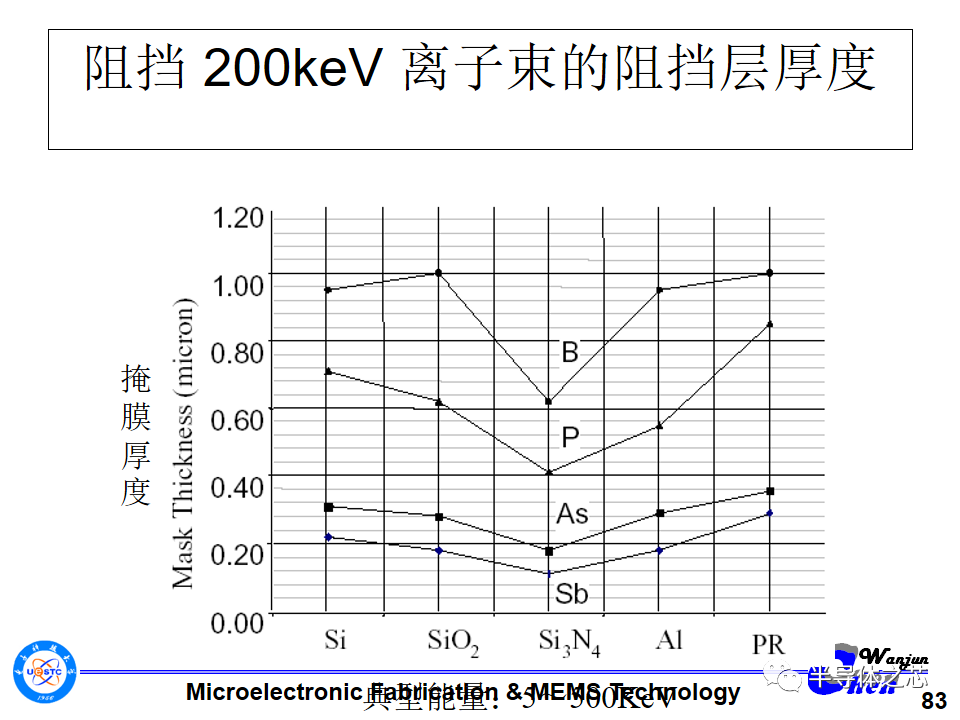
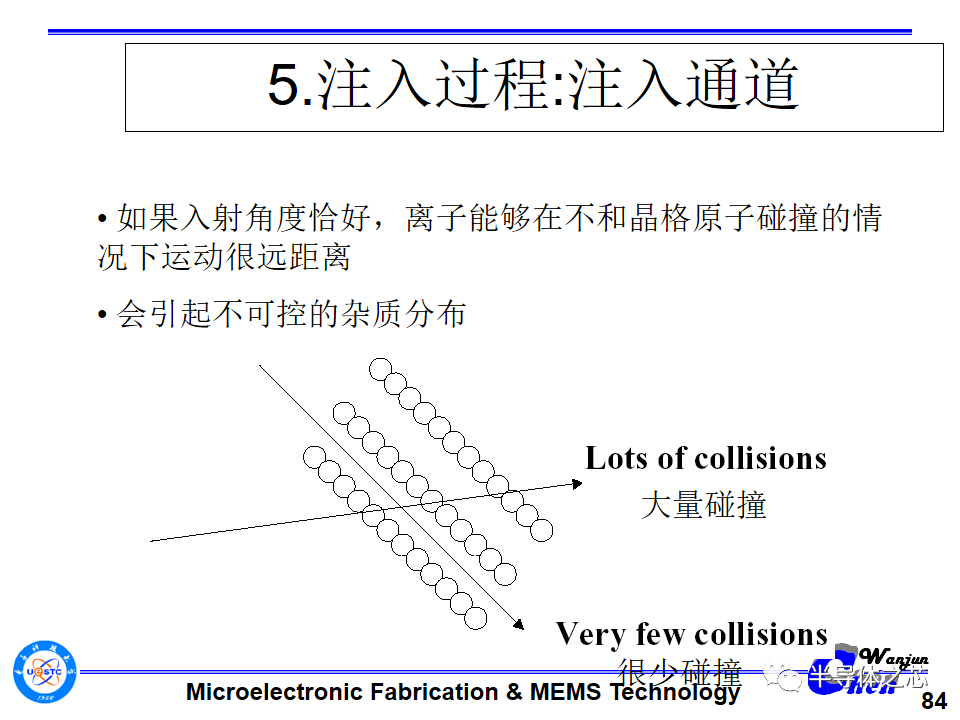
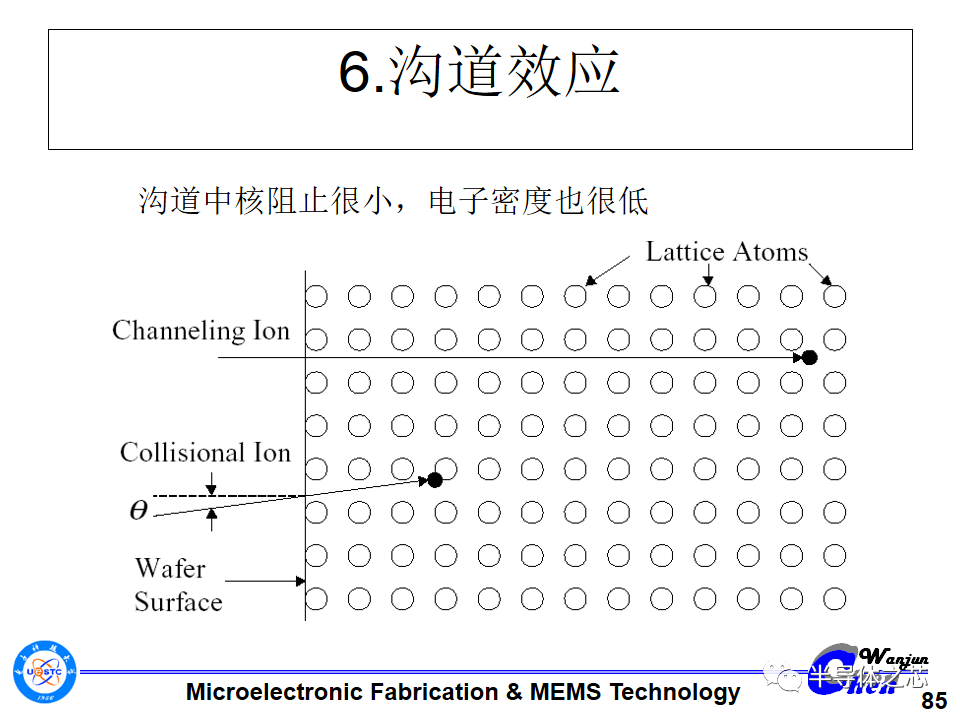
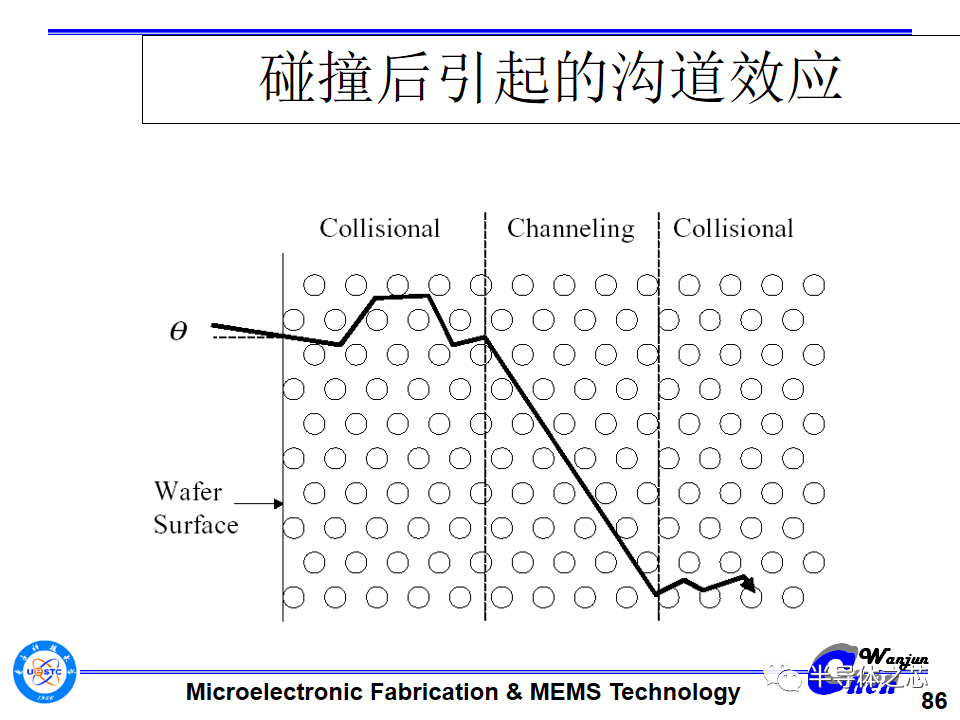
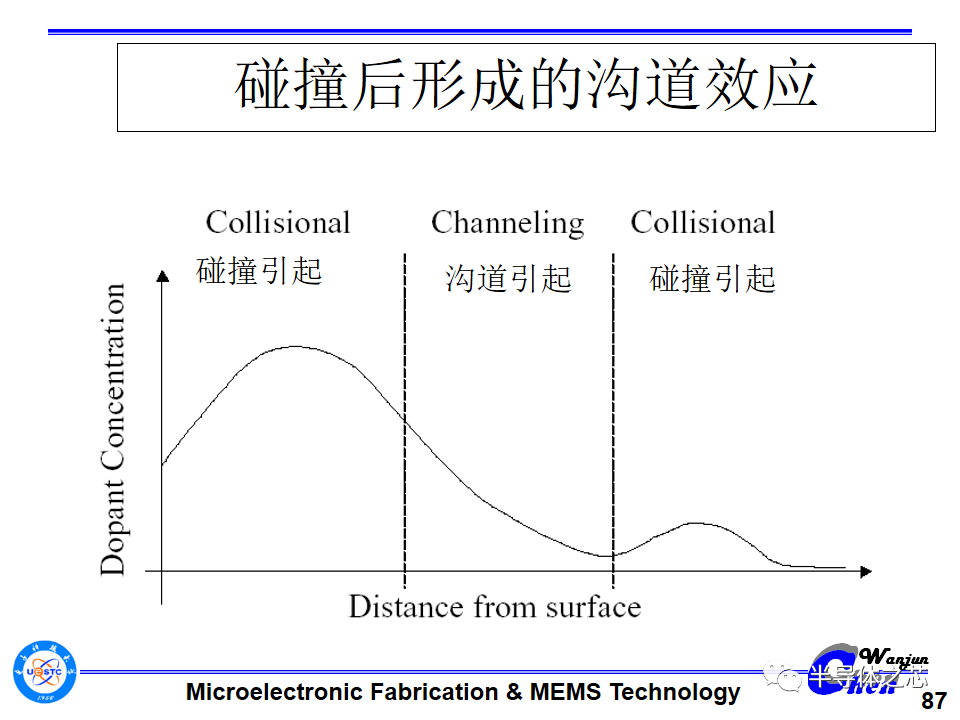
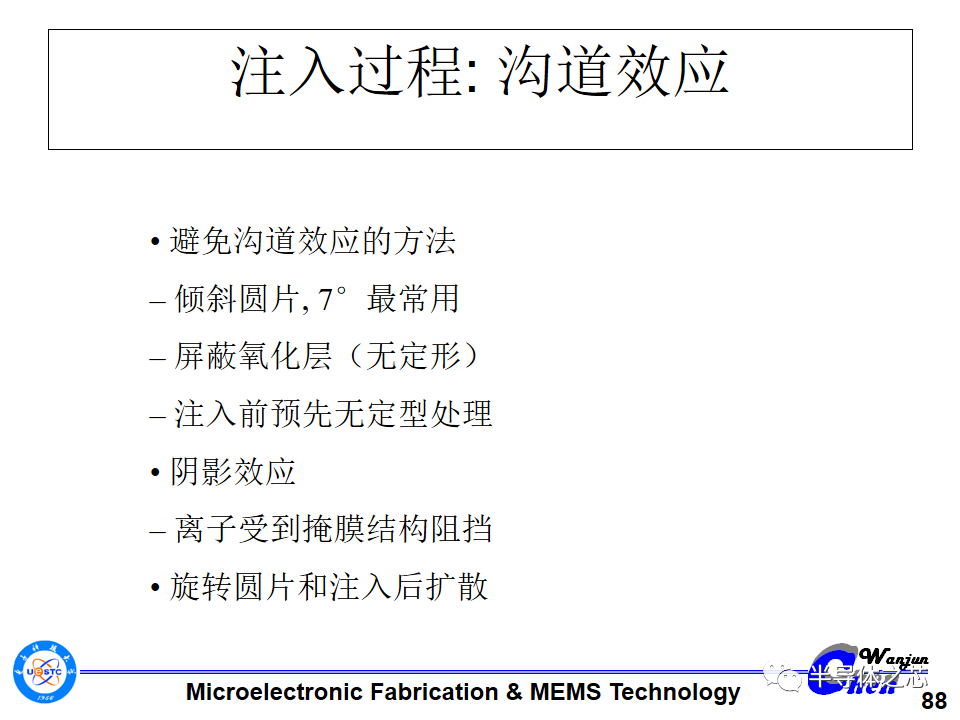
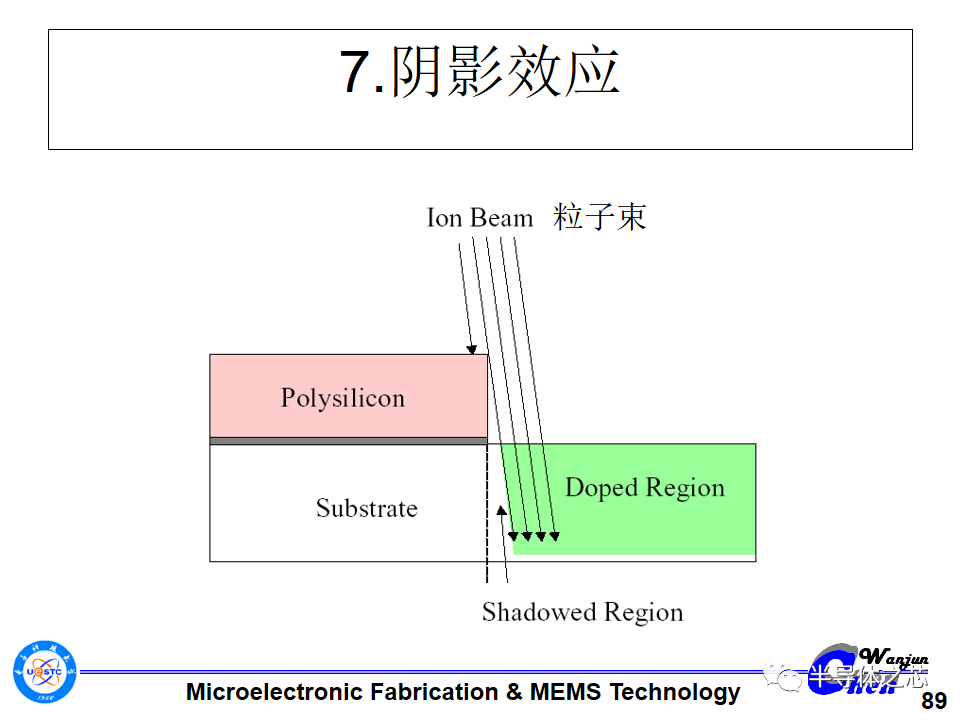
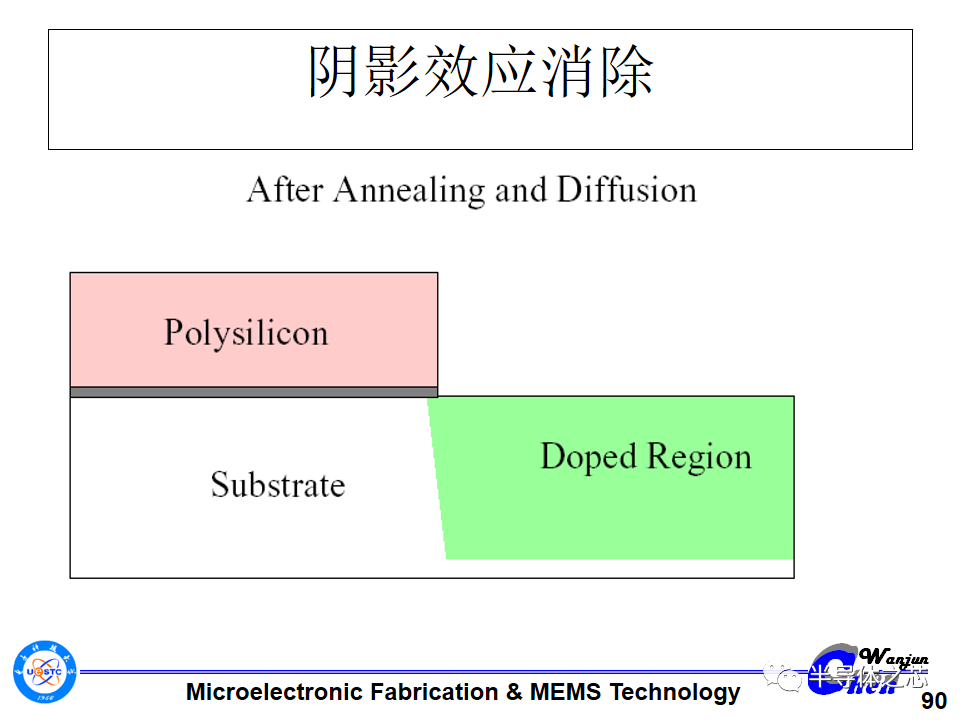
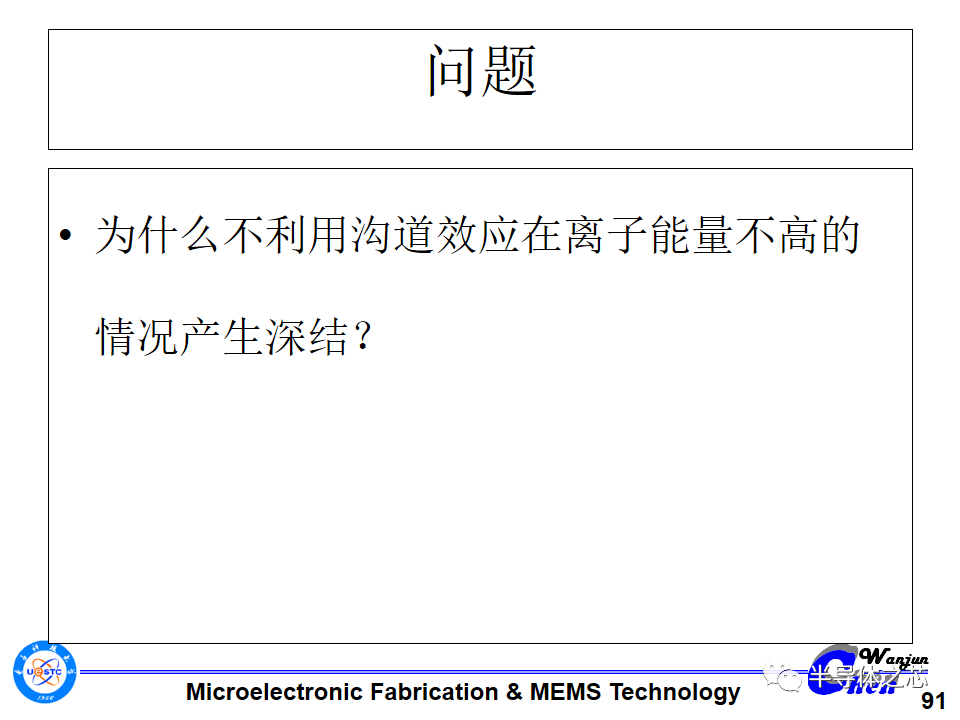
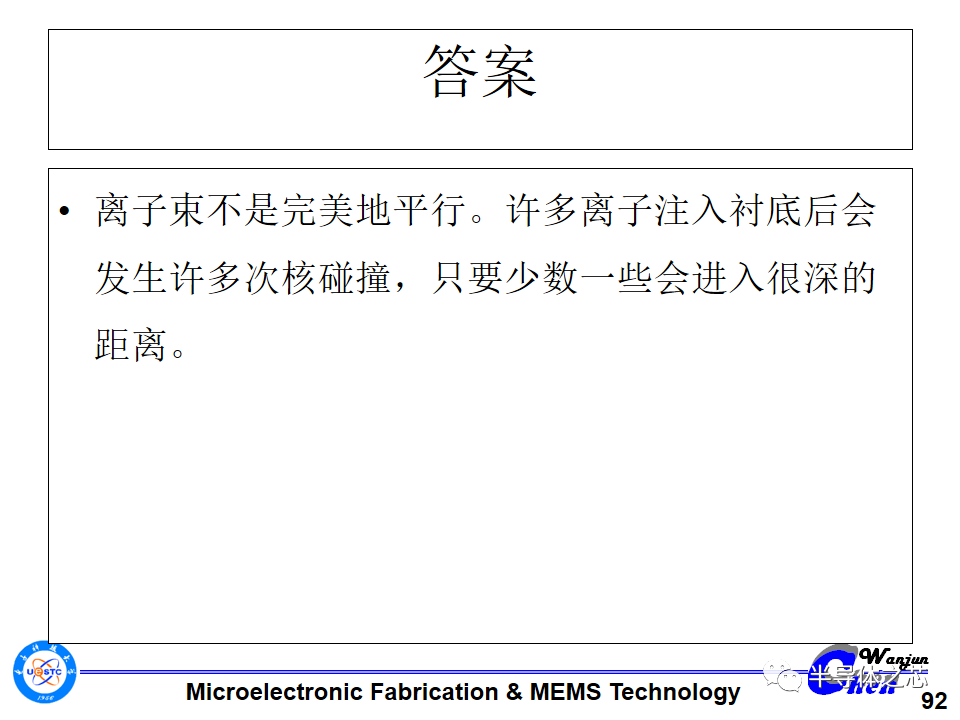

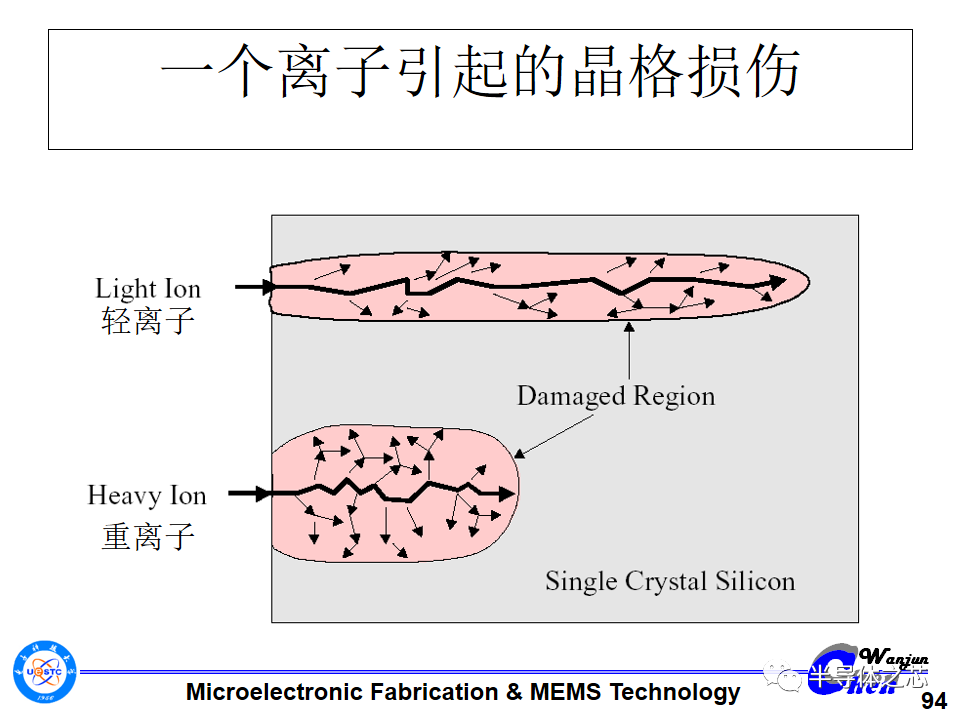
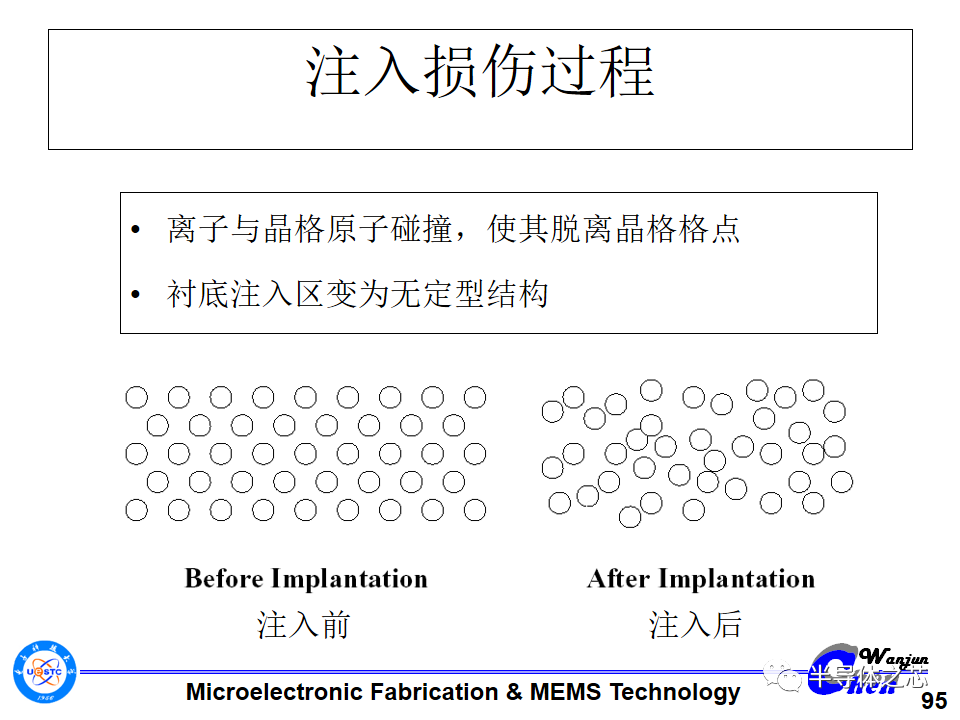
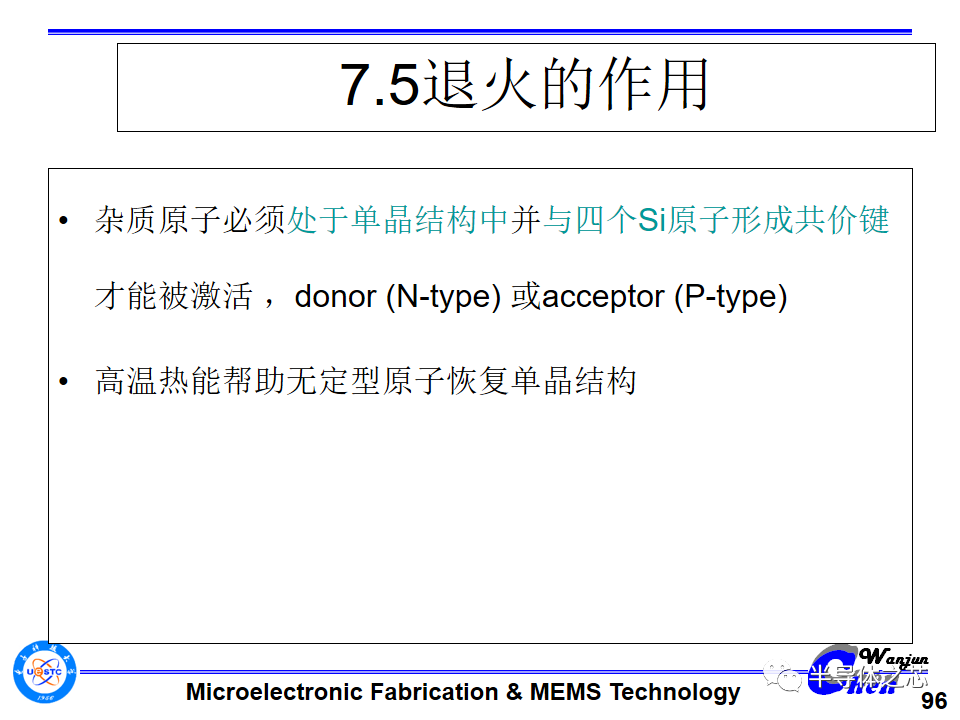
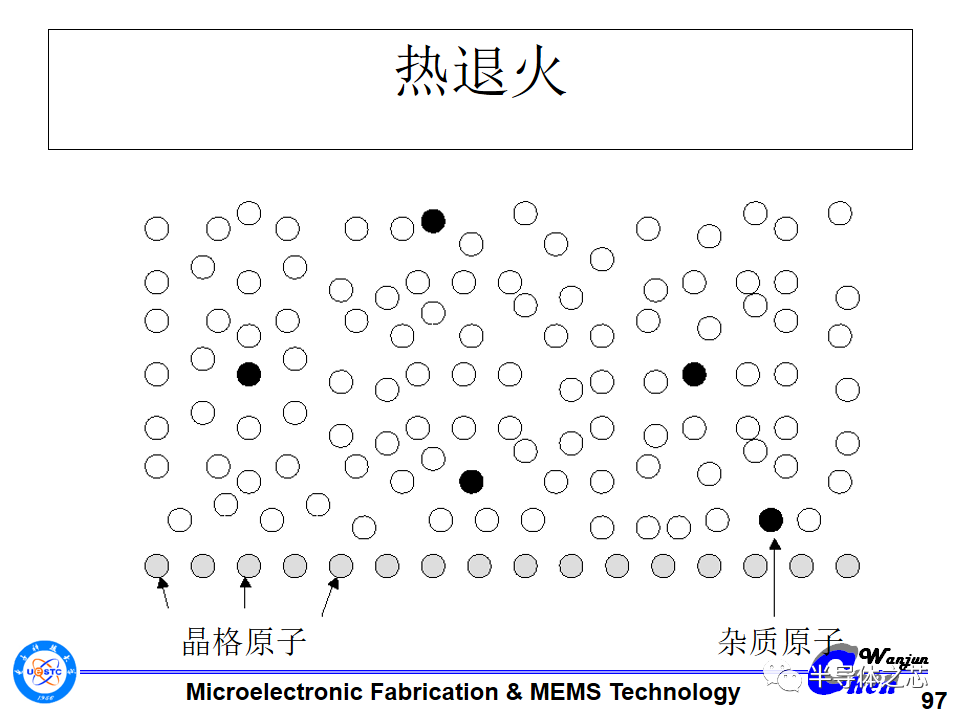
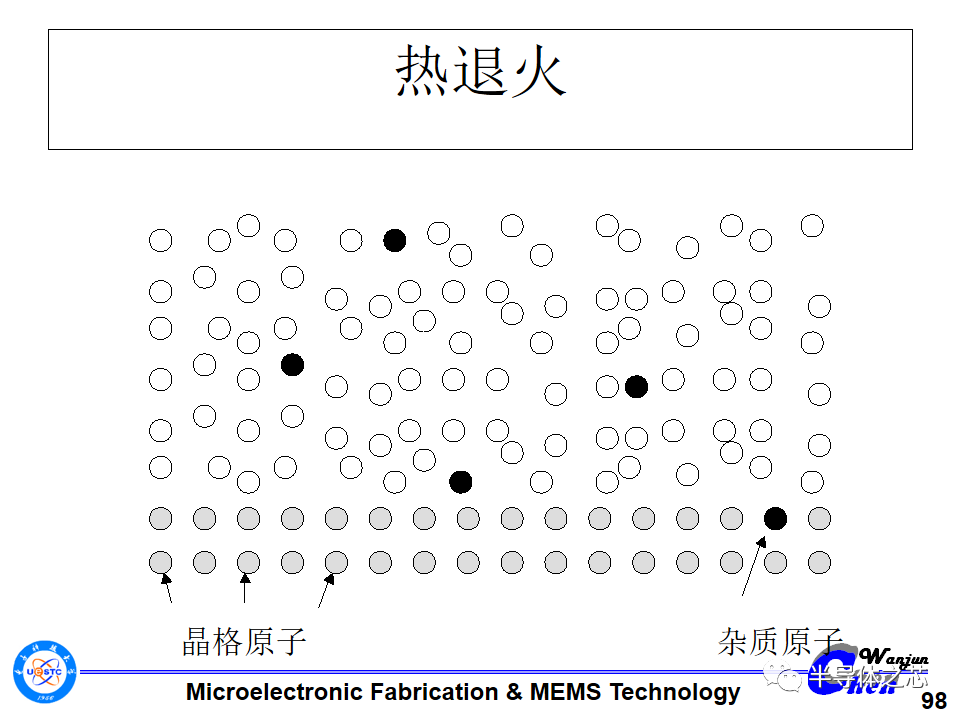
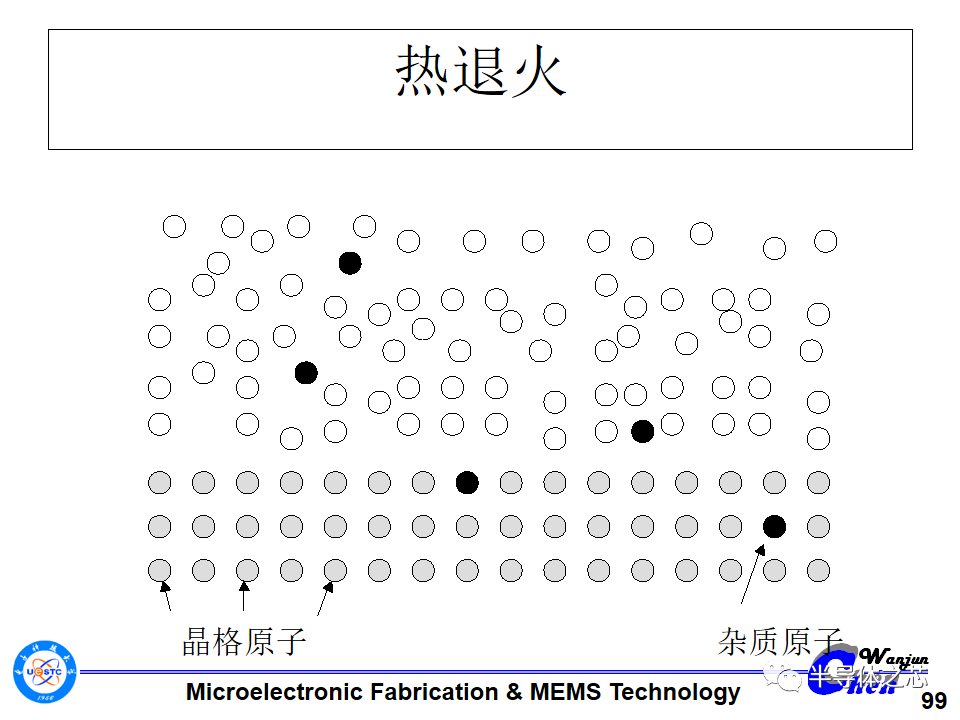
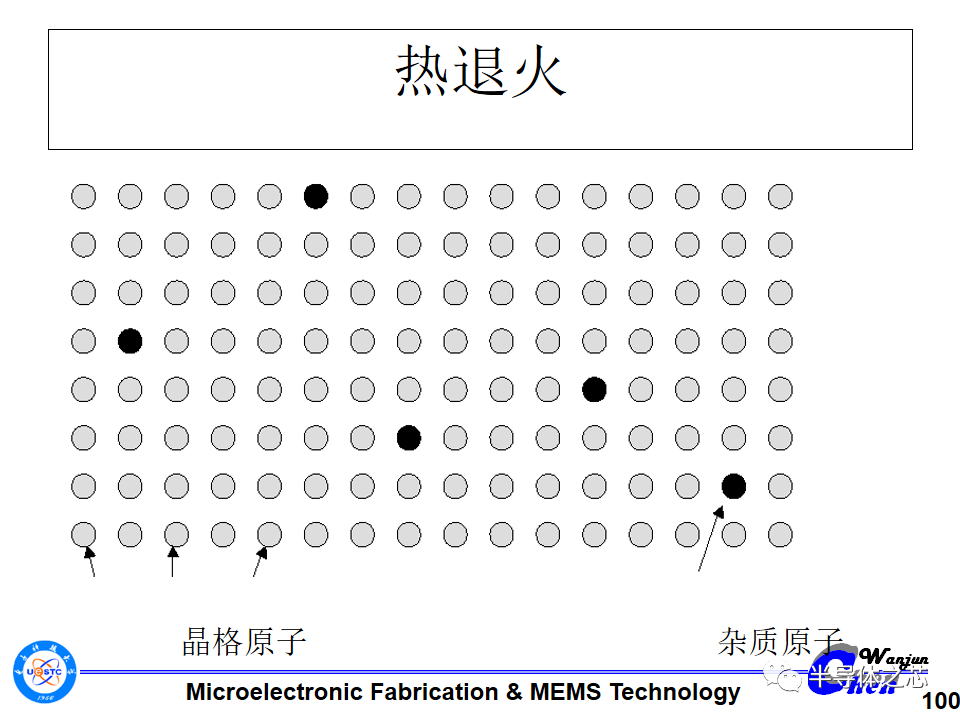
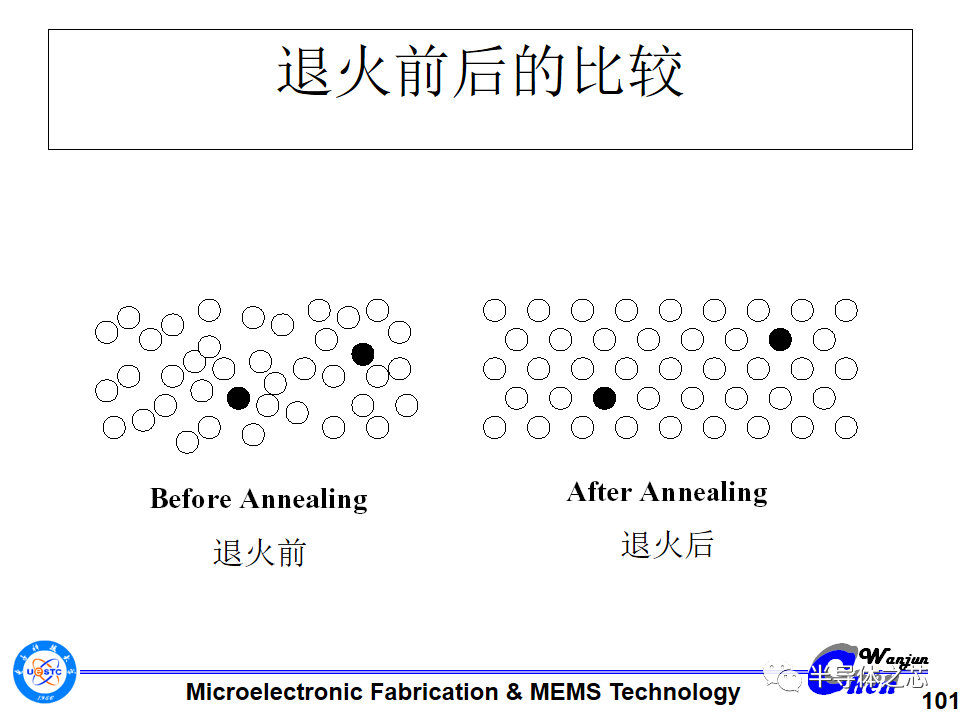
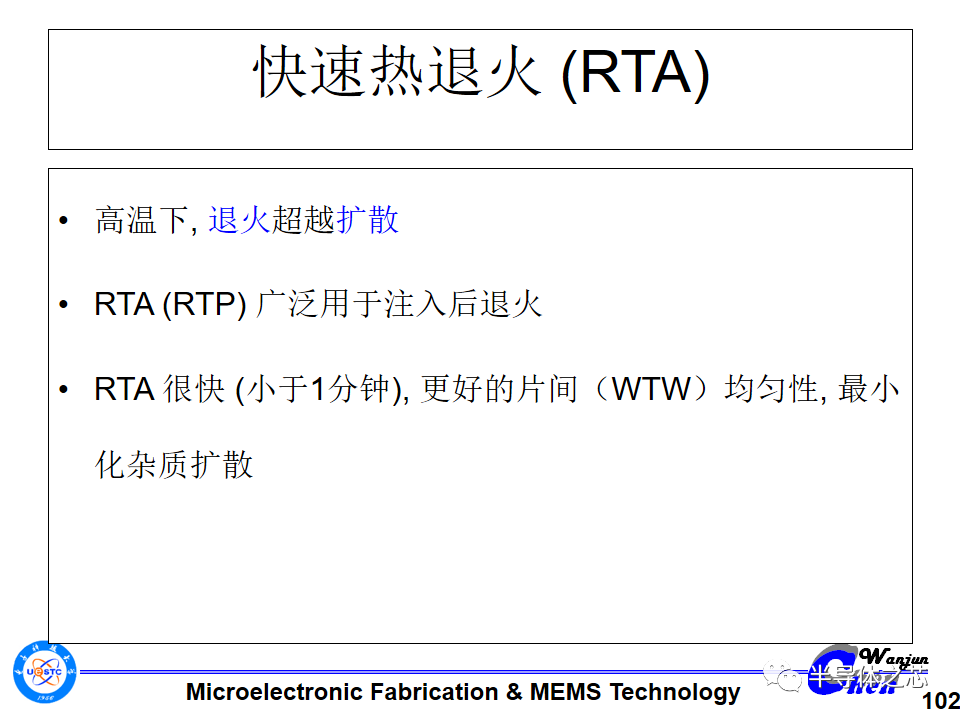
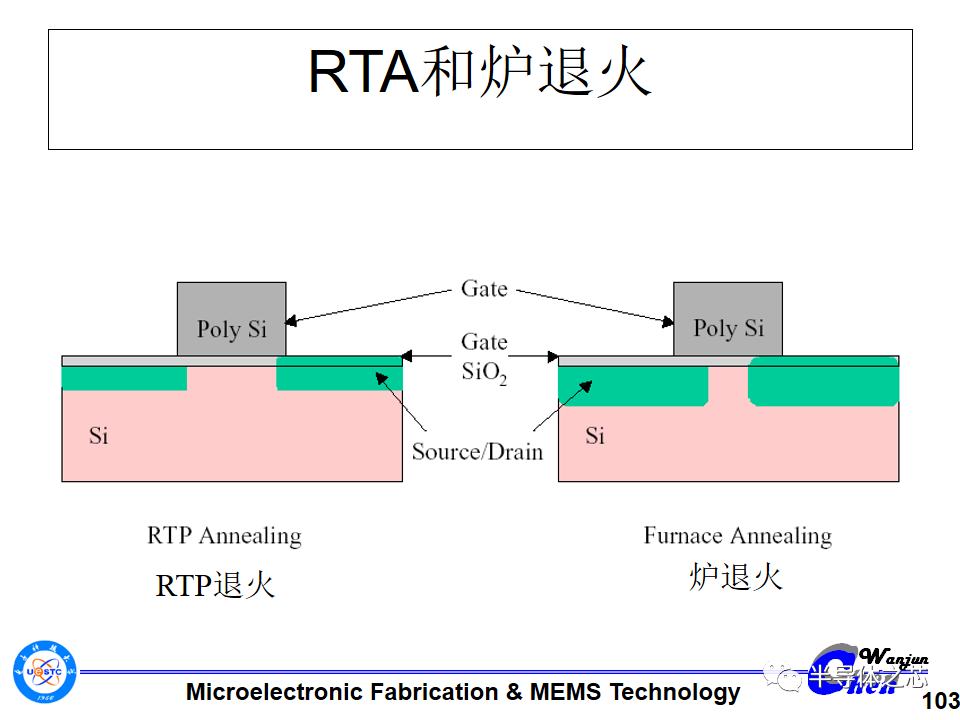
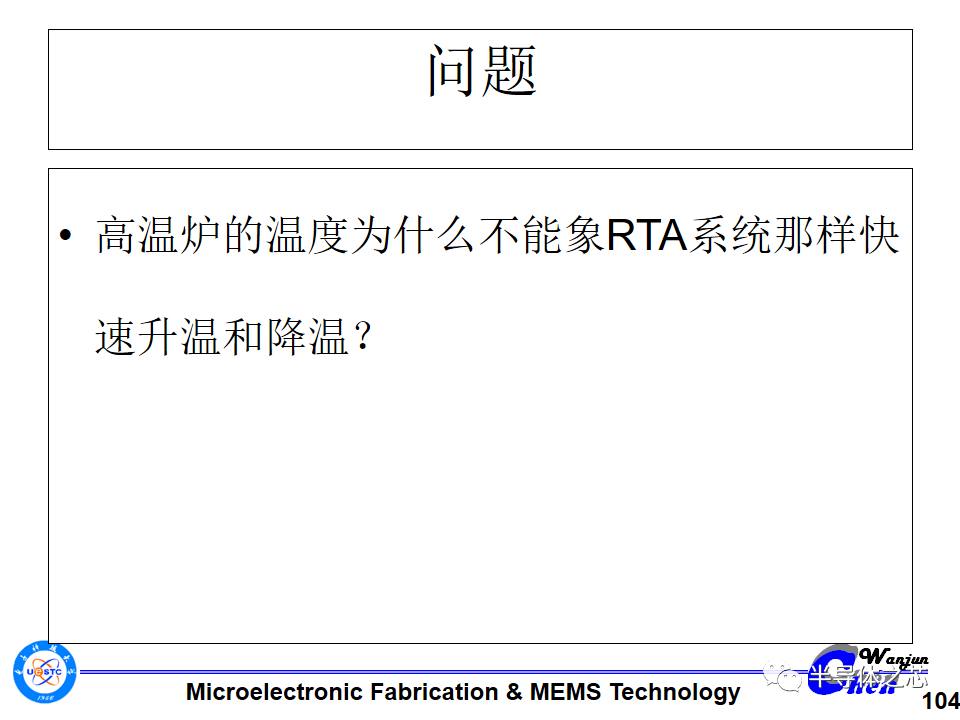
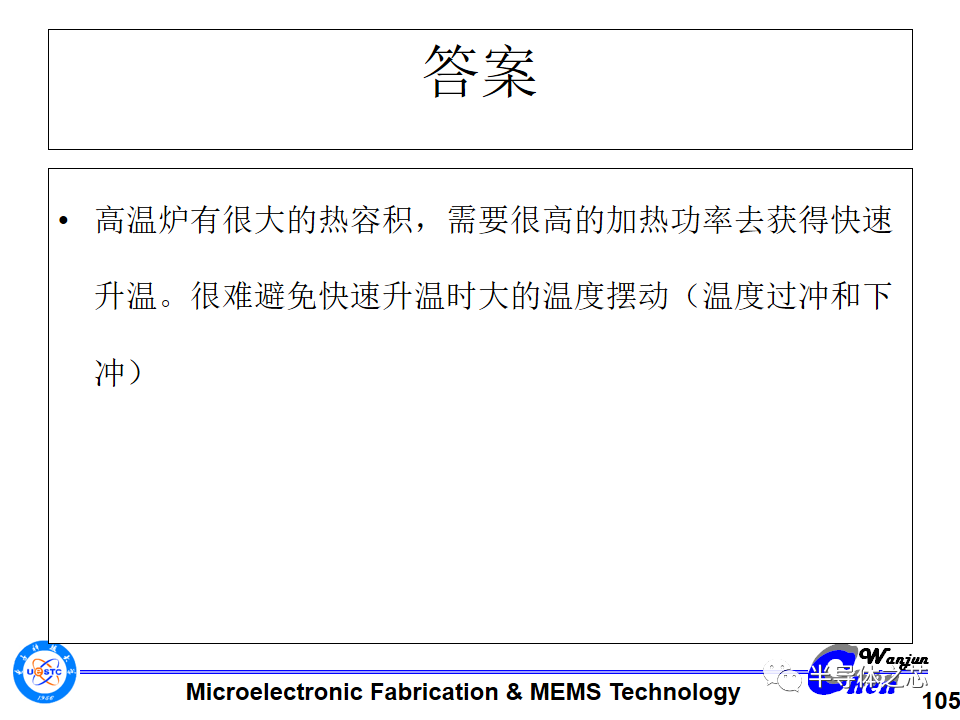

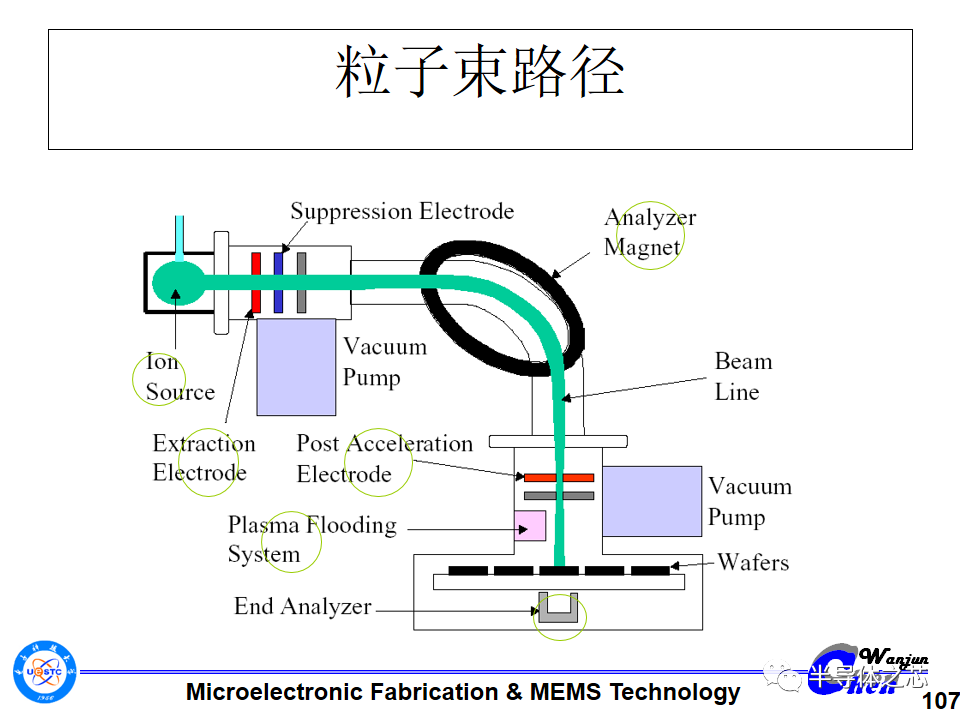
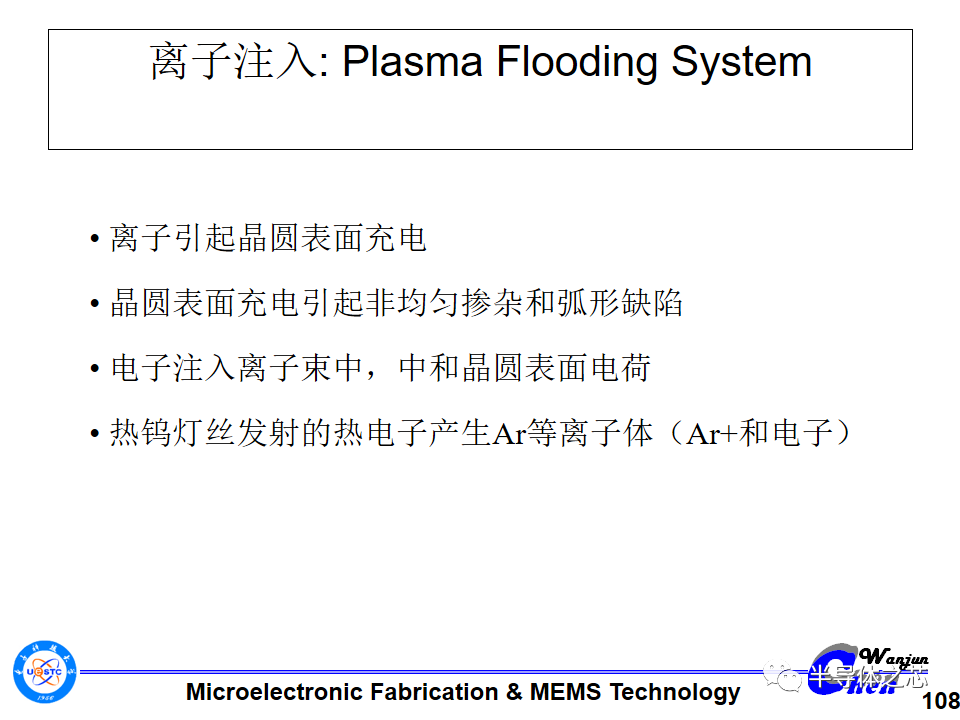
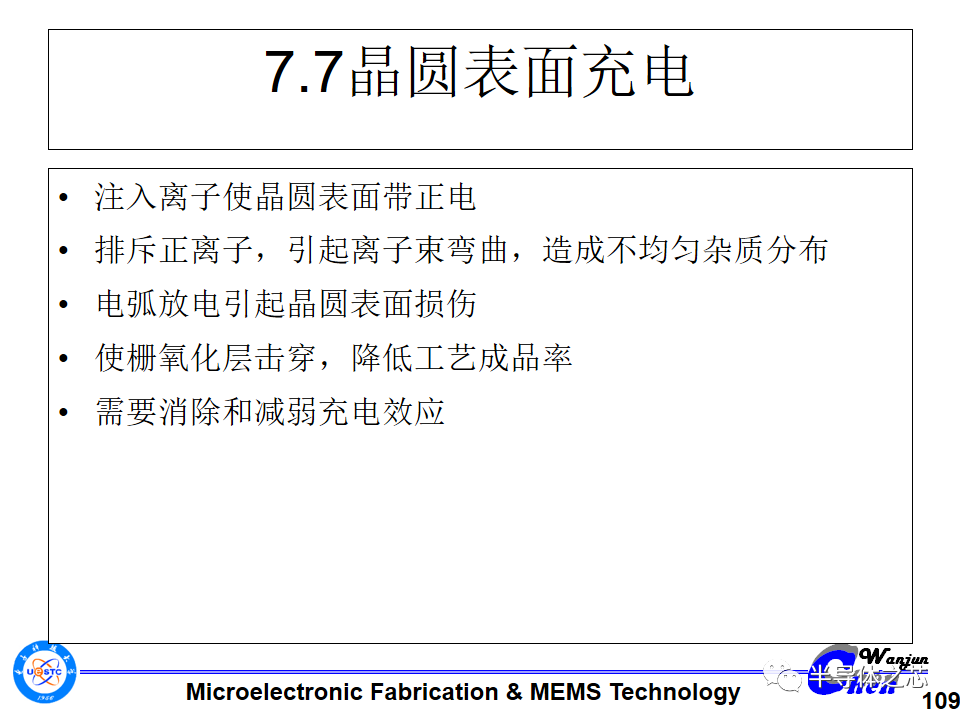
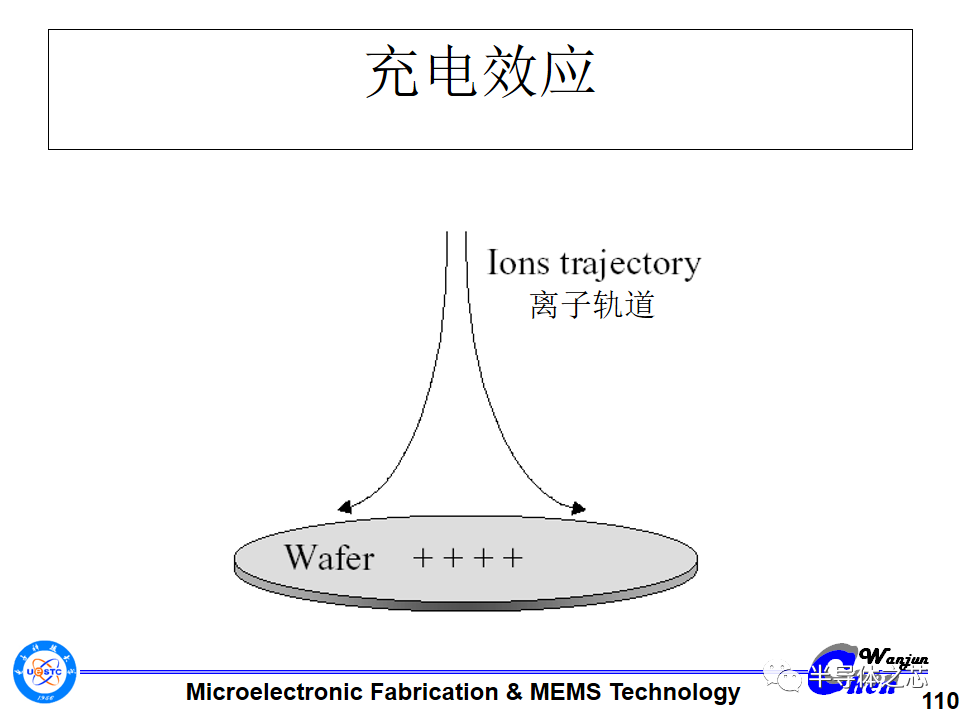
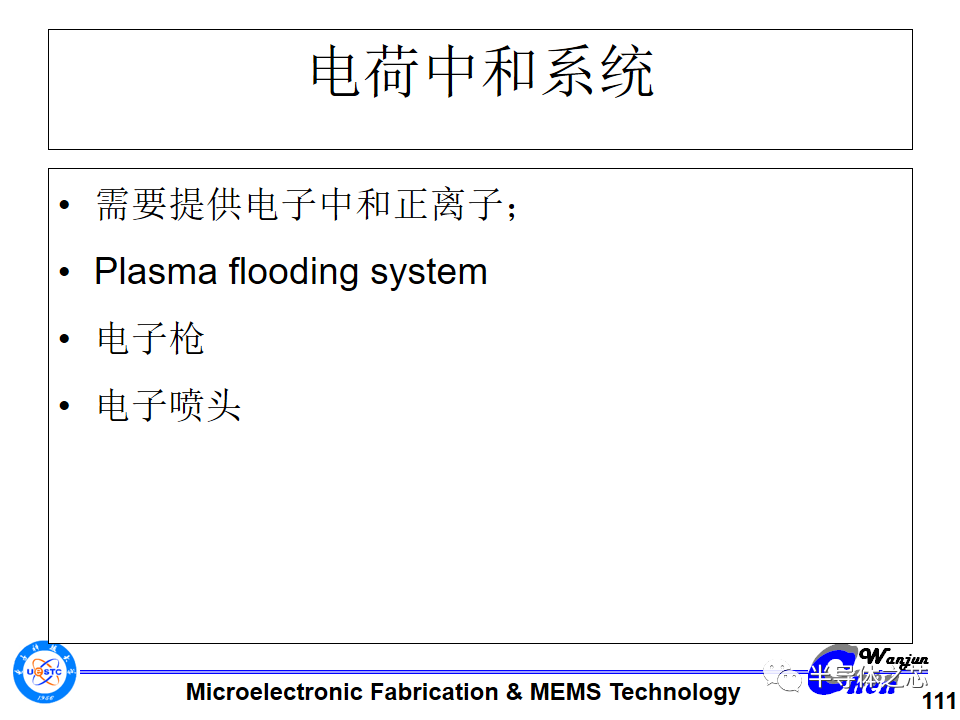
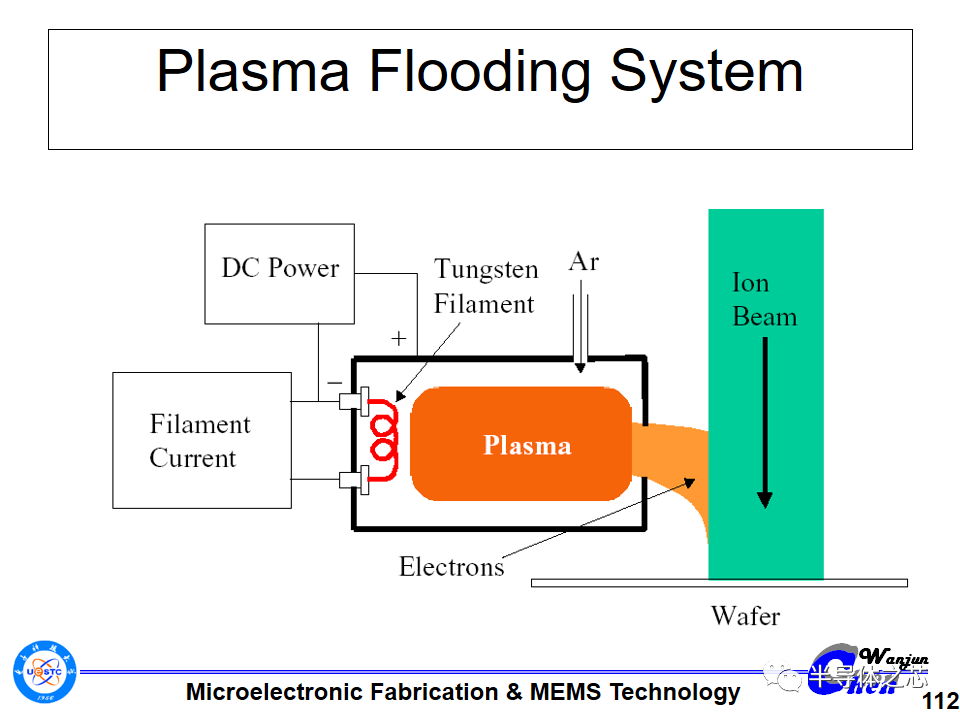
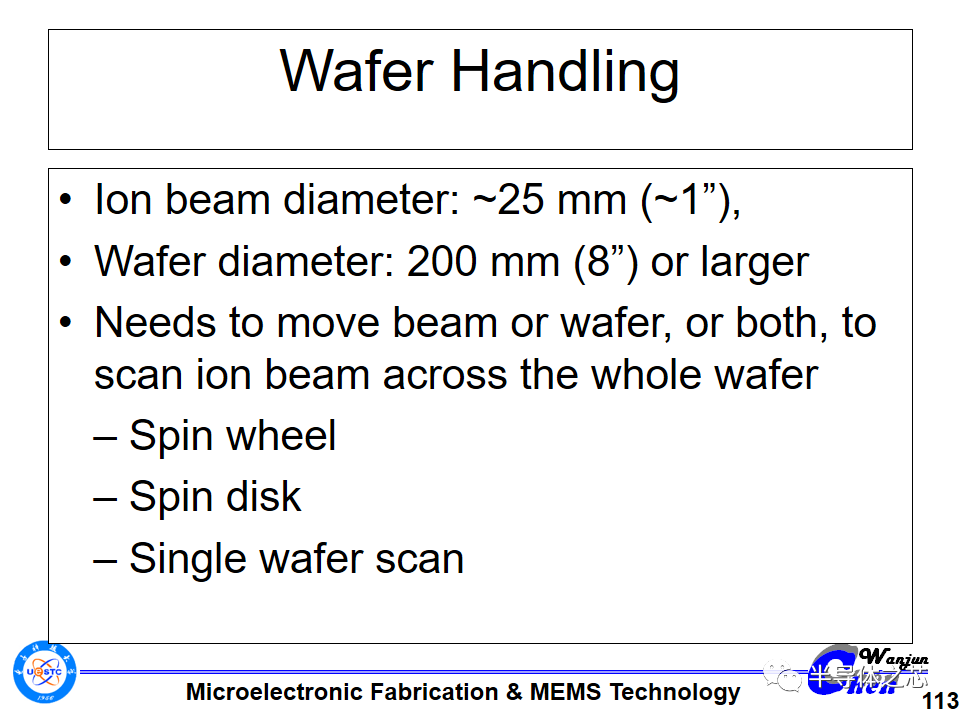
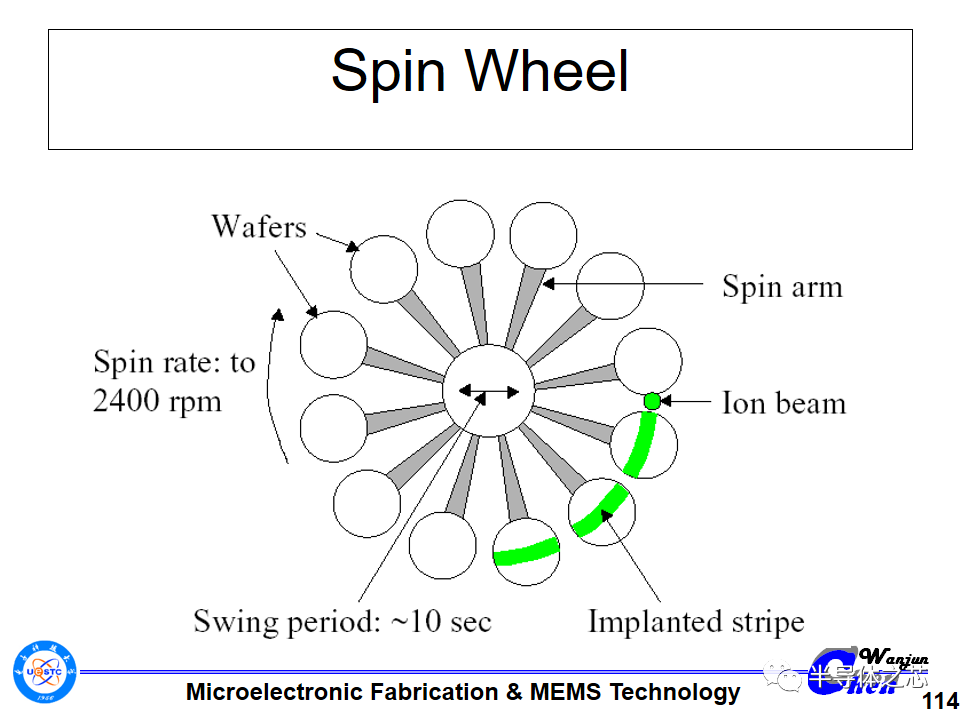
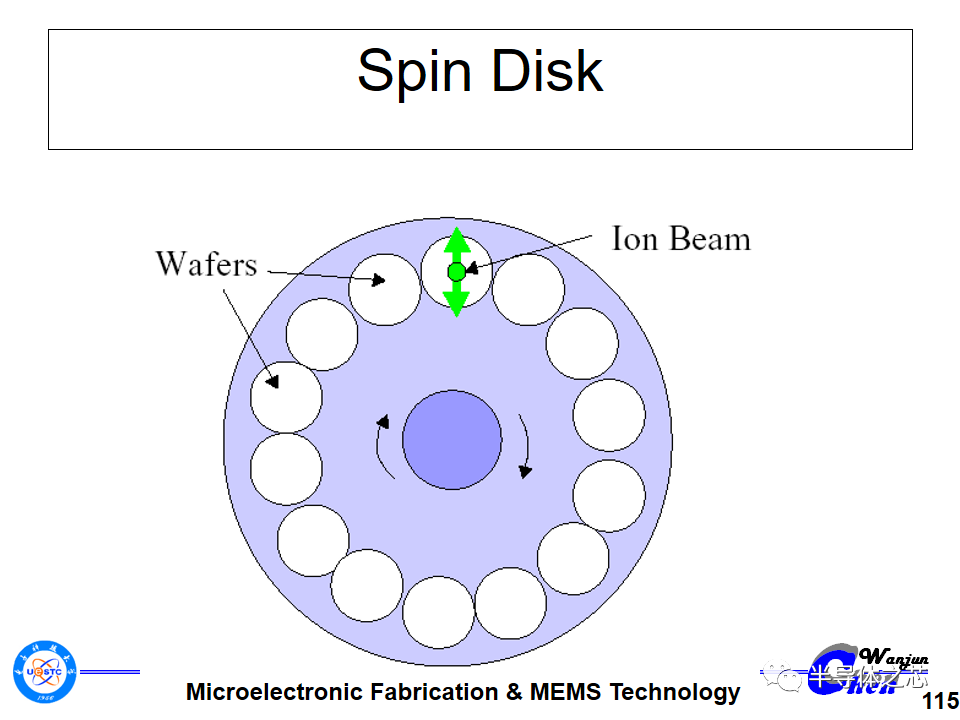
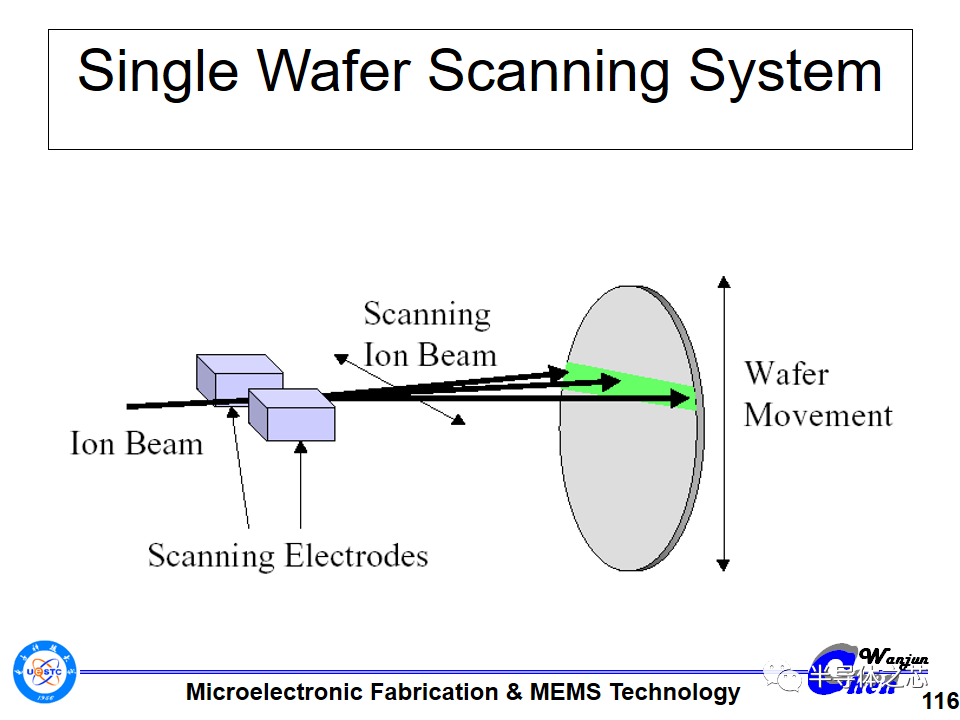
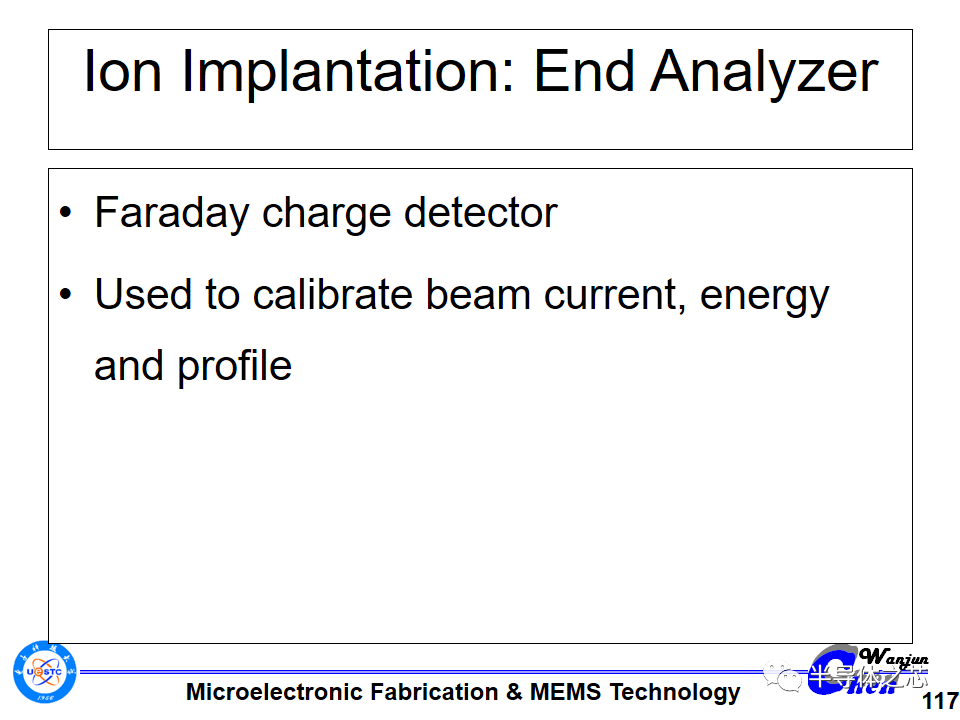
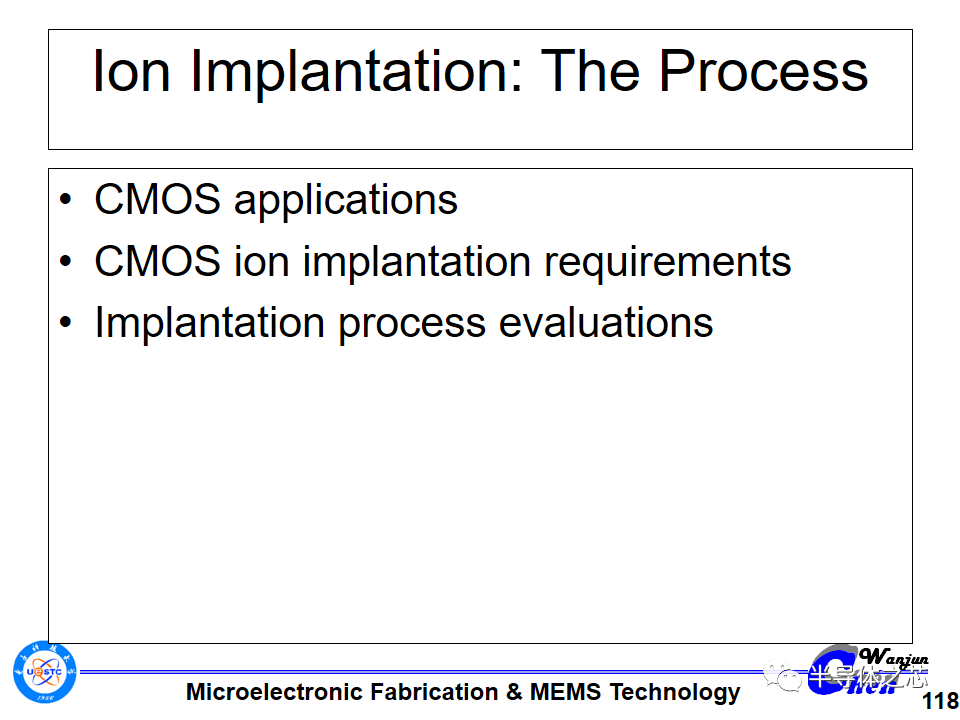

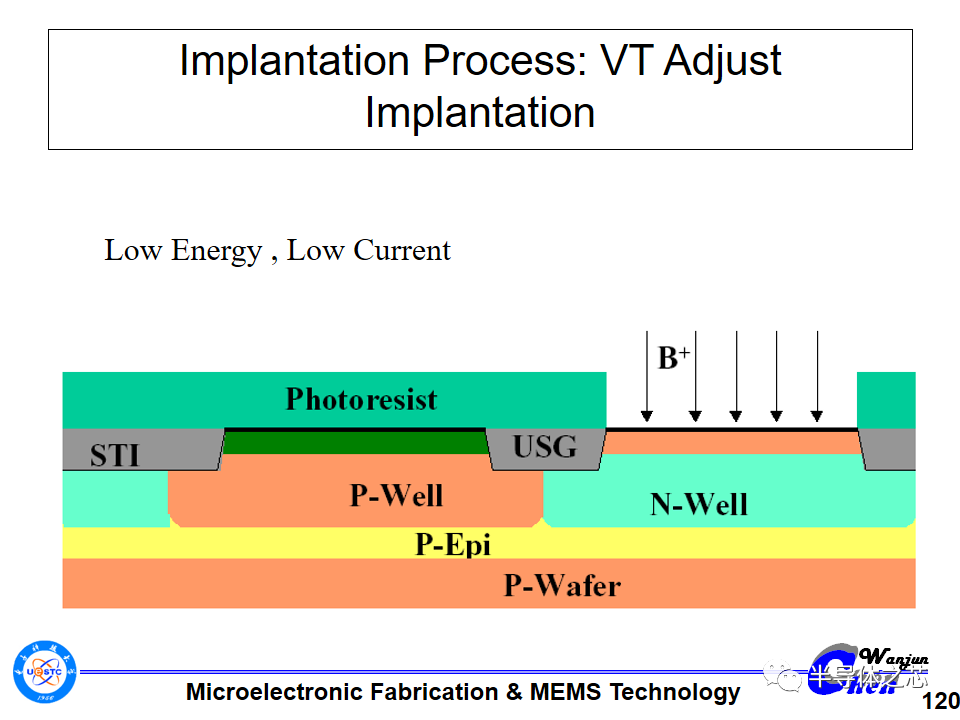
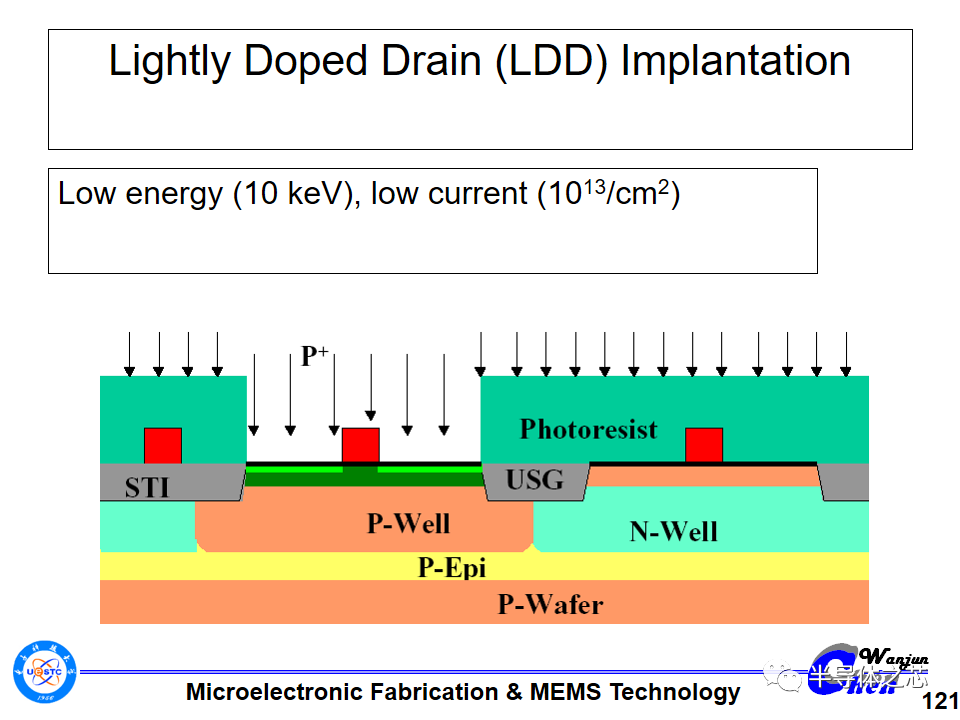
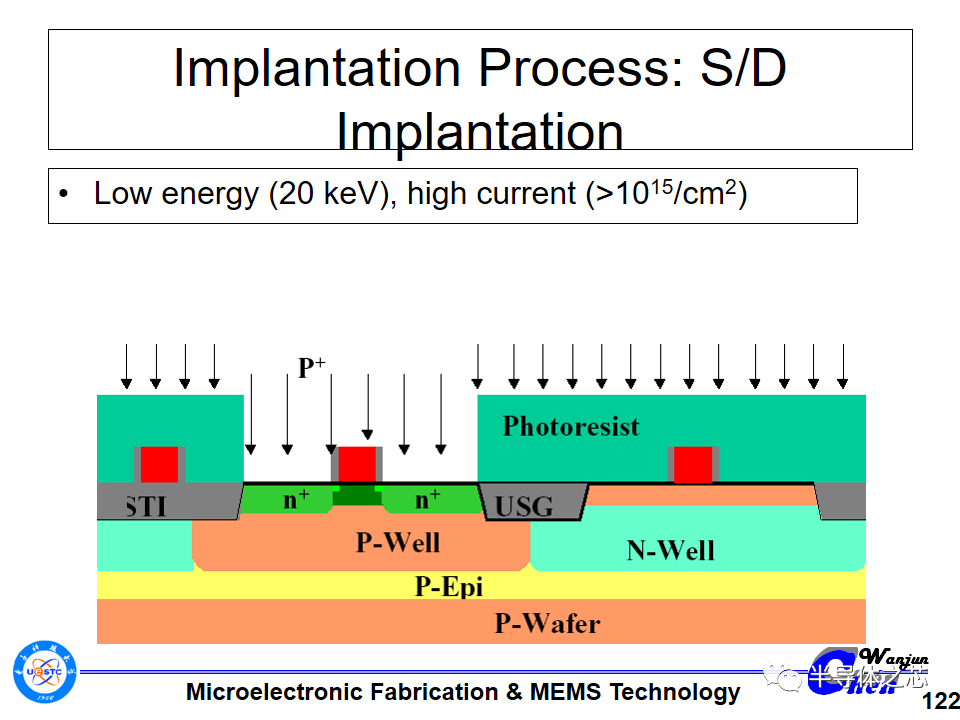
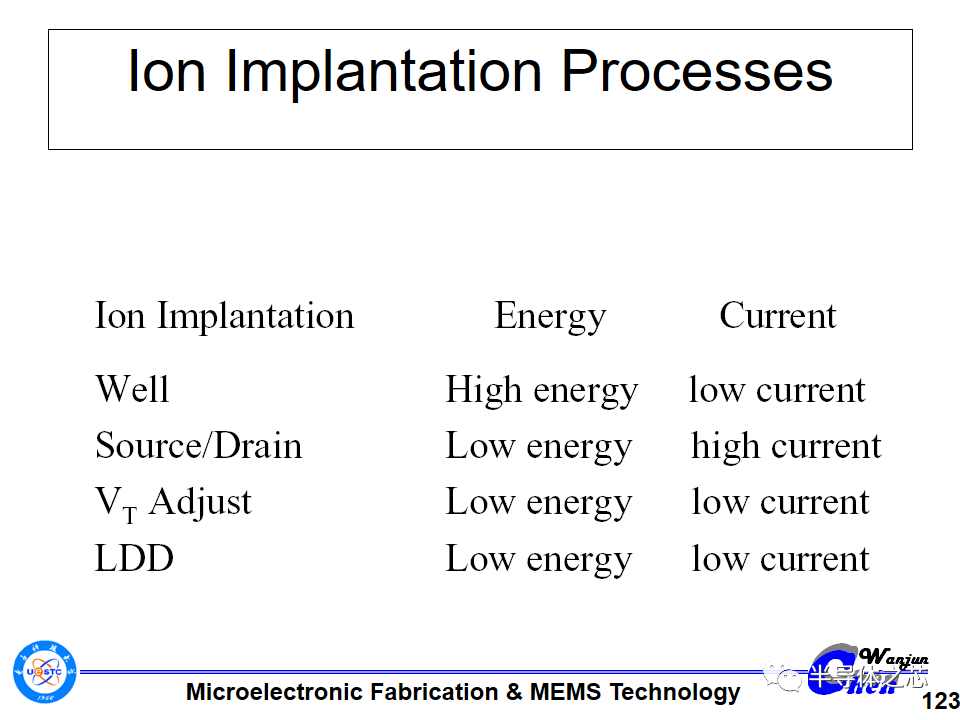
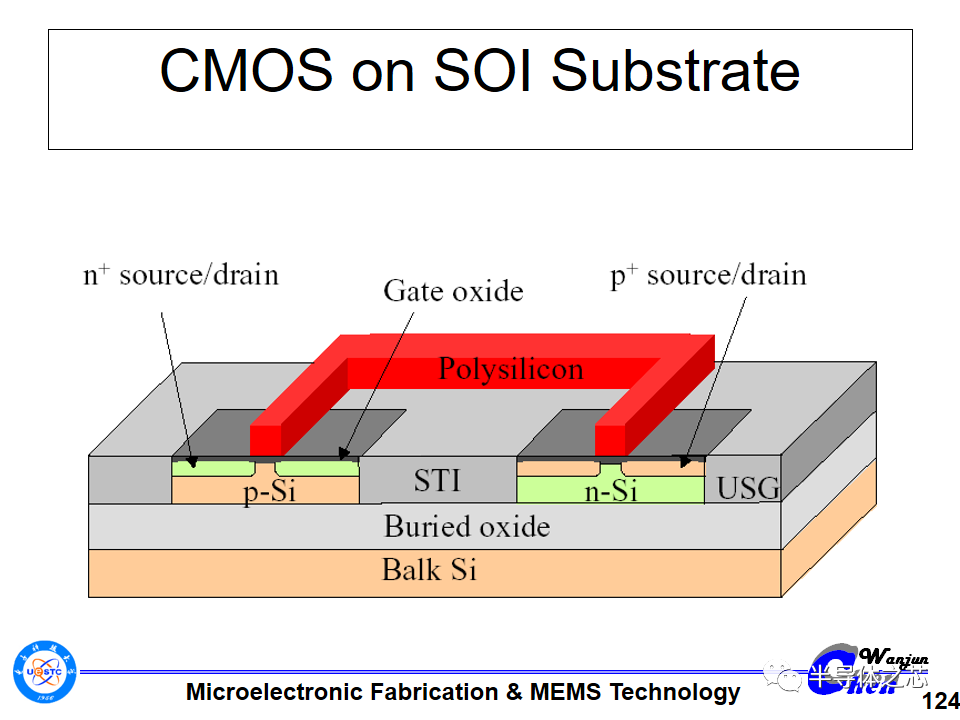
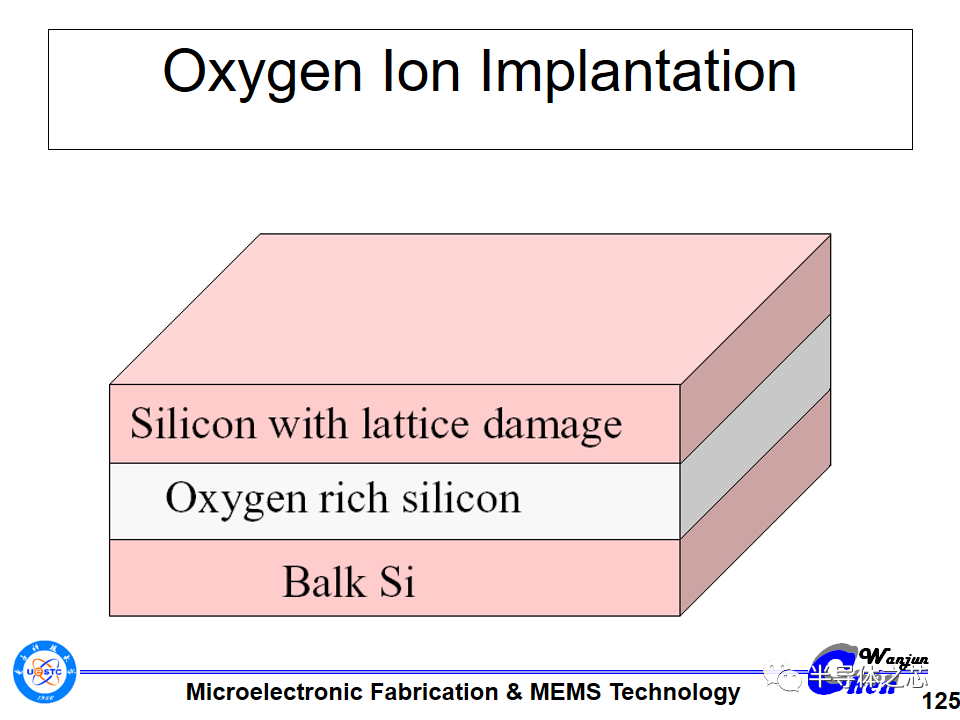
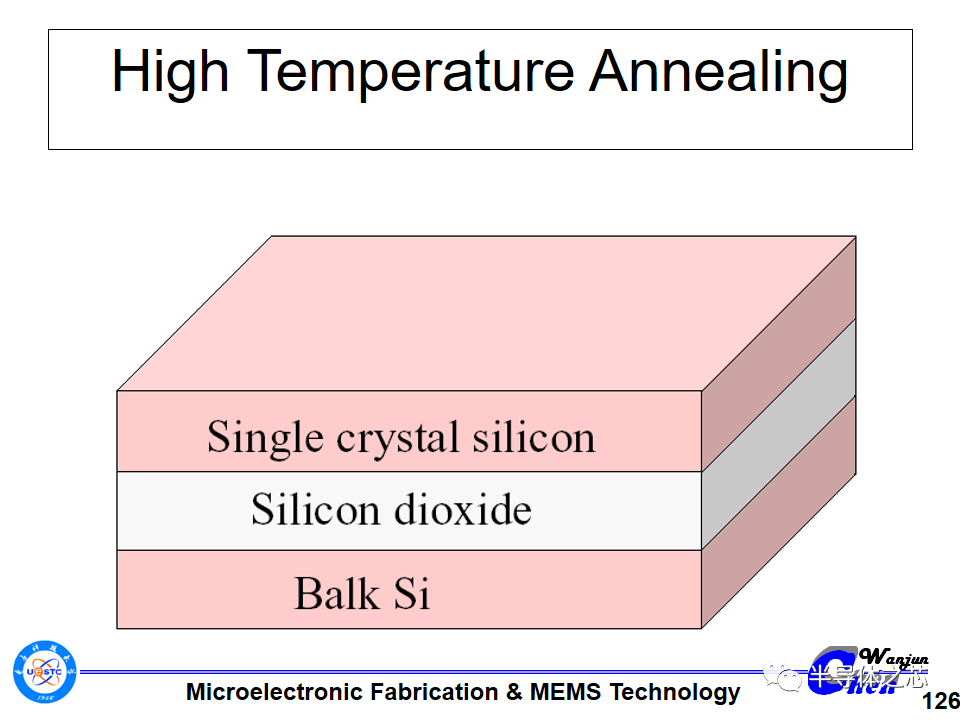
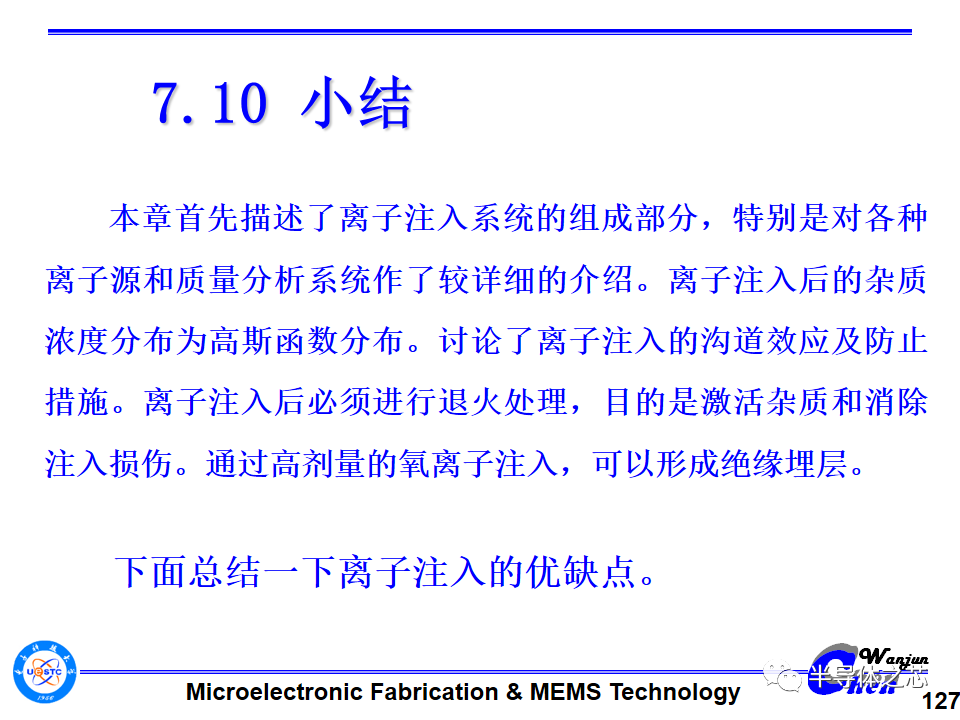
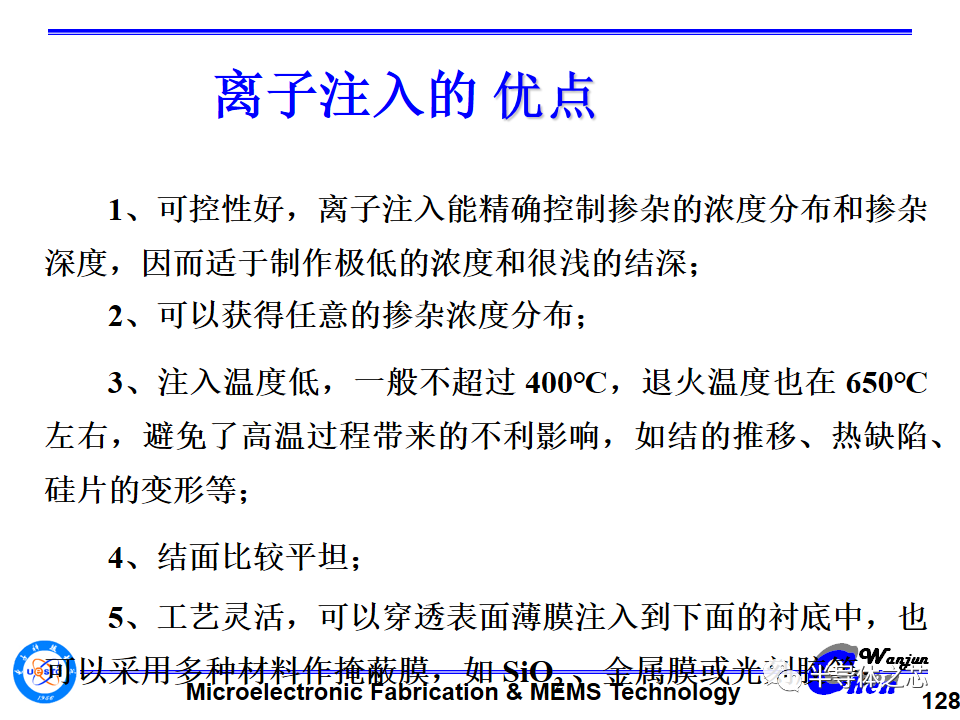
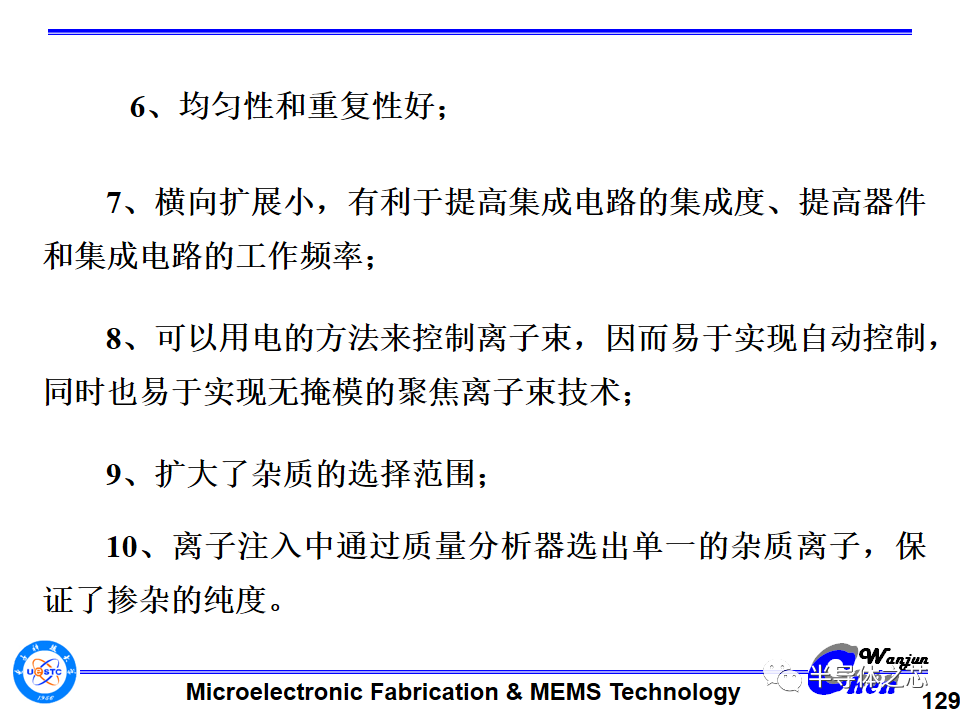
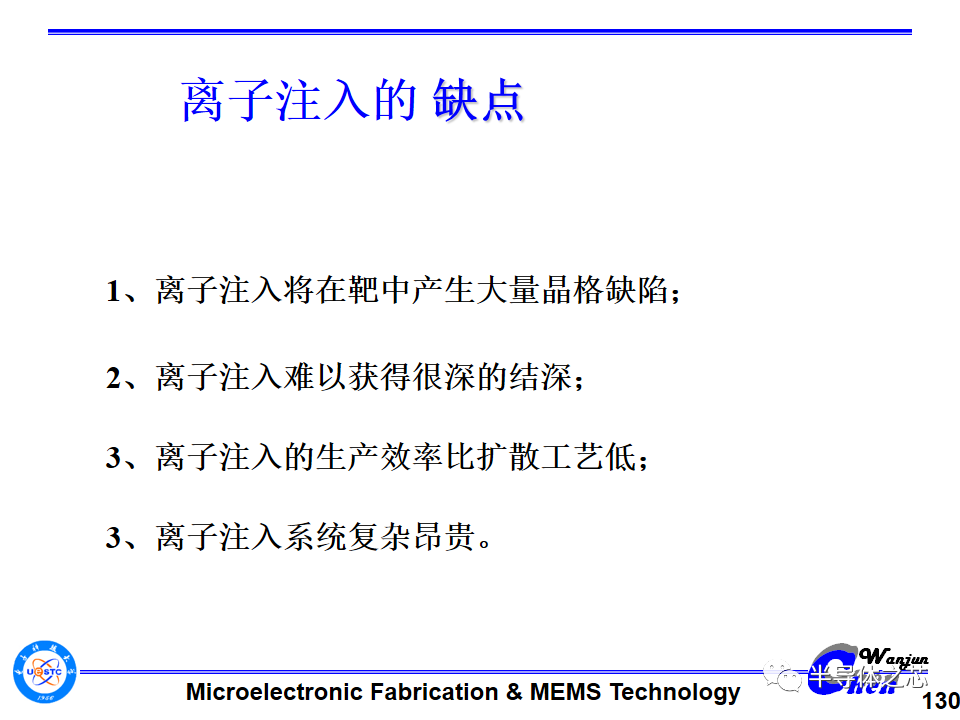
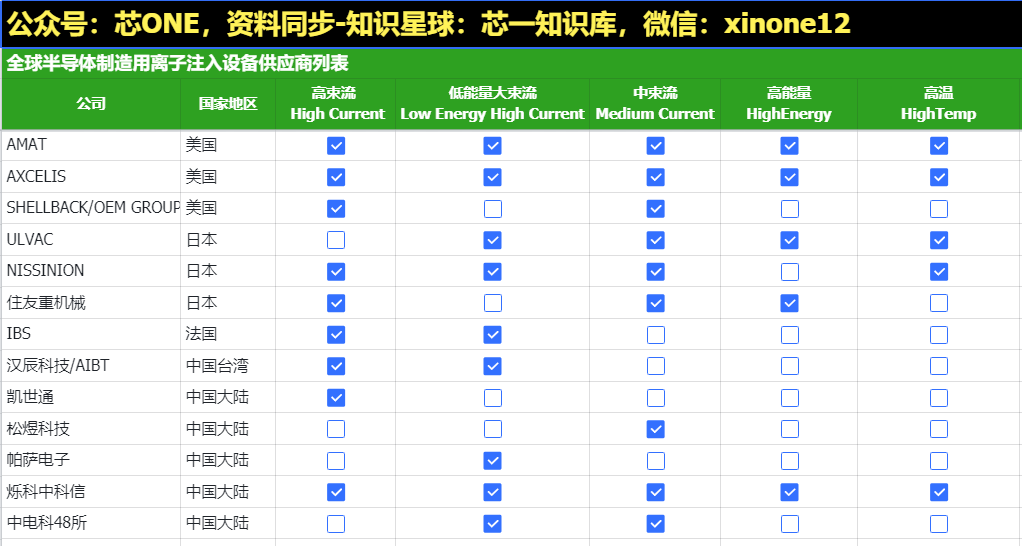
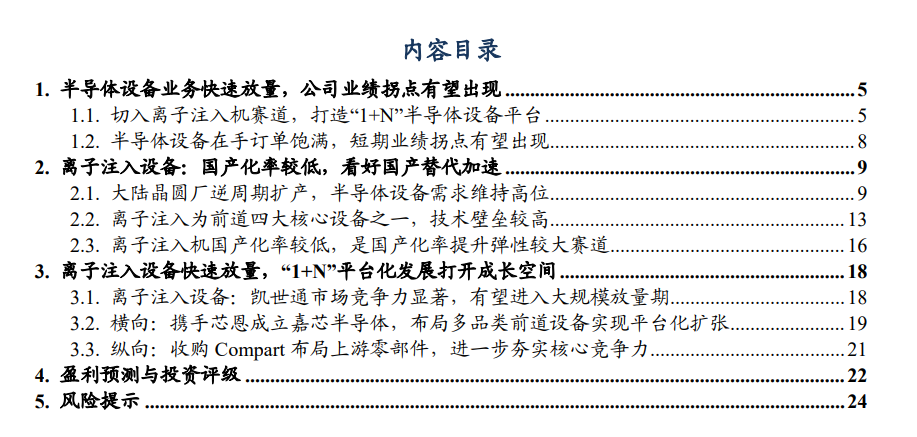
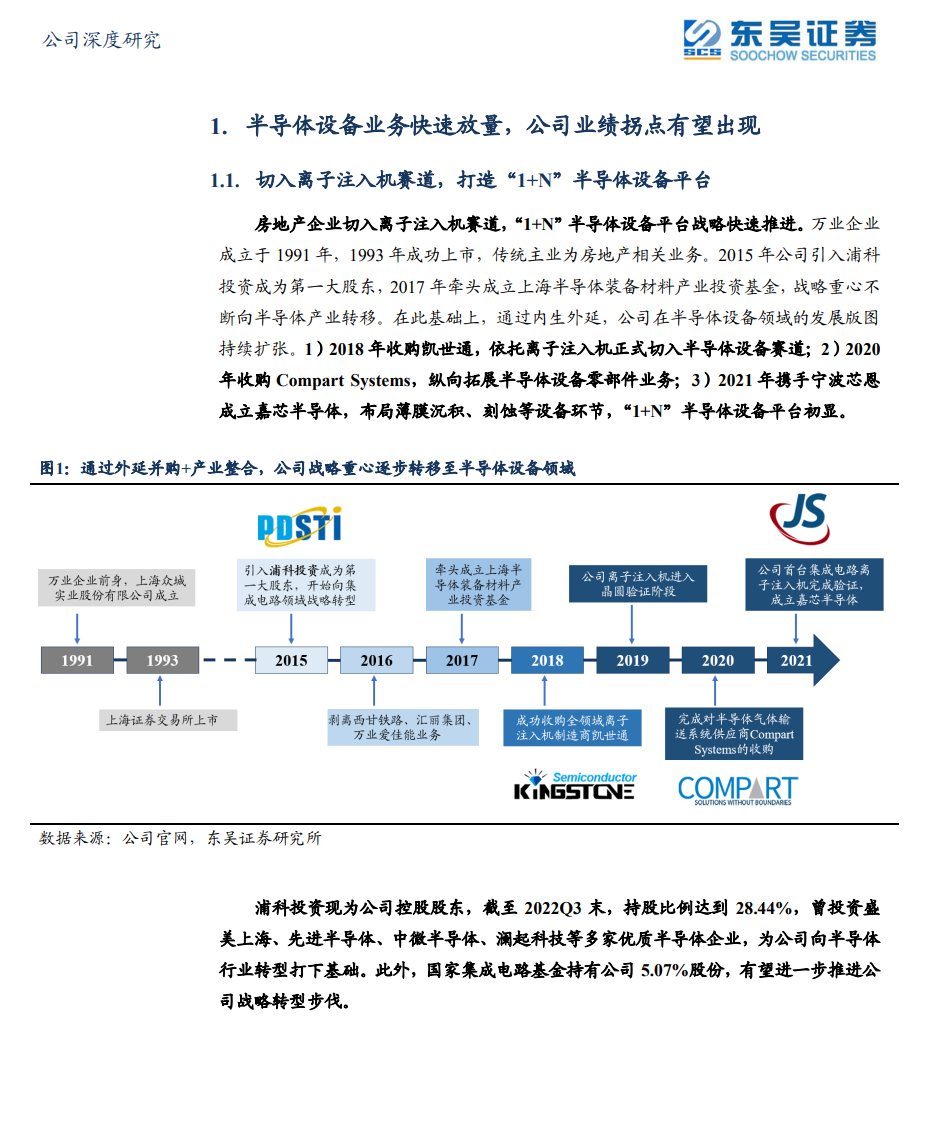
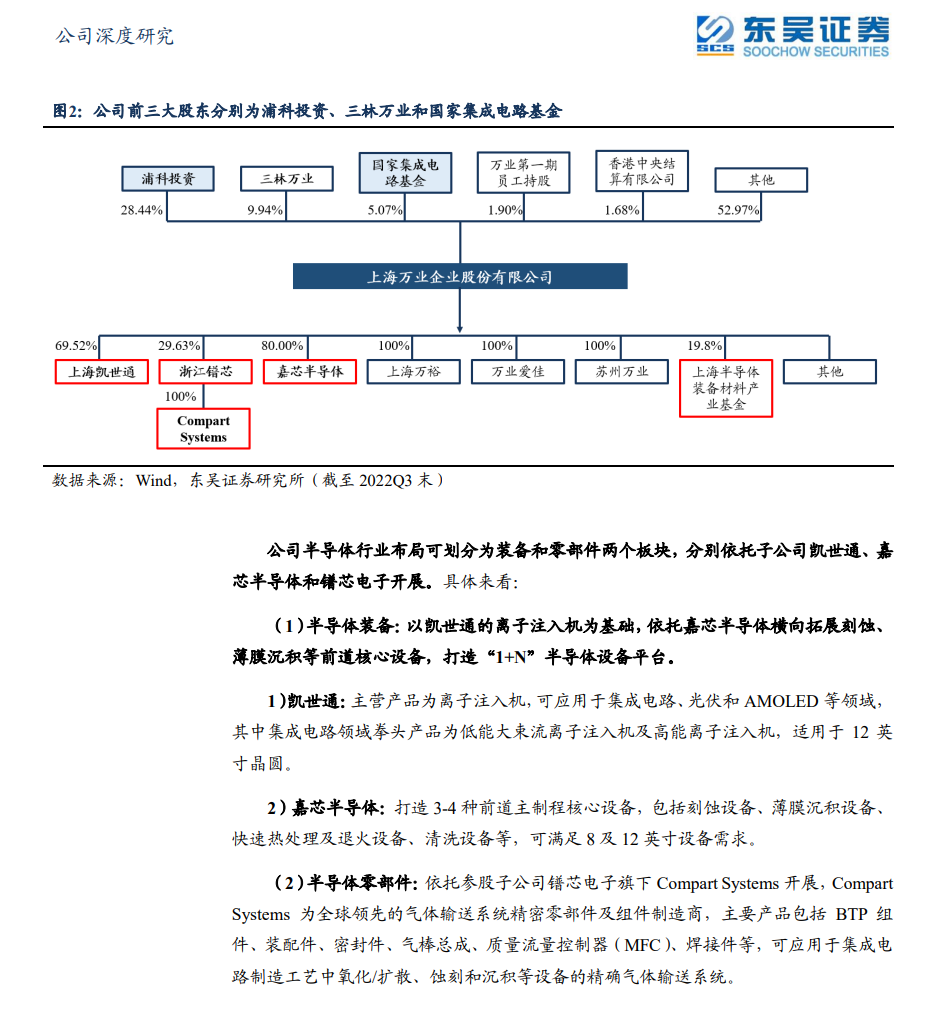
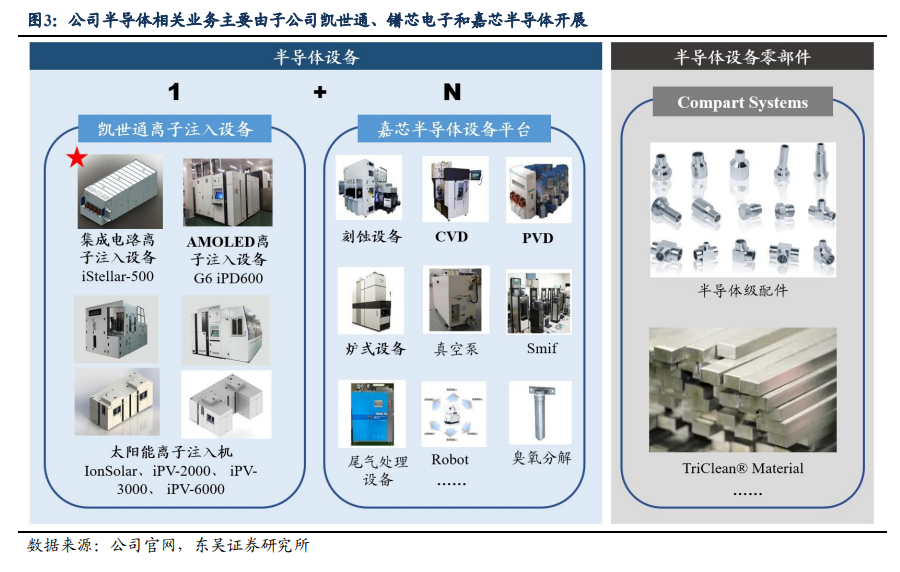
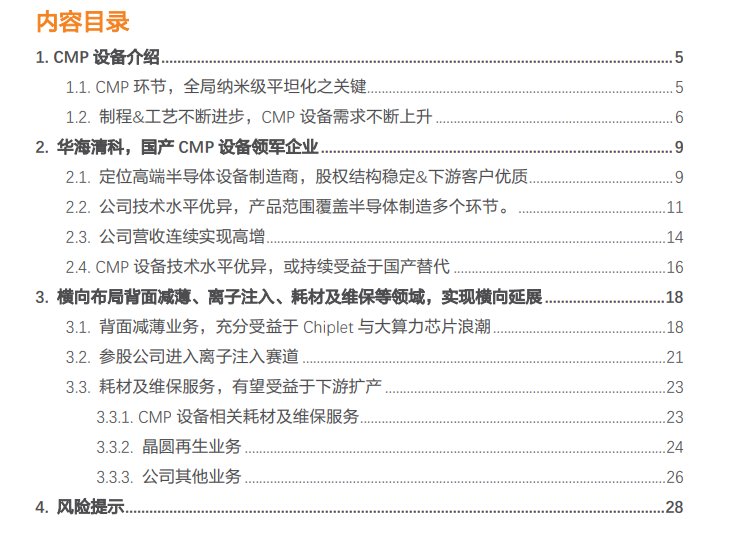
丨扫下图二维码,加入星球下载5000+资料
丨市场、技术、研究,半导体领域必备工具
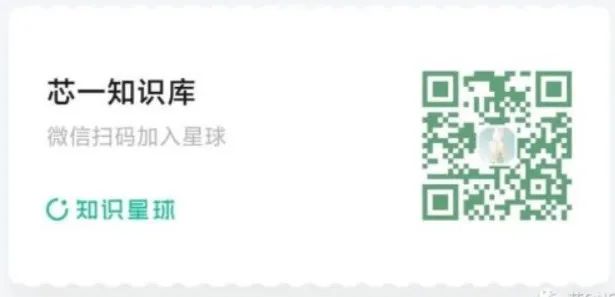
















