点击蓝字 关注我们 SUBSCRIBE to US
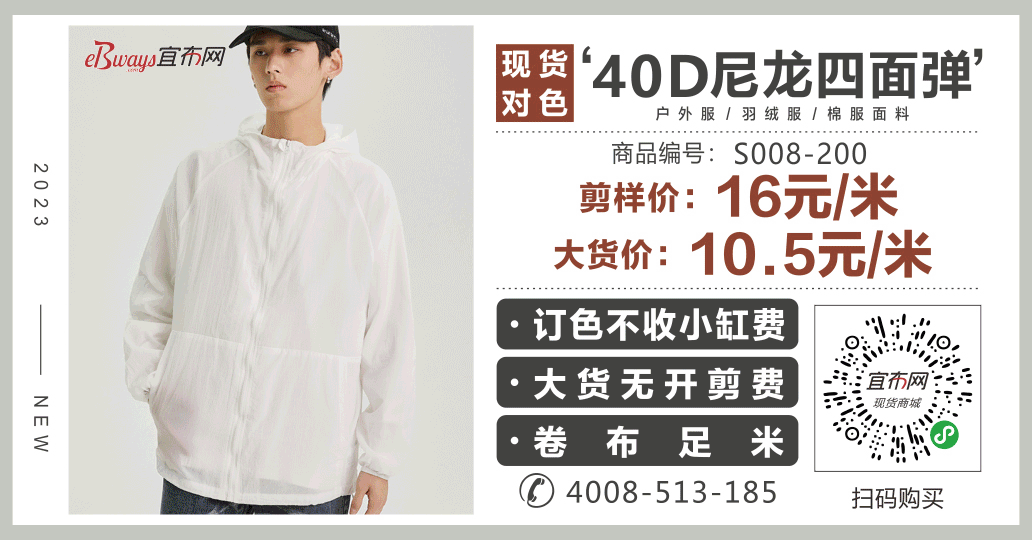
1、浆液浓度不正确
(1)调浆投料计量不准,成浆体积不符合标准。或因牵就黏度改变体积。
(2)蒸汽凝结水太多,造成浆桶、浆槽煮浆浓度变化太大。
(3)输浆或转浆时与其他浆液或水混合。(1)所用浆料黏度的热稳定性太差;尤其是淀粉类浆料要用新鲜未变质的。变性淀粉热稳定性要求85%以上。
(2)调浆时煮浆不充分,黏度未到稳定阶段,使用时变化大。
(3)浆液酸碱度pH值不正确。
(4)浆槽温度不稳定。
(5)用浆时问太长。(2)蒸汽凝结水过多,虹吸管损坏或位置不当,疏水器不灵或回水管不畅,影响烘燥效能。(6)压浆力不适当,压浆力两端不一致以及压浆辊、上浆辊表面损坏或不圆整。(1)由于调浆浓度偏低或蒸汽冷凝水多,使浆液稀释。(3)浆液面不稳定,主要是浮球等液位控制失灵,溢流板漏浆及浆泵作用不良。(3)预压浆辊压力不够,对于一些较难吸浆的经纱品种,应加强预压作用。(4)浆液分解不够,或者浆液配方中缺乏浸透作用的助剂。(3)两组预烘烘筒温度有差异,烘燥纱线热缩性不一致。机后的张力不匀,必然影响到干分绞区开口不一致和松紧不匀。分绞张力偏小,则会增加不匀。分绞张力适当增大,可以减少这种不匀性。从实际运转中可以看到,机后的张力不匀,分绞区的张力不匀,都会带给纱片卷入浆轴中,生产粗厚织物的纱片时尤其明显。通常必须增加卷绕张力和压纱辊压力,来减小相对差异。特别是借紧卷绕、重加压来提高浆轴的平整度,使织造送经时,避免浆轴不平整而造成的松经和经缩。张力和压力偏小主要因为设定值偏小。从后到前纱片经过的导纱辊、张力辊等转动部件不水平、不平行、不圆整,会造成整幅纱片两边张力不一致以及跑偏。必须通过吊线检查和安装调整从根本上解决问题。(2)经轴架上制动力不够,突然停车时出现的松经、扭结。(3)浆纱中出现的断头、抵卡(在筘齿处抵断)造成的部分经纱松弛。(4)起了机时带头不匀,补头不齐。上轴时生头不良造成的松纱。(5)浆纱粘并、绞头和毛羽不贴服造成邻纱粘连,织造开口不清。
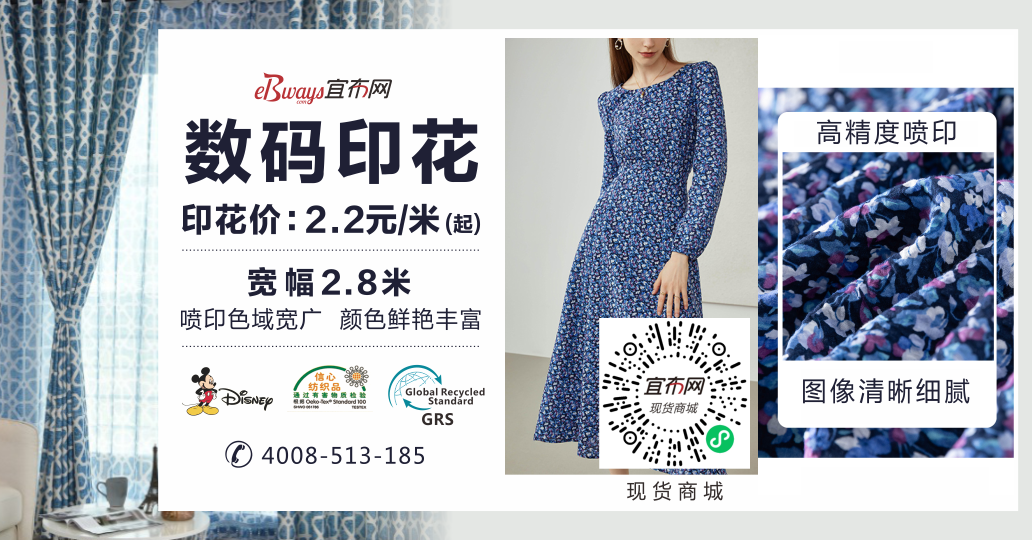
(1)落轴操作时间过长,未开蜗牛速度,压浆辊与上浆辊挤压区残留的浆液干涸,烘干后成为浆皮,使经纱难以分开或留下明显斑痕。(2)中途停车时间过长,如穿绞、处理机器故障和经纱疵点时,以及中途供电发生故障时,均会在压浆辊与上浆辊挤压区留下浆斑。(1)浆纱油脂质量差,浆液出现颗粒状悬浮物,大部分是油脂,黏附于浆纱上成深褐色浆斑。(2)浆槽底部聚积的浆块沉淀物(由于调浆不良造成),受蒸汽冲击浮起黏附于经纱上,经压浆辊挤压成为块状浆斑。主要是浆液表面结皮,又被带上经纱而形成。具体原因是:(1)浆纱了机与慢车运行中,蒸汽关小,浆槽液面静止。当与冷空气接触后,表面凝结成膜,开车前未处理,运转中黏附于经纱上造成连续性浆斑。(2)浆槽内边角处浆液流动性差,特别是上浆辊两头,压浆辊压下的浆液或泡沫容易聚集,凝结后成为浆皮,被上浆辊带到经纱上,经压榨形成浆斑。(3)调浆配方中搀用化学浆料,特别是聚乙烯醇PVA,其成膜性强最易结皮,应尽量选用部分醇解型和聚合度低的PVA,或变性PVA以减少浆斑。(4)操作方面,如动作较慢,停车处理问题的时间较长。了机时对浆槽清洁不彻底。平时对浆液面高低和温度掌握不稳定,突然开大汽冲击沉淀和引起浆液溅上经纱。(1)调浆用料不洁,如乳化油不良,油质低劣,或被弄脏。
(2)调浆桶传动装置油污掉入浆液内。(3)有的使用铁管输浆,在碱性化学浆料腐蚀下生锈,造成锈迹疵点。(6)浆纱通过的各辊和烘筒轴承以及链条油污沾染纱片。(11)运转揩车和保养检修时油花或油污带到纱片上。疵点形态:浆纱过程中发生断头未及时捻接上,在织轴上表现为两种形态:织轴表层头端不缺少经纱,穿经时全幅满穿人综、筘、片,但里层因曾经断头缺纱,织造到该层时,因缺纱接续不上,只好借边上的经纱接上,造成边纱减少,布幅变窄。浆纱落轴割纱时,已断缺纱还未接上,穿经时按头端现有根数穿入综、筘、片中,但织造中织轴退绕到里层时,断头展现出来,成为多余根数的经纱。(2)经轴制动不良,突然停车时经纱松弛形成小辫子,到伸缩筘处撞断。(3)整经时处理断头不良,形成“压绞”,退绕时扯断。(4)经轴上有松浪纱,上浆后在干分绞时扯断或伸缩筘处撞断。(5)经纱本身有细节、弱捻,在退绕时拉断,或经轴本身就有倒断头。(1)经纱本身有细节、弱捻,在通过浆槽时受到湿伸长,以及浆粘、挤压作用,断头缠在浸没辊、上浆辊、压浆辊上。(2)浆槽蒸汽太大,将纱线冲乱或粘并在一起,通不过伸缩筘,造成断头。(3)湿分绞棒表面粘浆,形成浆条、浆皮,把纱线拉断。(2)伸缩筘齿磨灭有纱痕,或飞花、回丝、杂物堵塞,纱线不能顺利通过,发生断裂。粘并的基本原因是纱线上浆以后未进行穿绞棒,使纱片分开,或者穿绞后断头,使分开的纱线重新粘并在一起。具体原因通常有以下几点:经轴架下绞线时有漏绞,或绞线经浆槽、烘房的较长运行中被扯动掉绞,穿绞棒时又有漏穿现象。有的新型浆纱机随机没有复分绞装置,因而只能把轴与轴之间的纱分开,不能把同一经轴的纱片中相邻纱线分开。对于高密织物,这样分绞是不够的,同一经轴上的纱线上浆后仍然可能粘并。如果经轴平整度差,表面凸凹不平时,纱线更容易挤在一起。在没有复分绞时,纱线经过浆槽浸没辊、上浆辊、压浆辊的挤压也会产生不均匀的横动。在湿分绞棒、导纱辊上绕过时也会产生横向位移,都会成为粘并的因素。在分绞棒处容易造成断头的因素,使重新分绞操作太频繁,而没有及时跟上,也就往往是造成粘并的原因。织轴纱片中,纱线排列不平行,相互错位,交叉点难以分开者,称为“死绞”,作为浆纱疵轴考核。具体形态有:(2)两根死绞成麻花状(其中一部分为结经机造成)。(1)浆纱过程中排纱不匀,在筘齿处随意搬动,造成前后错位。(2)断纱缠绕割断后,捻头不良,或未捻在相邻经纱上。(3)落轴时或落轴后,封头布或胶纸未粘牢,或夹板松动,浆纱移动,排列错乱。(4)车头加压测长辊上磨损太深,在辊表面匀头容易错位。伸缩筘调节重新插入纱片次数太多,使浆纱位置经常改变。(5)纱线在伸缩筘齿处撞断后没有理清,重新放人时摆放错位。(1)伸纱筘与织轴未对正,浆轴卷绕一头空边、一头叠边。(2)伸缩筘纱片幅宽与织轴幅宽不一致,织轴卷绕或是两头空边,或是两头叠边。(4)织轴轴芯布太窄,两端未包到位,造成小轴空边或松边。(5)压纱辊太短,压力过轻,两端压力不一致,造成松边。
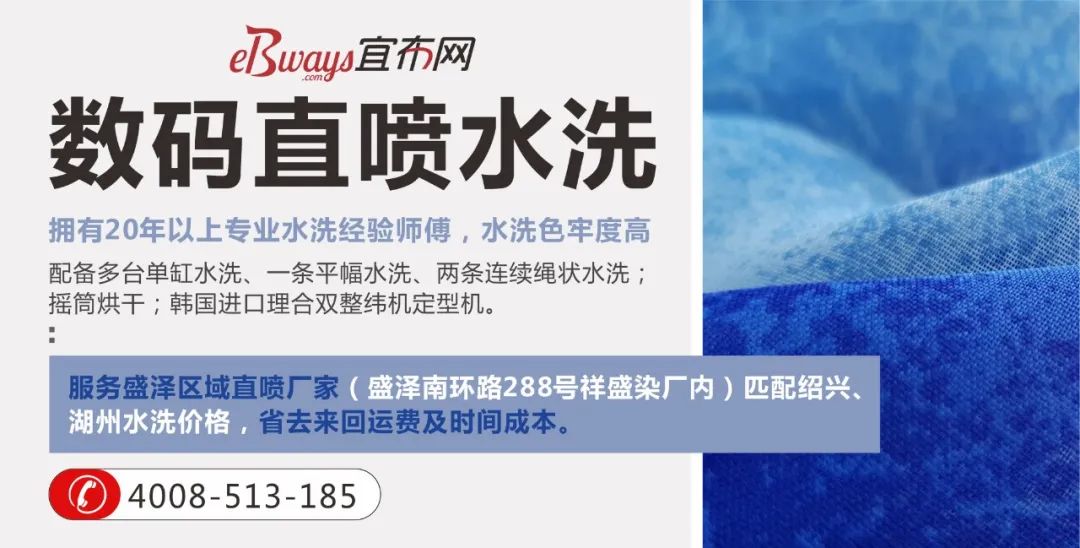
(1)织轴轴芯涂布浆糊太少或用时已干,织造了机松脱,不能进行到底。(2)织轴轴芯涂布浆糊太多,透到布的外面,造成浆纱搭连,织不到墨印。(3)织轴轴芯涂布浆糊不匀,纱片未梳匀平整地贴上,有部分纱未黏住,了机时松脱抽出,不能织造到底。(4)未使用轴芯布的,纱片未整幅均匀绕在轴心,有的纱线堆叠或松脱,也产生类似的问题。(1)加压测长辊轴头的磁性齿轮松动,或脉冲传感器、轴编码器及电路有故障,使测长不正确。或长度设定不正确。(2)加压测长辊轴承及拖引辊轴承损坏,运行有跳动。(4)喷印色水用完,色水有杂质沉淀,色水瓶漏滴等。 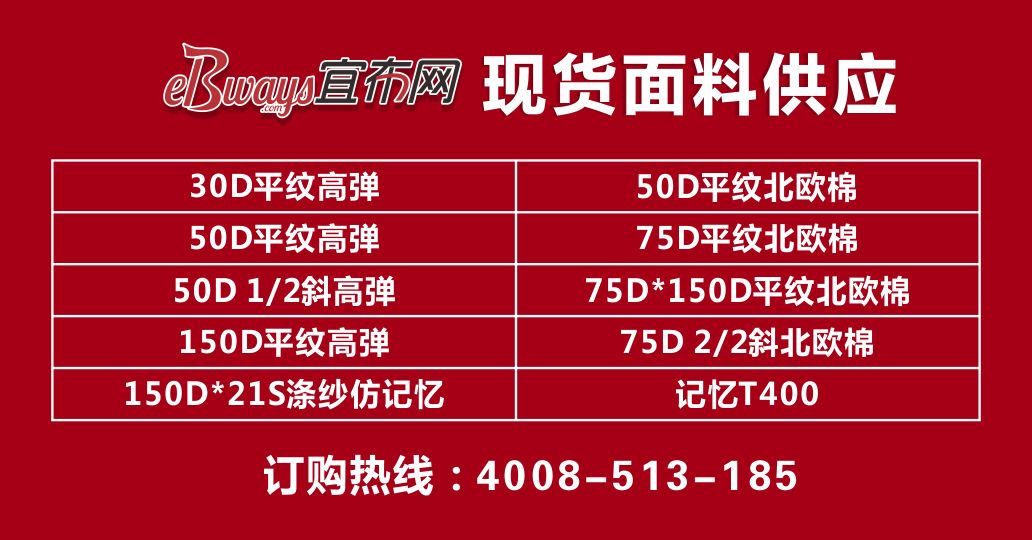